Improving railway operations using pneumatics technology
Posted: 14 June 2022 | Darryl Brunk, Emerson | No comments yet
Darryl Brunk, Business Development Manager – Automotive & Tire Segments at Emerson, explores pneumatics technology and why it is such an effective solution for the safety, comfort and performance of many applications that are found throughout passenger and freight trains.
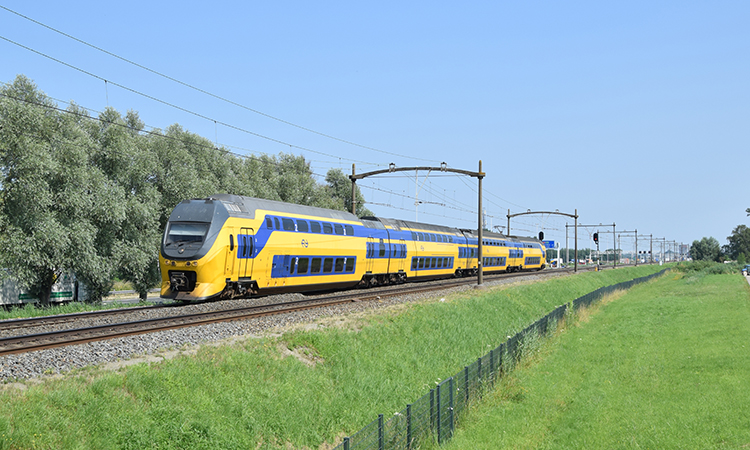
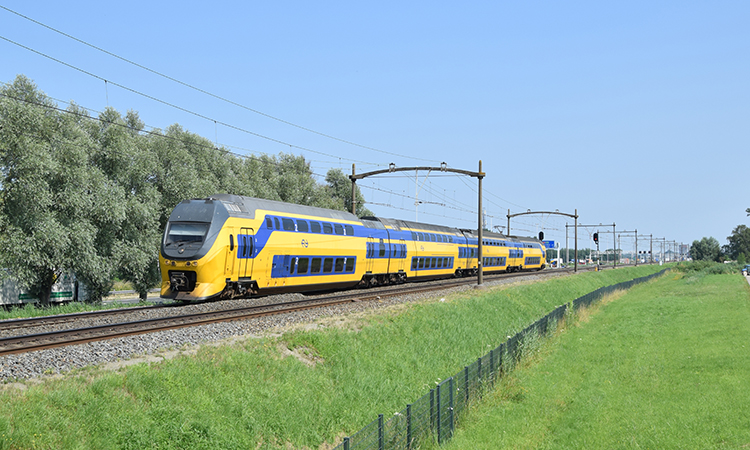
Whether they are used for transit or cargo, trains must move a lot every day – on schedule and in all conditions. From the nose cone to couplers, from pantograph to brakes, pneumatic devices improve the safety, comfort and performance of many applications found throughout passenger and freight trains. By integrating these products into railcar designs, manufacturers can extend maintenance intervals, minimise downtime, cut maintenance costs, and reduce energy use.
Extend air preparation service intervals
Railway pneumatics begin with a reliable, dry air supply. Most air dryers use a granular adsorption medium. Unfortunately, the shock and vibration from rail operations can cause channelling, air bypass and dust generation, or even lead to a breakdown of the granulate bed and a significant reduction in drying performance. This results in a shorter service life, requiring more frequent replacement of the adsorption medium.
Typically, the service interval for air dryers is less than two years. However, new developments in drying technology can extend that service life and reduce maintenance costs while increasing performance.
From the nose cone to couplers, from pantograph to brakes, pneumatic devices improve the safety, comfort and performance of many applications found throughout passenger and freight trains.
New technology available to the industry uses rolled-up desiccant drying technology that provides a consistent, highly open porous structure throughout the media, resulting in superior moisture uptake performance. Resistant to vibration and excessive water loading, this new technology can work in both horizontal and vertical orientations for more installation flexibility. Furthermore, the new technology provides a service interval of at least eight years (or more than 25,000 operating hours) instead of two years.
The design of the new technology is based on two columns containing the drying medium inside easy-to-replace cartridges, where one column is always drying the air and the second one is being regenerated by purge air. Once one column is saturated and must be regenerated, control valves will switch the air supply between the two columns automatically. The high moisture uptake and improved kinematics reduce the purge loss compared to conventional air dryer technology (less than 15 per cent), leading to less air consumption and more energy savings.
Gain greater control and precision
Safety comes first in both passenger and freight train operation. The technology used to control levelling and brake control, chassis suspension and pantograph control must be extremely reliable and durable enough to withstand rugged environmental conditions and extreme temperature ranges. Components must have a long lifecycle and be easy to maintain. Intelligent, durable and low-maintenance pneumatic components are ideal to fulfil a wide range of applications on trains.
Brake control and actuation
The use of air for braking on trains originated in the mid-1800s; 150 years later, pneumatics is still the best technology to use for brake control.
One of the latest key components in a railway brake system is the electropneumatic (EP) pressure regulator, which provides precise control of pressure and flow with dynamic regulation (this is especially important for the service brake control).
New pressure regulator technology available to the rail industry can direct electromagnetic actuation of integrated poppet valves to allow for very precise true proportional control with a high flow rate and combine dynamics, precision, and excellent repeatability with extreme durability. New solutions can provide robust poppet valve technology which does not require any special air quality. Furthermore, large cross-sections and a soft-sealing proportional valve seat can make the valve durable and resistant to contamination.
Chassis suspension and levelling
Besides braking systems, pneumatics play a key role in chassis suspension systems, such as the pneumatic control of air springs. An electronic levelling valve (ELV) provides significant benefits over conventional manual levelling valves. It primarily consists of one proportional valve, two switching valves and control electronics with sensors. The bus interface makes controlling easy and allows for life condition monitoring. Control electronics optimise the control and switching behaviour of the integrated valves while minimising air consumption.
Pantograph control and actuation
On electrically powered trains, when it comes to pantograph control and actuation, there is absolutely no room for compromise. Pantographs must work in all conditions at any speed. The primary challenge is to constantly maintain the contact between the catenary cable and the pantograph’s carbon strip without pressing against overhead lines too forcefully, otherwise they will rapidly wear or even rip. Pneumatic control solutions provide the dynamic performance this precise application requires. Compared with electromechanical solutions, quality pneumatic solutions are virtually wear-free.
Enhance passenger safety and comfort
From the moment passengers enter the train to the moment they exit, a range of pneumatic components ensure their experience is as safe and comfortable as possible.
Starting at the train door, rodless pneumatic cylinders provide reliable actuation of doors. For those trains that need a step to board quickly and safely, sensor-controlled cylinders in the sliding step provide exact extension and retraction to ensure the steps precisely line up with the platform.
Once passengers are in their seats, pneumatic components actuate and control HVAC systems, keeping the train ride comfortable. Pneumatic components that instantly close the fresh air intake help protect passengers from pressure changes when high-speed trains encounter oncoming trains or enter and exit tunnels. If the fresh air intake is not properly and quickly closed, pressure waves can enter passenger cabins.
Exceed industry standards
No matter how well pneumatic components function, equally important is that they meet current railway-specific standards and requirements. These include ratings for electromagnetic compatibility (EN 50121-3-2), corrosion resistance, fire protection (EN 45545), shock and vibration (EN 61373), temperature and more. It’s crucial to work with an expert supplier who knows the industry and offers support and products that comply with the latest global standards, for individual components or complete plug-and-play subsystems.
From braking to actuators, airflow and control, pneumatics can do it all. Whether a solution is needed for new trains or a refurbishment project, pneumatics designed specifically for the rail industry will help ensure all specifications can be met successfully.
Related topics
Cargo, Freight & Heavy-Haul, Operational Performance, Passenger Experience/Satisfaction, Rolling Stock Components (Interior/Exterior), Technology & Software