The influence of the whole lifecycle cost and digitalisation on the design of running gear
Posted: 19 July 2017 | Thomas Graetz (Siemens) | No comments yet
Modern running gear has to fulfil a multitude of requirements. As well as the diverse functional, operational and relevant environmental requirements, operational ruggedness combined with high availability is also expected. Thomas Graetz, Head of Bogies at Siemens, writes that aside from the technical aspects, the commercial influence of this key component is also of crucial importance and bogies have a significant effect on the whole lifecycle cost of a rail vehicle over its estimated service life of 30-40 years.
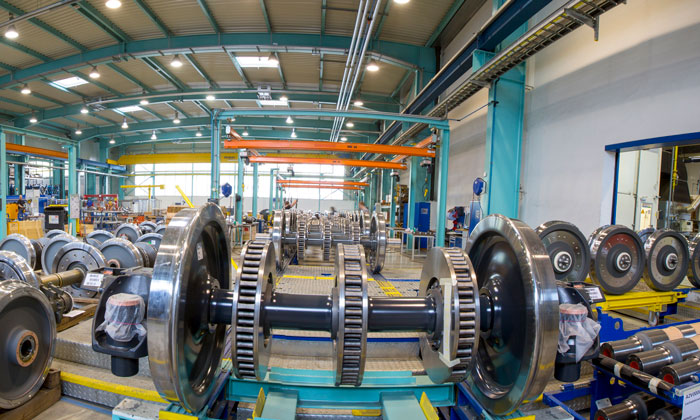
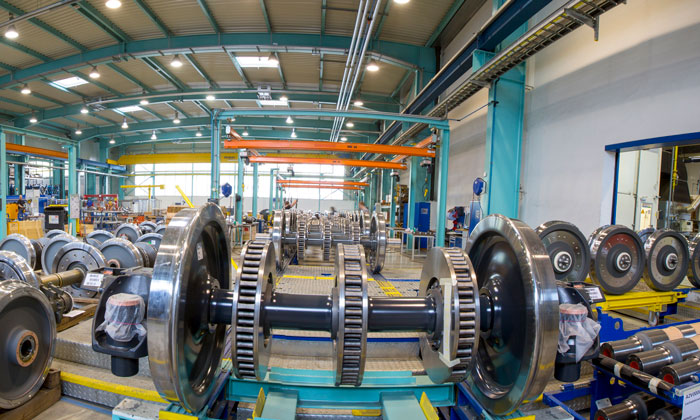
In our experience, the operating and maintenance costs of the running gear make up around 40 per cent of the total operating costs of a train – the biggest expenditure being on wheelsets and brakes. The main cost items of the running gear that can be influenced are as follows:
- Investment costs (unit cost and non-recurring costs)
- Energy costs
- Cost of maintaining the vehicle
- Cost of maintaining the infrastructure.
Not infrequently, the requirements of these cost blocks are mutually contradictory. Therefore, one of the tasks of development is to optimise these cost items and resolve contradictions.
Developments of the networks
The railway industry is constantly working toward optimising these highly stressed vehicle components. Railway and network operating companies place quite different requirements on the railway industry.
Some networks are increasingly developing toward high-density traffic with higher loads and service frequencies. The industry has to offer high reliability whilst achieving appropriate accelerations, passenger boarding and alighting times, as well as high loads.
In Great Britain and Switzerland, the emphasis is on the maintenance costs of the infrastructure; the infrastructure companies – Network Rail and SBB – demand from the rail operators the lowest possible wear on their superstructure. The network operators reward the use of track-friendly, low-wear bogies with lower track access charges (known in Great Britain as the VUC – variable usage charge), and penalise operators still using old running gear with higher usage fees. The introduction of similar billing models is also being discussed in other countries. However, it may be some time before this is introduced throughout Europe.
Another issue is the increasing amount of cross-border traffic, which requires the running gear to accommodate train protection systems for several different countries. From the outset, the design of bogies has to allow space to install the associated antennas and also take into account their combinatorics. Specific national conditions for accessing the network must also be observed.
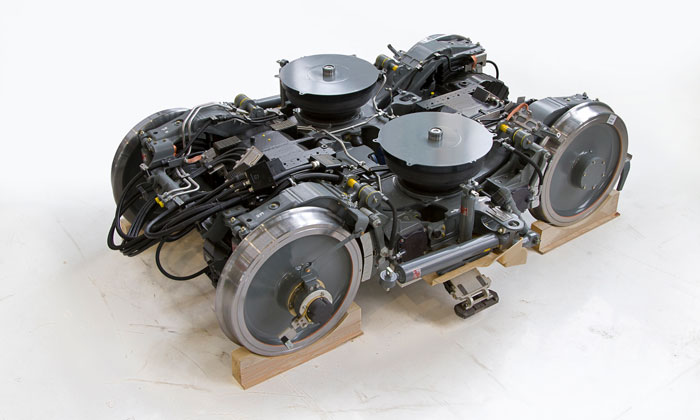
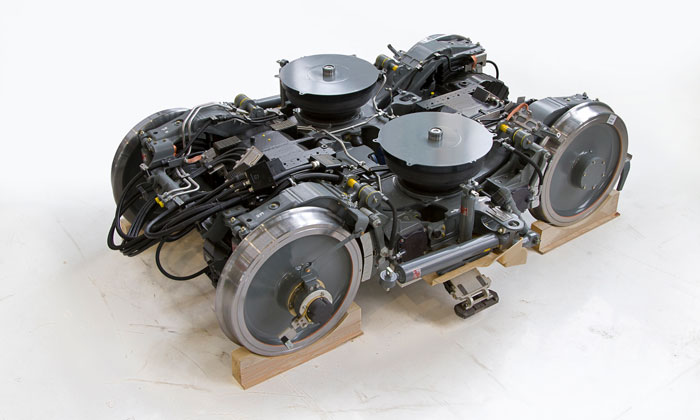
Innerbearing bogie SF 7000 (Thameslink)
Design to Value
The decisive factor in the decision to invest in a rail vehicle is the added value it could generate for the operator. Like all subsystems, all the cost blocks mentioned here have to be addressed when it comes to the running gear.
The unit costs are optimised in the product development process using target costing methodology. Efficient production is just as essential as effective supplier management. Development costs can be limited by creating platforms that incorporate planned product variants, which still serve a market with disparate requirements.
Probably the most powerful lever in optimising energy costs lies in lightweight construction. Lightweight construction approaches are followed, for example, in respect of the inboard bearing concept. However, the use of higher strength materials and optimising components by using modern methods and tools (for example, topology optimisation programmes) also contribute toward success. Another factor in the high-speed segment is that of aerodynamic design.
To achieve low maintenance costs, the product has to have a maintenance-friendly design. Replacement times have to be minimised and the service lives of the wearing components have to be optimised and synchronised. The target is for them to last for longer periods of time.
Successful products that generate these added values are generally created during extensive pre-developments of concepts and technologies. In this case, it is not sufficient to optimise the running gear alone – on the contrary, comprehensive concept studies of powered bogies. This significantly lightens the wheelsets. They are fitted with easily accessible tread brakes that slow the vehicle in conjunction with the generative braking effect of the motor. Only the
non-powered bogies, which are also considerably lighter, still have axle-mounted disc brakes.
The lighter and curve-compliant bogies have another side-effect, which helps to reduce the track access fees in Great Britain: The so-called T-Gamma wear number has been reduced by 75 per cent. This significantly reduces the wear on the rails and wheels, and so substantially reduces the whole lifecycle cost.
These technological approaches have been systematically further developed in the SF 7500 running gear. This running gear is used in the Mireo – the latest multiple unit generation from Siemens. Jakobs variants were also developed for the innovative concept of a long, articulated train which provides full operational performance with a reduced number of bogies. The running gear is suitable for higher loads and the mounting of magnetic track brakes.
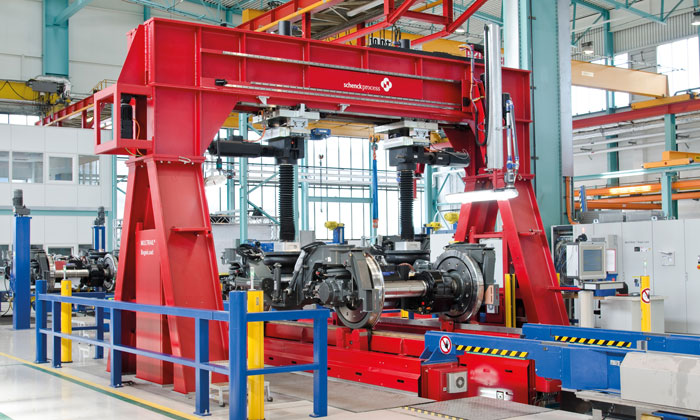
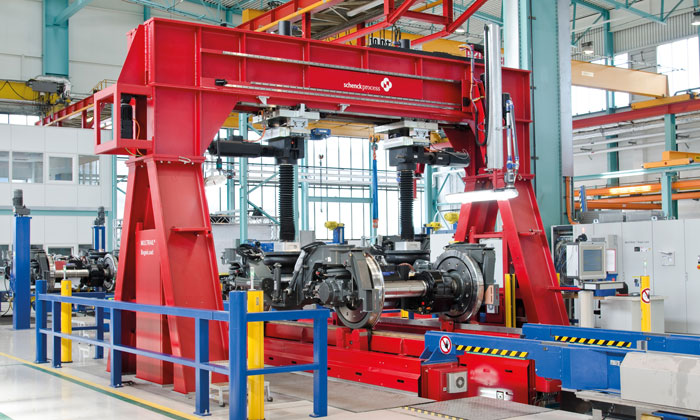
Bogie test rig
Digitalisation and simulation
Digitalisation also affects the product development and end product in the running gear. The use of perfected simulation methods in the design process enables the later product properties to be checked and optimised at a very early stage in the development process, and prepare the product as well as possible for industrial and partially automated production. Simultaneous engineering enables development times, and thus the time-to-market to be minimised.
Many components influence each other in the development of bogies and wheelsets. The use of simulations helps to save time and money before a mechanical trial takes place. It is not only the coordination and system integration that requires precision, but also other complex issues need to be safeguarded and coordinated with one another. These include mainly the following:
- Vehicle dynamics
- Mechanical strength of all structural assemblies
- Functionality of the braking system
- Simulation of the production.
Dynamic forces, masses, possible spring travels, required rigidities and the associated types of coupling elements, the wheelsets, the running gear frame concept and the interfaces to the car body all contribute to the CAD model. The strength and elasticity of the design is checked and its behaviour in operation is simulated by the finite element method. These results then flow back into the design. In addition, the simulated braking situations, the forces and temperatures they generate, as well as the system requirement specifications also have to be taken into account. Given that many properties influence other
properties, the digital development of a bogie is an iterative process.
Not least, the geometry of a bogie is oriented toward the possibility of optimally automating its manufacture. Welding robots handle a significant portion of production in the Siemens Competence Centre for Bogies in Graz, Austria.
At the same time, the designers are simulating the accessibility of those components that have to be checked visually, maintained, and replaced both preventively and correctively. Basically, access should be possible without the need to dismount other parts.
The experience of the engineers with earlier simulations – and the running gear that resulted – enables a reliable assessment of the digital model to be made at an early stage. This is discussed and optimised with an extensive range of experts from production, operation and maintenance, as well as, of course, cost calculation experts.
The first running gear will not go into passenger operation until the ‘virtual development’ has been completed and practical fatigue tests have been made on all relevant parts. The load assumptions made during the development and component tests are validated in extensive measurement runs before the vehicle is certified.
Digitalisation is also gaining importance in the production phase. ‘Industrie 4. 0’ intermeshes the means of production with modern information and communication systems.
Real-life examples: Diagnostics and condition-based maintenance
Bogies have already been monitored by sensors for around 20 years. Electronic obstacle and derailment detection is one of the essential extended functions of automated metro trains. Over the course of approximately the last 10 years, an ever increasing number of sensors have been installed in the bogies of locomotives and multiple units to detect the condition of components such as wheelsets, gear units, motors, and coupling elements. The data are collected and evaluated by diagnostic systems in the vehicle. A large amount of operational data is continuously and regularly passed on to the manufacturers’ service specialists – for example, in the case of Siemens to the Rail Support Centre – where it is stored and analysed. On the basis of this data, maintenance tasks and schedules are generated, which are then made available to the workshops. This means that when a train comes into the workshop, the priority tasks
and work steps are already known. As a result of extensive interaction with manufacturers, operators and workshops, almost 100 per cent availability can be
achieved. In the event that further major work is required on bogies, then the bogie is replaced and repaired.
This procedure reduces the maintenance costs, because firmly scheduled regular work can be performed more flexibly and the vehicles are not withdrawn from service unnecessarily. Checking and maintaining components on the basis of sensor data enables failures in service to be largely avoided. At the same time, the real service lives of the wearing parts can be exploited. They are not maintained or replaced at regular intervals but according to the actual state of
the components.
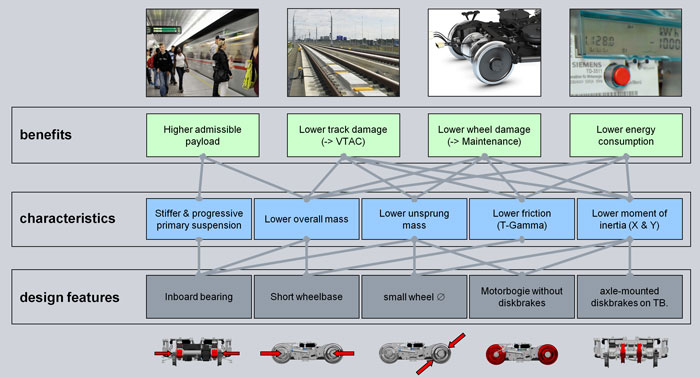
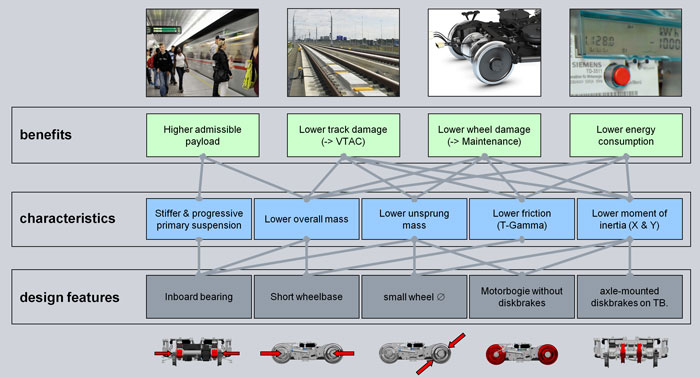
Relation of customer benefits and bogie design features
Digital Bogie 4.0
In future, scientific data analyses will allow predictive maintenance, which enables very high reliability and even more cost-effective maintenance and servicing. As the first company in the railway industry, Siemens runs a Data Analytic Centre, in which scientists from many disciplines, mathematicians, data analysts, and engineers analyse the patterns in the accumulated operational data of the vehicles. The aim is to reliably predict when and under which conditions a component will fail and when a repair or intervention is absolutely necessary. If a particular vibration pattern occurs in a specific frequency range, specially developed algorithms can predict whether, for example, a bearing or a damper will fail within a foreseeable period of time.
The prediction, when and how a response must be made to the detected phenomenon, must hold true with high probability, and could, for example, state that a bogie can still run for a few thousand kilometres before a certain repair becomes essential. However, it could also mean that a specific component needs to be replaced as soon as possible, before the vehicle breaks down. This therefore enables the service lives of wheel treads, gear units, brake discs and other components to be calculated – in each case, with the aim of only maintaining the vehicle when it is necessary, thus avoiding unnecessary down time.
As a rule, the vehicles and track are checked separately. Measuring vehicles check the condition of the track. To a certain extent the condition of the track can also be recorded and evaluated by sensors in the bogies of conventional trains recording the interaction between wheelset and rails. This data can also document changes in the condition of the line, which would otherwise only be checked by measuring vehicles at infrequent intervals.
However, a bogie sensor system will not generally replace the use of measuring trains within the foreseeable future. Nevertheless, the interaction between wheelsets, dampers and the track can help to reveal weak points in the track, such as at points, and offer the operator added value.
Overall, the Bogie 4. 0 has many advantages for the operator in terms of whole lifecycle costs. They include the following:
- Higher availability of the vehicles
- Consequent savings, as fewer vehicles are required
- Lower maintenance costs by avoiding unnecessary inspections
- Lower space requirement in the workshops
- Replacing components only when necessary, which can be scheduled predictively.
The diagnostic possibilities of future bogie generations will improve the competitiveness of the operators and directly affect the operating and maintenance costs over the entire service life of a vehicle.
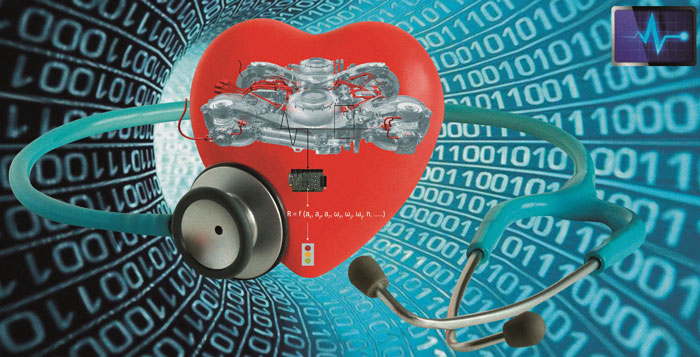
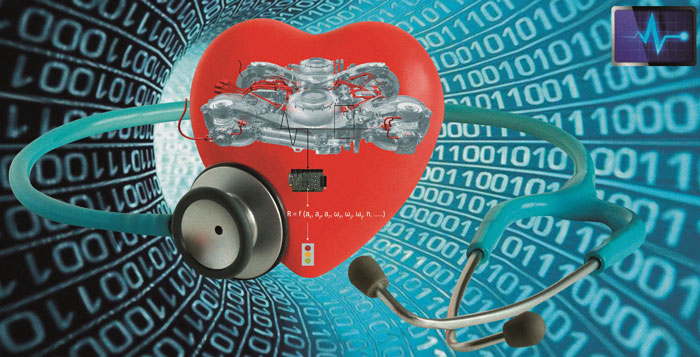
Bogie diagnostics
Specific requirements
All recent running gear developments take into account the aim of reducing the whole lifecycle cost. There is pressure across all segments to further optimise manufacturing costs. Depending on the type of vehicle, there are other aspects to which special attention is given.
Three and four figure numbers of locomotives are seldom ordered, but rather smaller batches as and when required. Therefore, all manufacturers are committed to platform concepts and modularisation in order to offer and produce the desired equipment variants economically. Bogies are therefore developed as modules for the required performance classes and gauges, which – as is the case with Siemens Vectron – do not require any significant design expenditure after ordering.
Another specific task is to integrate the train protection systems for various country corridors.
The top priorities for trains for regional passenger services are maintainability, lightweight construction, and low energy consumption. Relevant to the customer are the ride quality and the capacities of multiple units and passenger cars. Track friendliness is extremely relevant, but it is currently handled very differently in the country-specific invitations to tender. The ease-of-movement in curves, as well as the optimisation of wheel and rail wear, are therefore
currently very important goals.
The whole lifecycle cost is evaluated differently for high-speed transportation. In this case, reducing the unsprung mass of running gear has high priority (on ballasted superstructure but not on ballastless track). The maximum speed at which high-speed transportation is expedient is also a subject of discussion. Some are of the opinion that operation above approximately 250km/h is uneconomic; quite rightly citing the disproportionate increase in energy consumption and the issue of noise. The answer lies in substantially improving the aerodynamics of the whole train. This enables the installed tractive power in the vehicle to be held at an acceptable level. Cladding the running gear can make a substantial contribution to reducing the aerodynamic resistance. Furthermore, fully enclosing the running gear also reduces the propagation of sound. We are convinced that future high-speed vehicle platforms will also be capable of economic operation at speeds above 300km/h, and therefore enable the train to hold its own in the intermodal competition with the airplane.
Conclusion
The design of the running gear affects the whole lifecycle cost. In turn, the demand for low whole lifecycle costs affects the design of the running gear. The weighting of whole lifecycle costs in respect of an award is very different in the diverse invitations to tender. Roll2Rail, a European research programme in which Siemens is heavily involved, is attempting to find uniform evaluation criteria for the railway industry.
A running gear design must be able to address these numerous award criteria within its market segment. Despite all the differences, no manufacturer can avoid the necessity to continually optimise manufacturing costs throughout all parts of the value chain.
Investment in research and pre-development; taking the opportunities of digitalisation; and stable development, procurement and production processes are, as always, the best way of maintaining success in a changing market environment.