Track maintenance and machinery inspection
Posted: 28 November 2006 | | No comments yet
The strategy for the maintenance and renewal of track on the Great British network has been transformed over recent years. There is now a well embedded pro-active engineering culture of ‘predict and prevent’, rather than a reactive one of ‘find and fix’.
The strategy for the maintenance and renewal of track on the Great British network has been transformed over recent years. There is now a well embedded pro-active engineering culture of ‘predict and prevent’, rather than a reactive one of ‘find and fix’.
The strategy for the maintenance and renewal of track on the Great British network has been transformed over recent years. There is now a well embedded pro-active engineering culture of ‘predict and prevent’, rather than a reactive one of ‘find and fix’.
The results of this approach are demonstrated by steady and continued improvement in all track condition indicators (geometry, numbers of broken rails etc), and has been a major contributory factor in delivering improved train performance across the network, which is now at the highest level for over six years. This is against a background of significant increases in both passenger and freight traffic and resultant reduction in track access opportunity for inspection, maintenance and renewal of the track.
In order to deliver a high performing, low failure rate track network in this environment, it is essential to provide engineers with the right level of information on asset condition and performance. The frequency of measurement of that data has to be commensurate with traffic levels, track construction/condition and the level of performance required on a route by route basis. Network Rail has a fleet of infrastructure measurement trains which collect data on track geometry, structure gauging, rail defects and profiles, overhead line heights and staggers and radio communications systems. The data from these trains is all processed at the sophisticated Engineering Support Centre at Derby, which is rapidly becoming recognised internationally as a leader in infrastructure condition monitoring and data processing.
The frequency of recording has to be such that the information provided to engineers allows them to monitor trends and rates of deterioration with a high degree of certainty, thus enabling them to identify the need for work (tamping, rail defect repair/removal etc) sufficiently far in advance to plan resources and access within the normal planning timescales, avoiding the need for short-term intervention which is disruptive to trains and passengers. On the primary high-speed lines, the New Measurement Train records geometry at one or two weekly intervals and the Ultrasonic Test Unit (UTU) tests rails eight times weekly. Other routes are measured at lesser frequencies, but in most cases the frequency is greater than the minimum required by track standards, in order to support engineering decision making.
Further initiatives in the development of ‘intelligent infrastructure’ include the fitting of unattended geometry systems to service trains, the replacement of existing and installation of new, more sophisticated hot axle bearing detectors and wheel impact load detectors. Additional developments include the installation of ground penetrating radar to the UTU trains, which will provide valuable data in the understanding of track geometry behaviour and will support renewal specifications, together with the continued development of high quality video inspection of components with pattern recognition, which will further reduce the reliance on people walking the track to identify defects.
There have been a number of articles in professional journals and magazines covering the significant advances in infrastructure measurement and data management by Network Rail. Having all of the information on the condition and performance of our track is not, in itself, worth a lot unless engineers are translating that information into good engineering decisions which are leading to improvements in the actual maintenance of the track. The following are examples of that application of the information, which are delivering the improvements in condition and performance, described above.
West Coast Main Line
The upgrade of the West Coast Main Line has delivered high quality track which must be maintained to absolute track geometry in order to support the running of Class 390 Pendolino trains at up to 125mph in tilt mode round the curves, on what is a very curvaceous route.
The New Measurement Train now runs at weekly intervals on the route, providing frequent geometry data to the Area Track Engineer and the geometry maintenance team. Previously, a three monthly track recording of this route served only to act as an audit of activity on the asset, highlighting areas where rapid maintenance were required and where track quality had deteriorated to such an extent that on track machine maintenance required planning.
Any number of tunes can be played on the information to allow the engineer to target and analyse route performance. Simple standard deviations calculated by eighth of a mile for the normal four geometry parameters now become a powerful tool demonstrating a number of useful track quality trends.
As shown in Figure 1, the information from each run can be plotted adjacent to each other allowing deteriorations over both eight and 26 weeks to be plotted.
The difference between the time periods allows both the gradual and the rapid track geometry deterioration to be identified and investigated. This is irrespective of the quality of the track components and can therefore spot track that appears to be of good quality but where geometry is deteriorating to be highlighted. This offers two main benefits:
- It offers an effective replacement to the visual assessment of track geometry undertaken by the front line patrolmen, releasing the patrols to concentrate on component condition. This can then be planned into night time track access opportunities supported by adequate lighting. This has significant benefits in reducing disruptive daytime patrols and allows the periodicity between visits on good track to be extended to two weeks. Figure 2 illustrates how the application of this approach has reduced the train delay minutes on the West Coast Main Line South section (London Euston to Crewe).
- On track machine treatment can now be targeted at areas of track where deterioration is starting to affect the overall geometry quality but which has not passed the point at which the increasing track forces add to the problem. Timescales for accurate preventative treatment can now be extended to 26 weeks allowing economic planning and securing of resources.
Other technological improvements in the treatment of track deterioration at an early stage are the application of an absolute track geometry railway and the subsequent process of re-installing the design alignment.
On the West Coast Main Line South Area (WCML (S)), this is achieved by the use of the Em-Sat track geometry recording units to establish the lift and slue files required to replace the track to its designed position. The optimum geometry can always be maintained. This simple benefit manifests itself with dramatically extended frequencies between tamping treatments, especially on tight transitioned and curved routes.
Figure 3 shows a typical geometry output file showing the pre (Red) and post (Blue) traces. This clearly demonstrates the re-establishment of the transitions and cant.
With both the geometry and the position being monitored and returned to a good standard, periods between treatments are being extended by up to twice the previously perceived average.
Improvement to the rail management programme has also made the track engineer’s role easier. This is through the co-ordinated application of train borne grinding, effective lubrication management and the eight weekly recording of the rail condition through the Sperry UTU testing train.
The application of this grinding and ultrasonic testing regime has resulted in the achievement of zero rail breaks from ultrasonically detectable defects on the WCML (S) area for the year April 2005 to March 2006. It has also resulted in the reduction in the number of removable rail defects, due to the ability to understand defect growth rates and to therefore identify benign defects which do not threaten the integrity of the rail.
Current developments will soon lead to the fitment of a laser rail profile gauge to the ultrasonic test train to give a constant readout of the rail profile. This will allow trends in wear to be analysed rather than the cyclic application of a manual inspection/measurement regime.
Manual ultrasonic testing by on-track staff is now therefore only undertaken in areas where new suspect defects have been identified by the train rather than, as before, across the whole route. With the discovery of defects now at an earlier stage in their life, intervention can be planned to longer timescales ensuring that both inspection and removal cause less service disruption.
Southern Measurement Train
Operating predominantly on Network Rail’s south east territory, the Southern Measurement Train (SMT) comprises of the Plasser built UFM160, and its base systems, plus two additional systems (conductor rail measurement and UGMS) to meet Network Rail’s infrastructure measurement/ recording requirements.
The Southern Measurement Train is capable of measuring track geometry, rail profile, overhead line, and conductor rail locations, providing a significant measurement capability. It also includes non-measured systems such as rail surface defect detection, forward facing video, overhead line video, conductor rail video and thermal imaging. All of the measuring/recording systems employed on the SMT operate at up to 100mph (160 km/h), enabling easy integration with service train paths.
The methodology chosen to assess and demonstrate the business benefits of a vehicle such as SMT is a set of trials utilising the outputs to assess whether they can be used to undertake all or part of various visual track based inspections currently undertaken by Network Rail’s maintenance organisation. These trials are scheduled for completion in early 2007 and are to establish the usability of SMT outputs, particularly with respect to the requirements of Network Rails standard NR/SP/TRK/001- inspection and maintenance of permanent way.
The SMT currently operates on mainlines across south east territory of Network Rail as well as sections of the new Channel Tunnel Rail Link (CTRL) Line from Fawkham Junction to Dollands Moor.
The Plasser track geometry measurement system has demonstrated consistently high levels of accuracy, repeatability and reproducibility and has therefore been granted product acceptance from Network Rail’s professional head of track. It is intended that SMT will provide the majority of track geometry measurement in south east territory from 2007/08.
The rail profile system, manufactured by KLD Labs, has achieved the standards of accuracy, repeatability and reproducibility required by Network Rail for product acceptance. Product acceptance was granted by Network Rail’s professional head of track in April 2006, following detailed analysis by Network Rail wheel-rail interface engineers. This system has performed very successfully under trial conditions. On the Guildford track maintenance engineers section this system is replacing manual sidewear measurement on all SMT recorded routes. Many of these routes are heavily curved making sidewear recording difficult by requiring significant site lookout protection. It is anticipated that the automated sidewear measurement procedure will be extended to the remaining SMT routes before the end of 2006, delivering significant safety and cost benefits.
The SMT is equipped with video capability, recording forward facing (4ft and Panoramic) and overhead line. Network Rail has additionally purchased a video system to view the conductor rail which carries the traction current on much of the former Southern Region. This is the first train ever equipped with such a capability. The video has been useful for a variety of activities, including annual surveys, vegetation checks, pre-site planning, track renewal proposals and providing engineers with the current picture of the track condition.
The conductor rail measurement system measures the conductor rail profile, relative position to the running rail, ramp angle and distance, and conductor rail temperature. The vehicle is also equipped with a video monitoring system, and thermal imaging video. These systems have been added to the SMT by Network Rail, significantly enhancing the vehicle’s capability. They represent a significant step forward for conductor rail monitoring.
The Fraunhofer manufactured overhead line measurement system measures height, stagger and mast position of the overhead line. The system will be trialled on the Anglia area from October 2006.
Data has been delivered specifically for maintenance trials since April 2006 enabling area maintenance engineers to view the various SMT outputs and assess data usability for a variety of maintenance tasks. The availability of this information is playing an important part in the effective planning of inspection and maintenance activities and is removing the need for many of the current manual inspection and measurement activities.
The advances made to date by Network Rail in the development of cutting edge technology in the fields of track inspection and maintenance, are ensuring that the company is a world leader in this field. We will continue to build on this position to deliver a railway fit for the future.
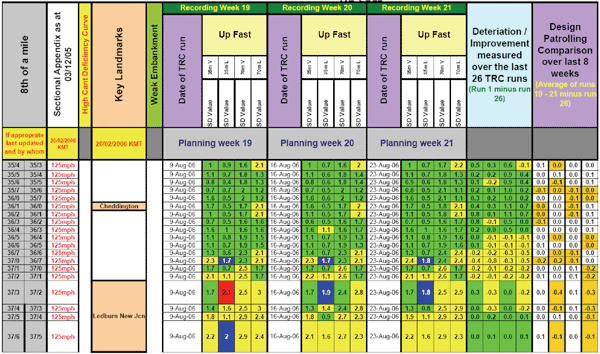
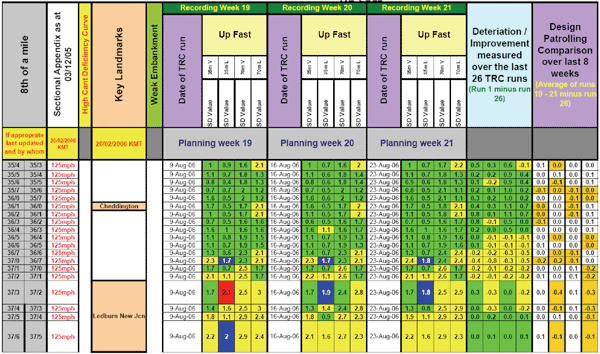
Figure 1: Information from each run is plotted adjacent to each other allowing deteriorations over both 8 and 26 weeks to be plotted
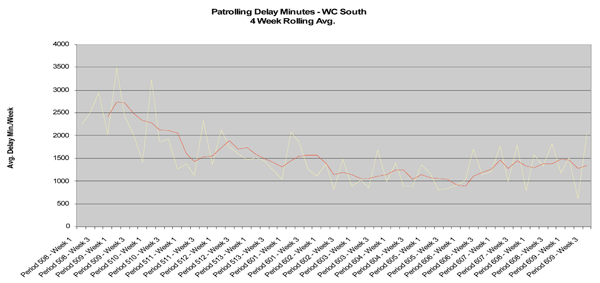
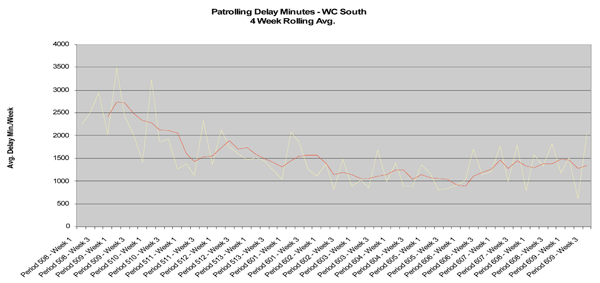
Figure 2
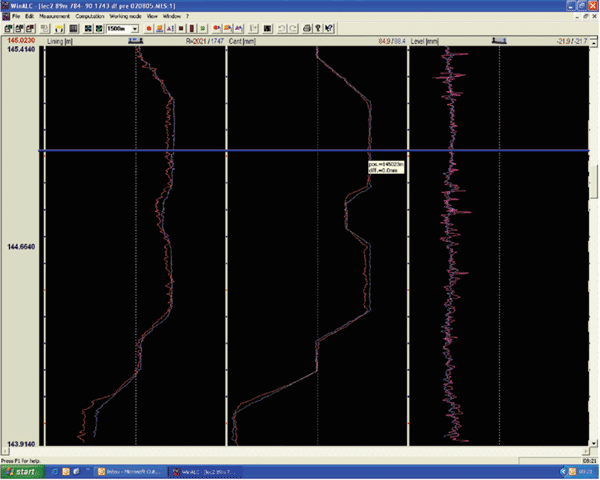
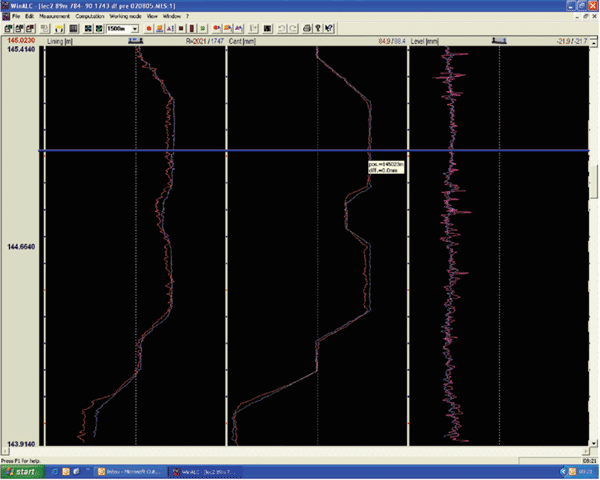
Figure 3: A typical geometry file output