Working together to advance Additive Manufacturing in rail
Posted: 13 May 2020 | Andreas Stjernudde | No comments yet
SJ AB – Sweden’s leading train operating company – is already benefitting from the use of Additive Manufacturing (AM), but its Digital Project Manager, Andreas Stjernudde, writes that, to truly realise the potential of this technology, industry collaboration is vital.
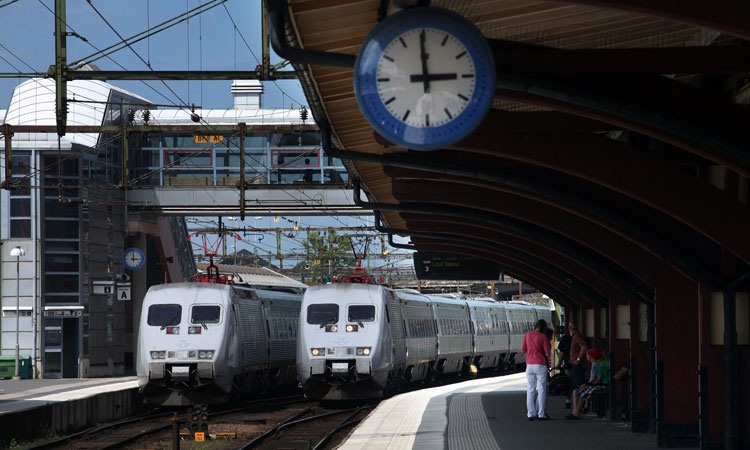
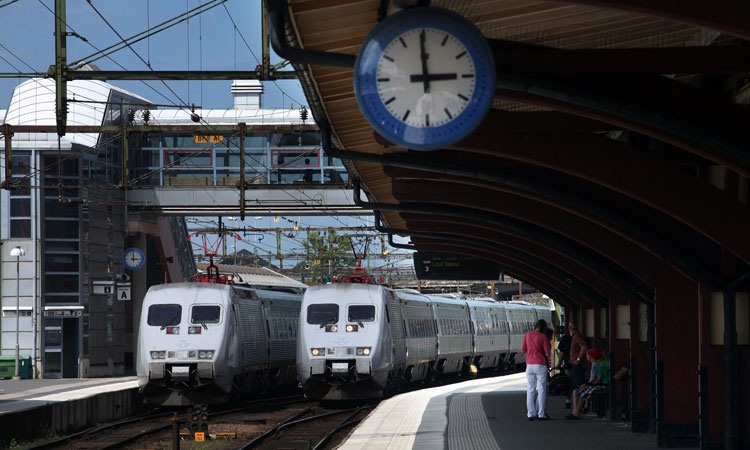
Like many train operators across Europe, SJ AB (SJ) has a diverse rolling stock fleet, with vehicles ranging from 1980s locomotives and coaches, to modern electric multiple units (EMUs). However, as SJ is not just a train operator but also the vehicle owner, compulsory rolling stock maintenance is a consequence of the deregulation of the Swedish market, resulting in SJ having to purchase the services that it needs to maintain its fleets.
Therefore, SJ must ensure that substantial technical modifications and upgrades are made to its fleet during their lifecycle, and thus needs to be well-informed about the various solutions on the market. One such area is the substitution of a variety of obsolete parts and spares, which can sometimes be a challenge. This can partly be attributed to the comparably low volumes of each individual vehicle type and, consequently, the diversity means that few parts are interchangeable between vehicles. This means that we must spend a lot of time finding alternative solutions for obsolete components.
A solution to a variety of challenges
Additive Manufacturing (AM) provides a solution to a portion of our challenges and, in the future, can be a powerful tool for us to provide a better service to our customers. Today, we have purchased several components through the means of AM that have provided us with business value, such as cutting costs and greatly reducing lead time. This is a means of production that we continue to use where it is fitting and we see a great potential for future applications. At the beginning of 2018, SJ began a project to identify some basic use cases to trial using AM. We began by going through our lists of issues and quickly found some good use cases. These were primarily parts that were obsolete or, in other ways, very hard to source. But, some were also added from a cost perspective, particularly small custom-made parts for vehicles. Some of these use cases ended up being produced through a variety of AM methods, and some have already been implemented on our vehicles. The project showed that AM could be useful to SJ from multiple points of view, including:
- Low minimum order quantities
- Lowered costs to produce parts with complex geometries
- Increased availability of parts (obsolescence).
Overcoming obstacles
However, not every case was a good match for AM. This is mainly due to the price of production, which is still considerable. There are also other things that hinder us from realising more cases, such as material properties and the need for post-processing. Regulations within the rail industry can also sometimes be a challenge, which must be handled through re-engineering.
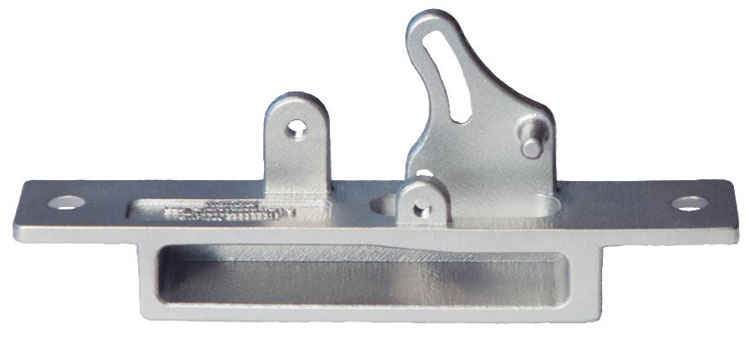
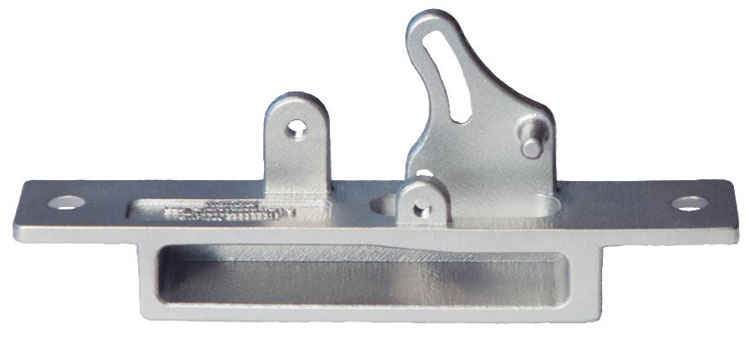
SJ has used AM to produce a replacement on-board toilet door latch, which is now an obsolete part.
Through the decreasing cost of production and advancements in materials and methods for AM, the niche of parts that are viable for printing is growing larger and larger. In the beginning, we only considered low volume parts, but we have since come to realise that even things that are considered consumables can be viable for printing. We have printed small interior parts such as curtain hangers, and large metal parts such as a wheel bearing cap, to great satisfaction. Identifying more parts is desired and, hopefully, we will be able to use AM to a greater extent, allowing us to provide value for our customers as the technologies become more mature.
SJ is continuously identifying new cases for AM, and the most interesting examples have been parts with complex geometries or low volume parts. Medium volume parts that are made to measure can sometimes be good candidates, especially if they can be improved upon – for example, if a part can be made more durable or be provided with indicators for replacement.
Large metal parts are usually avoided, but there are methods that make it feasible to produce large cast parts, if there is a lead time issue. It may also be a good thing to consider more aspects than just the production price to achieve a low total cost of ownership. How much time would you need to spend finding an obsolete substitute? How many parts do you need and what’s the minimum order quantity? What added values can an additively manufactured part provide?
Other advantages that the technologies provide us with include the ability to have parts printed on demand and production on sites closer to our facilities. Hopefully, in the future, we will be able to produce more parts locally and have polymer parts printable. But, as aforementioned, there are still some obstacles in our way and, to solve them, we have decided to be a part of the development.
Industry collaboration
SJ sees great potential in the use of AM, and we recognise that the industry must work together in order to advance the technology and make it available to the market. For this reason, we are working together with other European operators and the AM-industry through the Mobility goes Additive network, where we work on subjects that are important to us, such as the approval of parts or more materials that meet the flame retardancy regulations (EN 45545).
At SJ, we hope that, together with our European colleagues, we can prove that AM methods are viable for production, and we also hope to expand the use of the technology so that we can rely on a wider range of materials and standards. If we don’t know which methods and material can be used with which mechanical properties, any gain in lead time will be hard to capitalise on due to the approval process.
In the long-term, one possible way of supplying spare parts could be that the original equipment manufacturers (OEMs) provide printing files to workshops for local AM production. This would require us to have a new business model with the material suppliers.
Some of the use cases that SJ has already realised using AM include:
Curtain hanger: Low order quantity
One of SJ’s older EMUs had one of its window curtain hangers removed, which needed a replacement. The search for a replacement was a tedious process for the responsible engineer, as the old hanger was obsolete. In the end, a replacement that fit our specification was found, but it was not a standard product and thus had to be ordered in a large quantity. This was not suitable for us, so we investigated if this part could be printed instead. A trial was made using selective laser sintering and the result was so good that it was immediately implemented, with a small quantity of stock also provided.
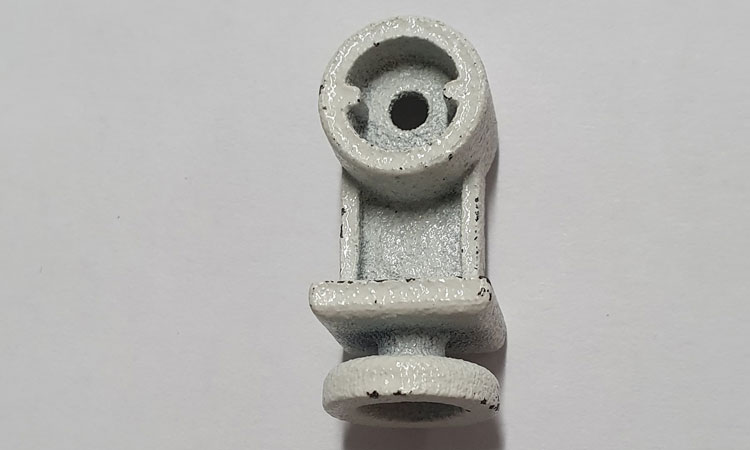
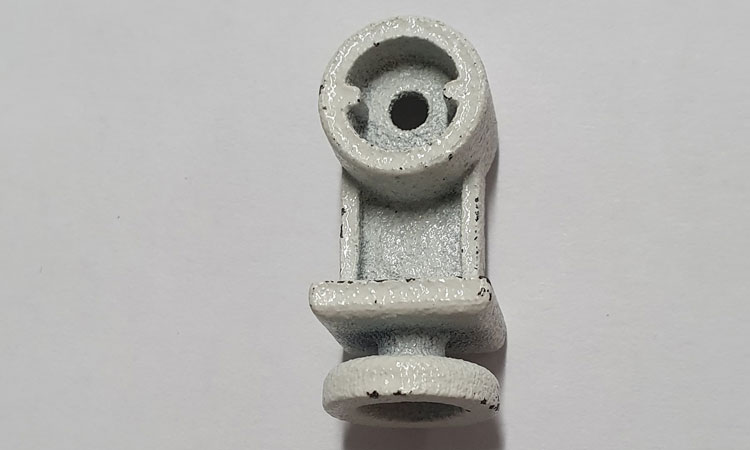
SJ has used AM to provide replacement on-board curtain hangers.
Toilet door latch: Obsolete part
On one of our more vintage vehicle types, some of the parts were designed and manufactured in the 1940s. One of these components was an old toilet door latch. The latch was designed for production using the old techniques and was casted in large quantities. This meant that the design was not optimal for CNC-milling, let alone printing. As the number of latches needed did not warrant the ordering of a new cast, SJ decided to print the latch instead. The design of the latch was improved and optimised for printing, where the exterior parts were kept true to the original, but the interior was simplified and improved upon. The latch also got a material change from aluminium to stainless steel, which has made it less susceptible to damage.
Wheel bearing cap: Long lead time
One part that suffers from long lead times is the wheel bearing cap. Although it is generally not a component that has a large turnover, it provided a good use case to try one of the technologies more adapted to printing large metal parts. With the permission of SKF and with the support of KTH, SJ proceeded with printing the part. As this is a part that is subject to heavy loads and is safety relevant, the approval process of this part is important and must follow CSM-RA. SJ is, at this moment, conducting tests to verify that the material properties of the printed material correspond to the outlined standard. The object of which is to prove that the material and the method is usable for replacement of old cast iron components and, through that gain, the lead time advantages that the technology can provide.
To summarise
Additive Manufacturing is a great tool to be used in our industry, but there are still some obstacles to truly realising its potential. Together, we can work on removing those obstacles and, in turn, provide our customers with greater value.
Issue
Related topics
3D Printing/Additive Manufacturing, Rolling Stock Maintenance