Laser scanners and drones enable investigators to reconstruct major train derailment
Posted: 27 August 2019 | Mary Jo Wagner | No comments yet
Detective Eric Gunderson of the Washington State Patrol led the accident reconstruction phase of the Amtrak passenger train derailment near DuPont, Washington, United States in 2017. In this interview he explains how using laser scanners and drones played a huge part in the accident investigation process.
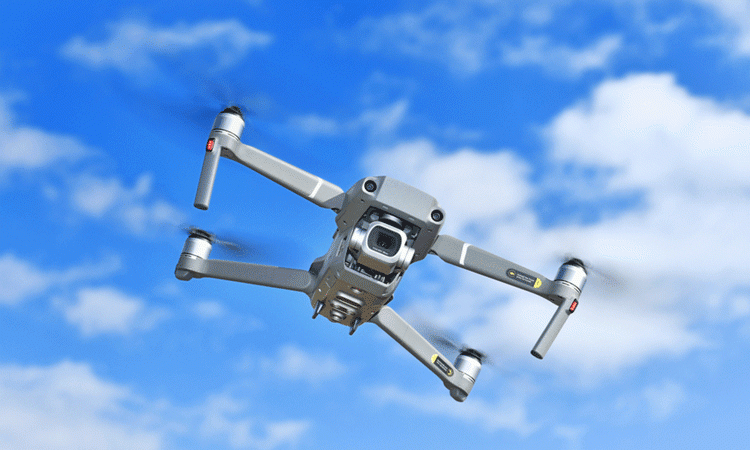
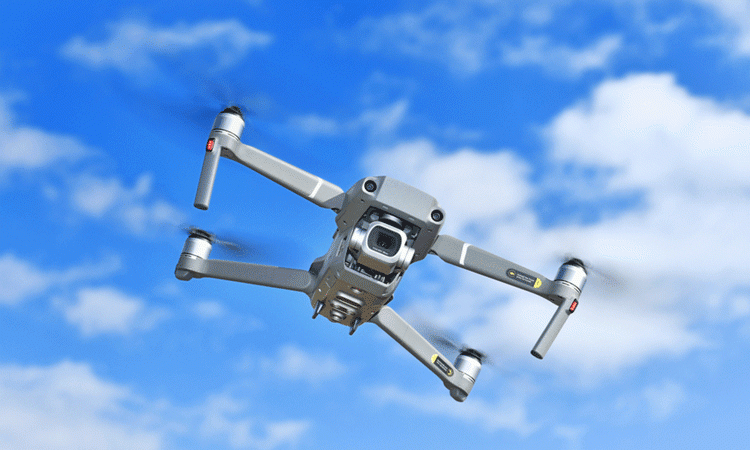
On 18 December 2017, an Amtrak passenger train was making its inaugural run between Tacoma and Portland, Oregon in the U.S. As it neared a curve leading to an Interstate-5 (I-5) overpass near DuPont, the train was travelling at 78mph – 50mph over the speed limit – and the lead locomotive, along with 11 of its 14 rail cars, derailed. It was 7:33 a.m. and I-5 was already teeming with commuters. The lead locomotive and three rail cars landed on I-5, causing a 14-vehicle pile-up. Three of the 77 passengers on-board the train were killed, and 62 passengers and six crew members were injured. The initial damage was estimated to be $40 million.
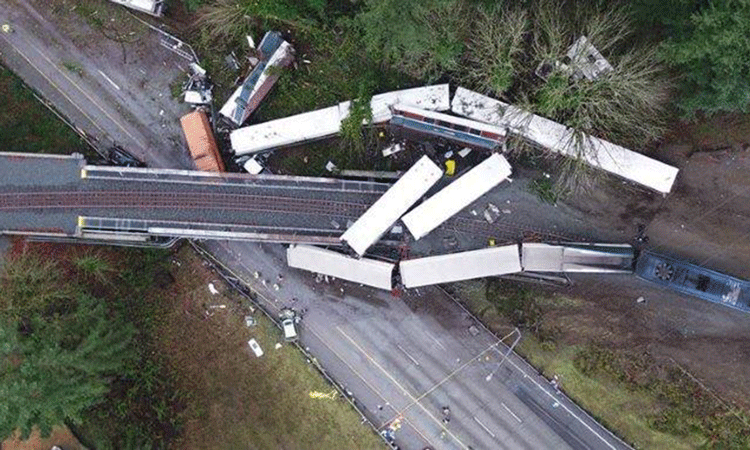
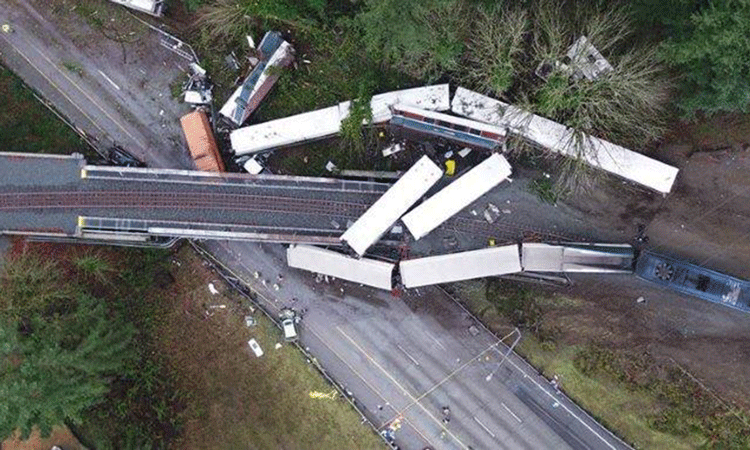
The as-found scene of the Dupont train incident where 11 of 14 rail cars of an Amtrak derailed, killing three people and injuring 62 passengers and six crew members
Detective Eric Gunderson of the Washington State Patrol (WSP), said: “Where this happened couldn’t have been a worse spot as far as impact to the region. I-5 is the major artery between Tacoma, Olympia, Portland and Seattle. With Puget Sound to the west, the Nisqually River to the south and a military base to the east, your only driving option is I-5.”
WSP troopers were on scene within five minutes of the accident. By 8:30 a.m. the scene was swarming with hundreds of troopers, detectives, firefighters and paramedics, all of whom had one thing on their mind: Rescue.
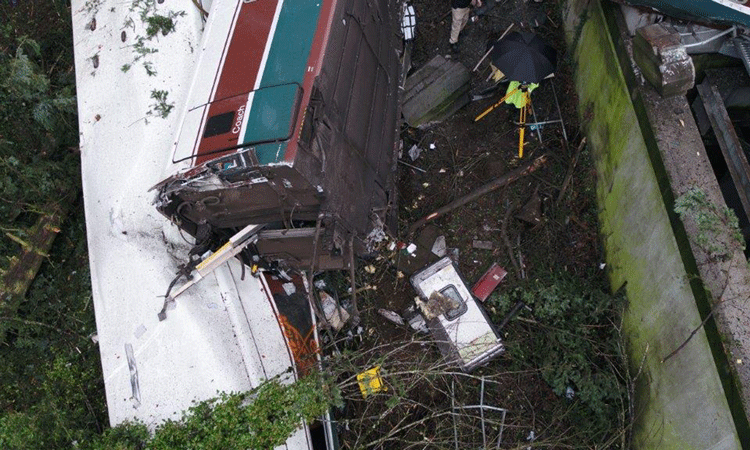
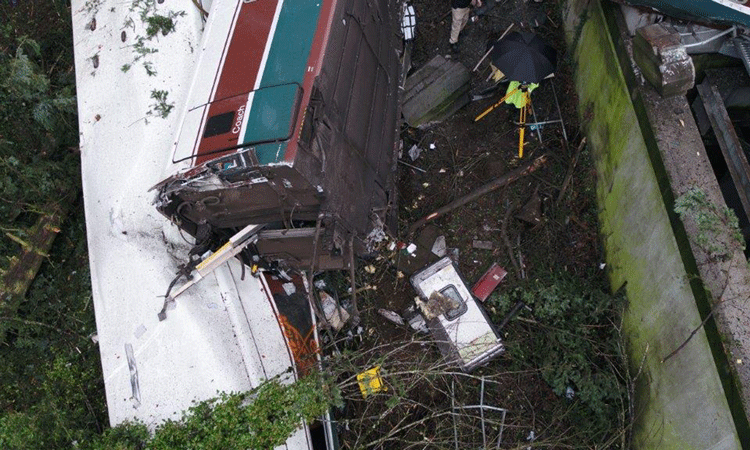
A TX5 stands protected by the elements as it scans the mangled rail car in front of it.
Eric continued: “For that kind of incident, the last thing you’re thinking of is preserving evidence. If I need to move a train or car to get someone out, that’s what’s going to happen. So, our first hour was consumed by all lifesaving first. But once we cleared the scene, everything began to slow down and we could start investigating. Then we owned the scene.”
Working in collaboration with the National Transportation Safety Board (NTSB), the lead investigating organisation, Eric led the accident reconstruction phase, bringing in four Trimble TX5 scanners and one DJI Matrice 200 UAV. Although he had been successfully using Trimble RealWorks Forensics to merge scan and UAV data into point clouds, he had never applied the approach to an incident of this magnitude.
Teams of WSP collision investigation detectives first walked through the debris-riddled scene, taking photographs, painting the footprints of important objects such as cars and tire marks, and documenting them. In parallel, he dispatched two teams per each of the four TX5 scanners and split them into two groups, one to work on the overpass section and one to manage the roadway section.
Setting up on each end of the tracks, the railway teams methodically moved towards each other, scanning all four sides of the individual rail cars and any strewn debris, and recording each object as it was found. The ground crew followed the same process. Starting at each end of the I-5 scene, the teams collected data points of the rail cars, vehicles, roadway, tire marks, paint marks, and anything that lay within the boundaries of the accident. In total, the four teams collected 82 scans and more than one billion data points in five hours.
“What’s awesome about scanning is that it ensures you don’t miss anything,” said Eric. “At the accident scene, you only get one shot to get what you need. You can’t put the trains back where they used to be, so you need to be right the first time. Scanning captures everything incredibly quickly and often captures something you didn’t know you’d need.”
While the teams were scanning the tracks and roadway, Eric flew the 920ft-long by 340ft-wide scene with the UAV. After a 10-minute set-up, he flew an overall pass at 200ft at roughly 70 per cent front lap and 50 per cent side lap to establish a base. He flew a second pass at 100ft and a final flight at altitudes between 15ft and 50ft to acquire some oblique photos. In 89 minutes, Eric collected 682 photos with the unit’s 20MP camera.
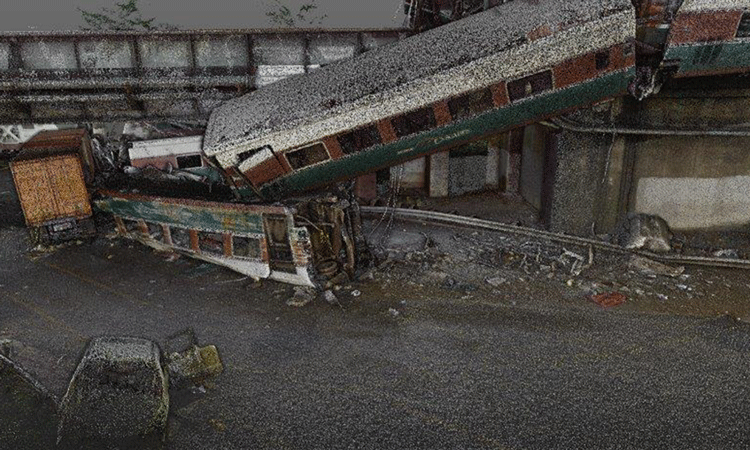
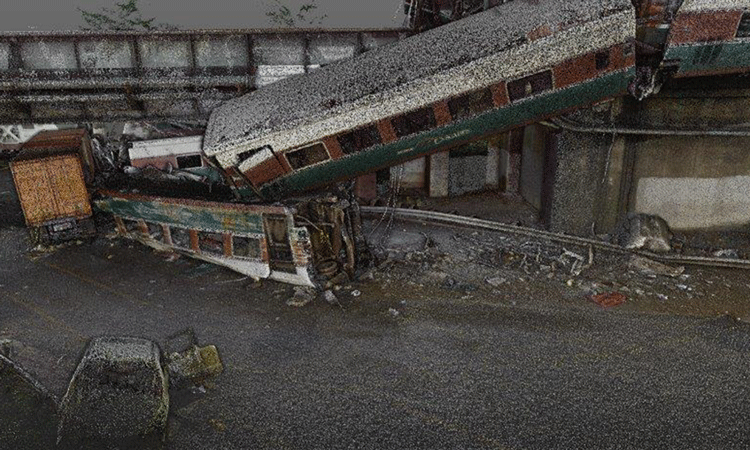
The wreckage captured by a Trimble TX5 laser scanner. In total, four teams collected 82 scans and more than one billion data points in five hours.
Eric said: “I could’ve handled the accident with just one technology, but given its scale, I wanted to have data redundancy. The drone would provide different view angles since the scanner can’t get the top of the train. In addition, with the volumes of data I’d collect, it would be a great opportunity to test how well I could merge the two massive datasets together.”
By 14:00 that afternoon, Eric was able to pack up the gear and head back to the office to process the data.
Creating a complete 3D picture
For efficiency, Eric loaded the UAV photos into their photogrammetry software for batch processing overnight, so when he returned to the office the next morning, the data would be ready.
Preparing the 3D point cloud began by importing the 82 scans into the RealWorks software, which allows investigators to quickly register, segment and classify 3D laser scan data for analysis and reconstruction. As there was data from four different scanners, Eric had to first group and register, or ‘stitch together’, all scans from each scanner to produce four scan-data groups. Then he merged each of the four groups to create one overall point cloud.
Since teams were collecting data during the active accident investigation, the scanners also captured the hundreds of responders working the scene, which resulted in superfluous or ‘parasite’ points. RealWorks provides automated clean-up tools to help clear unneeded points. With the automatic classification feature, he moved irrelevant objects into designated layers and removed the parasite measurements from the finished point cloud.
Eric said: “RealWorks’ ground extraction tool is excellent. I can separate the ground from another layer, and then cut out the parasite points like the police cars, fire trucks, and people walking around so I can produce the clearest model possible. Being able to almost freeze the scene gives us more confidence when investigating after the fact.”
With the laser scan point cloud complete, Eric focused on importing the processed UAV point cloud into the RealWorks point cloud. Once imported, he used the automated extraction tool to clean up and remove any superfluous points and then combined the dataset with the master point cloud to produce the final 3D model of the train derailment. The two came together perfectly, he says.
“Integrating UAV data into RealWorks is nearly seamless because the software views the data as a laser scan file,” said Eric. “Pairing the tops of the train cars from the UAV data with the scanning data of the cars gives us a complete view of the incident scene, and one we wouldn’t have if we had just used one technology. You can spin the model, rotate it, move along any axis, measure anything and zoom in. It’s just like being there.”
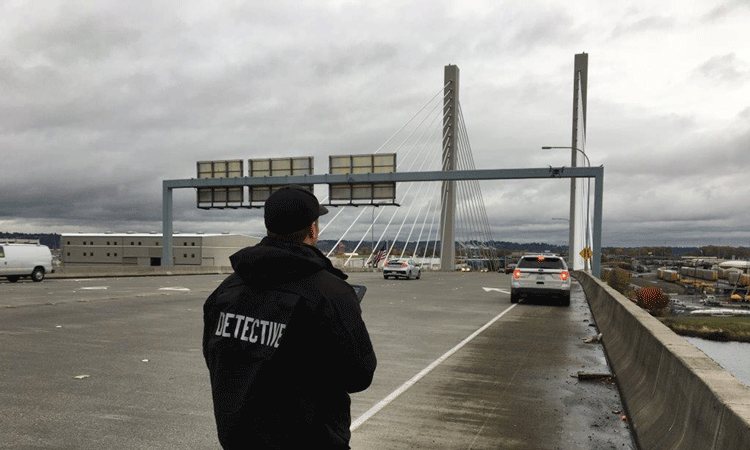
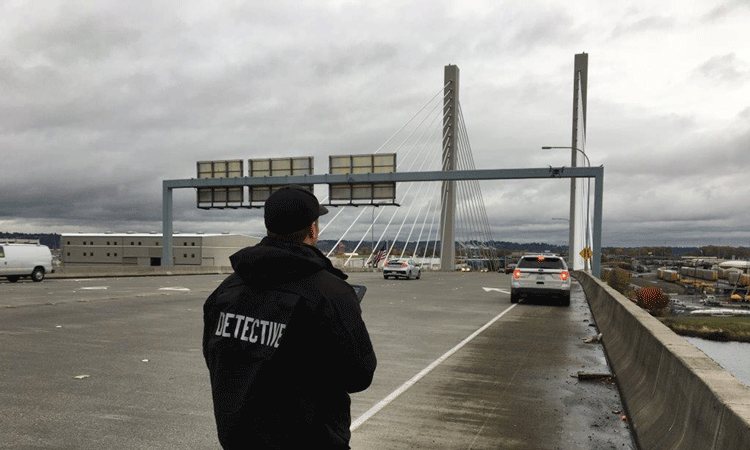
Detective Gunderson operates the WSP’s Matrice 200 UAV.
In total, it took Eric approximately nine hours to create the finished incident model. In less than 36 hours after the initial derailment, he was able to provide a 3D view of the entire accident scene.
That afternoon he presented the NTSB with the 3D data and ‘walked’ the officials through the point cloud, demonstrating its visual content and its capabilities.
Eric said: “They were wowed by the model. I don’t think they’d ever seen something like this before and as I moved through the scene, they could immediately see the benefits of the detail, accuracy and interaction the point cloud provides for their investigation. They can now revisit the scene from their desktops anytime they need to find evidence or verify details, and they may even find something new to aid the analysis.”
Finding answers
The final point cloud result of the DuPont train derailment not only demonstrated the success of Eric’s multi-pronged approach, it helped cement these technologies as core data sources for the WSP.
Eric said: “The benefits of the laser scanner and the UAV are unparalleled. I can’t fly the UAV in a house, but I can definitely scan it. But if I have a mile-long accident scene, I can fly that in five minutes, and I can supplement with the scanner. I can capture great scanning data at each end of the scene and then connect the two in RealWorks. Having these choices allows us to tackle any scene.”
Last summer, the department upgraded their scanners and acquired three Trimble TX6 laser scanners. The new units give them 500,000 points per second, better intensity detail, which makes objects stand out more clearly, faster scanning and the ability to scan in the rain – an important feature for the Pacific Northwest.
They also launched a UAV pilot programme in July 2019 and outfitted 15 collision technology specialists across the state with smaller UAV units. The aim was to assess whether the technology could help them map straightforward accident scenes more efficiently and accurately. Soon after the pilot began, a team responded to a one-car pedestrian accident on I-5. Prior to the UAV, they would have worked the scene for a few hours with traditional baseline methods. Using the UAV, they cleared the scene in 18 minutes.
Eric said: “Someone from the state DOT (Department of Transportation) once told me that any time the I-5 is shutdown, the cost to the region is approximately $350-$400 a minute. That adds up to a big number really quickly.”
Based on the success of the pilot, the WSP is adding 75 smaller UAVs to its force and more than 50 WSP detectives have been issued the smaller UAVs.
“Pushing the envelope with our technology is having a huge impact,” said Eric. “We could never have trained for an incident like the derailment. But when it happened, we didn’t hesitate to respond because we knew we had the technology and tools we needed. You’re going to have victims who want answers and investigators who have to give those answers. Our ability to provide information that will help people find the answers feels really good.”
The author of this article is Mary Jo Wagner, a freelance writer who has been covering the geospatial industry for 25 years.
Related topics
Drones, Safety, Technology & Software, Training & Development