High speed and high accuracy keep German trains moving
Posted: 5 May 2015 | Deutsche Bahn AG (DB AG) | No comments yet
With more than 33,000km of track, the German rail system Deutsche Bahn (widely known as ‘DB’) handles more than 26,000 passenger trains and 5,100 freight trains every day. While DB operates the majority of trains, trains from other countries also use the system’s tracks for trans-European freight and passenger traffic. Working closely with its technical contractors, DB uses detailed, precisely defined processes to provide safe and comfortable transportation.
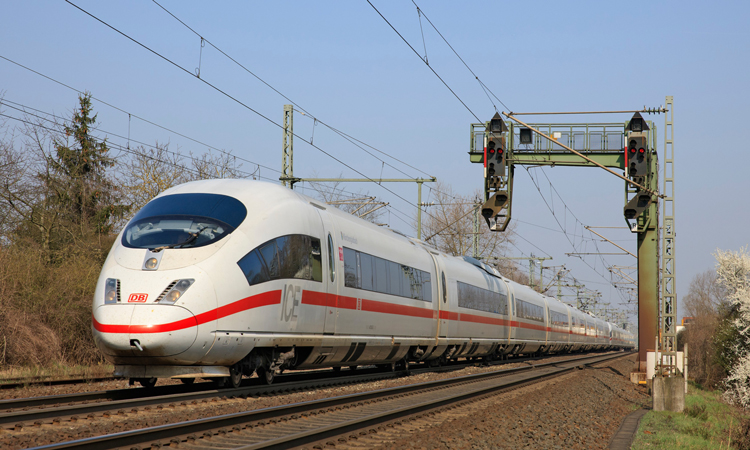
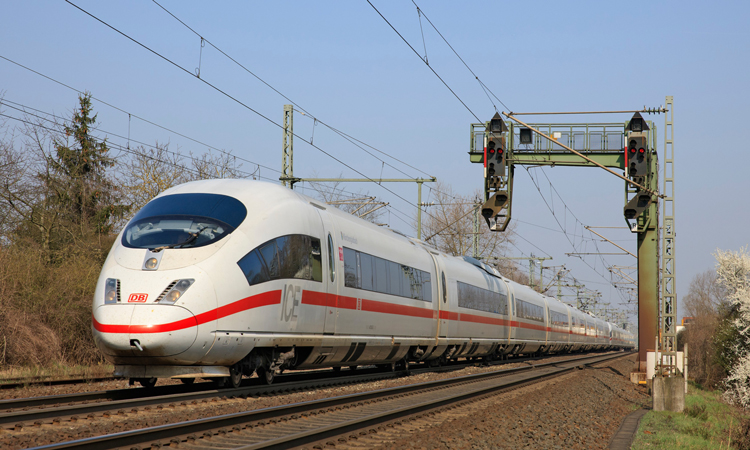
Credit: Deutsche Bahn AG / Georg Wagner
A clear path
Adequate clearance along the tracks is critical for safe passage for locomotives and railcars. Rolling stock varies slightly between countries, and certain railcars may be larger than those owned by DB. Some cars carry oversized cargo, which may exceed the normal railcar parameters. In addition, the trend to larger cars and higher speeds puts additional demands on DB infrastructure. DB uses the concept of ‘clearance envelopes’ to define the space that a railcar can safely occupy as it passes any given location.
To help ensure safety and smooth flow, DB and its contractors conduct clearance surveys to locate and document constrictions, which occur when objects are close to the clearance envelope. Constrictions can occur at signs and signals, stations, bridges, retaining structures or walls, tunnels, and underpasses as well as congested areas in cities and industrial areas. DB also requires clearance surveys to be performed for all construction and modification work in track areas. Information from the surveys is kept in a centralised database called ‘LIRA’.
Traditional clearance surveys employ a large frame that acts as a reference for local coordinates. The frame is manually placed on the track at the location of a constriction and static photographs and photogrammetric methods provide measurements of the constriction related to the track centerline. While the approach produces suitable results, working with the frame on site can be slow and require additional staffing for measurement and safety.
Providing fast and flexible measurement
Frank Herzbruch, Owner and General Manager of Ingenieurbüro Herzbruch GmbH (IBH), recognised the need for rapid, accurate constrictions measurement. With offices in Schwelm and Roitzsch, Herzbruch’s company specialises in surveying for railway applications. IBH uses a broad range of Trimble technologies to support DB activities in engineering, construction, inspection and maintenance activities.
One of IBH’s most flexible tools is the Trimble® GEDO solution for precise track measurement and data collection. The GEDO solution is based on a track-mounted trolley equipped with sensors to measure odometry, cant, and track width (gauge). Additional sensors, such as Trimble GNSS receivers, prism target for Trimble S-series total stations or 3D scanners can be mounted on the trolley. Operated by one person pushing it along the track, the trolley and its instruments are controlled using a Trimble TSC3 controller or Trimble Tablet rugged PC running GEDO field applications. It can be easily removed and replaced on the track as needed to accommodate traffic. In the office, specialised GEDO software provides data processing, analysis, and exchange.
Herzbruch’s firm uses the GEDO Rec configuration to measure and document existing track, including 3D data for track location and profile. To support DB maintenance operations, IBH uses GEDO Vorsys to conduct pre-tamping measurements to feed precise track data to tamping machines and to conduct post-tamping inspection. Based on the performance of the GEDO system in these applications, Herzbruch decided to put the GEDO Scan solution to work in clearance surveys.
The GEDO Scan system consists of a Trimble TX5 3D scanner mounted onto the GEDO trolley. The scanner’s vertical axis is locked so that the scanner measures in a single plane. As the operator pushes the trolley along the track, the scanner captures a 3D point cloud tied to the track centerline. The Trimble scanner can measure more than 950,000 points per second with accuracy of ±2mm at a range of 25m. Data for cant, gauge, and distance along the track are also recorded.
The forward motion of the trolley and rotating scan beam produce a helical scan along the direction of the rail axis. The distance between measured points is controlled by the rotational speed of the scanner together with the forward velocity of the trolley. In normal operation the trolley moves at roughly 0.5m per second and the scanner works at 50Hz, producing point intervals of roughly 10mm along the track axis and 12mm at a 5m vertical distance. Herzbruch said that thin objects (such as signs oriented perpendicular to the track) can be challenging to measure. IBH solved the problem by rotating the scanner to measure in a plane at a 45o angle to the track axis. “Narrow objects can be recorded reliably even at normal pushing speed,” Herzbruch said. “They can very clearly be recognised in the point cloud at the evaluation stage.”
A key factor for track clearance assessment is the high relative accuracy of the system, which is provided by the laser scanner and the fixed mechanical movement of the trolley. Before using the scanning solution on a project, IBH conducted a test to verify its accuracy. They placed a series of targets along a section of track and measured their position using a Trimble S8 1-sec total station. Then they compared the results with data from the GEDO Scan system. The GEDO measurements agreed with the total station to within 4mm.
High performance confirmed
IBH then conducted a pilot project at a DB rail station at Leverkusen. They used the scanner to measure new and existing features along 900m of newly-constructed tracks. Potential constrictions included signals, a building, masts for signs and power as well as the station platform and its roof. The Trimble® GEDO system required only one person to complete the scan in less than one hour.
In the office, data from the scanner was loaded into Trimble® GEDO Scan software, which combined it with measured values from the trolley and track geometry to produce a 3D point cloud. Then the software applied the clearance envelope to automatically detect any potential encroachments. When a constriction was found, the software collected the scanning data onto a plane orthogonal to the track at the location of the constriction and generated a vector representation of the encroachment. From there, the information could be exported for use in DB’s LIRA database.
As a final confirmation of the performance of the scanning system, IBH compared information from the Trimble® GEDO solution with known values and results from optical surveys. The stationing of constrictions determined by the scanner agreed to within 10cm of the optical surveys. Horizontal and vertical offsets from the track axis were within 5mm of the optical measurements. The results demonstrated that the GEDO Scan system performs well within DB specifications and can replace the optical methods. In addition to meeting requirements for accuracy and eliminating the need for a physical frame, the Trimble® GEDO system can significantly reduce time and costs in collecting the high-accuracy data.
Herzbruch pointed out that the reduced time for measurement is an important benefit. When using the GEDO solution for constrictions as well as documentation or pre-tamping measurements, the system’s fast operation reduces costs associated with track downtime and safety precautions during the measurement process.
Flexible solution for railway information
For the clearance surveys, IBH used the Trimble® GEDO Scan solutionn to collect points relative to the centerline. The system can also be configured to collect absolute position data based on local 3D coordinates or a dereferenced coordinate system. In these configurations, Trimble R10 GNSS receivers or Trimble S-Series robotic total stations determine the location of the trolley as it is moved along the track. During processing, each point captured by the scanner receives 3D coordinates in the local or global system.
When used with the optical or GNSS positioning sensors, the GEDO Scan solution can provide dense, high-precision information on track and surrounding structures. Measurements of complex or confined spaces such as tunnels and underpasses are completed quickly, and the resulting 3D point clouds can be inspected in detail. For example, the 3D point cloud generated by using GEDO Scan can be used in planning new alignments or modified structures. Clearance envelopes can pass through the point cloud to conduct collision tests against new designs. And because the scanner captures even small details in a single pass, it eliminates the need to revisit a site to collect additional data needed for design or analysis.
A smart solution for railway measurement
Herzbruch believes that the Trimble system gives him a significant competitive advantage. “The Trimble® GEDO Scan system provides very high accuracy and is an effective, economical solution for clearance surveys,” he said. “The outstanding properties of the system include end-to-end digital data processing and the improvement in productivity associated with automated measurement and information management.”
As railways adapt to increasing demands for speed and capacity, engineers and managers rely on accurate, timely data on their assets and surrounding environment. The Trimble® GEDO solution plays a key role in providing information to support informed decisions and safe, economical operations.
Issue
Related topics
High-Speed Rail, Infrastructure Developments, Track/Infrastructure Maintenance & Engineering