Safety of the railway axle: The last mile for EURAXLES
Posted: 21 March 2014 | Léa Paties, Raimund Abele | No comments yet
The recent intermediate report from the European Railway Agency (ERA) on the development of railway safety in the European Union has shown that the safety of the European railway system has, undeniably, continuously improved. However, it is imperative that safety critical sub-systems or components – such as wheelsets and axles – are properly addressed in this complex context. It is within this framework that the EURAXLES1 project was launched in November 2010 as a three and a half year Research and Development project coordinated by UNIFE. This EU-project, funded via the Seventh Framework Programme for Research and Development is bringing together 23 European partners, covering the rail sector, with the final goal to minimise the risk of axle failure in rail transport to such a level that it is not considered as a significant threat to the safe operation of the European interoperable railway system.
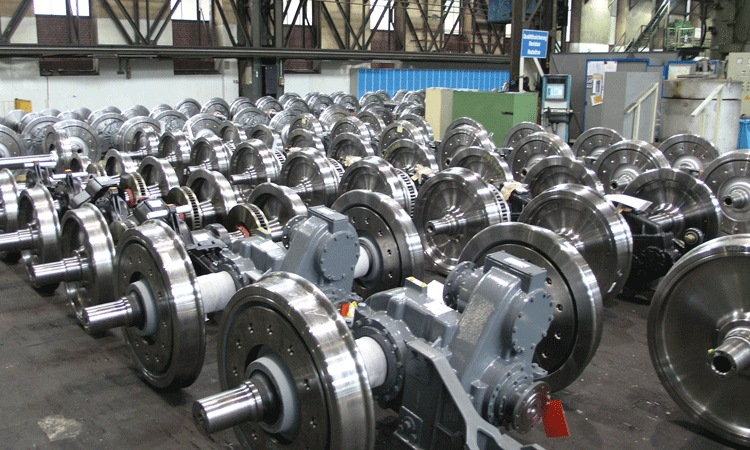
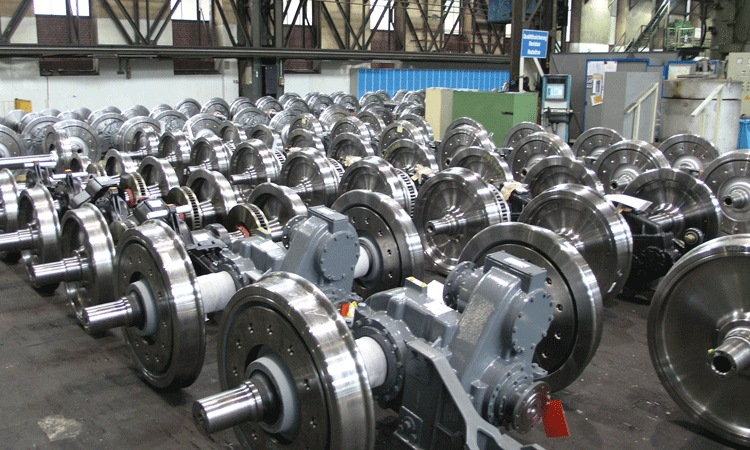
Realising the necessity of finding an inclusive solution to the European system, the project brings together the major players in the entire rail sector, including manufacturers, operators, suppliers, and academics. With a potential 3.5 million axles in service today throughout Europe, the EURAXLES project advocates an innovative and global approach that may be adopted in order to further decrease the risk of axle failure.
EURAXLES aim
The primary aim of EURAXLES was not only to guarantee the current level of safety, but improve it in an interoperable network at an optimised cost. The main concept of the project was to follow three complementary routes which took into account in an innovative way the combined influence of axle design, production and maintenance standard parameters whilst retaining a safe management of the life-cycle. The results will be used to define new or improved standards for product requirements, design and maintenance.
As the project nears its end, we can now assess the first major achievements, according to its original objectives which included:
- To commonly agree at European level on an innovative axle design approach
- To develop: a) improved procedures for axle protection against corrosion; new design recommendation for unpainted axles; b) improved adhesion of coatings with a study of the roughness influence (adhesion and fatigue behaviour); improved quality test method for coating systems; c) new, innovative coating solutions, developed in public-private partnership between companies and universities. The new solutions also have to fulfil environmental requirements to avoid or limit VOC emissions.
- To evaluate and simplify new/improved Non Destructive Testing inspection methods that allow the in-service inspection of axles, so as to guarantee safe service conditions with a low impact on the vehicle availability.
- To carry out RAMS and LCC analyses that will allow a cost benefit comparison of the proposed solutions for an optimised market uptake.
The EURAXLES project plans to improve the definition of loads applied on structures for the freight and conventional main train categories. Current design standards only relate to maintenance practices but have no real link with the main defects observed in service. Additionally, the existing standards specify the criteria to qualify steel grades and their testing but do not allow the determination of fatigue limits, especially for new steel grades applied for high-speed train axles. Therefore, there is no margin for innovation in order to propose improved or indeed breakthrough solutions with the current standards.
EURAXLES already achieved developing load spectra for different rolling stock types, as well as for different kinds of track and different usages. In parallel, a method to analyse a fatigue load with variable amplitudes and determine a ‘fatigue-equivalent load’ is being developed. The next step is to define an approach to estimate the real distribution of the load severities by using the database, the fatigue-equivalent method and information from operation and to compare it to the normative load.
A severe fatigue-equivalent load will be used in Finite Element Analysis models, which provide more accurate results for complex structures such as power axles with many radius transitions. A probabilistic treatment of data will then allow a comparison between stresses and the strength of the structure, which will help determine the safety margin of the system. As a result, EURAXLES allows the development of innovative solutions based on risk analysis and not only on field experience.
Regarding the numerical modelling of axles, the project has developed recommendations for the accurate modelling of the axles with finite elements with special focus on the determination of the stress concentration factors in the different sections of the component. In addition, the fatigue behaviour of press fitted parts has also been analysed with the numerical models. Tests are being performed to validate the Finite Element models being developed.
The reliability and availability of railway axles in service depends among other influences on the surface conditions. EURAXLES investigated previous problems associated with existing surface coating methods (e.g. corrosion and damage), first through improved adhesion and new innovative coating and secondly through treatment processes. All this whilst considering the real service conditions and environmental requirements.
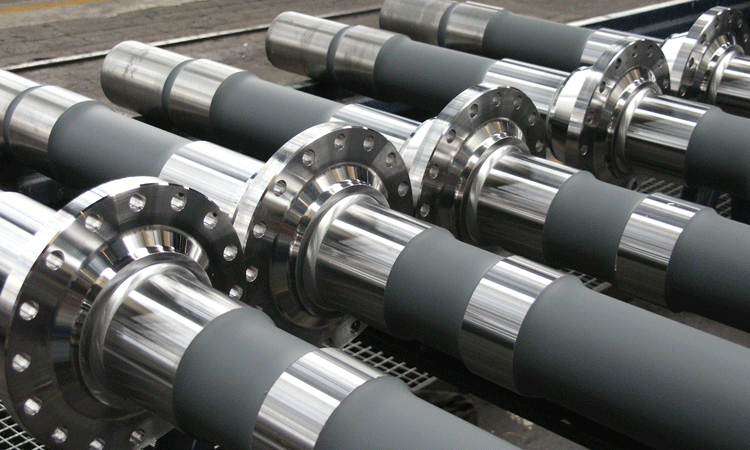
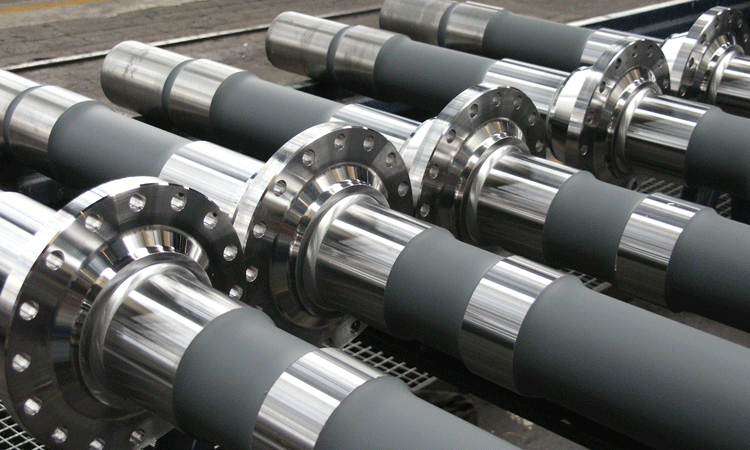
EURAXLES aims to minimise the risk of axle failure in rail transport
In view of their experience, the project partners analysed the results coming from an extensive survey among partners, European railway operators and the paint supplier advisory group. The current situation, existing solutions, national requirements and standards were investigated and determined their limitations in terms of coating process, quality test methods and validation of protective coatings. General recommendations for the whole painting/coating process will be given to improve the protection of railway axles. Expected results are also new surface preparations and procedures for the design method of wheelset axles, including new fatigue limits, associated to the alternative axle surface conditions (changed surface roughness or unpainted solutions) and their protection systems. Steel grid blasting with defined parameters and process description as an alternative surface preparation method for new-built axles was investigated regarding improved paint adhesion, impact on non-destructive testing and fatigue limit with promising results. New or improved quality test methods for painting and coating systems are proposed to be introduced in the existing standard. Alternative protection systems were also investigated, removing the need for traditional paint application methods, such as the improvement of corrosion resistance of wheelset axles by innovative coating processes without any VOC pollution. The results should also be the base for new improvements of painting/coating systems and simplify the development of new products for corrosion protection of railway axles.
Wheelsets are the most critical component for safety; for this reason they are periodically inspected to guarantee their structural integrity in order to prevent failure and vehicle accidents. EURAXLES plans to improve the currently used ultrasonic techniques for inspecting the complete volume of the axle, thus reducing the risk of human error, increasing the precision and optimising the periodicity of the inspection. The fatigue testing shall make use of readily available cracked axles.
New NDT techniques (e.g. the Laser Based Ultrasound Inspection Method) have already been studied. In order to be the most complete possible, theoretical aspects of the method are followed by results and measures obtained in the laboratory. Promising innovative techniques that might allow accurate inspection (including corrosion detection in the hidden spot of the axle) without the train stopping for several days have also been investigated. Promising results have been obtained when identifying the presence of a crack by means of sophisticated signal processing on vibration signals, obtained during working. These kinds of studies have been carried out in a scaled rig, and afterwards they were validated in a real axle installed on a lathe. The work continues to obtain promising results.
In addition, RAMS and LCC analyses that will allow a cost benefit comparison of the proposed solutions for an optimised market uptake have been faced. Results will be disseminated to the different stakeholders and the European standards/regulations for railway axles and, as a result, wheelsets will be improved across Europe. A survey to analyse the state-of-the-art of the RAMS/LCC techniques with particular emphasis in the railway sector has been performed. The results have allowed the consortium to identify the most relevant standards that are applicable to the different steps of a RAMS/LCC analysis and to define a common tool that will be used to compare the different innovative solutions. The tool takes into account the most relevant stages of the axle’s life-cycle which, according to the EURAXLES partners, correspond to the acquisition and operation phases with a differentiation between the preventive and corrective maintenance related costs. The analysis performed has shown that the risk of axle failure in service is very low – confirming that railway transport is one of the safest transport modes. In addition, it has been concluded that different approaches for the maintenance of axles are applied in Europe, showing a lack of harmonisation of maintenance rules in Europe.
The EURAXLES consortium comprised the main actors in the rail sector, all of whom have a strong desire to promote railway transportation as the safest and most economically competitive land-transport mode.
Reference
Republic. He has worked for more than 17 years in the railway suppliers industry. With good connections in the German and French railway industry, Raimund is especially dedicated to the small and medium sized component supplier enterprises. He is currently a Chair for ERWA (the European Rail
Wheel Association) which is an Associated Member of UNIFE – both of which are strong supporters of EURAXLES.
in 2010 and previously gained experience in EU research programmes and services to large companies as a Business Analyst in public subsidies at Ineum
Consulting in Brussels. Léa is the Coordinator of EURAXLES and is the Secretary of ERWA (the European Rail Wheel Association) as well as the Co-Secretary of ERRAC (the European Rail Research Advisory Council).