Increasing the level of research to improve design and materials of bogies and wheelsets
Posted: 23 May 2023 | Anish Poudel, Dustin Clasby, Kerry Jones, Ulrich Spangenberg, Walter Rosenberger | No comments yet
Wheelsets and bogies play a significant role in railway operations. Recognising the need for safety, efficiency, and reliability in those operations, the Association of American Railroads (AAR) directs research toward wheelsets and bogies to improve the design and materials of components, their performance in various operating conditions, and enhancements to inspection practices. Colleagues from MxV Rail (formerly TTCI), a wholly owned subsidiary of the AAR, explain how they carry out this research and that a recent move to new facilities sets the stage for an increased level of research in the laboratory, test track, and revenue service environments.
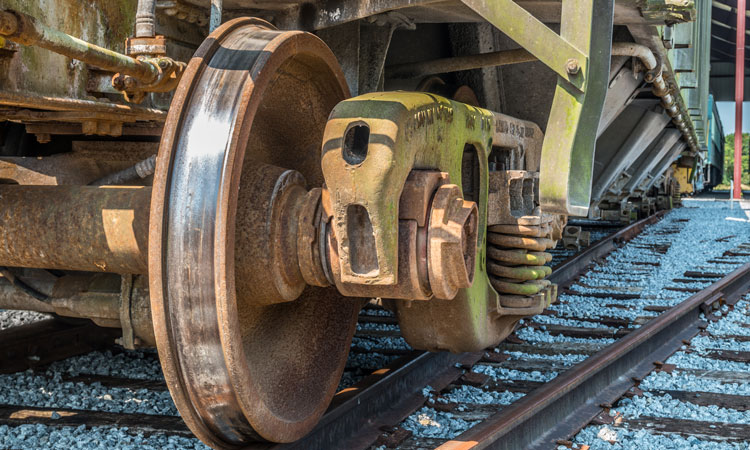
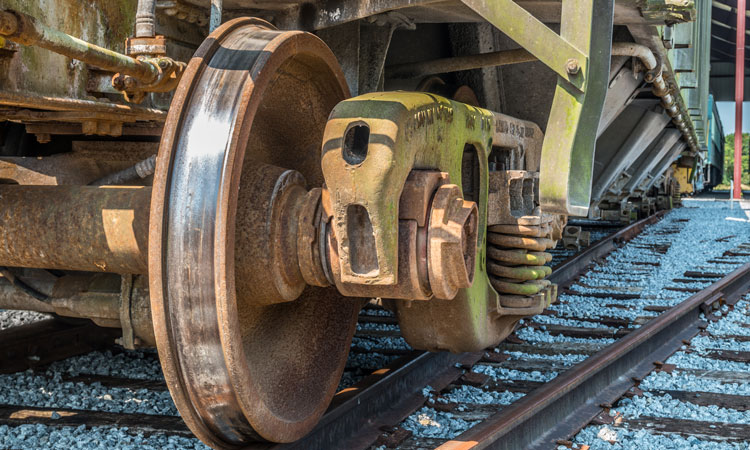
Train inspection technology
The prevailing method for inspecting railcars in service is periodic manual, visual inspection while a train is stopped. Reflecting an industry focus on safety, efficiency and productivity, MxV Rail focused much of its effort on train inspection technology. This effort included enhancing the effectiveness of existing wayside detectors as well as investigating new inspection technologies.
Wheel Impact Load Detectors (WILDs) are among the most important wayside inspection devices deployed on the railroad. These devices drive most of the wheelset changeouts in North America. Most changeouts require a car to be intercepted, shopped, repaired, inspected, and released, thereby reducing car availability and delaying shipments. MxV Rail has determined empty-car WILD wheel impact values that can predict whether loaded-car values will exceed defect levels. Identified empty cars can be routed to home shops, minimising repair costs and delays for shippers. MxV Rail conducted additional research by leveraging the capabilities of WILDs and associated Truck Hunting Detector (THD) systems.
MxV Rail continues to investigate newer inspection technologies as a means of inspecting wheels for subsurface cracks while the wheels are in revenue service. Finding cracks in wheel rims is analogous to finding defects in rail heads. The importance is similar too, as a broken wheel derailment is often as catastrophic as a broken rail derailment. MxV Rail has evaluated several automated cracked wheel detection systems (ACWDS) that employ contacting ultrasonic non‑destructive evaluation (NDE) techniques. In 2020, one ACWDS tested at the Facility for Accelerated Service Testing (FAST) in Pueblo, CO, inspected 10,408 wheels; finding seven broken wheels and 23 with subsurface fatigue cracks. However, ACWDS generally exhibit some performance issues that challenge a commercially successful implementation.
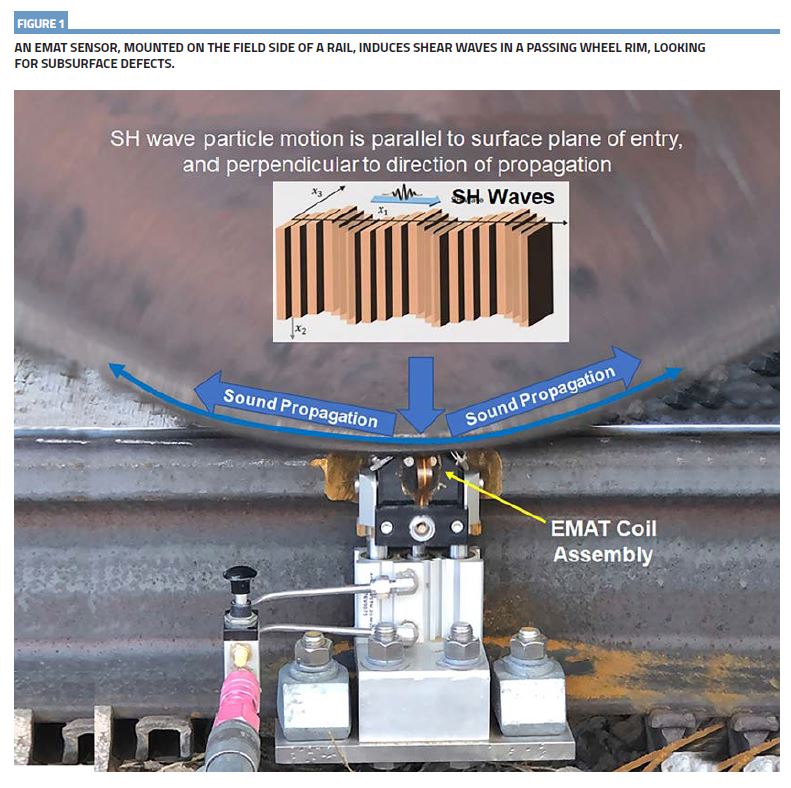
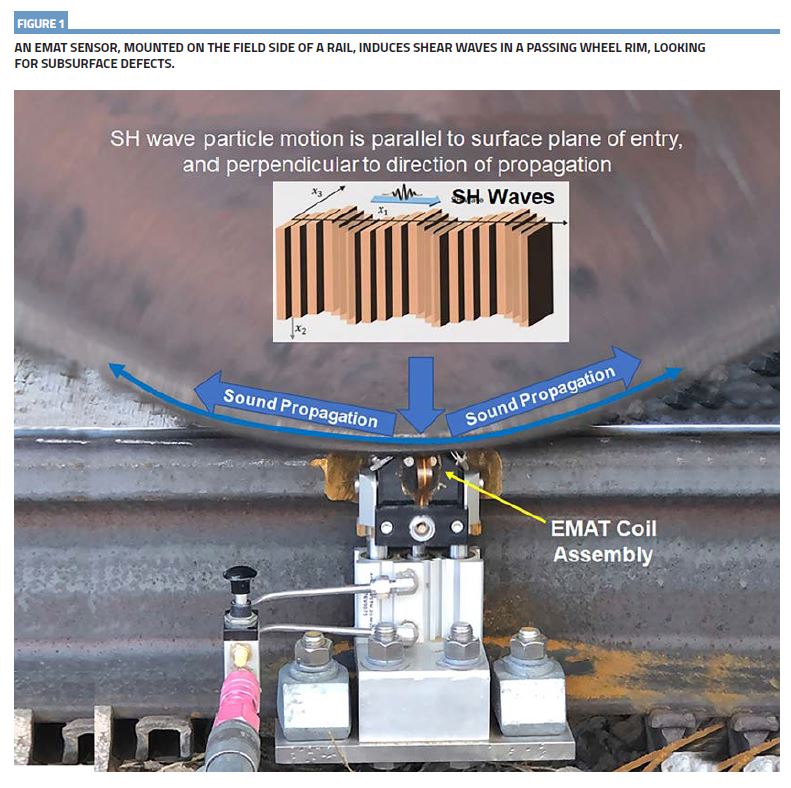
MxV Rail recently began evaluating electromagnetic acoustic transducers (EMATs) to detect subsurface defects in wheel treads. The EMAT systems do not require a couplant or contact between the transducer and the wheel. Instead, EMATs create a magnetic field and induce eddy currents near the surface of the test piece, thus creating ultrasonic waves in the material.
MxV Rail evaluated off-the-shelf EMAT systems in a feasibility study, discovering EMATs demonstrated excellent detection capability with good signal levels in wheel samples that had known defects. Next, MxV Rail worked with a vendor to develop an EMAT system to inspect complete wheel circumferences with the wheel in motion. This requires guided surface acoustic waves, specifically shear horizontal waves, rather than the bulk ultrasonic waves generated in previous ACWDS. Shear horizontal waves offer the best potential for inspecting wheels in motion because wave motion is parallel to the tread surface. However, tests found that non-contact Lorentz force EMATs suffered from noise due to surface conditions. The solution was to add a highly magnetostrictive strip that requires contact with the wheel.
A prototype was built and installed on a short piece of laboratory track with a test wheel rolling over it. The system successfully detected flat bottom hole (FBH) calibration defects, and even found a previously unknown defect in a test wheel. Further development will be required to test the prototype across the entire tread and to the appropriate tread depths.
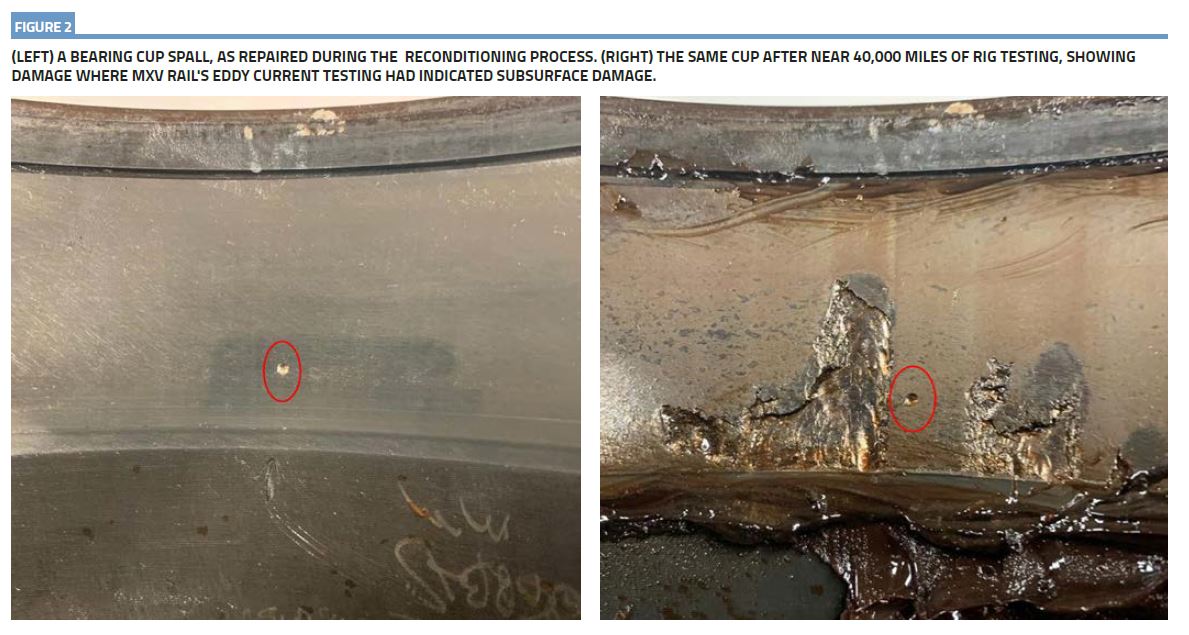
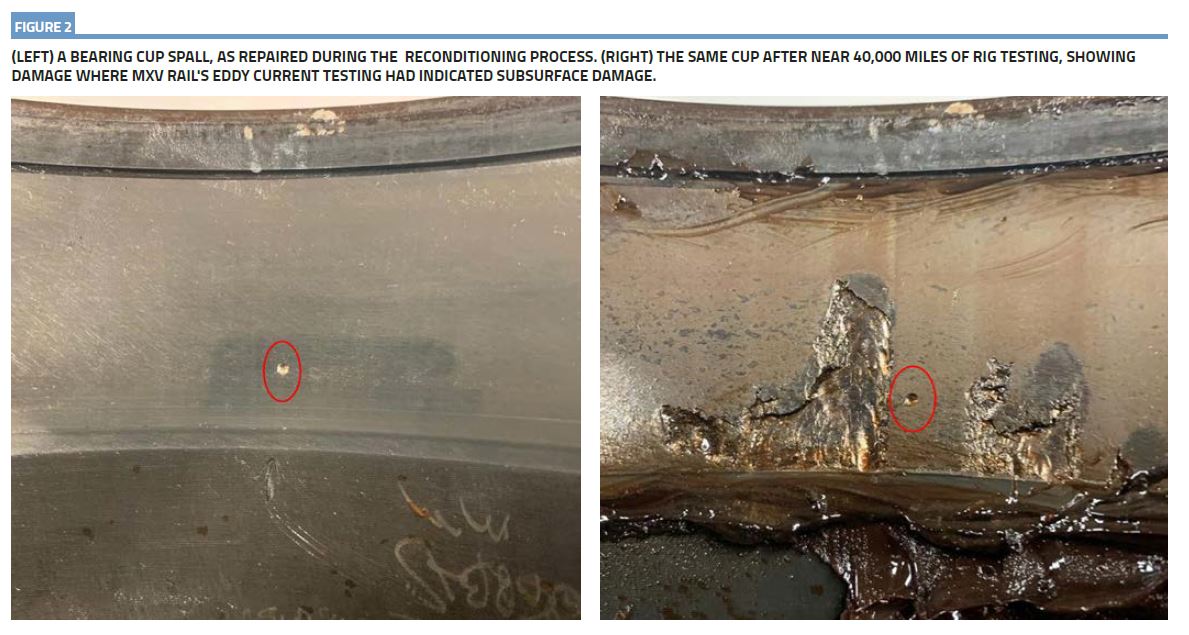
Hunting/curving performance
There continues to be a need to better understand vehicle and bogie performance in terms of high‑speed stability and curving performance. Hunting has the advantage of being detectable THDs. The most common THD is associated with WILDs and uses a vendor-proprietary algorithm to generate a hunting index (HI) value. For several years, the AAR has used HI values indicating hunting to repair cars. Likewise, railroads have long maintained lists of speed-restricted cars – often entire car series or groups – based on adverse experiences such as derailments or significant lading damage.
MxV Rail analysed five years’ worth of HI and THD pass data to determine the risk of hunting behaviour of a given severity (HI) at a given speed. This analytical approach (versus the traditional experiential approach) accomplishes the following objectives in the interest of safety and efficiency:
- Makes speed restrictions deterministic, based on actual measured performance
- Removes unnecessary restrictions on equipment that does not require it
- Can identify equipment previously overlooked for restrictions
- Allows for precise definition of speed‑restricted groups.
MxV Rail performed an additional analysis to determine what physical car characteristics (as identified in UMLER®) might be associated with a higher hunting risk. This is one of many ways that this statistics-based methodology could be used to assess hunting risk. As an outgrowth of this research, MxV Rail studied the relative effects of track conditions at THD sites and began studying the variability in THD measurements.
MxV Rail used simulations to study the curving performance of M-976 trucks (as defined by AAR specification criteria) in turnouts. These simulations included M-976 trucks in new and worn conditions. The simulation results showed that AAR’s Dynamic Curving test regime was more critical than turnout geometry conditions in assessing bogie performance. Further investigations involving adversely worn wheel and rail profiles are planned.
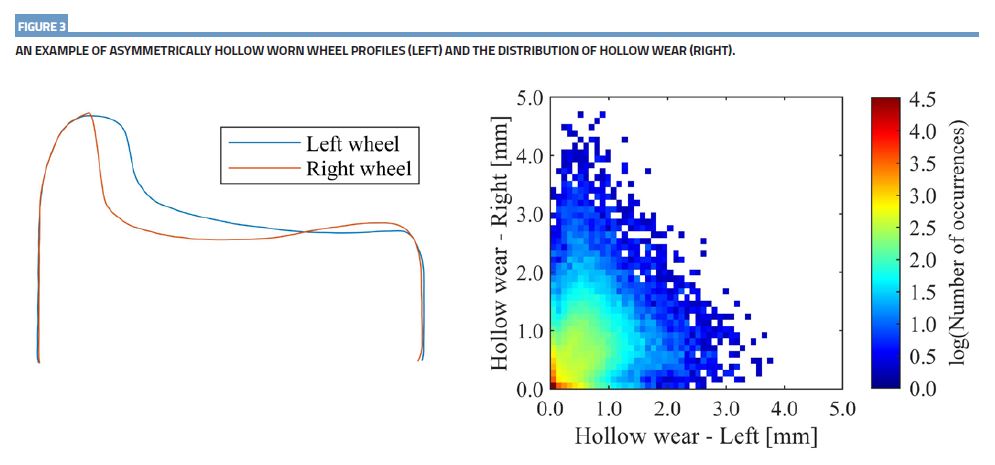
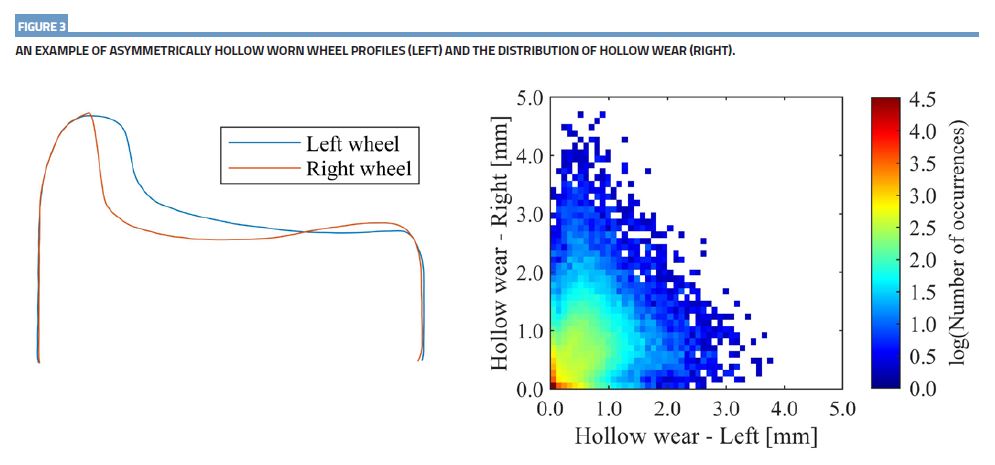
Wheel-axle-bearing components
Basic research into wheels, axles, and bearings as critical equipment components continues with a focus on high-performance wheels and better reconditioned bearing inspections. Defective wheels account for a significant portion of repair costs on North American railroads. Many of the defects are caused by subsurface fatigue, rolling contact fatigue (RCF), and thermal-mechanical damage. MxV Rail’s High-Performance Wheel (HPW) study evaluates potentially improved wheel metallurgies in both FAST and revenue service environments. The latest HPWs have experienced eight removals at FAST and none in revenue service to date. MxV Rail is now planning an additional study where HPWs will be applied to severe duty under articulated intermodal equipment.
Improved bearing reliability is another MxV Rail project. Most bearings supplied in North America are reconditioned bearings that were removed from wheelsets for a reason unrelated to the bearing itself. The reconditioning process includes a careful, manual, visual inspection of bearing components and a manual remediation of visible defects, such as spalls. MxV Rail’s bearing reliability work involves sampling reconditioned bearings, performing eddy current defect testing on bearing cups that have had spall repairs, reassembling the bearings, and then running the bearings on a bearing test machine. These research efforts will hopefully provide the industry with new inspection and repair tools that can be used during the bearing reconditioning process, promoting safe and reliable performance in service.
Wheel-rail interaction and the RCFS
Wheel-rail interaction is fundamental to wheelset and bogie performance, involving the largest capital expenses on both the infrastructure and equipment sides: rails and wheelsets. MxV Rail’s research relies on the Rolling Contact Fatigue Simulator (RCFS), revenue service tests, and an analysis of wayside detector data.
The RCFS is a unique machine designed to study wear and the formation of RCF in detail in a laboratory environment where all variables can be controlled. Recently, MxV Rail studied the effects of water and solid lubrication on the wheel and rail running surfaces. Conditions included a newly turned Class C wheel on new and worn rails with a 15-mrad angle of attack. Water in the contact patch cut the traction ratio and the wear rate by more than half compared to dry rail. However, the cracks propagated deeper in the wet zone than the dry zone. As with water, solid lubricant reduced wear depth by half, and when compared to dry rail, generally reduced crack depth.
In revenue service, MxV Rail tested coal hoppers and intermodal cars with brakes disabled (under a government waiver) against cars with functional brakes. The study evaluated shelling due to RCF, wheelset survival rates, and tread wear rates. Ultimately, there was no significant difference in any of these parameters. Despite numerous brake applications, there was no indication of tread‑braking-induced thermal‑mechanical damage.
Finally, in an analysis of wheel profile detector (WPD) data, MxV Rail found no clear root cause for the development of asymmetrical wheel wear patterns, including the tape size matching tolerance for new wheelsets. The analysis indicated that asymmetric hollow wear:
- Developed more frequently on intermodal and vehicular flatcars (AAR types Q, S, and V)
- Resulted in a lateral wheelset shift but not an increased angle of attack
- Was related to the location of hollow wear and the difference in flange wear on the same wheelset
- Was unrelated to any other wear parameter on the same wheelset.
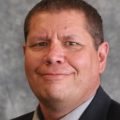
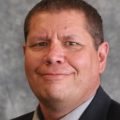
Kerry Jones is a Principal Investigator at MxV Rail, managing wheel and truck component research and supporting other projects. Kerry received his B.S. in Metallurgical and Materials Engineering from Colorado School of Mines in 1993. He worked as a metallurgist in several foundries, then spent 12 years in the oilfield services industry before joining MxV Rail in 2012. His work focuses on preventing freight car wheel failures.
Issue
Related topics
Related organisations
Related people
Anish Poudel, Dustin Clasby, Kerry Jones, Ulrich Spangenberg, Walter Rosenberger