The present and future of eddy-current brakes
Posted: 12 September 2016 | Daniel Valderas | No comments yet
The ECUC project (Eddy-CUrrent brake Compatibility) is a three-year collaborative research and development (R&D) project co-funded by the European Commission which aims to show that eddy-current brakes (ECBs) are a highly effective and applicable solution for increasing the braking capacity of new high-speed trains. Moreover, it aims to solve the concerns raised by infrastructure managers by proposing concrete and realistic solutions to overcome any possible drawbacks that ECB have experienced on some lines. The ECUC project proposes ECB electromagnetic and thermal models; new designs and test procedures; as well as Project Recommendations for the correct interoperable functioning of the ECB in a complex railway system. ECUC Coordinator, Daniel Valderas, explains more.
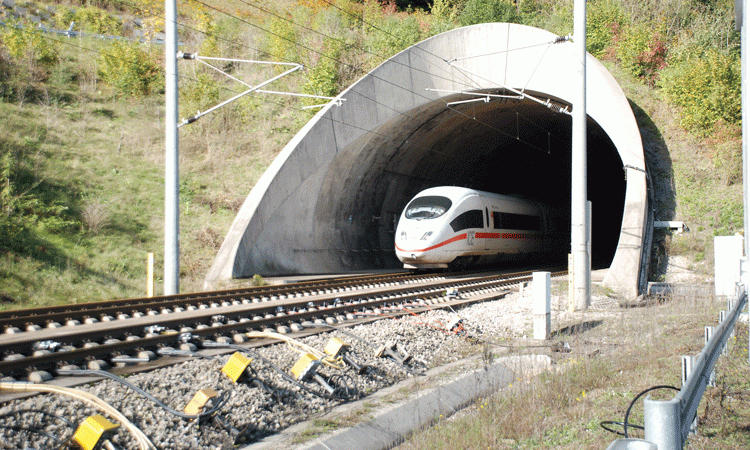
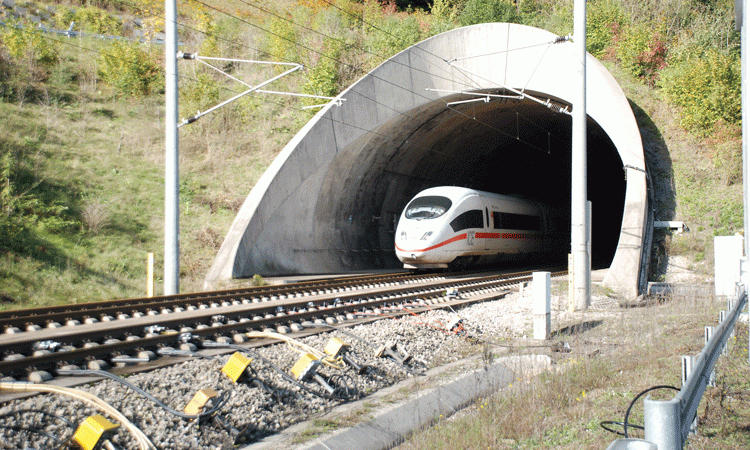
Running test in ECUC for ECB compatibility verification with an ICE3 high-speed train
Consortium
The ECUC consortium is composed of eight partners: Ceit-IK4 (Coordinator), Knorr-Bremse, Alstom, SNCF, Deutsche Bahn, Network Rail, UNIFE and Frauscher. The research team includes all the key players needed to accomplish the proposed challenge: large and small-medium enterprises; one European association; a research centre; railway operators and infrastructure managers. These partners have gained extensive knowledge whilst working in key positions in the development of ECB. This positive starting point means that progress beyond the state-of-the-art has been facilitated through an improved understanding of the interaction between eddy-current brake, track and trackside signalling equipment.
Physical principle
The linear ECB is based on a simple principle: a magnetic field across an air gap between the bogie mounted magnets and the rail head produces a braking force. Therefore, there is no mechanical contact between the brake and track: no-wearing, no smell and no fine-dust are emitted. The use of linear ECBs in rolling stock shortens the stopping distance and reduces the dependency of the actual braking capability on the wheel/rail adhesion properties. Moreover, these brakes also allow the use of friction braking systems to be considerably reduced, thus reducing their lifecycle cost to a large extent.
ECBs have been applied successfully in Germany for many years in a number of vehicles. The main difficulties in extending its application to other countries in Europe are based on Electromagnetic Compatibility (EMC) with wheel sensors located alongside the track and possible track buckling due to the elevated rail head temperatures, which increase longitudinal forces and introduce extra vertical ones. In the context of the ECUC project, computational models are provided to study worst case conditions for ECB-wheel sensor and ECB-track interaction. The study has been performed in two domains: electromagnetic and thermo-mechanical.
Scope of the project
Knorr-Bremse’s L4 and L5 linear ECBs are considered in the study. From an EMC point-of-view, their interaction with Frauscher RSR 123 and RSR 180 axle counters is considered. Three cases have been studied: the presence of ECB passing by the signalling device (where the mere existence of a metallic mass can be interpreted by the axle counter as a ‘wheel’); the analysis of the ECB switched on with low frequencies involved (Hz) coming from the induction caused by a fast moving DC source; and the analysis of the ECB switched on with high frequencies (KHz) emanating from the harmonics of the power supply. After contrasting the model outcome with data obtained from a measurement campaign, worst interference conditions can be anticipated. The EM model is realised within a CST Microwave Studio environment.
One of the outcomes of the model and measurement analysis is that interferences of ECBs at the frequency of operation of axle counters probably won’t be the most important factor to watch. The interaction of ECBs and axle counters are realised through the rail, to which both are very close. It is the change in the properties of the rail – caused by the action of ECBs – that could hypothetically impact the axle counter readout.
The thermal model provides temperature in the rail after the use of ECB and it can be compared to maximum temperature levels provided by technical specifications. Different scenarios are considered: varying the velocity of trains; the frequency of operation; rail initial temperature and ambient temperature. Thermal calculations are focused on UIC60 profile. Fitting of parameters to consider evacuation of heat (through convection) is based on experimental results. Evacuation of heat through the lateral surface is also covered in the model. The temperature model is realised in FEM. All kinetic energy is assumed to be converted into heat and introduced to the rail.
The model supports scientific knowledge of the actual phenomenon. For instance, intuition says that maximum speed (300km/h) and brake performance will lead to a maximum track temperature increase. However, in reality that it is not always the case. The modelling and measurements show that there are speeds that are more critical for rail heating in combination with maximum ECB performance, such as 120km/h.
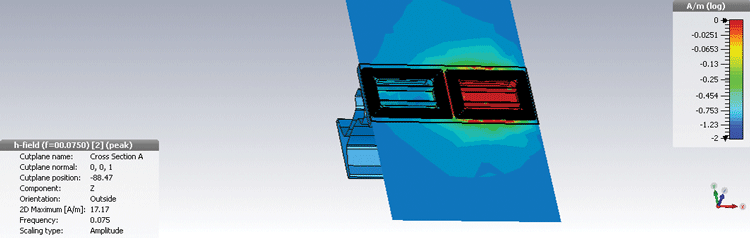
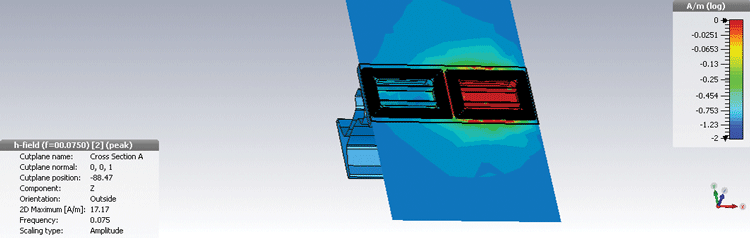
Figure 1: Snapshot of part of the ECB Electromagnetic model by ECUC
Test procedure and recommendations
Furthermore, the design of a test set-up and test procedure towards approval tests definition for linear ECBs has been developed. In the test procedure, worst case conditions are recreated for compatibility with axle counters. A key feature of the project was the design and implementation of state-of-the-art testing facilities. Using the Knorr-Bremse test bench, the ECUC team designed a physical set-up for testing different ECB systems under real-world conditions.
With the setting of the model and the test procedure in place, the development of new design, engineering and operational guidelines for ECBs and trackside signalling equipment are provided so that a proper input for the current standardisation process can be technically supported.
For example, each country has its own tabulated threshold track temperatures over which there is a certain risk of infrastructure damage. This temperature limit can now be observed from the point-of-view of ECB performance superimposed on the current agents that increase rail temperature. In the case of electromagnetic emissions, the standard that probably lies closest to the study is the CLC TS 50238-3, which defines compatibility between rolling stock and train detection systems, particularly in regard to axle counters. However, this standard ignores the usage of ECBs. ECUC does not intend to directly impact on any standard, but can initiate a review by providing insights and recommendations.
In this manner ECUC defines Project Recommendations for the correct interoperable functioning of the ECB in a complex railway system and provides input for revisions to Technical Specifications for Interoperability.
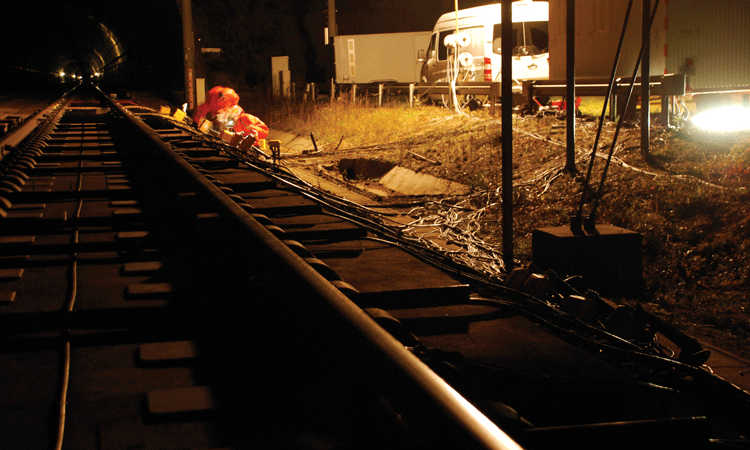
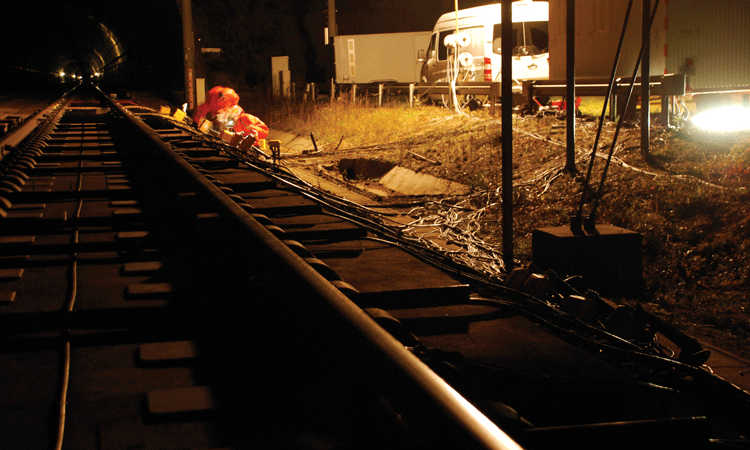
Preparation of the measuring campaign in ECUC
In this context, it is observed that the following techniques can be applied to reduce ECB emissions:
- Improvement of the filter strategy, either by redistributing current filtering on critical points or by adding extra coils (e.g. like the ones corresponding to the actual magnet)
- Extending the cable length from the traction container to the first magnet at each side by four times, for example
- Decreasing the parasitic capacitance of the first pair of poles of the first magnet connected to the traction container (for instance by decreasing the height of the poles)
- Feeding in parallel the aforementioned pair of poles
- Shielding them by a metallic sheet.
New generation ECB
According to these and other recommendations, a new generation ECB is outlined in the project to meet present and future EMC and thermal compatibility demands and ensure proper and safe expansion of its usage.
Conclusions
The ECUC project’s roadmap has covered the following items:
- Improvement in the understanding of the interaction between the eddy-current brake and the track and trackside signalling equipment
- Identification of critical thermo-mechanical and electromagnetic parameters and the related vehicle and trackside compatibility limits
- Design of a test set-up and test site that enables approval tests for linear eddy current brake systems focusing not only on the functionality but also on thermal, mechanical and electromagnetic requirements
- Design of a test procedure that recreates representative worst-case conditions to prove the compatibility between eddy-current brake, rolling stock, track and the signalling systems
- Development of engineering and operational guidelines for eddy-current brakes and trackside signalling equipment
- Inputs for the standardisation process of ECB
- Design and manufacturing of a New Generation ECB.