Network Rail’s infrastructure monitoring surveys from the sky
Posted: 15 April 2020 | Sean Leahy | No comments yet
Network Rail’s Air Operations Team use a variety of visual and thermal imaging techniques, plus drone technology, to safely and efficiently inspect infrastructure, whilst minimising disruption for passengers. As part of the team, Sean Leahy, National Aerial Survey Specialist, explains the work involved in gathering images and data, and the benefits of this activity.
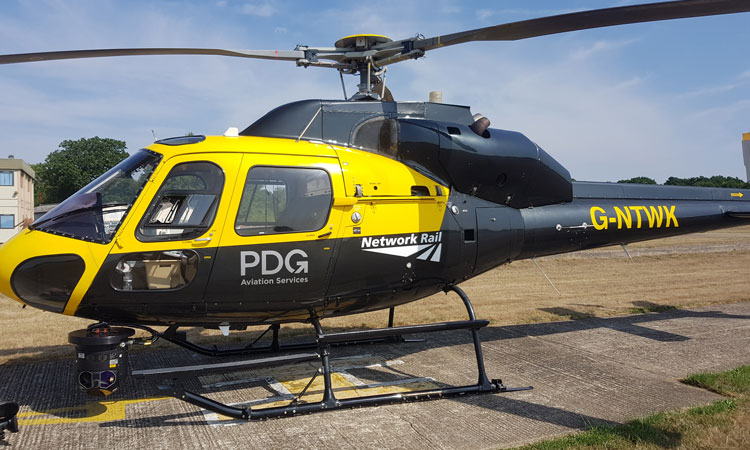
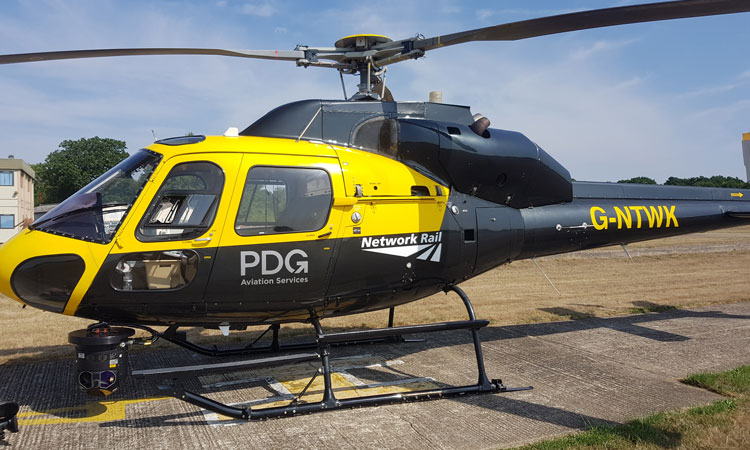
There are almost five million passenger journeys on Britain’s railway every day. Those people choosing to travel by train – whether they’re travelling to and from work, or visiting friends and family – rely on us to deliver a safe and reliable railway, as do the freight operators who move 200,000 tonnes of goods and materials across the country each day.
It may seem strange to some that Network Rail has its own dedicated Air Operations Team. However, based in Milton Keynes is the Head of Air Operations, Drone Manager, three dedicated Aerial Survey Specialists and two admin support staff who work closely together to monitor the condition of our assets more safely and efficiently than our teams on the ground are able to. That includes 20,000 miles of track, 30,000 bridges, tunnels and viaducts, and thousands of signals, level crossings and stations.
Benefits
Safety
Inspecting our rail infrastructure takes boots off the ballast – reducing the need to send colleagues trackside to inspect railway equipment. It is important to emphasise that we are not here to replace front line staff. We are here to support them and make sure that they have the right information to work in the limited possession times they get. With more and more areas becoming Red Zone Working prohibited – an area where trains still run whilst engineering activity takes place – the need to check these areas is ideally suited to an airborne platform.
Performance
Ultimately, our work is carried out to improve the operational performance of the railway by identifying infrastructure faults and better understanding our assets. As part of our ‘predict and prevent’ maintenance strategy, we are able to target track maintenance more effectively, and there is no disruption for passengers whilst our helicopters and drones are flying as trains can continue to run.
Efficiency
We are always looking for improvements in financial efficiency, and our drones and helicopters are a highly-cost effective solution for inspections, with drones particularly useful for difficult-to-access structures, such as building roofs, bridges and overhead wires.
As an Aerial Survey Specialist, I work mainly on the helicopter, gathering and processing significant amounts of data. It may sound like a glamourous job, but it’s not for everyone, as a lot of my time is spent living out of hotel rooms around the country.
Our helicopters are twin-engine, which is essential for safety, as we operate over some very built up areas and have exemptions to operate where most civilian operators cannot. Each helicopter is fitted with a satellite telephone system used for emergency communications between the crew and Network Rail’s Operations centres – for example, if the crew see something that requires an emergency line blockage to keep passengers safe.
Thermal imaging
The introduction of our FLiR Star Safire 380hdi camera system in 2012 really brought our ability to accurately fault report into the 21st century. When we identify a fault, the system allows us to fire a laser at the fault, providing us with the latitude and longitude of exactly where the crosshairs are pointing, with the help of an app called ‘Where am I?’, which the team helped develop. This is then sent through to the engineers – within two hours of landing – so they can assess what action needs to be taken.
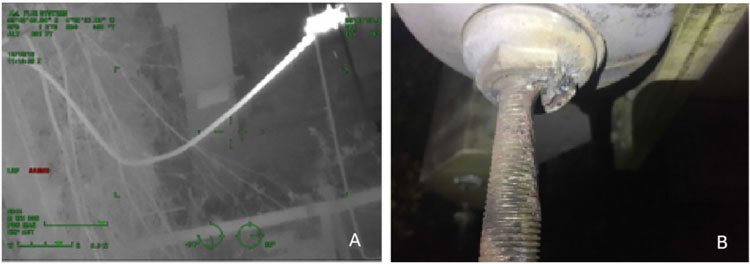
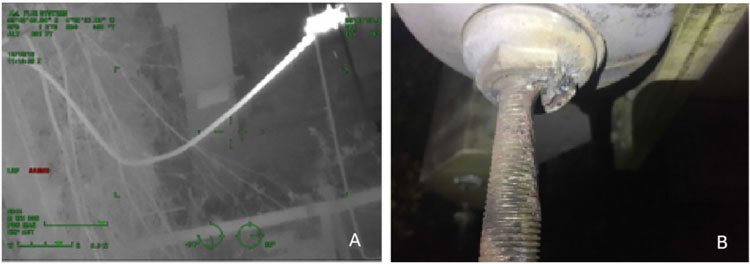
Figure 1a shows an image of a potential fault on a booster transformer and Figure 1b shows what the team found; this was almost a catastrophic failure which would have caused considerable disruption for passengers.
The beauty of the system is that, because the cameras are so good, we can sit between 1,000 to 2,000ft above the railway and clearly read things such as point, signal and electrification structure identification plates. It is also an ideal way of spotting potential faults, because heat shows on the components as white on the screen, meaning they show up better.
Figure 1a is an image of a potential fault on a booster transformer, which was found in 2018 near Kirkhill in Scotland within a Red Zone Working prohibited area. Within 48 hours of the fault being identified, a team had arranged a non‑disruptive possession. Figure 1b shows what the team found; this was almost a catastrophic failure which would have caused considerable disruption for passengers.
Visual imaging
Visual imaging is another service we provide via two platform capture systems. The use of a GSS turret on the helicopter allows us to use a variety of different camera lenses to capture high-definition still imagery in a stabilised gimbal.
The most common use of this system is a unique Network Rail platform, designed in collaboration with RSK Orbital, called Route-View. We use an 85mm lens and a Canon camera to capture an image of the railway every three seconds, accessible to anyone with a Route-View account. Route-View has many unique features, including a measure feature and a tool allowing the user to compare changes over two different image dates.
The beauty of Route-View is that it can help to reduce the need for site visits when work is being planned. It allows planners to be more efficient and keeps them in the safety of the office environment. Another area where Route-View comes into its own is emergency response and incident management, because it allows controllers to direct emergency services to the nearest access point to the incident.
Figure 2a displays images from Route-View, showing the versatility of the system using the compare tool. It shows a signal at Bridgewater taken during the flooding in 2014. The image on the right was taken four days earlier than the image on the left, and it allowed engineers to count the signal ladder rungs to see if the flood water was rising, receding or staying at a steady level.
Figure 2b was captured when we were inspecting overhead line equipment in Scotland, and this is what the engineer sees when they open the system at their desk.
Figure 2c is what the engineer can see once the image has been opened fully, allowing them to carry out a full asset condition survey – again, from the safety of their office environment.
In a more traditional inspection of this equipment – depending on the line and how long the possession is – at best, two boosters per night could be inspected, at a considerable cost in staff resource and equipment. It would require a non-disruptive possession to be imposed and the traction current would need to be isolated.
With air operations, maintenance is carried out during daylight hours, while trains are still able to run. Helicopters with full fuel will typically have around two hours working time in the air, meaning all boosters would have been surveyed between Berwick upon Tweed and Edinburgh with a crew of just two.
The second platform we use for capturing visual images is basically a handheld camera, which gives us more versatility. While carrying out a thermal survey recently, a switch on the overhead wires was identified as overheating, see Figure 2d.
The blackening as a result from burning could be seen, but the full extent was known when we were able to open the picture in Route-View, as shown in Figure 2e.
Still imagery allows pictures to be shared among engineers, enabling more informed decision‑making. They can also be used by our media team to keep passengers informed of what is happening and why their train might be delayed.
Drones
Accompanying the traditional helicopter in our fleet are Unmanned Aerial Systems (drones) – the new kids on the block. As battery technology and Beyond Visual Line of Sight (BVLOS) rules improve, they will come into their own.
Network Rail not only has a framework of companies that deliver UAS work on our behalf, but also has several staff that are trained as operators.
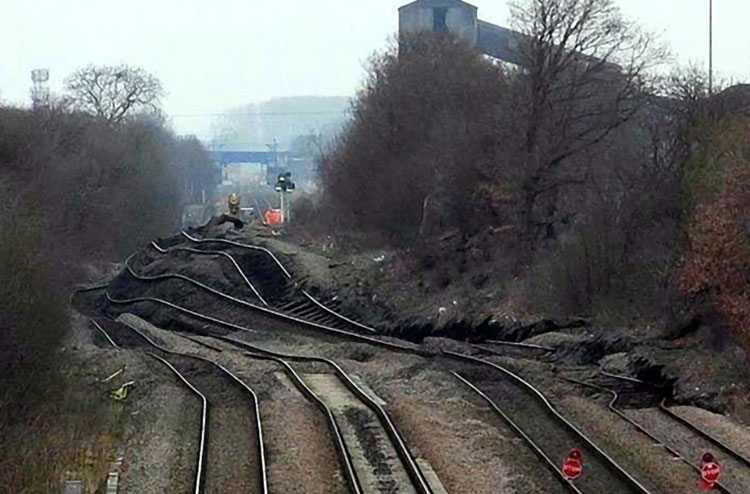
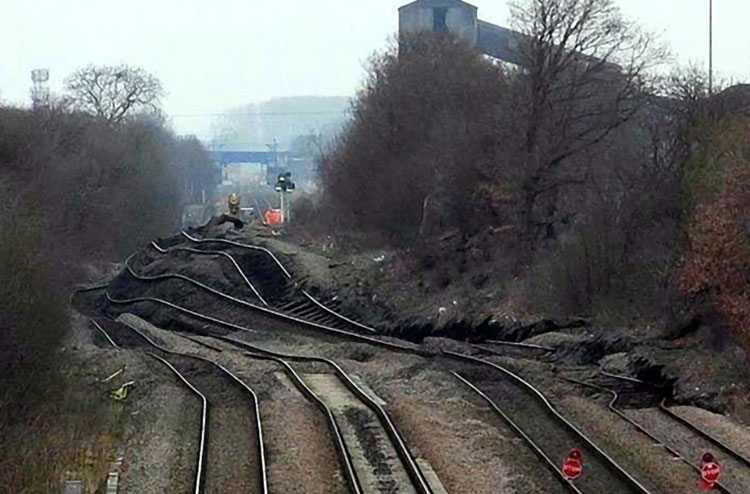
Figure 3: An example when using a UAS was more cost-effective than using the helicopter.
UAS and helicopter services complement each other due to economies of scale. The area that a helicopter can cover in an hour would take at least a week to cover by UAS. So, if the areas require long linear surveys, then the helicopter is the platform of choice. But, if spot surveys are required of a single location, then a UAS is better suited. However, as technology evolves, this will inevitably change.
Figure 3 is an example of where a UAS was more cost-effective than using the helicopter.
On the line next to the now closed Hatfield and Stainforth Colliery, there was a slag heap in the colliery grounds next to the railway. There was an onset of heavy rain which caused the heap to dramatically gain mass, pushing the railway.
The helicopter was despatched to take the first initial photographs of the incident, but engineers wanted twice daily flights to monitor the site to check for any further movement. A UAS was dispatched for this task as it is ideally suited to monitoring a small site.
Evolving technology
The realm of aerial surveying is constantly evolving. We are always looking for, and developing, new techniques to give our engineers the edge in predicting and preventing asset failures, including hyperspectral imaging, LiDAR surveying and coronal imaging, to name but a few.
As UAS technology evolves and sensors get smaller, I am sure that, in years to come, I will be sitting in a warm office in Network Rail’s HQ, operating a camera over a city somewhere while drinking a cup of tea.
Issue
Related topics
Big Data, Digitalisation, Drones, Infrastructure Developments, Safety, Technology & Software, The Workforce, Track Maintenance Machinery, Track/Infrastructure Maintenance & Engineering