Controlling Crossrail’s noise and vibration: Track design and construction methods
Posted: 10 November 2017 | Andrew Bird | 1 comment
Crossrail – officially named the Elizabeth line when services start in December 2018 – links 40 stations over 118 kilometres; from Reading and Heathrow to the west of London, to Shenfield and Abbey Wood in the east.
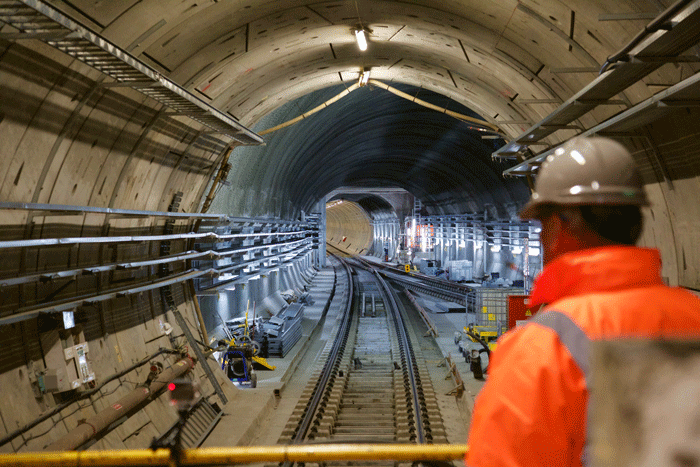
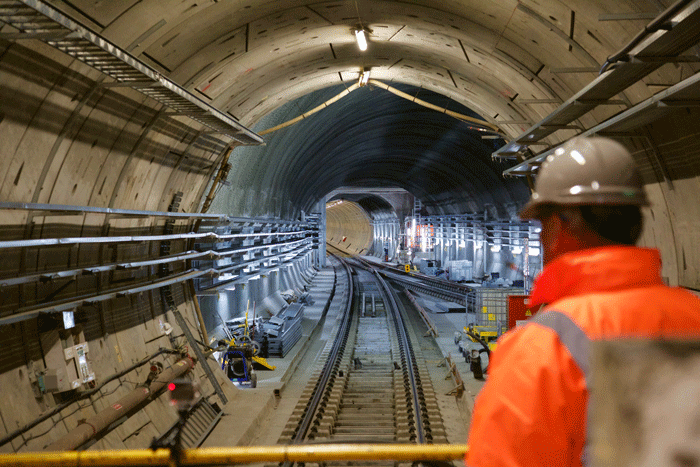
For Global Railway Review, Crossrail’s Acoustic Manager Andrew Bird, and Jo Webb, President of the Institute of Acoustics, explain that because the route will pass through dense residential and commercial areas, the design of its tracks and the best ways to limit ground-borne noise and vibration have been vital aspects to consider throughout the project.
The new railway consists of 21 kilometres of new twin-bore tunnel, 10 new stations and improvements to 30 more, and extensive upgrades to the existing national railway infrastructure. The Elizabeth line will provide a metro style service, with a train departing approximately every six minutes in each direction in the section across central London.
Part One: Track
With much of the route passing through dense residential and commercial areas, the project is subject to several requirements to limit the ground-borne noise and vibration impacts of the operational railway. The primary method for controlling ground-borne noise and vibration for this new railway scheme has been in the design of the 42 kilometres of permanent track that has now been installed in the tunnels.
Commitments
Crossrail Ltd and its design team, Arup Atkins Joint Venture, were required to design the permanent track system in the tunnels to ensure that the level of ground-borne noise arising from the Elizabeth line is predicted in “all reasonably foreseeable circumstances” not to exceed the levels set out in the Crossrail Information Paper (IP) D10 Groundborne Noise and Vibration provided in Table 1. Note that the metric LAmax,S is a measure of the maximum noise level reached during an event such as a train pass-by.
IPD10 also requires that where the level of ground-borne noise arising from the operation of the Crossrail passenger service is predicted to equal or exceed 35dB LAmax,S near the centre of any noise-sensitive room in a residential property, reasonable endeavours should be made to adopt mitigation measures. These measures should further reduce any adverse impact, provided they do not add unreasonable costs to the project or unreasonable delays to the construction programme.
As well as the design criteria, specific commitments were made to protect particular areas and facilities. For example, a commitment was given to protect the recording industry based in Soho and another to preserve the acoustic conditions in the Barbican Concert Hall, both of which required bespoke track selections.
These noise and vibration requirements were only one element of a multitude of requirements that the final track designs had to satisfy. Key track components, such as resilient elements and concrete bearers, had to have a design life of 50 years and structural concrete lasting 120 years. The track also had to be installed at a particular rate to enable the construction programme to be met and the railway to open on time. Another design consideration was maintenance: With the Elizabeth line operating from 05:30 to 01:30, only four hours will be available for maintenance each day, meaning that any rail or track component replacement must be capable of being carried out within that time.
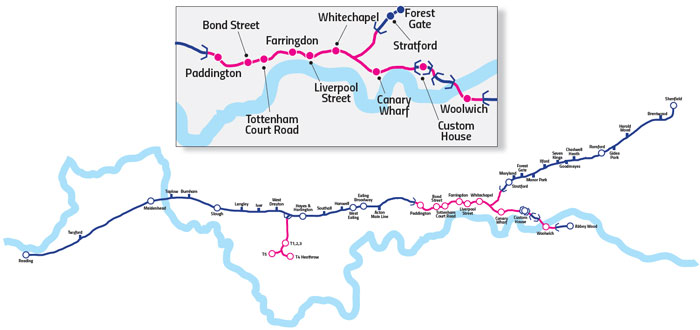
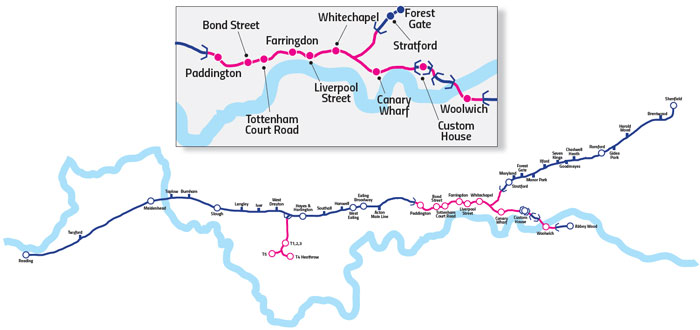
Figure 1: The Elizabeth line route
Prediction
A model for predicting ground-borne noise and vibration from the operational railway was required to determine the type of track system required along the tunnels. The model selected for use on Crossrail was based on the proven method developed for High Speed 1 in the UK (HS1)1.
The empirical method was developed from analytical principles, validated with regression analysis between well-defined source terms for vibration and measured levels of ground-borne noise inside dwellings close to sections of existing railway. Since development, the method has been implemented and further validated on a wide range of railways worldwide.
Development of the prediction method used specifically for the Crossrail project enabled its application to various different types of noise sensitive property in London.
To demonstrate that the track system designs would perform as needed, the proposed system was modelled using Arup’s in-house finite element modelling package, which represents the train-track system as a series of masses, beams and springs.
The aforementioned method was linked to Crossrail’s Geographical Information Systems and buildings database to provide the information needed to evaluate the design, and to support rapid assessment of different track options at more than 400 buildings above the tunnels.


Figure 2: Accuracy of the HS1 method for predicting ground-borne noise. The datasets include measurements from London Underground, UK; Deutsche Bahn ICE trains in Germany; SNCF TGVs in France; Intercity trains on the East Coast Mainline (ECML) in the UK; Metropolitan Rapid Transit (MRT), Singapore; Manchester MetroLink; Tangara Trains, Sydney, Australia; and measurements made above the HS1 tunnels, UK.
Crossrail track designs
Four types of track system were identified, determined by the required level of ground-borne noise reduction, cost and programme implications, reliability, maintainability and safety considerations.
Acoustically Isolated Track Systems
Over 80 per cent of the permanent track is a highly resilient track system, type Sateba 312 V S3. This system comprises a precast concrete bi-block supported on resilient pads encased in rigid plastic hulls and has the advantage of meeting the acoustic performance requirements and being relatively quick to install.
Sateba High Attenuation System
Over three kilometres of the Sateba High Attenuation System (HAS) was incorporated into the design, where the design criteria demanded more acoustic isolation to be used, namely a system having a lower natural frequency. Crossrail will be the first in-service use of the HAS system. As well as its greater level of acoustic performance, HAS can be laid at comparable rates to the Sateba 312 V S3 system. HAS is a resiliently supported, booted, mono-block slab track system.
Floating Slab Track (elastomer)
To achieve the commitment to install floating slab track in the running tunnels under the Soho area, a floating slab track on elastomeric bearings design was developed. This type of track was designed to ‘float’, which involved a concrete slab supported on discrete elastomeric bearings, which in turn are supported off the tunnel invert concrete layer. The elastomeric bearings have an equivalent dynamic stiffness of 11.1MN/m per metre of track. The reinforced concrete slabs were designed with access chambers that allow installation and inspection of the elastomeric bearings. In order to meet the required slab mass within the space constraints, an incredibly dense concrete called Magnadense was used. Magnadense is more than twice as dense as normal concrete due to its iron ore content.
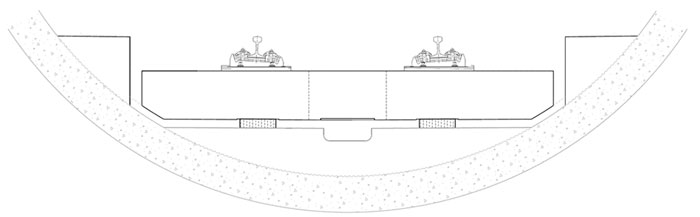
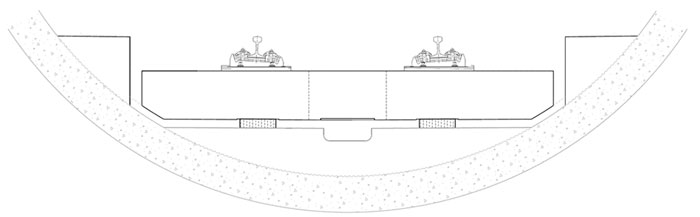
Figure 3: An indicative cross section of Floating Track Slab (elastomer)
Floating Slab Track (spring)
The Barbican Centre is a cultural venue with a famous concert hall, theatres, cinema, galleries and home of the London Symphony Orchestra, and the Crossrail eastbound tunnel is located directly below the building. To achieve the commitment to install floating slab track in the running tunnels under the Barbican a floating track slab with a minimum slab mass of 2,875kg/m and a maximum unloaded fundamental natural frequency of 7Hz was installed.
The slab is supported from the tunnel invert concrete layer by discrete steel springs with an equivalent dynamic stiffness of 10.1MN/m per metre of track. As with the floating slab track used in the Soho area, Magnadense was also used to meet the mass requirement.
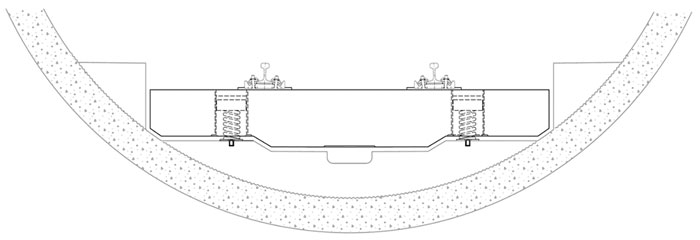
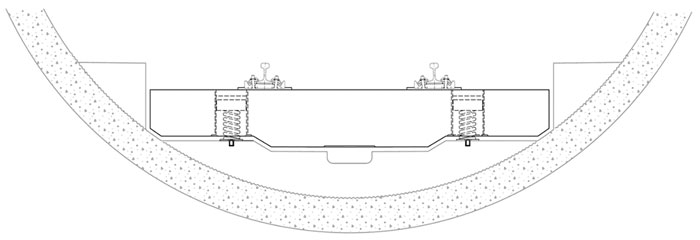
Figure 4: Indicative cross section of Floating Track Slab (spring)
Relative performance
Before discussing the relative performances of Crossrail’s track systems, it is important to emphasise that all of the track types are highly performing systems acoustically. Sateba 312 V S3, which is used on over 80 per cent of the route, has a far greater acoustic performance than the majority of track systems installed in tunnels located in urban areas in the UK.
The insertion gains of Crossrail’s track systems are shown in Figure 5. Insertion gain is a measure of the attenuation and amplification of vibration transmission to the ground relative to a rigid reference track.
The insertion gain is an indicator of the acoustic performance of the track system, because it shows the frequencies at which amplification peaks (the loaded track frequency) and attenuation will occur (below the zero intersection). In general, the lower these frequencies (the further left), the lower the level of audible ground-borne noise generated at properties on the surface.
It can be seen in Figure 5 that the HAS track system provides more attenuation of ground-borne vibration than the Sateba 312 V S3. Owing to the greater mass and low stiffness slab supports, the floating track systems are predicted to provide even greater ground-borne noise reduction compared to the Sateba systems.
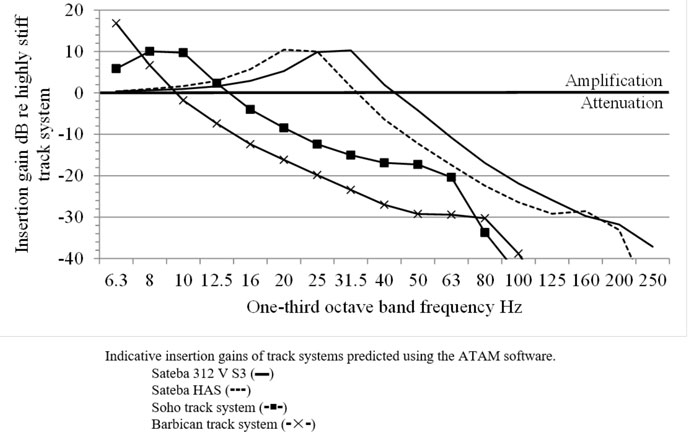
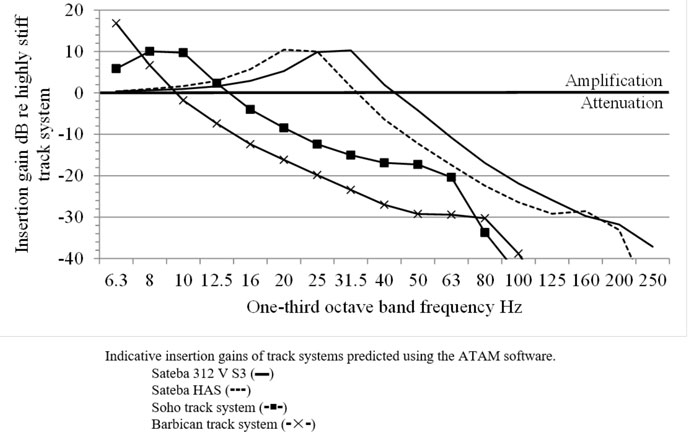
Figure 5: Predicted insertion gains of the Crossrail track systems
Track – conclusions
The track systems in Crossrail’s tunnels have been designed to meet the project commitments and specifications relating to ground-borne noise and vibration using proven models. These were an empirical prediction method for ground-borne noise and vibration, and a finite element model for predicting the acoustic performance of the track.
The track designs are predicted to achieve all design commitments without imposing unreasonable costs or delays to the project.
Part Two: Control of noise and vibration during construction
By the time Crossrail is operational its construction works will have spanned almost nine years. Major civil engineering works – including the construction of tunnels and underground stations – have taken place close to residential and commercial properties, often during the evening, night and at weekends.
The control of noise and vibration during construction has been one of the project’s key challenges with over 90 per cent of all the environmental complaints received relating to noise and vibration.
Commitments
Commitments given during the parliamentary process to gain authorisation for the scheme require the project to obtain and work within consents approved under Section 61 of the Control of Pollution Act 1974 (CoPA)2. This requirement was cascaded to all the principal contractors working on Crossrail and in close collaboration with the local authorities.
Crossrail operates a noise insulation and temporary re-housing scheme whereby one or both is offered to the occupiers of dwellings where the noise is likely to cause particular disturbance for substantial periods of time. The scheme is similar to those adopted by other major infrastructure projects such as HS1, the Thameslink Programme and now HS2.
The main legal provisions controlling noise from worksites are contained in the CoPA and require contractors to use Best Practicable Means (BPM) to control noise and vibration. BPM is the fundamental requirement for controlling construction noise and vibration from worksites. However, it is important to recognise that BPM does not set fixed standards and will change over time or depending on site specific context. What was considered to be reasonable 20 years ago may not be considered so nowadays. Construction practice is continually evolving in the light of new technology and new construction methodologies, and major infrastructure projects have the potential to play a significant role in driving forward the standards that are used to manage construction noise and vibration.
Given the scale and duration of the potential impacts of construction noise on local communities, Crossrail and its contractors have prioritised construction noise and vibration management. As a result, there are numerous examples of physical noise mitigation measures that were developed and used across the sites. Avoiding the mechanical breaking of concrete is a good example, with alternatives such as drill and bursting, chemical cracking, wire sawing, stitch drilling, pile cropping and hydraulic processing (munchers) being used extensively, along with large scale enclosures in some locations where noise at source could not be mitigated further.
However, once the construction works were underway, it became clear that the focus could not solely be on contractors controlling or reducing noise levels. Reducing the impacts on people is not only achieved by controlling or minimising noise levels. Community response to noise is strongly influenced by people’s attitudes towards the noise creator. In this context, the approved Code of Practice for construction noise acknowledges that ‘…people are more likely to tolerate the noise if they consider that the noise is necessary and that all reasonable steps are being taken to control and minimise noise impacts’3.
It is for this reason that factors such as community engagement, effective planning, management processes, leadership and culture were identified as being critical to successful noise management on sites. To that end, Crossrail developed a performance measurement process whereby contractor performance could be measured against all these areas and graded from basic compliance to world-class performance. Targets were then set for each contractor as to what they should be achieving to most effectively control their noise impacts and reduce the levels of disturbance experienced by those surrounding the sites. Over time average performance levels improved to the extent that several contractors achieved world-class noise control performance. Further information on this process can be found on Crossrail’s learning legacy website4.
References:
- Greer RJ, Methods for Predicting Groundborne Noise and Vibration from Trains in Tunnels. Proceedings of the Local Authority Rail Impact Forum (1999)
- Control of Pollution Act 1974 (CoPA) [online], available at: http://www.legislation.gov.uk/ukpga/1974/40/part/III/crossheading/construction-sites
- Code of Practice for construction noise BS5228-1 (2009 + A1:2014). Code of Practice for Noise and Vibration Control on Construction and Open Sites
- http://learninglegacy.crossrail.co.uk/learning-legacy-themes/environment/noise-and-vibration
Biography
Biography
Related topics
Noise & Vibrations, Track Construction, Track Systems, Track/Infrastructure Maintenance & Engineering, Tunnelling
As a line side neighbor to crossrail sidings I find this article unbalanced. Whilst it is pleasing to read about the intent to mitigate noise pollution and to engage affected communities, my family and neighbors have endured unacceptable levels of noise during the construction phase, without any substantial communication on the impact to us or detail on what to expect post construction. In our case, the execution of the intent described in this article was extremely poor.
To add insult the Crossrail sidings became operational in May(TfL / MTR), and noise mitigation is still not in place in November. The old class 315 trains that share the new Crossrail sidings emit noise from their compressors throughout the night. This really should have been forseeable and certainly would have been raised by residents if the design intent had been communicated and residents consulted.
Our suffering continues..