Simplifying portable precision wheel truing
Posted: 18 December 2017 | Global Railway Review | No comments yet
Unlike obsolete manual lathes, CNC-controlled portable wheel lathes enable safe, precise and fast wheel truing in workshops and on-site. This article explores how Ontario Northland Transportation Commission and Bay Line Railroad have adopted a new approach to wheel profiling…
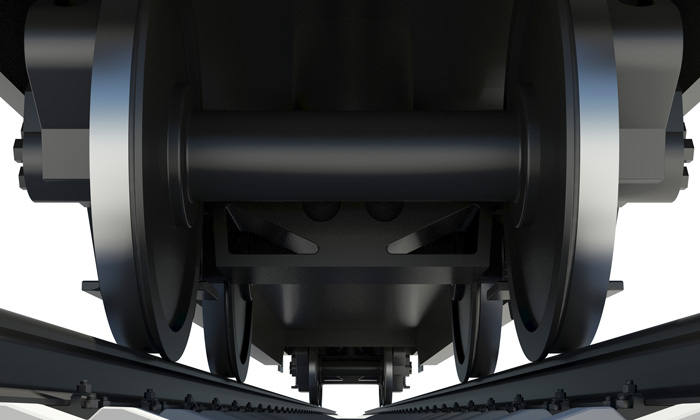
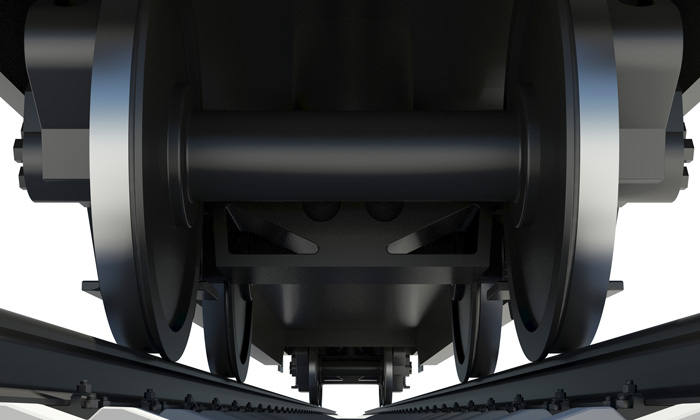
Wheel-related service disruptions can easily cost rail operations $10,000 or more per incident, including downtime. This includes time waiting for repairs, the cost of shipping wheelsets or moving entire locomotives to reconditioning facilities, outsourcing wheel profiling to mobile contractors, lost revenue from cancelled train departures and even Federal Railroad Administration (FRA) fines.
Now, however, the availability of CNC-controlled portable wheel lathes is dramatically expediting wheel profiling and reducing costs by enabling safe, precise, on-site locomotive wheel truing; whether on-site or in a workshop. Unlike outdated portable lathes that require operators to work at the wheel in a labour intensive, manual process, these easy-to-use lathes are controlled using a handheld pendant at a safe distance from the machine.
Just as CNC technology has revolutionised the precision metal parts manufacturing industry, multi-axis, coordinate-based profiling eliminates the potential for human error, so that a virtually perfect wheel and flange can be cut every time. Because such equipment costs a fraction of the price of in-floor wheel systems, it is even affordable for short lines, and can pay for itself in less than one year by reducing repair costs and service downtime.
Wheel safety and compliance
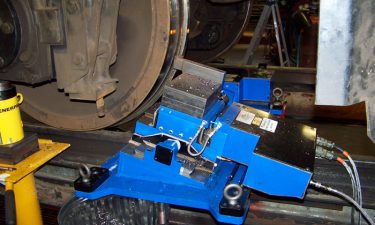
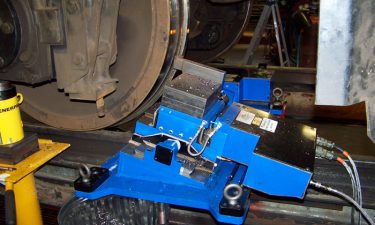
A virtually perfect wheel and flange can be cut every time.
For rail operations, inspecting and maintaining locomotive wheels is a critical function. To ensure proper wheel-rail interface, the FRA requires locomotive wheels to be inspected every 90 days. The wheels must pass inspection for defects such as flat or shelled spots, thermal cracks and thin or high flanges, as well as meet specified wheel measurements that are designed to prevent wheel failures and train derailments. Noncompliance can result, not only in costly downtime and repair to get back in service, but also enforcement actions and penalties.
“Previously, if we had a locomotive wheel defect in our Cochrane terminal, we would ship the locomotive to our larger North Bay facility, which took it out of service for up to five days,” said Chris Wilson, Manager of Training and Continuous Improvement at Ontario Northland Transportation Commission; a public agency that operates 24 locomotives and provides vital transport services to Northeastern Ontario, Canada. “For us, that could mean not being able to run a train, which is a huge loss of revenue.”
According to Chris, Ontario Northland considered purchasing an in-track wheel truing machine. However, the $2 million price tag was prohibitively expensive for the smaller facility. After some additional research, Chris successfully turned to a portable CNC wheel lathe from Delta Manufacturing.
Since such equipment is portable, it can quickly be brought to a disabled locomotive to re-profile wheels onsite. The Delta Manufacturing Wheel Hog, for example, can be utilised at the remote site, with the locomotive raised on mechanically locking jacks, so the wheels can be quickly and precisely re-trued. This approach can dramatically reduce the cost of service downtime and eliminate the expense of moving a locomotive or shipping wheelsets to a reconditioning facility.
Bay Line Railroad, which runs 23 locomotives along 108 miles of track and supports approximately 15 short line railroads in the Southeast region of the US, has also switched to a CNC portable lathe.
“Without our portable CNC lathe, we would have to move a locomotive, or spend approximately $10,000 to buy a wheel and bring in a crane to install it,” said David Nunnery, Mechanical Manager at Bay Line Railroad, which uses the equipment in its workshop and on-site as needed. “Instead, we can bring a portable wheel lathe right to the locomotive and cut the wheel on-site.”
According to David, Bay Line Railroad previously paid a contractor approximately $3,000 per wheelset trued on-site as required. “Now we’re paying just $400 to have our own employees cut a wheelset with the portable CNC lathe,” he said. “On our short line operation, we save approximately $70,000 a year with it. For remote repairs, mid and long line operations could save considerably more.”
Operator safety and precision
While very precise, high-speed CNC-controlled machine tools have been used for decades in manufacturing, until recently the only choice for portable units in rail had been outdated, manually-controlled devices.
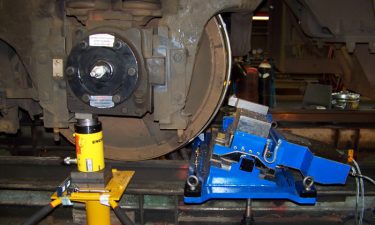
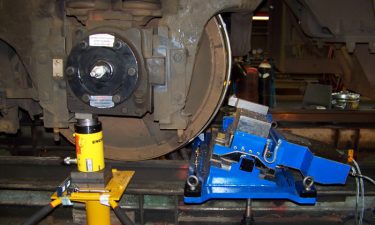
It can quickly be brought to a disabled locomotive to re-profile wheels onsite.
“With the old hand cranked wheel lathes, you worked up close to the wheel,” said Chris. “With our portable CNC machine, however, you stand back at a safe distance, control the operation with a handheld pendant and watch the machine do the work. We’ve had no injuries during the two years we’ve been using it.”
According to Chris, Ontario Northland chose the CNC portable wheel lathe because it is very safe, precise and fully automatic. He points out that it provides the same wheel profile every time and is not so dependent on the skill of the operator. Once the machine is set up, it cuts the wheel profile exactly to the Association of American Railroads (AAR) required standard.
Because the lathe is computer controlled, it is much more accurate than the old hand cranked lathes, noted Chris. “After you set the x and y axis during set up, there’s no more wheel profile measuring required,” he said. “It monitors it automatically and keeps a running total of how much material you’ve removed from the wheel.”
With the CNC unit, truing a single set of wheels takes approximately 4–6 hours to complete, depending on wheel condition, which is a relatively short time to recondition an entire four- or six-axle locomotive.
“Now if we have a wheel defect, we can put the locomotive back in service again in roughly 24 hours,” said Chris. “The lathe paid for itself in the first six months just in the reduced downtime.”
Chris notes that the CNC lathe allows Ontario Northland to eliminate wheel defects that can increase impact with the track and lead to broken joints on electric traction motors. This approach can significantly reduce maintenance costs.
“Since we’ve had the CNC wheel machine, we’ve had an 80 per cent reduction in traction motor failures on the locomotives on that terminal,” said Chris. “We’ve saved at least $300,000 in failed traction motors in about two years.”
When also factoring in the ability to keep the locomotives in service longer with less downtime for repairs, Chris estimates that adds another $100,000 in savings per year on maintenance costs.
For locomotive mechanical officers considering their wheel maintenance equipment choices today, David from Bay Line Railroad offers some advice:
“You will never go back to a hand cranked lathe once you try a portable CNC unit. Whether you set it on a rail, on a flat surface, or over a pit with adapters, it is easy to use. You can teach a new operator to use it in one or two wheel cuts and virtually eliminate issues related to operator error and service downtime.”
Related topics
Digitalisation, Infrastructure Developments, Rolling Stock Maintenance, Safety