Rail track maintenance machinery – Innovations in the UK
Posted: 31 January 2017 | | No comments yet
In this article for Global Railway Review, Brian Counter, Technical Director of the Permanent Way Institution (PWI), reviews current methods and innovations in the UK rail industry’s track maintenance machinery sector.
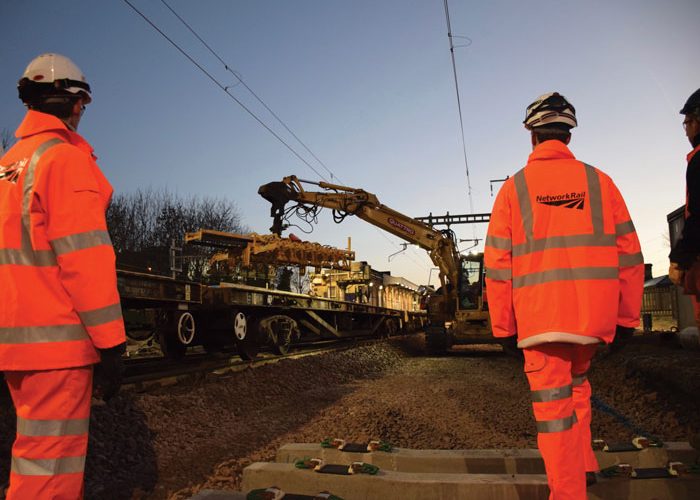
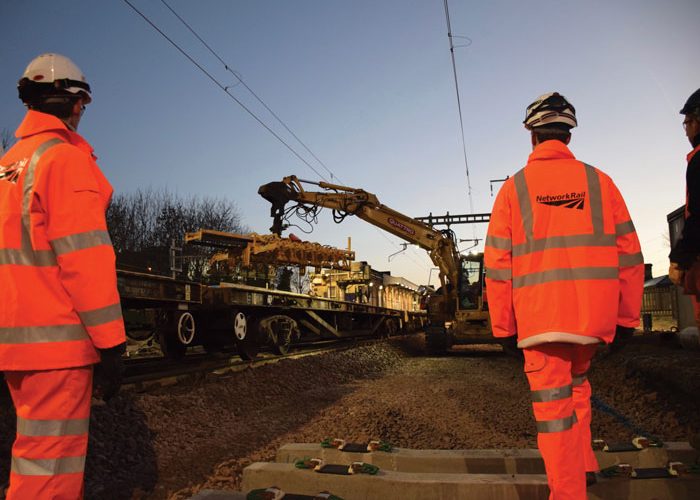
The UK rail infrastructure industry has gone through significant changes in the use of mechanised technology in the last 50 years. Large fleets of tampers and ballast regulators were introduced for maintenance and for renewals the new machinery consisted of ballast cleaners, rail cranes and tracklayers. In the 1980s new processes led to the introduction of stone blowers and dynamic track stabilisers.
Following privatisation in 1995, we have seen major shifts in the use and type of track maintenance and renewal machinery with much investment in high output track and ballast renewal equipment and modular switch wagons. However, following the rail regulator’s conclusions on CP5 in 2014, the formal concept of track refurbishment was established which bridged the gap between track maintenance and renewal. This has led to a number of innovations in this area. Also of particular relevance is the stunning growth in UK rail passenger numbers which have more than doubled in the last 20 years. This has led to reduced access and speed restriction availability, not only on mainlines but on the London Underground too where the ‘Night Tube’ was introduced in late-2016, effectively offering 24 hour running over the weekends.
Mechanised track maintenance
The mechanical maintenance of vertical and horizontal alignment (top and line) in the UK is carried out by a combination of two types of machine. These are tamping machines and pneumatic ballast injection machines (stoneblowers) being specifically designed for either plain line or switches and crossings (S&C). They combine the functions of correcting top, line and cross level on the one machine, and normally all corrections are carried out during the one pass of the machine. Top is measured and the necessary correction applied, and the machine lifts the sleeper to the correct level.
In tamping, vibrating tamping tines are inserted into the ballast cribs adjacent to each sleeper and squeezed towards each other up to the sleeper’s edges. The sleeper is then released if the tamper’s computer signals that the correct lift and cross-level has been attained, otherwise it is re-tamped and the tamper moves on to the next sleeper for treatment. In the case of stoneblowing, chippings are injected at this stage and a similar checking process is applied.
In most cases, as the mechanised maintenance activity occurs on a long-term planning basis which could be up to two years in frequency, a maintenance design is carried out. This relates to the vertical and horizontal profile and can be unique or related to previous fixed datum points.
In design tamping or stoneblowing, the starting information will typically be a profile prepared for a re-levelling scheme. This will contain information about the existing and proposed reduced level at every sleeper throughout the section of track to be treated.
Up to the 1980s, only tampers were used. However, when more sophisticated track recording systems were developed it was identified that vertical track geometry deteriorated rapidly under the passage of traffic following tamping. The resultant vertical profile was virtually identical to that which preceded tamping which became a phenomenon known as ‘ballast memory’. Tamping machines cannot easily change this inherent ballast profile because, with small track lifts, no extra stone is introduced underneath the sleepers.
The stoneblower was developed in the 1980s with pilot machines and within 10 years a full fleet was active in the UK. Stoneblowers (see Figure 1) are designed to obviate the problem of ballast memory by introducing additional ballast in 20mm chipping form beneath the track sleepers, in effect an automated version of what was called manual measured shovel packing. This resulted in track top durability between three and eight times better than tamping.
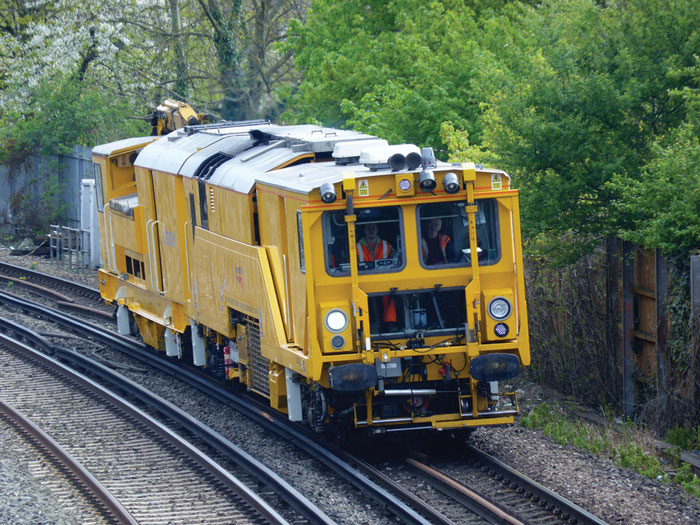
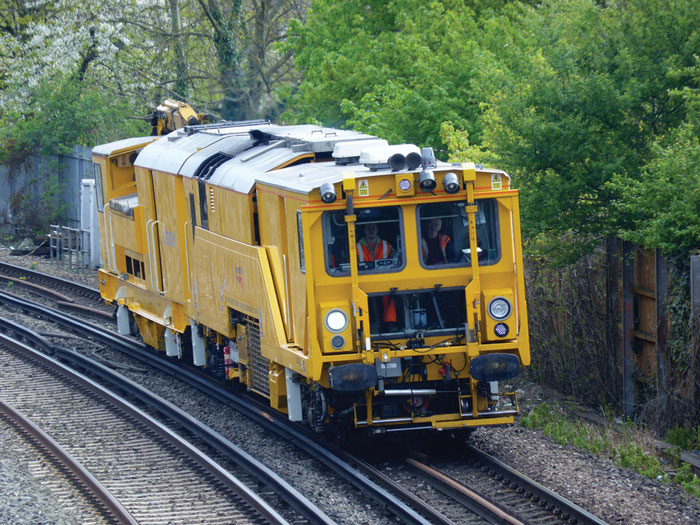
Figure 1: A stoneblower operating on UK tracks
Conventional tampers actually damage ballast by reducing it to fines; over 2kg of dust being produced for each tamp of sleeper bed, unlike stoneblowers that introduce all the requisite ballast and due to the method employed do not reduce ballast to fines. The true measure of the effectiveness of a treatment is not how fast it can be executed, but how long the effects last. This is where the stoneblower process shows its results most clearly.
Treating a poor section of track with a tamper could improve the top’s typical standard deviation from 1·94 to 0·82, but following the resumption of traffic it could be back to 1·95 within just nine weeks. A similar section of track treated by the stoneblower improved from 2·08 to 1·17, and took three years to deteriorate down to 2·10.
There are a number of other benefits which contribute to robust asset management by giving sustainable and efficient use of materials. Track suffering from sub-standard ballast conditions such as ash ballast, wet or clay spots, etc., can be satisfactorily maintained and life extended. The advanced computer systems ensure that only areas of track actually requiring attention will be treated, leading to less intervention which will give longer life to the track asset.
Therefore it was found that far fewer stoneblowers are required to maintain track than tampers, with savings in capital expenditure, machine maintenance, manpower and track possessions or disruption to rail traffic. In the UK, many secondary routes have been successfully maintained at low whole life ballast costs using stoneblowers.
Specialist treatments
There are a number of machines available in the UK for removal of ballast – mainly for heavy maintenance purposes rather than complete track renewal or ballast cleaning. Typical examples of the need for this type of machine could be under S&C or for isolated formation failure where ballast needs to be completely replaced over lengths of track up to 50m.
The ‘Railvac®’ machine (see Figure 2) is a rail-mounted, self-propelled, high capacity vacuum ballast removal facility; in effect a full-scale rail vehicle around the size of a large locomotive. The machine has a 250mm diameter tube with a tungsten tip connected to a hydraulic arm system with a remote control operating unit. The vacuum is a high power facility and can be used with a large variety of cohesive and large particle size non-cohesive materials. There is an integral hopper which collects the material and has side discharge chutes for the disposal of the spoil.
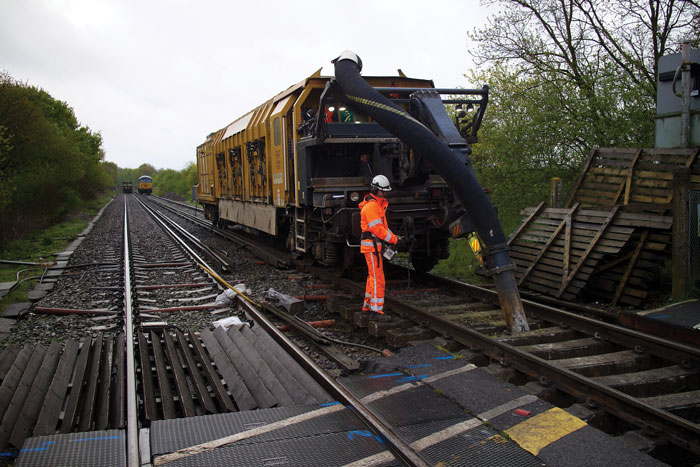
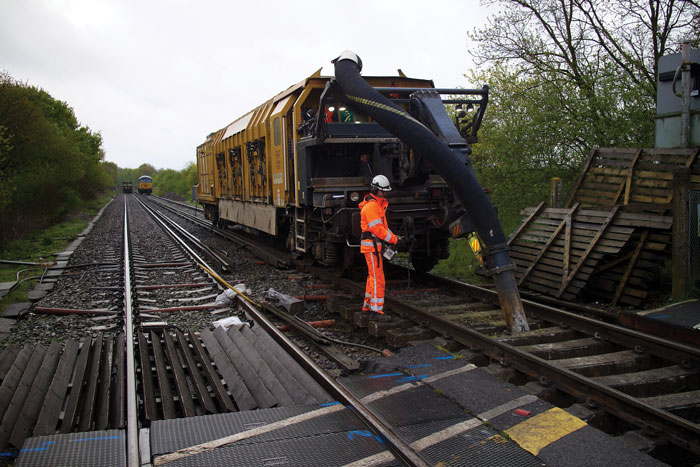
Figure 2: A Railvac® machine working in the UK
Recent innovations in track maintenance
The pressures and challenges within the rail industry are principally related to value and customer service. The use of innovative techniques for life extension of track effectively tick both boxes in that it is sustainable to get best value by refurbishing track assets and this work can cause the least disruption to the rail passenger. Techniques that allow essential repair and maintenance work to be completed in very short possessions are very attractive to train operators.
The Railvac® vacuum re-ballaster has developed in four areas since it was introduced to the UK by me some 10 years ago; Geotextiles using a continuous ballast loader, specialist packing using vibrating poker type and spinning blades on the tube end. An issue for track quality has been the formation treatment and through the use of lasers, specialist geotextile mats and focused consolidation recent results have provided a high quality repair. In some cases, where there may be hard spots and other materials, a spinning blade has been introduced to improve productivity.
Network Rail has invested £50 million in eight Robel-built Mobile Maintenance Trains (see Figure 3) which are mobile covered workshops that can be quickly set-up to carry out track work. They can be used for switch and crossing repairs, welding and replacement of defective rails and insulated block joints. The whole of the track asset can be maintained including the components using the special widening system where necessary. This system is not only very efficient but it also brings significant improvements to quality control and workforce safety.
I am aware of a number of other innovations associated with rail welding such as the use of the mobile flash-butt welder, mechanised puller and heater restressing for the elimination of rail joints. Also, work is in hand to potentially reduce the cooling time for alumino-thermic welding.
Conclusion
Although the UK railways are very similar to Europe and the rest of the world, the unprecedented growth in rail use has prompted the rail administrations and suppliers to promote the use of additional resources to the development of further innovation. The PWI works with partners and is licensed by the Engineering Council for professional registration and represents approximately 3,000 individual members and 30 corporate organisations. The aim is to promote technical excellence in track and rail infrastructure through networking, seminars and publications.
Biography
Dr. Brian Counter is a Chartered Civil and Railway Engineer who obtained a PhD in Life Extension of Railway Track Systems. He previously worked for British Rail, Balfour Beatty, ORR, Carillion and was Head of Built Environment at Derby University. Brian is currently Technical Director of the Permanent Way Institution and Lecturer, Consultant and Researcher in Rail Systems.