Towards a real assessment of Scope 3 emissions by rail operators
Posted: 23 May 2023 | Herbert Minarik, Leena Jäger, Matthias Landgraf, Sven Schirmer | No comments yet
Herbert Minarik, Sven Schirmer, Leena Jäger and Matthias Landgraf explain how the Austrian Federal Railways (ÖBB) successfully tackled the first steps of volume data collection.
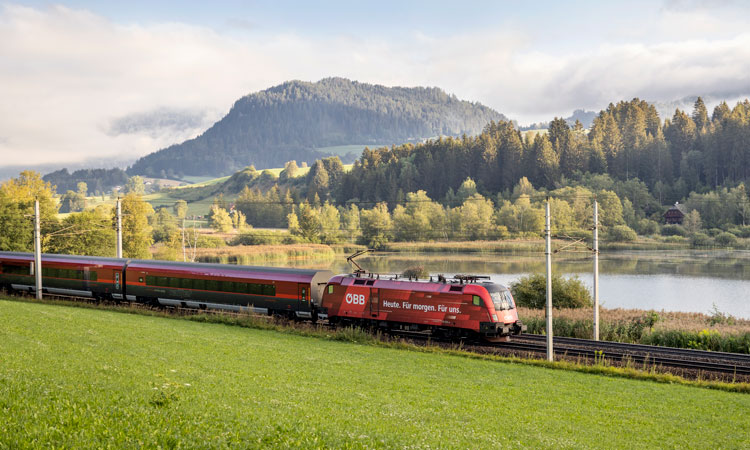
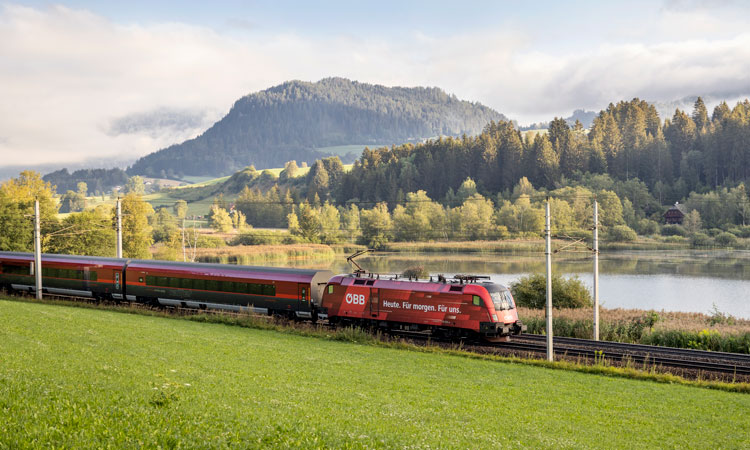
Credit: ÖBB
Initial situation
ÖBB is a company focused on sustainability. It bears economic and social responsibility, as its business activities have an impact on the environment and society. However, while establishing sustainability as a strategic focus and setting ambitious goals is one thing, implementing appropriate initiatives and measures and thus continuously improving sustainability performance is another. The measurable achievement of goals is also important, as is transparent reporting. The balancing of greenhouse gas (GHG) emissions is an essential basis for ÖBB’s decarbonisation paths and an important component of reporting.
A wide range of standards must be considered in reporting, such as those included in the GHG Protocol. Due to the implementation of the Corporate Sustainability Reporting Directive (CSRD), further new reporting obligations and standards will follow for ÖBB from the reporting year 2025 onwards. The European Sustainability Reporting Standards (ESRS) define new mandatory disclosures for climate reporting. In addition to Scope 1 and 2 emissions, the reporting of Scope 3 emissions will also be mandatory in accordance with the GHG Protocol. A valuable effect is that the knowledge of concrete quantities also serves as a profound basis for the development of a circular economy strategy. This is also a topic that is gaining new importance within the framework of the ESRS.
The GHG Protocol defines Scope 3 emissions as “all indirect emissions (not included in Scope 1 and 2) that occur in the reporting company’s value chain, including upstream and downstream emissions.“
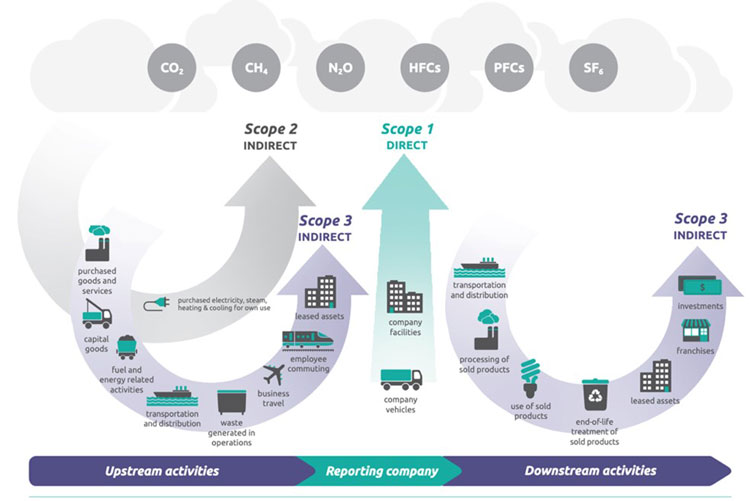
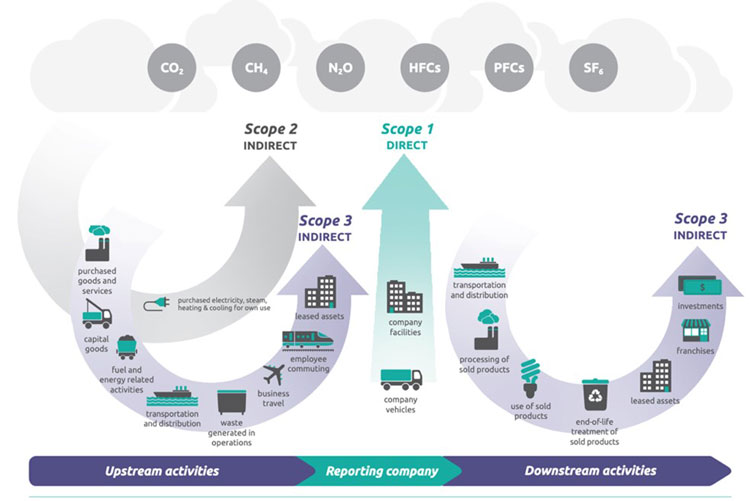
Figure 1: Direct and indirect THG-Emissions (https://ghgprotocol.org/sites/default/files/standards/Corporate-Value-Chain-Accounting-Reporing-Standard_041613_2.pdf)
For rail operators, indirect emissions account for between 80% and 90% of total emissions. This can be seen from individual sustainability reports of other rail operators. Upstream and downstream emissions are structured in a total of 15 categories.
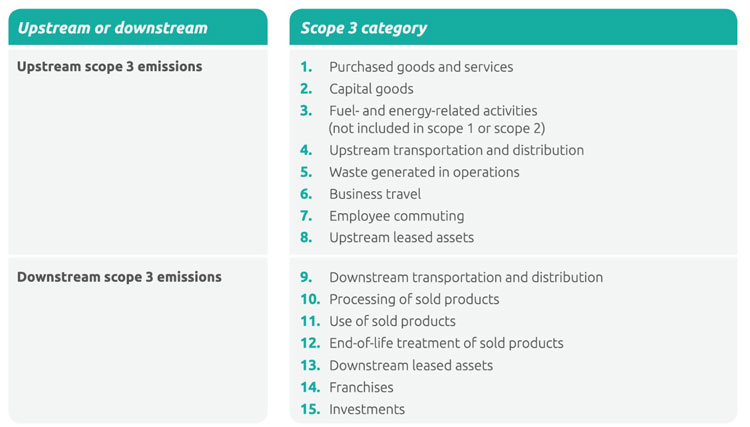
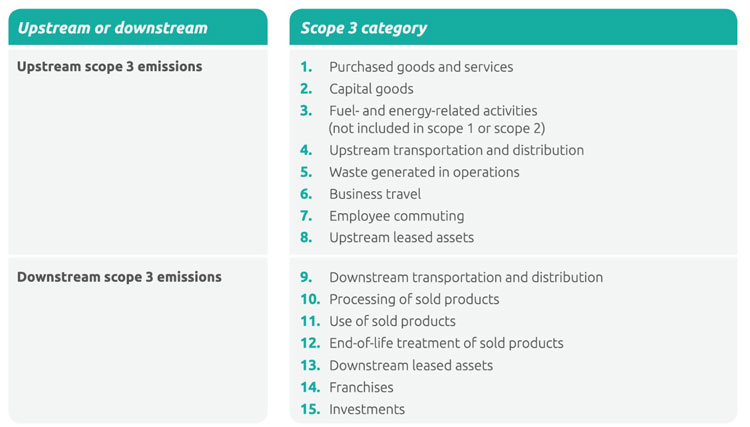
Figure 2: List Scope-3-Categories (https://ghgprotocol.org/sites/default/files/standards/Corporate-Value-Chain-Accounting-Reporing-Standard_041613_2.pdf)
For rail operators, purchased goods, services and capital goods are particularly significant (categories 1 and 2 of Scope 3 in the GHG Protocol). The product groups are characterised by both high procurement volumes and high CO2 intensity, which must be individually determined in each case. When selecting the company’s own product groups for the CO2 calculation, the reporting company should include all activities that:
- Are expected to make a significant contribution to the total Scope 3 emissions
- Offer the greatest opportunities for reduction
- Are most relevant to the company’s business objectives (page 65, GHG Protocol).
Problem definition
The challenges for most large companies are obvious: Scope 3 emissions are the most difficult to capture and account for. Not all processes along the value chain are known or fall directly within the company’s sphere of influence. At ÖBB, most of the GHG emissions under Scope 3 are therefore procured through purchasing. In relation to ÖBB’s role – both as a manufacturer/operator of rail infrastructure and as a mobility provider in rail transport – large quantities of goods and services are procured every year. This also amasses large quantities of Scope 3 emissions.
In the area of mobility in Austria, ÖBB currently emits slightly more than 200,000 tonnes of Scope 1 and Scope 2 GHG emissions annually, but the company is also responsible for between 1.7-2.4 million tonnes of Scope 3 emissions. The majority of these come from procurement, e.g., from construction activities, maintenance and from the production of procured vehicles.
The range of Scope 3 emissions from procurement is currently calculated at ÖBB based on annual financial procurement volume. Although this is currently not forbidden by the GHG Protocol, it is not expedient for managing targeted reduction potentials. Price increases for raw materials and products and price increases for expended energy distort the results. GHG reduction effects of real reduced quantities of goods, materials and services can even be equalised or falsified in the calculation of GHG emissions.
Meaningful GHG management of Scope 3 emissions from procurement can only be achieved through concrete volume data. The challenge, however, lies in the structured collection of the necessary data. This is because data is either not available comprehensively or not of required quality. To be able to collect the correct volume data in purchasing as efficiently and pragmatically as possible, two questions arose:
- How can ÖBB filter out exactly which activities make the greatest contribution to Scope 3 emissions, if up to now the calculation has still been carried out on the basis of CO2 equivalents per procurement value (€)?
- How can a realistic roadmap for volume data collection be developed for the next few years which: a) Ensures rapid collection for the most important Scope 3 drivers in purchasing?; b) Realistically plans according to data maturity within ÖBB and its suppliers?; c) Enables the continuous refinement and improvement of the volume data basis?
The objective of a joint project was to structure this process for the collection of volume data on the largest GHG drivers from ÖBB procurement. It was the essential groundwork to obtain the required data, which in turn will be used to calculate ÖBB’s Scope 3 emissions. The project was led from ÖBB-Holding AG by Herbert Minarik in the Systems Engineering and Corporate Production Department of the Sustainability Team. External consulting was provided by the management consultancy eolos GmbH in collaboration with Matthias Landgraf (evias e.U., private lecturer at Graz University of Technology). Their years of experience in the industry, professional project management and a sound database, especially in the rail sector, were an essential baseline for solving the aforementioned challenges in pre-structuring the largest Scope 3 drivers at ÖBB.
Approach
To identify the relevant GHG drivers in ÖBB’s purchasing, all product groups were evaluated step by step according to various criteria. This then enabled prioritisation of the quantity data collection.
First classification
The product groups were assigned to the corresponding Scope 3 categories according to the GHG Protocol (purchased goods and services and capital goods).
More detailed granularity
For further improved structuring, the product groups were again assigned to specially defined ‘GHG groups’. They consider different criteria such as material, composition, complexity and CO2 intensity.
Furthermore, the product groups were assigned a qualitative ‘GHG relevance’. The scale here was set between ‘1’ and ‘4’, where ‘1’ means a low GHG intensity per unit (e.g. simple services) and ‘4’ a very high intensity (e.g. batteries).
These two in-depth steps of more granular categorisation were the most complex and iterative part of data structuring. They required knowledge of the CO2 intensity, the different materials and compositions in the rail sector. The project management and content expertise of eolos and Matthias Landgraf were essential. Their many years of experience in both the industrial and scientific sense were essential for the assessment of the product groups. Due to the large number of decarbonisation projects and GHG balances already carried out by them in the rail sector, it was possible to make rapid progress in the project here. The well-founded assessments were further discussed and verified through iterations with the respective experts within ÖBB (e.g. in the context of stakeholder workshops and interviews).
Final identification of relevant product groups
The relative procurement volume per product group of the last five years was included in the prioritisation and combined with the GHG relevance. The resulting ‘criticality’ now represents a ranking of the relevant product groups: from high prioritisation for Scope 3 emissions to irrelevant prioritisation.
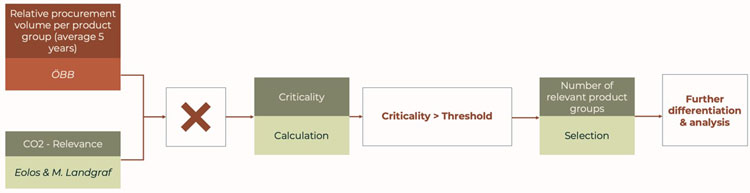
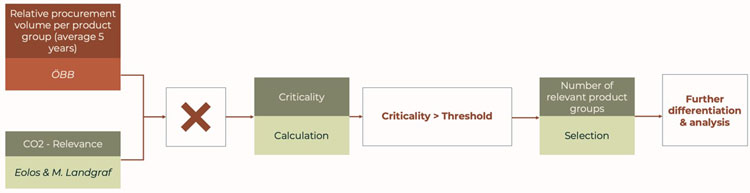
Figure 3: Determination of the decisive product groups of Scope 3 emissions.
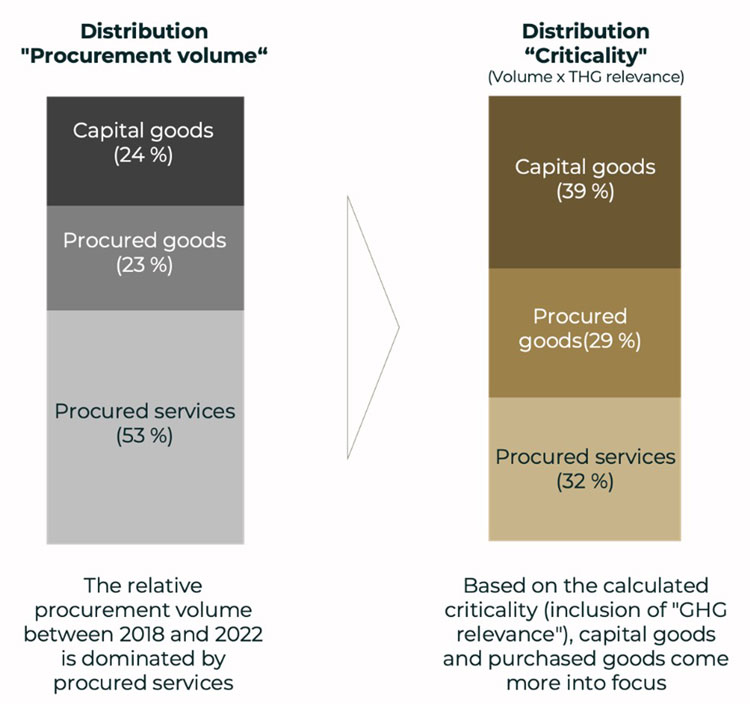
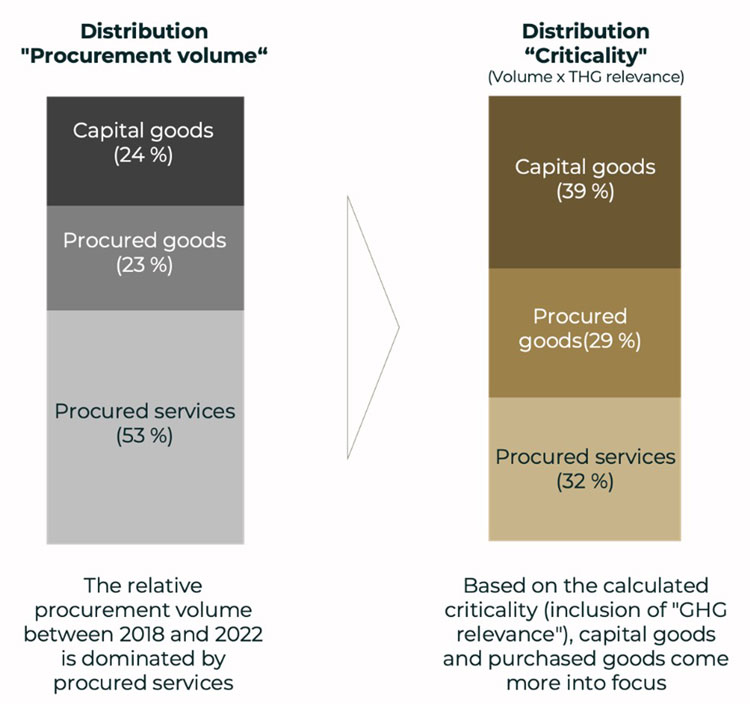
Figure 4: Distribution of product groups according to calculation with “criticality”
Translation of the results into a roadmap for the process of volume data collection
In a final step, a roadmap was developed that shows a realistic way of continuously increasing data collection over time for the different product groups. It is based on the calculated results of steps 1 through 4 and can be flexibly adapted to the framework conditions within ÖBB and the degree of maturity of the data by the suppliers. It is also ideally suited for internal communication and visualisation of the procedure to take for ÖBB employees.
Results
The presented methodology allowed an evaluation and ranking of the individual product groups. This made it possible to determine that 80% of the total GHG relevance can be covered with the detailed calculation of about 90 product groups. The top 10 product groups are already responsible for 44% of the total GHG relevance. This shows that a step-by-step calculation of Scope 3 emissions according to the GHG Protocol can make sense if one starts with the calculation of the most relevant product groups.
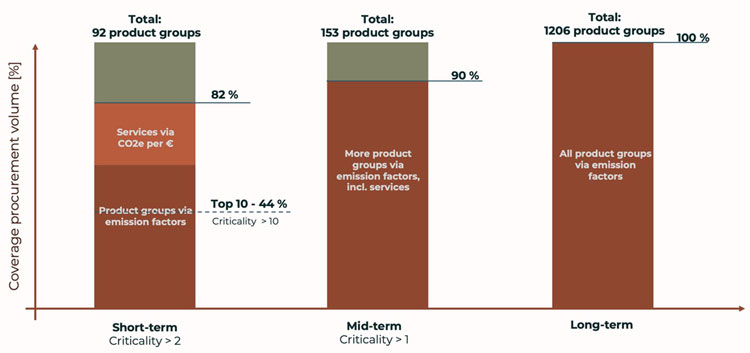
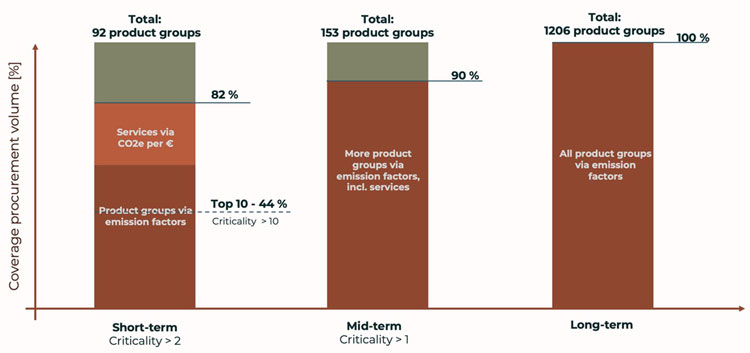
Figure 5: Roadmap extended data collection for the next years.
The creation of the data structure necessary for the Scope 3 calculation requires intensive coordination between all subsidiaries of the Group. It is worthwhile to establish a calculation of Scope 3 emissions that is as automated as possible. Due to the ever-improving ‘emissions transparency’, it will be possible to develop targeted sustainability strategies. The lifecycle inventory necessary for the calculation of emissions implies that the relevant quantity flows are also known. This applies not only to decarbonisation strategies, but also to the implementation of circular economy strategies.
Outlook
The present ranking of the product groups according to their GHG relevance now enables a targeted procedure for the procurement of quantity data. ÖBB has decided to tackle the top 10 product groups in greater detail in the first phase of further analysis. Data procurement is to be carried out in parallel from several sides, including:
Use of data that is centrally available via the IT systems of the purchasing department
After semi-manual improvements to the data from 2022, automated data queries have already been defined for 2023 data. They will be evaluated for the first time at the beginning of 2024.
Further roll-out of the TCO CO2 tool for procurement processes in the Group
In the future, the existing Total Cost of Ownership (TCO) CO2 model within ÖBB will be increasingly used to calculate the emissions of individual product groups in purchasing. The tool was developed by the Strategic Group Purchasing in 2020. It enables the product-specific calculation of the environmental impacts caused by the production, construction and utilisation phases when submitting an offer. These environmental impacts are monetised and integrated into a TCO, which means that they are directly incorporated into the award process.
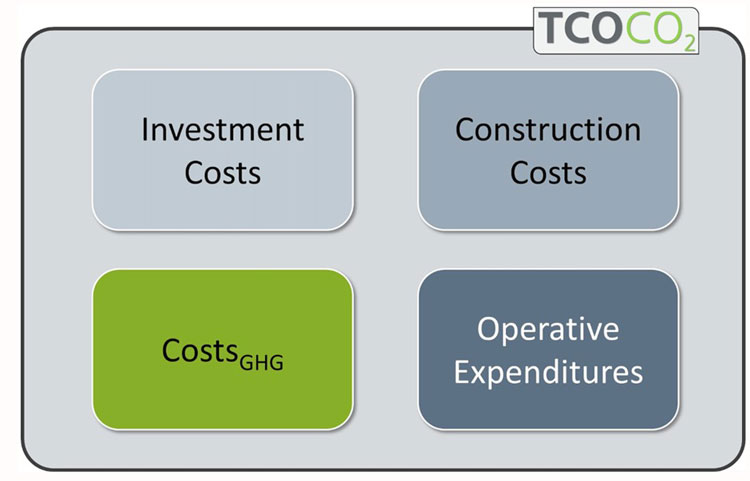
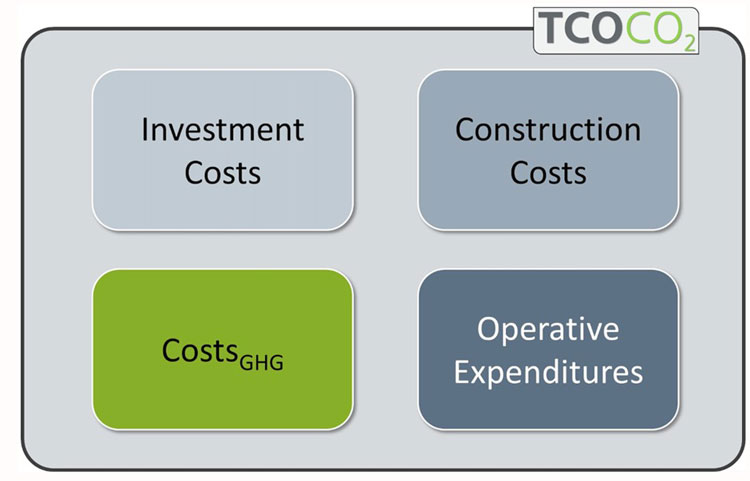
Figure 6: Ecological tendering system TCO CO2.
If the long-term goal of applying this model in all tendering and award processes of the ÖBB Group is achieved, the annual calculation of Scope 3 emissions would also be directly integrated. With the consideration of ecological effects in the tendering process, a simultaneous reduction of the environmental effects at the group level can also be promoted.
Additional support for ÖBB’s subsidiaries
The companies are called upon to actively address the issue of reducing Scope 3 emissions. This means, for example, prioritising the analysis of goods and services with high GHG relevance and, if possible, implementing Scope 3-reducing measures. This ranges from examining potential alternatives to the materials used (raw materials, material qualities, manufacturing processes, etc.) to the type of delivery (e.g.: truck or rail) or logistical alternatives for distribution within ÖBB, to the processes for any assembly and maintenance work. The inclusion of the current internal ÖBB users (= purchasers) of goods/services procured via ÖBB Purchasing is essential for a reduction of Scope 3 emissions.
The process outlined cannot usually be implemented quickly in large corporations, but this way of obtaining data helps to create the basis for controlling Scope 3 emissions. It will also likely be realised in further processes, in which it is impossible to obtain detailed or usable data for relevant product groups. In this case, the GHG emissions will continue to be calculated via the financial procurement volume. However, ÖBB’s medium-term goal is to at least control the reduction of the most significant GHG drivers from procurement via concrete quantity data. Centralised procurement, good cooperation across different divisions of the company and the inclusion of the current users/purchasers are important prerequisites for managing the reduction of Scope 3 emissions in a meaningful way. In addition, suppliers will also be required to provide corresponding data (ideally automated or certified in the future). Moreover, moving forward in the topic of circular economy will clearly benefit from the Scope 3 reduction process.
Although large corporations such as ÖBB are dependent on the market and/or technological developments when it comes to Scope 3 emissions from procurement, they will raise awareness across the market and among their suppliers in their role as one of Austria’s largest corporations bringing society into a sustainable future.
Related topics
Related organisations
Related regions
Related people
Herbert Minarik, Leena Jäger, Matthias Landgraf, Sven Schirmer