Optimisation of gearbox assembly lines towards innovation
Posted: 19 July 2018 | CAF MiiRA | No comments yet
CAF MiiRA, the only wheelset supplier that designs and produces its own gearboxes, has developed and installed new state-of-the-art assembly lines including a new concept of working. The new facility has been designed for assembling the most technically demanding gearbox types for all railway sectors, including high-speed, locomotives, commuters, metros and trams.
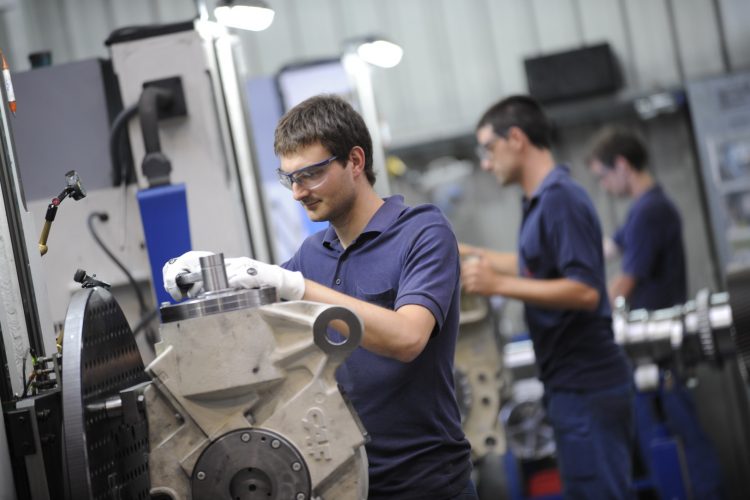
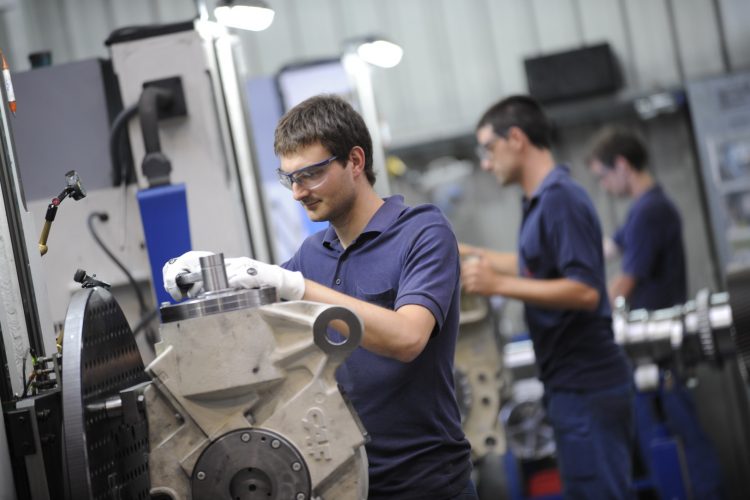
The new assembly lines, in combination with a highly experienced engineering team who offer technological innovation and smart, custom-made solutions, represent an investment to ensure even the most demanding customers are satisfied by improving production flexibility, product quality and reducing delivery lead times. The new gearbox assembly section is made up of four U-shaped lines with six mounting stations each. Each gearbox that comes off the line is finished, tested and ready to be assembled. This new assembly line design has been created to help meet the specific requirements of each customer, therefore assisting CAF MiiRA in meeting their goal of total customer satisfaction.
This approach, with high productivity, maximum quality and minimum delivery times, alongside the combination of lean management and manufacturing tools and different Industry 4.0 technologies, gives CAF MiiRA a more efficient production model that is focused on achieving results. By eliminating the intermediate stock, lead-time is greatly reduced. This also gives CAF MiiRA the ability to construct a wider range of products with shorter changeover times, leading to a reduction in delivery lead-time and thus proving it flexible and adjustable to customer demands.
To guarantee the highest quality, the system’s control of defects has been strengthened by situating the operator control at the assembly stations, meaning final inspection and testing occur on the same assembly line. Combined with its supply chain improvement project, which helps to sequence the supply of materials to the assembly line, CAF MiiRA’s optimised workflow has improved the efficiency of production and provided greater flexibility. The improvement is also due to the use of Industry 4.0 technologies such as ‘digital work instructions’. These allow any operator worldwide, across different production facilities, to work with the most recent version. Furthermore, a paper-based workflow is eliminated which helps to reduce mistakes.
All data on executed procedures, inspections, production losses or checklists are recorded in a central database which can be accessed from anywhere by anyone approved to do so. ‘Digital work instructions’ software is able to detect incorrect data entered by an operator or a machine, or any other nonconforming activity. Procedures are configured so that the operator is immediately alerted, who is then required to communicate the problem to a team leader or to fix the problem themselves following additional instructions. ‘Digital work instructions’ software also provides a high level of versatility among CAF MiiRA workers. Production data, overall equipment effectiveness (OEE) and any other KPI are monitored in real time, providing fast and accurate information and alerts to all employees that make decisions or prevent problems, in addition to implementing continual improvements.
This is very useful when defining, following and achieving clear objectives, focusing on producing value for the customer, working with standardised methods, encouraging proactive teamwork, suggesting improvements and using problem solving tools.
These improvements allow CAF MiiRA to offer complete wheelset solutions that are designed and manufactured in-house. This offers a comprehensive solution for gearbox requests, with the opportunity for the customer to have a single supplier for the complete package, assuring time and cost efficiency and facilitating the supply chain management.