Track stiffness optimisation to improve performance of switches & crossings
Posted: 21 May 2014 | Elias Kassa | No comments yet
Switches and crossings – or otherwise known as ‘set of points’ or ‘turnouts’ – provide a railway network with operational flexibility by enabling vehicles to be directed from one track (or line) to another. The most common switch and crossing (S&C) layout consists of a switch panel, a crossing panel and a closure panel between the two. Even though S&Cs are an important track asset in the rail network, they are one of the weakest links in the network demanding very high maintenance costs in comparison with plain lines. Several remedies are proposed by different researchers to reduce the high maintenance costs associated to S&Cs. Elias Kassa, Professor for the Department of Civil and Transport Engineering at the Norwegian University of Science and Technology (NTNU) explains further.
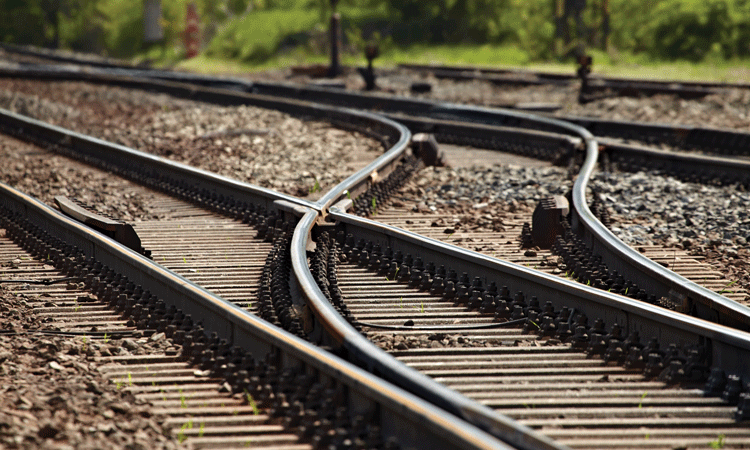
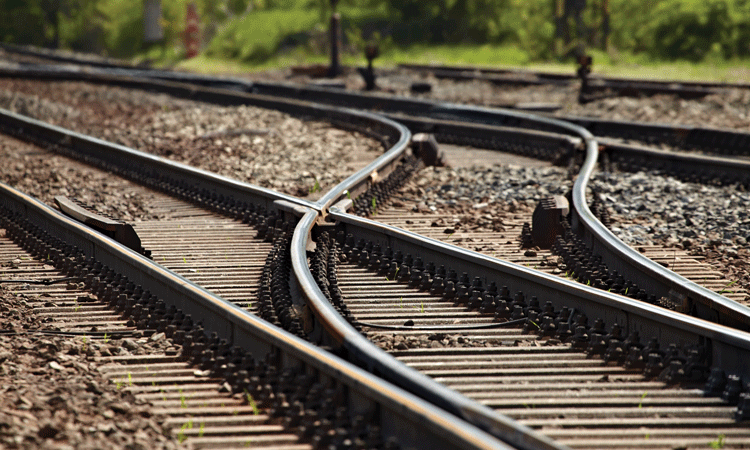
One obvious suggestion to reduce the maintenance effort is reducing the turnout population in the network. Some researchers are now focusing on using more durable and advanced materials, such as Chromium bainitic steel grade ‘CrB 1400’ which have shown to triple the S&C life time in comparison to a standard rail steel grade R350HT1. Others suggest adopting a preventative maintenance strategy instead of corrective maintenance to reduce the overall maintenance costs of S&Cs.
On the other hand, there is a high demand by railway administrations for a novel and optimised S&C design, both the turnout geometry and the support stiffness, to reduce the maintenance frequency of S&Cs. These require detailed understanding of the forces and their effect on the degradation modes. The structural design of the switch support can be optimised so that a more uniform stiffness is obtained along the turnout by minimising the abrupt stiffness changes at the switch panel and crossing panel. The geometry design entails both the general layout of the turnout, such as the curvature, transition curves, track gauge, etc. and the rail profile change within the switch and crossing panels, by that to provide a smooth running surface for the train wheels. Advanced models are needed to study the dynamics of the train-turnout interaction and the wheel-rail interface within the switch to perform geometry design optimisation of an S&C.
This research work is part of the research at NTNU – Norwegian University of Science and Technology – to demonstrate how the vertical stiffness of the track is optimised, possibly by adjusting the rail pad and under sleeper pad stiffness along the turnout. In this way the abrupt changes in track stiffness due to the appearance of two rails or changes in a rail cross-section could be reduced and wheel-rail contact forces minimised. A simple numerical procedure is followed based on varying the measured track data parameters of the vertical track stiffness.
Simulation tools
In recent years, multi-body simulation (MBS) packages have been used for the prediction of railway vehicle dynamics and associated wheel-rail contact forces2. In particular, S&C studies use such simulations due to a need for a better understanding of the dynamics and the wheel-rail interaction which, hence, is used as input for the optimisation exercise. A track model based on a moving mass-spring-damper system with 7 degrees-of-freedom (dof) coupled to each wheelset is implemented (see Figure 2). Such type of moving track model is particularly suited to this study as its high simulation speed facilitates the large number of simulations required for the optimisation process. Additionally, the model accounts for the variations in track stiffness along the turnout through time-varying stiffness and damping values. These variations in bending and torsional stiffness of the rails are mainly due to the continuous variations in shape of rail cross-sections and the size of the sleepers, but also due to variation in ballast support of the sleepers along the turnout.
Track receptances
To set a frequency range where the 7-dof moving track models can be used with a sufficient accuracy, and to obtain a rough estimate of the contribution of rail pad flexibility on the total track stiffness, vertical track receptance is calculated and compared with a Finite Element (FE) model of a track. The upper spring-damper element value (kp, cp) represents the change in the rail and rail pad stiffness and damping values of the track, while the lower stiffness and damping values (kb, cb) for the spring-damper pairs represent the combined flexibility of the sleeper and ballast of the track system (see Figure 2). Although the simple moving track model represents the combined rail and rail pad flexibility by a single spring-damper element (kp, cp), the track receptance is able to match the FE model results up to 400Hz.
Measured track receptances with single point excitation applied on the rail head of the switch and stock rails, both in vertical and lateral directions, were used to obtain input data for the 7-dof model. The receptances were measured at three locations in the switch panel at 4.5m, 9.1m and 21.85m from the front of the turnout. The linear stiffness and damping values for the spring-damper pairs of the 7-dof track model is determined by fitting the receptances of the moving track model to the measured track receptances. The increment of the upper and lower stiffness element is almost at the same rate. The stiffness at the second measurement location (9.1m) is increased by 40% compared to the stiffness at measurement point 1 (4.5m), while the increment at the third measurement location (21.85m) is 70% compared to the first point.
Track stiffness optimisation
Two alternative stiffness variation models are developed to improve the smoothing of the large change in track stiffness along the switch panel. The optimisation procedure is to limit the maximum variations of the track stiffness from 70% to only ±30%. This ±30% track stiffness change is expected to be gained by adjusting the rail pad stiffness. The influence of the rail pad stiffness variation along the switch on the global stiffness and its effect on the wheel-rail contact forces is investigated.
In the first stiffness optimisation model (kp_v1), the value of kp is increased by 30% at location 1 and reduced by 15% at location 3, keeping the value at location 2 unchanged. This can be achieved by placing stiffer rail pads starting from some distance before the front of the turnout. This gives a smaller change of kp values along the switch panel: 416MN/m, 448MN/m, 462.4MN/m at location 1, 2 and 3, respectively. The stiffness values in the second alternative model (kp_v2) limits the stiffness increase between location 1 and location 3 down further, to about 8%. This is obtained by increasing the value of kp at location 1 by 28%, and reducing by 6% and 19% at location 2 and 3, respectively. This gives values of kp at the three locations of 409.6MN/m, 441.6MN/m, 454.4MN/m.
However, optimising only the kp values in the switch panel does not bring significant improvements. Together with the kp optimisation, the lower spring-damper element stiffness (kb) variation is also considered in the optimisation exercise. The value of kb is changed by a maximum of ±20%, from the measured values. The kb value increased by 20% at location 1, reduced by 10% at location 2 and reduced by 20% at location 3, which gives 39MN/m, 41MN/m and 46.8MN/m, respectively. Keeping the kp values as nominal and varying kb reduces the wear index by almost a half, from 10N to 5.3N. A relatively large reduction in the wear index is obtained when optimised kp and kb stiffness values are applied together. As shown in Figure 4, the maximum wear index, which is at 10.7m from the front of the turnout, reduced from 18.9N to only 9.5N, which is a good improvement on the performance of the S&C.
Conclusion
A vertical track optimisation process is carried out using numerical simulations, in the switches and crossings. A moving track model with 7-dof and varying track model parameters (rigid masses, stiffness and damping) to incorporate the variation in track stiffness along the turnout, is implemented. The track model data are extracted from track receptances measured at three locations in the switch panel. Optimising only the kp value (only changing the rail pad stiffness) shows a slight reduction in the maximum wear index. A considerable improvement in the wear index is obtained when both kb stiffness value (using varying under sleeper pads) and the kp are optimised.
References
- A Zoll, Assessment of Rail Materials for Switches and Crossings, Proceedings of the 2nd International Conference on Railway Technology, Ajaccio, Corsica, France, 8-11 April 2014, pp.1-7
- D Nicklisch, E Kassa, J Nielsen, M Ekh and S Iwnicki,Geometry and stiffness optimisation for switches & crossings, and simulation of material degradation, ProcIMechE, Part F, Journal of Rail and Rapid Transit, 224, 2010, pp.279-292
The Norwegian University of Science and Technology (NTNU)
The Norwegian University of Science and Technology (NTNU) – with its motto ‘Knowledge
For A Better World’ – aims to create the basis for the development of knowledge and to create value – economic, cultural and social. NTNU is one of the largest universities in Norway with specialisations in technology and the natural sciences. Railway is becoming one of the core areas of research within the department of Civil and Transport Engineering at NTNU. Please visit http://www.ntnu.edu/
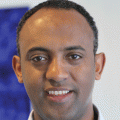
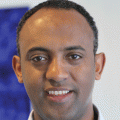
Dr. Elias Kassa is a Full Professor of Railway Engineering at the Norwegian University of Science and Technology (NTNU) Norway since March 2013. He has been working actively for the last 12 years in railway related activities. He is responsible for railway education at Master and PhD levels at NTNU and he is invited lecturer at other universities. Prior to his position at NTNU, Elias has been involved in a range of railway specialised projects in Sweden and the UK, and has published papers of his work in scientific journals. Elias obtained a Bachelor of Science degree in civil engineering from the Addis Ababa University, Ethiopia in 1998 and his Masters degree in 2002 and PhD in 2007 both from Chalmers University of Technology, Sweden. He has practical experience and is highly knowledgeable on railway engineering – mainly in the permanent-way (track superstructure) including switches and crossings, railway-vehicle interaction and wheel-rail interface.
Issue
Related topics
Infrastructure Developments, Track Systems, Track/Infrastructure Maintenance & Engineering