Bogie and wheelset development over the last 20 years: big bang or just incremental changes?
Posted: 24 May 2023 | Kurt Strommer, Martin Rosenberger, Thomas Moshammer | No comments yet
Siemens Mobility Austria colleagues Kurt Strommer, Thomas Moshammer and Martin Rosenberger explain how bogie and wheelset design has changed in the last 20 years, focusing on some of the most important issues regarding safety, noise, wear, and weight reduction, and they offer an outlook on what the challenges and opportunities are for further improvement of these components over the years ahead.
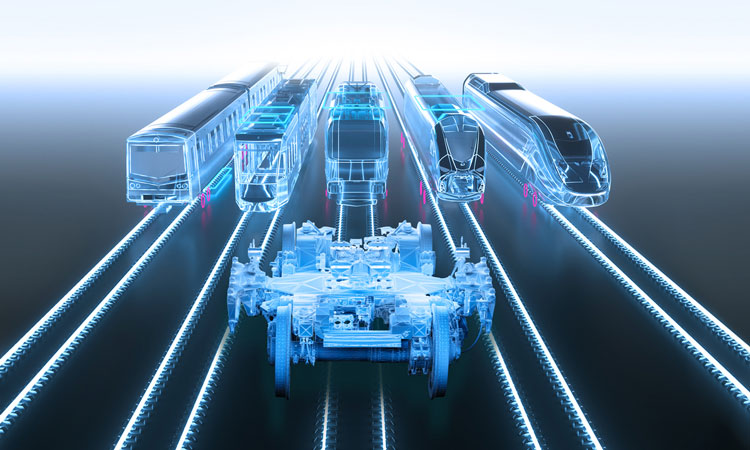
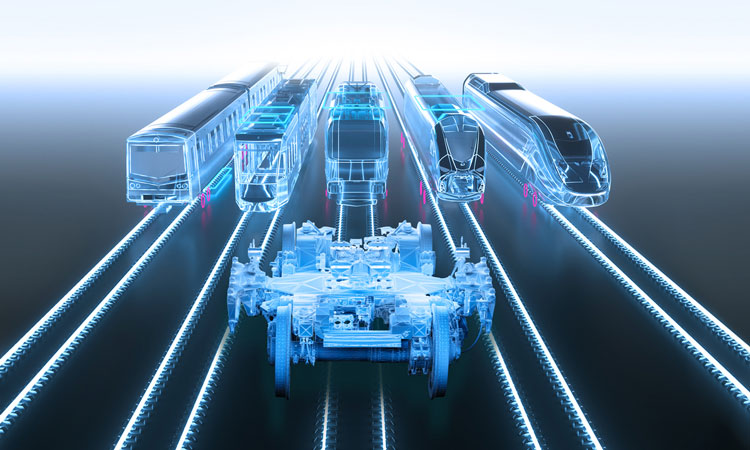
Credit: Siemens Mobility
The Siemens Mobility Rolling Stock Bogie Unit in Graz, Austria is part of MoComp – the family of rail components and the world competence centre for bogies within Siemens Mobility, which means that all bogie developments (for European and international projects) are completed in the Graz and all bogie activities in the satellite production units are managed by Graz.
Although product design is, of course, still mainly driven by customer requirements for key parameters, there are several changes and developments which have made a huge impact on the design of modern bogies and wheelsets.
New manufacturing methods
Beside the raising requirements regarding accuracy in strength design in the last few years, the challenges in terms of the degree of automation in production have also increased. Already in the early development phase, it is analysed whether the frames can be welded on highly automated robotic lines. For this purpose, investigations regarding the accessibility of the welding seams must be performed in an early development phase. This is the basis for manufacturing the bogie frames efficiently at highest quality.
New materials for bogie frames
As weight reduction is one of the most important requirements for a modern bogie, new materials for bogie frames were investigated in the last years. Some of our competitors presented several designs made from carbon fibre reinforced plastics (CFRP) for different applications. Within Siemens Mobility Graz, the strategy is to build lightweight bogie frames with high tensile steel (see Figure 1). The communicated weight saving for both CFRP as well as for high tensile steel is in a range of 40-50%.
Computational simulation and design methods
The process for fatigue strength calculation is shown in Figure 2.
Lightweight design supported by new fatigue assessment methods – advanced load assumption methods, more detailed FEA models and advanced fatigue assessment methods (e.g. notch stress) – enable lightweight structures while at the same time allows robustness to remain the top priority.
The accuracy of the FEA-modelling has increased here over the years. Today, a finite element model consists of approximately 700,000 to 1,400,000 elements. In the simulation of the multibody system, it is necessary to take elastic bodies from structural components into account to be able to depict the correct behaviour of the operation.
In sum, strategic lightweight design has become very important from various aspects including energy efficiency, efficient use of resources, and reduced track access charges.
Dynamic simulation
For the development of railway bogies, the methodology of multi-body-system simulation (MBS‑simulation) is used for vehicle dynamics simulations to assess and fulfil the requirements with respect to safety against derailment and running behaviour for more than 30 years. However, due to the development of more detailed sub-models and modules for different components like rubber metal parts, or advanced processes to incorporate elastic structures into the MBS-simulations not only the forecast quality has increased but also the application area has expanded to load assumptions as well as to ride comfort and acoustics. This was possible because in the last 20 years enormous efforts have been made to bring the simulation and testing of components, subsystems, and vehicles closer together.
Nowadays the simulation models already fulfil the highest requirements with respect to validation, so that they are already in use for virtual homologation of safety critical parameters like derailment safety and running behaviour.
Since the beginning of railway transport, wear of wheel and rail is an enormous cost factor in the rail system. The high-fidelity MBS Simulation models, together with field operational data of wear and tear phenomena, led to the development of more accurate wear and deterioration models of wheel and rail. These approaches are now already used to optimise wheel profiles and the wheel‑rail interface in general, e.g., by using intelligent friction management system. As a result, reliability and availability can be accompanied by reduced life‑cycle costs of the rail system.
Changes of standards
Wheelsets
In the development of wheels, axles, and bearings, standardisation has high influence on product design, as these components have the highest impact on both safety and on lifecycle costs in wheel-rail systems. The safety triangle with design, manufacturing and in service maintenance is deeply regulated. In the following, some examples of the changes of standards and procedures and their impact on wheelset design will be explained.
In the development of wheels, axles, and bearings, standardisation has high influence on product design, as these components have the highest impact on both safety and on lifecycle costs in wheel-rail systems.
The standards for axles have got further approvements with a new procedure for the application of new axle materials as high strength steel 34CrNoMo6 taking into consideration the effects of fretting. The additional definitions were motivated by problems in service and based on the results of European research projects as ModBogie, Euraxles and Widem.
As experience from service plays a major role in validation of the existing components, the publication of incident investigations improved the possibility of the know-how transfer from field into new designs in the last 20 years.
The wheel design standard in calculation procedures for strength design and for sound emission, now gives a chance to optimise the wheel regarding contradictory requirements of weight reduction and noise reduction. If the design is not suitable to be accepted by simulation, the standard offers a second stage, based on experimental strength test results and noise measurements.
Currently, the thermomechanical acceptance procedure for tread braked wheels is limited to tests on dynamometer test benches, however the possibility of simulation for multiaxial strength and for low cycle fatigue assessment, as well as for heat transfer calculation, will be included in near future. This is very important as tread brakes were experiencing a revival during the last years.
Running behaviour
In the field of running behaviour standards like the EN14363 have been extended significantly. Based on sector wide efforts financed by the European Union, methods and processes were established together with assessment metrics that allow the evaluation of the model validity for different application areas of running behaviour assessment. Together with the advance in the forecast quality of MBS Simulation models the use virtual homologation possibilities is consequently increasing. Metrics have been developed that allow the evaluation of the model validity for different application areas.
Integration of new technologies
Besides improvements based on new standards, methods and processes, the mechanical system bogie has been expanded fundamentally by the development of new electronic diagnostics and monitoring solutions which are already in use in several railway vehicle fleets to optimise bogie and railway vehicle maintenance. Based on sensors on railway bogie and carbody together with edge computing devices and intelligent algorithms from simple signal processing approaches up to machine learning and artificial intelligence the health states and the remaining useful lifetime information of bogie components and the bogie subsystem are provided. This information is then used in the maintenance depot to establish condition-based maintenance processes, so that lifecycle costs can be reduced, and availability can be increased.
Possibilities of further improvements
There are several opportunities that will aid further improvements in the future, including:
- Digital twins of both vehicles and infrastructures:
- as a basis for virtual homologation
- a chance for a reduction of time to market
- optimisation of system availability
- Data-driven engineering
- Change from periodic to condition-based maintenance supported by digitalisation, machine learning and AI for a sustainable improvement of operation
- Broad application of new lightweight technologies in bogies for less energy consumption and an increase of transport capacity.
Summary
The design and performance of bogies has changed dramatically in the last 20 years driven by several issues. Nevertheless, especially the intensified use of digital methods will facilitate further impovements in the next 20 years.