The Internet of Rail: How to transform data into asset management improvements
Posted: 13 February 2018 | Christophe Sanguina, Pierre Dersin | No comments yet
Ahead of Global Railway Review’s webinar in association with Alstom on 15 February 2018, we posed some questions to Christophe Sanguina, Director of Marketing for Services at Alstom, and Pierre Dersin, Prognostics and Health Management Director at Alstom.
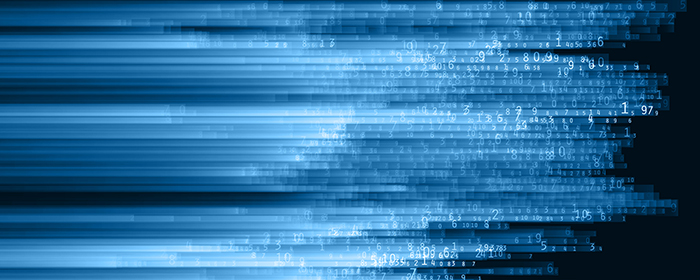
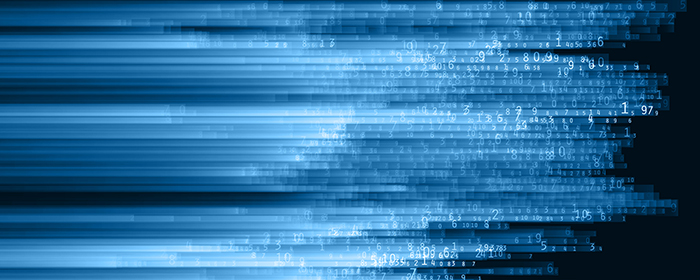
What can we expect to learn during the webinar?
Sanguina: The Internet of Things (IoT) is opening up a wide range of possibilities. We now possess increasingly powerful computers, smaller sensors, much faster transmission, greater storage capacity, and all this at lower costs. The main challenge for us today, and in the future, is therefore channelling all this data to improve performance of the rail system and, in particular, the way we manage assets.
HealthHub™ is Alstom’s answer to these challenges. With HealthHub™, maintenance tasks are based on the actual condition of the equipment. The aim is to anticipate precisely when tasks should be performed: Before any failures occur, but not too early either; only when needed.
Not only does this mean we save on not having to perform unnecessary activities, but it also prevents service being affected by failures, enabling our teams to schedule only the necessary tasks. HealthHub™ makes it possible to identify the components that need to be repaired or changed without taking the train out of service. All this allows us to have a pit-stop approach: Everything is ready when the train arrives at the depot, enabling the maintenance staff to work more quickly and efficiently.
How does HealthHub™ work?
Dersin: The purpose is to translate field data into decisions and actions through the development of Prognostics and Health Management (PHM) algorithms. The first stage is to gather the available data by means of our capturing tools: TrainTracer, TrainScanner, CatenaryTracer, TrackTracer and Motes. The second stage is to transmit the data to the server, which can be challenging in very isolated areas that often lack telecom networks with sufficient bandwidth. The third stage is data hosting and analysis – analysis being the most important element as that is what transforms mere data into valuable information. This is the brain of the system. Finally, there is the visualisation of analytics’ outcomes: The actual results on a user-friendly interface with actionable information and, if requested, a set of rules able to trigger tasks. This whole process enables the assets (trains, components, infrastructure and signalling) to ‘talk’ to the maintainers. HealthHub™ is the language the maintainers use to communicate with the machines.
What makes HealthHub™ stand out in the market?
Sanguina: There is a lot of talk about predictive maintenance in the rail market but very few players have actual experience to show for it. HealthHub™ is already being used as part of several projects worldwide: In the UK for the past 12 years, but also in Italy, France, USA, Poland, South Africa, Australia, Chile and others. With HealthHub™ we have experience in rolling stock (monitoring over 1,400 trains from 60 different fleets), signalling and infrastructure. We are improving maintenance tasks, reducing preventive and corrective maintenance labour, reducing material consumption, reducing downtime of assets and improving the lifecycle cost.
Related topics
Digitalisation, Infrastructure Developments, Passenger Experience/Satisfaction, Technology & Software