Development of freight wagons
Posted: 31 May 2005 | | No comments yet
European freight wagon designers have for a long time been guided by the principle that wagons must be capable of being used on all standard-gauge railway networks in Europe. For more than 50 years the International Union of Railways (UIC) has standardised many freight wagon components – in particular their running gear, brake system and the draw gear1, 2. This is in order to achieve interchangeability between the various freight wagons from different origin and ownership running through Europe. The standardisation is necessary for the interfaces between different wagons in a train, i.e. brake systems and the draw gear, but is less evident for the running gear, i.e. bogies and single-axle suspensions.
European freight wagon designers have for a long time been guided by the principle that wagons must be capable of being used on all standard-gauge railway networks in Europe. For more than 50 years the International Union of Railways (UIC) has standardised many freight wagon components – in particular their running gear, brake system and the draw gear1, 2. This is in order to achieve interchangeability between the various freight wagons from different origin and ownership running through Europe. The standardisation is necessary for the interfaces between different wagons in a train, i.e. brake systems and the draw gear, but is less evident for the running gear, i.e. bogies and single-axle suspensions.
European freight wagon designers have for a long time been guided by the principle that wagons must be capable of being used on all standard-gauge railway networks in Europe.
For more than 50 years the International Union of Railways (UIC) has standardised many freight wagon components – in particular their running gear, brake system and the draw gear1, 2. This is in order to achieve interchangeability between the various freight wagons from different origin and ownership running through Europe. The standardisation is necessary for the interfaces between different wagons in a train, i.e. brake systems and the draw gear, but is less evident for the running gear, i.e. bogies and single-axle suspensions.
Although these goals and principles have considerable advantages in cross-border traffic, they also keep back the development of freight wagons and – indirectly – rail freight competitiveness. The running gear and its performance is particularly important where there is a need for fast overnight transport across longer distances, and/or improved transport qualities from a load damage point of view.
Most of the designs of running gear used on today’s freight wagons in central, northern and western Europe originated in the 1950s and 1960s. The running gear is either two types of bogies – the link bogie or the Y25 bogie – or single axles with link suspension.
To increase competitiveness of freight traffic on rails, it is desirable to increase axle load and sometimes also speed. This would – at least at some operational conditions with standard running gear – mean to exceed existing limits for ride quality and wheel-rail forces.
Just as important is to improve ride qualities in order to reduce damage to transported goods at ordinary speeds and thus being able to attract customers that require transport services for sensitive finished goods.
The European standards concerning the necessary ride qualities for freight wagons are quite liberal regarding the levels of vibration. For example, in a frequency range of 0.4 to 10Hz the permissable accelerations on the wagon floor are 5m/s2 in vertical direction and 4m/s2 in lateral3. This is for a brand new two-axle freight wagon to be tested under intentionally well-defined conditions. Due to wear and varying operational conditions the real performance may deteriorate and become worse. For high frequencies (above 10Hz) there are no requirements at all.
It is easy to understand that such vibrations may cause damage on certain types of sensitive goods, not being extraordinarily well packaged for rail transport. Due to the high combined vertical and lateral vibrations there is risk of load movement on the floor of the wagon, which would ultimately lead to load damage.
General rail freight development in Sweden
From the early 1990s a large government funded rail investment programme – in particular in the Swedish rail infrastructure – has been in effect. Actually, during the years 2004-2015, a total of almost ?12 billion is envisaged for infrastructure improvement, according to current parliament decisions. This is part of the policies for a future of ‘sustainable’ development in the transportation area.
Rail traffic in Sweden declined for many years in the 1970s and 1980s. Since the mid-1990s it has been catching up again and reached new record levels during 2002-2003, both in passenger and freight transport. In 2003 the total rail freight transport volume was about 20 billion tonne-km.
Today the general rail freight traffic in Europe is run at maximum speeds of 80-100km/h with a maximum axle load of 22.5 tonnes. This is also the case for much of the general wagonload freight in Sweden, in particular for the border-crossing freight, where the European standard is often necessary to maintain.
However, just part of the Swedish rail freight is cross-border traffic. Of the total transport volume (in tonne-km) 64% is entirely domestic and an additional 10% is iron ore transport in dedicated block trains in exchange with Norway. Thus, approximately 3/4 of total rail freight volume – about 15 billion tonne-km – is either domestic or is run in special cross-border block trains. In all these domestic or domestic-like freight operations general international standards are not mandatory.
Although the Swedish rail traffic may be more ‘domestic’ than in most other countries in Europe, there is usually a considerable portion of ‘domestic’ rail freight in most other countries as well, except the smallest. Further, in many cases of cross-border operations it is possible to reach mutual agreements for non-standard equipment or practices to be used.
A number of undertakings have been introduced during the last 5-10 years in order to increase the competitiveness of rail freight in Sweden. Besides the improvements due to increased capacity of the rail infrastructure, the following should be pointed out:
- Increased axle load (25 tonnes) on many trains and lines for heavy freight transport
- A larger loading gauge, rectangular with a height of 4.83m and a width of 3.6m, on certain lines where it is needed
- 30 tonnes of axle load is currently under introduction on the ‘Iron ore line’ in the most northern part of Sweden in exchange with Norway
Many domestic trains are today running with the higher axle load than the usual limit of 22.5 tonnes, and/or with the larger loading gauge. Some more advanced special freight train developments should also be mentioned:
- Mail trains with special two-axle freight wagons running at speeds up to 160km/h, covering the main cities in south and mid Sweden
- Special wagons for paper roll transportation, allowing fast and convenient loading and unloading as well as reduced damage of the paper rolls
Both the mail trains and the special-purpose paper wagons are equipped with a new type of single-axle running gear providing improved ride qualities. In addition, on the mail trains the speed is extraordinarily high. Both types of trains are run by the freight operator Green Cargo.
Research for improved competitiveness
Part of the Swedish programme for improved competitiveness of the rail sector is the programme for research and development. This programme is administered by the Swedish National Rail Administration (Banverket). During 2005 this programme amounts to about ?10 million in funding. In addition the rail industry and other government agencies also contribute to research.
Technical research is performed at a handful of Swedish research institutes and technical universities, of which KTH (Royal Institute of Technology, Stockholm) is the largest. One of the themes is ‘Efficient train systems for freight transportation’ covering economics, management and technology. An important issue is how to improve freight wagons and their running gear.
Firstly, the project aims to study and learn how freight wagons behave dynamically on track. This is made for the three European types of standardised running gear as well for novel designs.
The second step is to analyse and test possible improvements in the designs, in particular, the standardised designs now dominating European rail freight traffic.
A third part of this project is to investigate the causes of track deterioration and to propose mathematical models for prediction of deterioration.
Improved ride qualities and running gear
It would be possible to achieve better dynamic performance of freight wagon running gear in two ways:
- By using novel designs
- By improving the current standard designs
For domestic traffic in closed loops the first way may be the most attractive, in particular on new freight wagons. For international traffic with higher demands on interchange and standardisation, as well as for improvement of a great number of existing freight wagons, the second way would be preferable.
Freight wagons with link suspension are the most common type of suspension for freight wagons in Europe today. It has principally existed for more than 100 years. Link suspensions are used on the so-called G-type bogie, as shown in Figure 2. Link suspensions are also used in single axle running gear. Both are standardised by the UIC.
The link suspension is a quite simple and robust design. It occupies a modest amount of space vertically and laterally. Stiffness and damping are both provided by one system and are intended to be proportional to the vertical load of the axle box, i.e. the ride qualities are intended to be independent of the actual wagon load.
The research at KTH has concentrated on three areas:
- Tests on link suspensions
- Dynamic simulation of freight wagons with a variety of suspension and loading parameters on various track, also including different means of improvement
- On-track tests with improved link suspension bogies and single axles
The first issue in the research programme is to learn and explain how link suspensions really behave and to investigate their characteristics, i.e. forces versus displacement in the different directions of suspension. The actual testing includes both stationary tests on wagons as well as dynamic laboratory tests4. Figure 1 shows examples of the lateral characteristics as found in stationary tests.
We observe the typical characteristic with a considerable hysteresis, which provides an energy dissipation, i.e. a damping of the motions in the suspension. However, the variation in characteristics between different cases is significant. The variations are found to be even larger in the laboratory tests, in particular the hysteresis damping diminish to very low values after a few hours of motion.
The standardised running gear with link suspensions exhibit quite fierce dynamic motions, as shown in the generous allowance in the UIC rules. The large variations in characteristics introduce an additional risk for degraded ride qualities, although part of these variations is certainly included in the allowances.
Another part of the KTH research programme was to investigate – by means of so-called ‘multi-body simulations’ (MBS) – how link suspended bogies and single axles behave dynamically under different conditions. This was made by the multi-body railway code GENSYS. A large variety of simulations were performed with various vehicle parameters and loading conditions at different speeds and track quality5, 6. In particular, the possibility of improving ride qualities by means of supplementary dampers was investigated, by adding friction dampers as well as hydraulic dampers. Hydraulic damping was found to be the most efficient method to generally improve ride qualities, in particular at speeds of 130km/h and above.
The third step was to perform on-track tests with freight wagons, equipped with various supplementary hydraulic dampers, including the ‘null case’ with no additional dampers at all. One four-axle wagon with two link suspension bogies was tested, as well as a two-axle wagon with link suspended single axles. Tests were run at speeds up to 160km/h, occasionally up to 170km/h, in loaded and tare conditions. Tests were performed by KTH in cooperation with the operator Green Cargo and the testing company Interfleet Technology. The wagons were rebuilt by K-Industrier and Dellner Dampers supplied the dampers.
For testing purposes the wagons were equipped with various dampers at different locations as shown Figure 2; secondary yaw dampers, lateral dampers (working partly in the vertical direction as well) and longitudinal dampers. Not all of these dampers are always necessary for improved ride qualities, in particular not at the lower ordinary speeds. A total of 12 dampers (sometimes just four of them) seem to be sufficient for a four-axle wagon, while a two-axle wagon usually needs six additional dampers. The final evaluation of the tests, as well as the final tuning of damper characteristics, is underway.
In Figure 3, an example of three records of measured lateral acceleration at the carbody floor in a two-axle wagon is shown. The speeds are 100 and 160km/h. The improvements of ride qualities are quite substantial.
Conclusions
A number of activities for the development of rail freight transportation and freight wagons have started in Sweden during the past 5-10 years.
The Royal Institute of Technology performs extensive studies to learn how freight wagons behave dynamically in interaction with the track. The possible improvements in freight wagon ride qualities are also studied. This is important for the possibility to carry sensitive goods without high risk of load damage. Sometimes it is also important to increase speeds due to the need for overnight transport over long distances.
By the research made so far, it is found as being possible to substantially improve ride qualities on existing freight wagons with European standard running gear, both on bogie wagons and on two-axle wagons. This can be made by adding a number of hydraulic dampers to the ordinary designs. This is an alternative to completely new designs, in particular in international freight operations with special needs of interchange and standardisation.
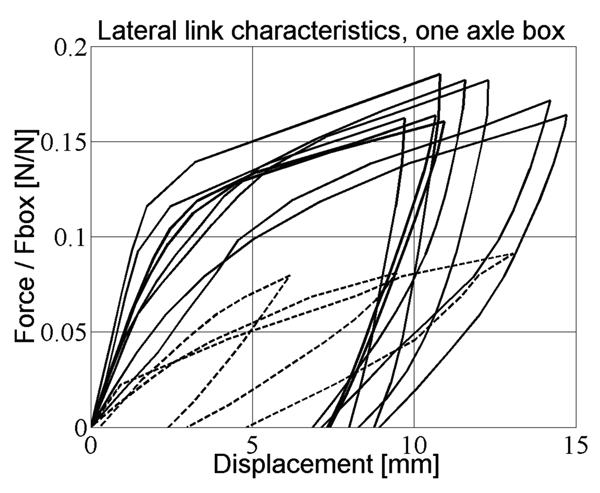
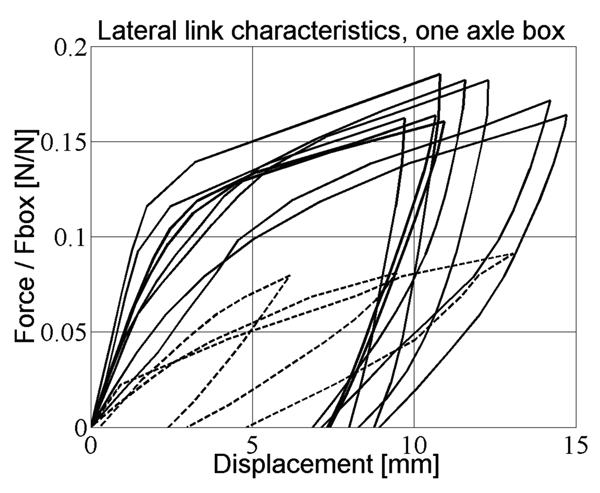
Figure 1: Characteristics of the link suspension have considerable variation between different tests on different wagons. The results above are all from stationary tests in the lateral direction. Dynamic laboratory tests under better defined conditions exhibit a wider variation.
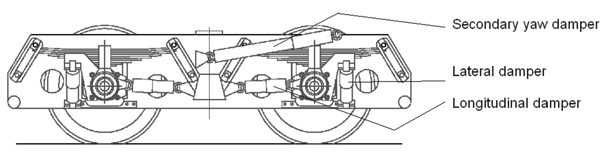
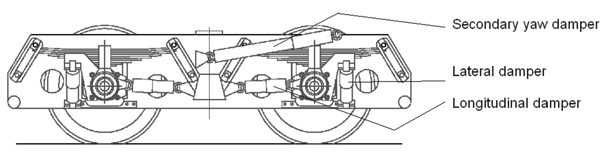
Figure 2: Improved link suspension bogie, equipped with a full damper configuration. In most practical cases a lesser number of dampers are needed.
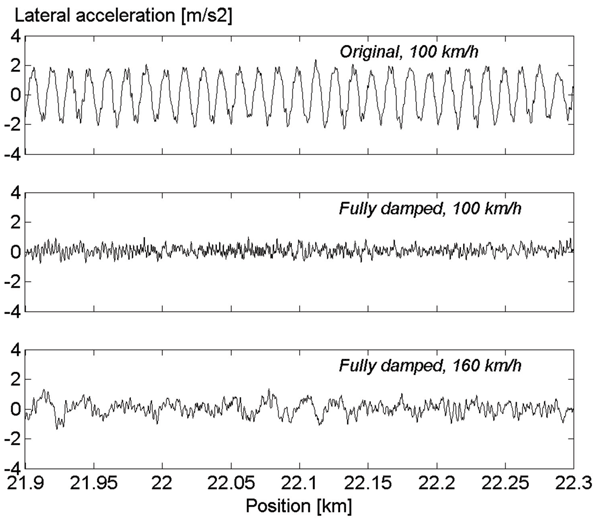
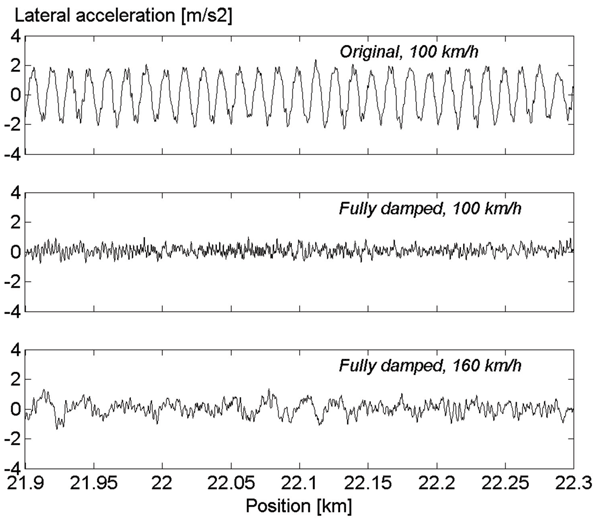
Figure 3: Improvements in ride quality are usually very substantial. Example, on-track tests with two-axle wagon. Upper graph: Lateral dynamic accelerations as measured at the carbody floor on the 'original' standard two-axle wagon at 100 km/h. Middle graph: lateral acceleration with 6 additional dampers at 100 km/h. Lower graph: Lateral acceleration with six additional dampers at 160 km/h.
References
- UIC Leaflet 510-1. Wagons – Running gear – Normalisation, 9th edition, 1995.
- UIC Leaflet 517. Wagons – Suspension gear – Standardisation, 6th edition, 1985.
- UIC Leaflet 518. Testing and approval of railway vehicles from the point of view of their dynamic behaviour, 2nd edition, 2003.
- Jönsson P-A.: Modeling and Laboratory Investigations on Freight Wagon Suspensions, with respect to Vehicle-Track Dynamic Interaction, TRITA AVE 2004:48, Licentiate Thesis, Division of Railway Technology, Royal Institute of Technology (KTH), Stockholm 2004..
- Stichel S.: Running behaviour of railway freight wagons with single-axle running gear – A parametric study, TRITA FKT 1998:40, Division of Railway Technology, Royal Institute of Technology (KTH), Stockholm 1998.
- Jönsson P-A., Andersson E.: Influence of Link Suspension Characteristics on Freight Wagon Lateral Dynamics, 6th International Conference on Railway Bogies and Running Gear, Budapest, Hungary, September 13-16, 2004.