New rail freight traffic for 2015
Posted: 28 May 2008 | | No comments yet
This article discusses new technologies, dimensions and production systems for rail freight traffic – based on genuine situations in Germany.
This article discusses new technologies, dimensions and production systems for rail freight traffic – based on genuine situations in Germany.
This article discusses new technologies, dimensions and production systems for rail freight traffic – based on genuine situations in Germany.
The growth of goods traffic in Europe that has come along with globalisation and the actual discussions about the environmental impact of the transport sector require new concepts to increase the efficiency of rail freight traffic. The predicted growth of rail freight will soon exceed the capacity of today’s railway system. For this reason, operational innovations which will impact promptly will be necessary in order to cope with the expected growth at a customer-friendly service level. The intended enhancements of the network – which are necessary as well – may be implemented too late. In the view of many customers, rail freight is too inflexible, too expensive and too slow in comparison with other means of transport. However, the environmental friendliness and safety reasons speak in favour of it.
Nowadays, the dimensions of freight trains are limited, among other reasons, by the poor towing capacity of the antiquated screw coupling (see Picture 1). In contrast to this, in many countries like the USA, Canada, Russia, China, South Africa and Norway, freight trains with a gross weight of between 10,000 and 30,000 tonnes and a length of partly more than 2km are common. The railway undertakings, which run such trains, generate the lion’s share of their gains with them. Usually the networks in these countries are not as dense as in Europe and rail freight transportation is dominant, being in cases such as passenger rail transportation, almost inexistent. These conditions are thus very different to the ones existing in Europe. Notwithstanding this fact, the discussion about an enhancement of the train dimensions in Europe should not be finished here, particularly since the transportation market constantly strives for an enlargement of the transportation units.
The legislator defines the limits of the vehicles of the different modes of transport in order to harmonise the interaction between vehicles and infrastructure. With the aim of having reliable planning criteria, these limits can not be changed regularly. However, the market consistently demands consistently an enlargement of the vehicle sizes:
- With the aim of having a higher capacity (volume) and if applicable a higher payload, road haulers seek to have trucks with a length of more than 18.25 metres, which is the maximum allowed length in Germany. For that reason, the so-called EuroCombis or GigaLiner, which can have a maximum length of 25 metres and a gross weight of up to 60 tonnes, were – and partly still are – allowed to run in a testing phase.
- Inland vessels increased their size frequently during recent decades. Large inland freight vessels with a length of 110 metres and a breadth of 11.4 metres, that spread from the river Rhine to other waterways in the 80s, nowadays seem to be non-productive in many cases. Still, many waterways are not adapted to their size. Nevertheless, the inland vessel is increasing its size. For example, it is planned to adapt parts of the river Neckar for vessels with a length of 135 metres1.
- Airfreight grows in a scale that apparently makes giant air freighters profitable, which in the past only were used for military purposes.
- Again and again, it is requested to increase the railway loading gauge in Europe with the aim of transporting containers in two layers. With the existing gauges even Megatrailers or high-cube containers can only be carried by special wagons under the contact wire. Double-stack container cars, which are frequently used in the USA, require very expensive extensions of the gauge. Trace fees will not be able to recover the costs. Furthermore, double-stack container trains could only be realised on routes without contact wire.
The state has to find a compromise when balancing different aspects of a traffic system, such as in the attractiveness of the market, the costs of the infrastructure expansion, increasing maintenance costs and safety issues. This results in a rather complicated decision process that leads to some field tests but to no big changes at all. This is why a productivity increase of the freight transport system should be achieved within today’s boundary conditions or as a consequence of small changes, for instance by modifying only one of the limiting parameters.
Enlargement of the train dimensions
Today’s limiting boundary conditions
According to the DB guideline 408 ‘Züge fahren und Rangieren’(‘Running Trains and Shunting’), which is part of the terms of usage of the railway network of DB Netz AG, the length of a rake of wagons is limited to 700 metres. Including the traction units, the total train length can reach a maximum of 740 metres. This limiting parameter is employed to configure the railway infrastructure and the railway operations. On one hand, it gives concrete requirements for the usable length of train formation tracks and of overtaking points, but on the other hand, the process of forming trains is affected by this limiting parameter.
A train length of 740 metres means 35 to 50 wagons per train, depending on the kind of wagons. This number seems to be appropriate for the times of steam or diesel engines. But also the limits of the antiquated screw coupling and the pneumatic brake control are achieved with this limit of length. In order to reduce the longitudinal forces in the train to a level that prevents from derailments or breakings of coupling, the total weight of the train and the length has to be limited according to the characteristics of the track sections.
Longer trains
Freight trains with light goods rarely reach the load limit before reaching the length limit. Therefore, it is theoretically possible to run trains with more than 740 metres with conventional technology – traction at the head of the train, screw coupling and conventional air brake. For example, this could be the case with trains consisting of empty double-deck car carriers, reaching a length of approximately 900 metres. However, new solutions for the train formation have to be found because most of the train-formation tracks are designed for a maximum train set of 700 metres.
The clear track signalling systems based on the axle counting installations that are currently in use, limit the number of axles per train to 250. With four axles per wagon, this means a maximum of 62 units per train. Assuming an average length of 18 metres per wagon, a train set would reach a length of approximately 1,100 metres. With freight wagons with only two axles or with double-deck car carriers – that usually have an axle every 6 to 8 metres – 250-axled-trains would have a length of 1,500 metres and more.
During transport, extra-long trains can not stop in passing tracks, because these are built for trains of 740 metres. But even today it must be checked for each case if the length of the passing track is enough for the train, because many of these tracks are actually shorter. Keeping this in mind, the problem of the passing tracks seems to be solvable with an intense disposition of the extra-long trains in the operation centres. The extra-long trains could be handled as trains with out-of-gauge load.
Nonetheless, in the annual timetable overtakings of trains are avoided as much as possible because they decrease the capacity of the track. With a further implementation of the strategy Netz21 the problem of overtakings of trains outside of network nodes will diminish. Netz21 is a concept for a specialisation of tracks with a separation of freight trains and faster passenger trains.
The train formation of extra-long trains could be done a follows: two train sets of 500 metres would be formed on two tracks of the existing formation yard. After the inspection of carriages and wagons, a full brake test would be done for both train sets, using the main-line locomotive for one set and a fixed brake testing device for the other. Then the locomotive would pull the first train set out of the formation yard and push it back to pick the second set. Both sets would be coupled together and only a partial brake test would be necessary before the extra-long train starts. The estimated occupancy – approximately 10 minutes – of the outlet switches should be tolerable for this.
Splitting the train could happen analogously. The train would enter a reception track of the formation yard and disconnect one set that fits with the usable length of the track. Then the main-line locomotive would pull the remaining set out of this track and push it back into another one. For this, a loop line of the hump should be used to avoid an interruption of the gravity shunting. When pushing a train set with the main-line locomotive, a shunter will be needed at the rear of the train.
During the train run, a train with a length of more than 740 metres occupies two bloc sections at once – if having short blocs. According to this, the route for the next train will be released later and level crossings will stay closed for a few seconds more. Adaptations at the control and safety technologies will be necessary2.
The impact of such train runs on the train operations can be tested by simulations at exemplary routes – in the same way disturbance scenarios have to be investigated. The dynamics of vehicle movements of long but light trains should not differ too much from normal freight trains. Modern traction units have sufficient power for these kinds of trains.
The new European control and safety technology, ETCS, works without clear track signalling systems in the last level (level 3). For this reason, the train has to check its integrity by itself. This means that there has to be data communication between the head and the rear of the train. From a present-day perspective, rail freight can only achieve this with a new coupling system that includes an electric data wire. A wireless system can not guarantee a safe rear signal control. Therefore, new freight wagons should be retrofittable for automatic rear signal controls from now on.
The German railway infrastructure price system is based on a basic charge per train kilometre and it is independent from the train length. For heavy trains, surcharges have to be paid3. Therefore, it would be consequent to keep this system even with trains of more than 740 metres.
With the assumption of such a price system, a train operating company would cut down costs when using extra-long trains, because of the saving of a traction unit, a driver and a slot fee (in case of a double-long train). The network company could generate a higher utilisation of capacity and if applicable, sell another slot.
A successive introduction of extra-long trains seems possible regarding to the aspects mentioned above. Firstly, the trains could carry light goods as cars or car parts or run as empty block trains (two separate trains for the load run, a double-long train on the way back). This could be done nearly immediately, operational problems are not expected. Secondly, to comprise trains with homogeneous load characteristics as block trains or intermodal trains. Later on, mixed trains with loaded and empty wagons (single wagon trains) could be operated as well. Multiple units (master- and slave-locomotives) should be distributed within the train set. For this technology the authorisation is still missing in Germany.
The aim of the project ‘GZ 1000’, which is funded by the Federal Ministry of Economics and Technology, is to proof the feasibility of extra-long trains of approximately 1,000 metres in Germany. In this context Deutsche Bahn AG already ran test runs in March 2008, with trains of more than 800 metres between Maschen near Hamburg and the Danish station Ringsted. In Denmark, trains with a length of 835 metres are already allowed3, 4.
Increase of the gauge
The main problem of today’s gauges of Europe’s railways is the limitation in the upper corners, which reduces the possible height of intermodal loading units and which is the reason for the barrel-shaped roofs of covered freight wagons. The gauges are a result from the profiles of old tunnels and arched bridges. Step by step, these restrictions disappear from the network, but there is no consequent extension strategy.
It will not be possible in the near or mid-term future to run double-stack container trains in Germany. Anyway, the permitted gauge should be transferred shortly to the GC-standard. In light of the growing demand for transport volume in the logistics sector, this would definitely enhance the efficiency of rail freight.
Central buffer couplings
The automatic central buffer coupling Transpact (Faiveley) is compatible with the UIC screw coupling. Therefore, it can be implemented step-by-step. If used exclusively in special trains, all advantages can be used immediately. The air-brake hose and an additional electric bus for data transfer or power supply couple automatically as well. No laborious coupling by hand will be needed any more. One advantage of the electric data bus is the possibility of transferring the brake impulse with the speed of light (electro-pneumatic brake). In today’s rail freight traffic the information is transferred via a decrease of air pressure with sonic speed, needing up to three seconds to reach the last wagon. The electro-pneumatic brake is generally used in the case of passenger trains since years, but it failed in rail freight until now because of its costs. The time consuming and personnel-intensive brake test, which is necessary before the train runs, could be done in a few minutes by one person using the data bus and additional devices (e.g. brake position sensors). Besides, the order of the wagons would be checked automatically.
Automatic central buffer couplings will reduce the intensive longitudinal dynamics of today’s trains. In order not to exceed the maximum towing capacity of the draw-bar of the screw coupling, nowadays it is necessary to start cautiously and to limit the train length and weight. Furthermore, after a full implementation of the new coupling, the side buffers could be left away, thus enabling easier and lighter wagon structures. This way the traction energy consumption could be reduced.
Flexible operation
The private railway sidings, where the wagons are loaded or unloaded, are basic production items in conventional railway freight transportation. If the operators of the railway sidings do not own shunting equipment themselves (like shunting locomotives or road-rail vehicles) they are forced to hire shunting services from a railway undertaking that fetches and delivers wagons for them locally. Usually, this service is performed according to the railway undertaking timing criteria, which normally does not match with the logistics of the rail siding owner.
In this context, a concept for a self-propelled freight wagon is being investigated. The wagon is operated via radio-remote-control. Thereby, this technology would enable the operators of private sidings to move the wagons within their areas. The working time of the railway undertaking’s locomotive for delivering and fetching the wagons could be reduced in many cases. The biggest effects are expected in huge factory sidings.
New production systems
Conventional rail freight traffic mainly consists of the production systems block train and single wagon traffic. A block train transports goods directly from the loading location at the customer’s to an unloading site of the consignee; it usually operates empty when coming back. In the case of single wagon traffic, the wagons are collected from railway sidings and sorted in marshalling yards. Following this, they run as one train to the next marshalling yard, where they are sorted again. These operations can take place several times before the cars reach their destination, explaining why the commercial speed of single wagon traffic is very poor. Beside these production systems, the intermodal transport has gained relevancy over recent decades, which uses initial and/or final legs carried out by road.
With the new Train Doubling (TD) system, two given trains are coupled in order to run a certain railroad section as one train. However, with the current train length limitation of 740 metres only relatively few train combinations could be interesting from a productive point of view. In order of being profitable on the initial and final legs, a train should be longer than 400 metres. If the maximum train length would be raised to 1,500 metres (or more), TD would suddenly become a primary option for increasing the economy of rail freight transportation.
The Train Coupling and Sharing (TCS) system is still more consequent with the principle of coupling train modules. Groups of wagons with their own traction (TCS-modules) are coupled together in intermediate points with other TCS-modules that match in time, location and direction. After running a part of their individual routes jointly they split into several TCS-modules again. In an ideal case, this could happen while normal running or during short stops in sidetracks. With this system, it would be possible to avoid the time consuming stops at the marshalling yards on dedicated relations without consuming too much traces. Evidently, TCS systems require an automatic coupling and a locomotive remote control system for the distributed traction.
Own investigations resulted in a door-to-door speed of 50 kilometres per hour that could be reached with TCS, which is comparable to the speed of the existing block trains or road traffic. In contrast to this, single wagon traffic between railway sidings and over rail yards reaches a commercial speed of less than 20 kilometres per hour.
Vision
The productive freight railway runs extra-long trains with double-stack container cars and high capacity wagons with at least 25 tonnes load per axle, powered by multiple traction. The trains run over long distances either directly between shippers and consignees or between important freight centres by means of effective marshalling – for example with TCS.
The freight cars have an automatic central buffer coupling and concomitantly an electrical trough-passing wire, enabling them to use the electro-pneumatic brake, to execute automatic brake tests, to control the train integrity and to monitor the condition of the transported goods.
The quality of freight railways is similar to that of road freight just as the system costs. The majority of the goods are containerised and there are transhipment facilities (road–rail) close to freight villages as well as a number of shippers’ railway sidings connected to the main railway network.
The railway network is consistently divided according to the concept Netz21. There are exclusively dedicated tracks for long-distance passenger traffic, for urban and suburban traffic and for freight. All network sections are restriction-free and working at full capacity.
Finally, the network administrator can cover its expenditures for maintenance, replacement investments and new constructions of infrastructure. This is possible by rationalisation and increased traffic.
The last section has portrayed a vision. But all technologies for this vision are available and the political will to support the environment-friendly railway is still given. The goal should be a freight railway that works without subsidies and which achieves a modal share twice as high as today. It therefore requires the encouragement of the driving forces to pursue this large goal within a long-range strategy. For this, privatisation is not necessary. The pressure on the freight market should already be high enough. A private railway undertaking will never – with or without the network – have such good terms of financing as is the case today. So, let’s get on with it!
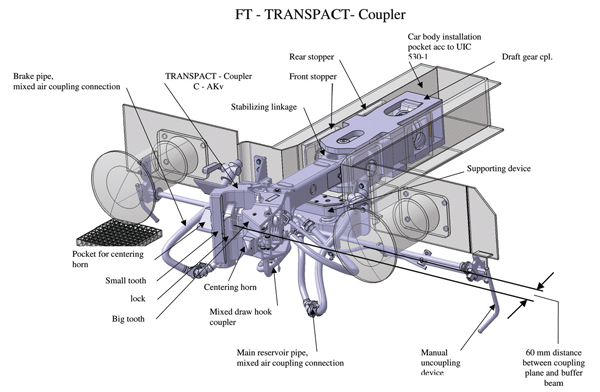
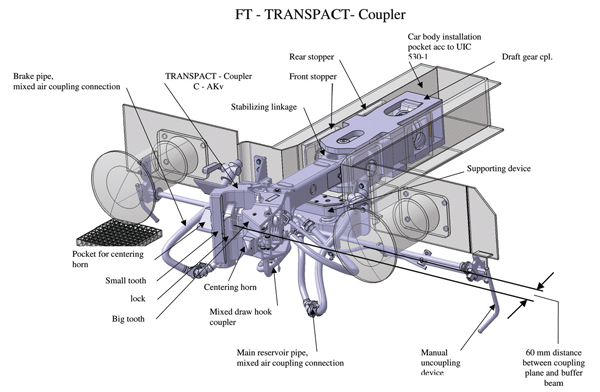
Figure 3: The new coupling Transpact


Figure 4: The train coupling and sharing system
References
- Investitionsrahmenplan bis 2010 für die Verkehrsinfrastruktur des Bundes (IRP), Anlage 3, Bundesministerium für Verkehr, Bau- und Stadtentwicklung, April 2007
- Der Eisenbahningenieur 04/2008, S.72: Längere Testzüge nach Dänemark
- Schienennetz-Benutzungsbedingungen der DB Netz AG (SNB), Abschnitt 6 Entgeltgrundsätze sowie Trassenpreissystem, Liste der Entgelte der DB Netz AG 2008 für Trassen (http://www.db.de/site/bahn/de/ geschaefte/infrastruktur__ schiene/infrastruktur.html)
- Bundesministerium für Wirtschaft und Technologie: GZ 1000 – Betrieb mit längeren Güterzügen (http://www.bmwi.de/BMWi/Redaktion/PDF/S-T/transport-logistic-gz1000,property=pdf,bereich=bmwi,sprache=de,rwb=true.pdf, Download 23.04.2008)