Investing in modern maintenance technology to deliver an improved railway
Posted: 6 December 2019 | Piotr Majerczak - PKP Polskie Linie Kolejowe S.A. | No comments yet
The track is the most integral part of railway infrastructure and its maintenance is thus vital. Piotr Majerczak, Member of the Management Board and Infrastructure Maintenance Director of PKP Polskie Linie Kolejowe S.A., explains how recent investment in modern technology has transformed the way track maintenance activities are carried out across Poland’s rail network.
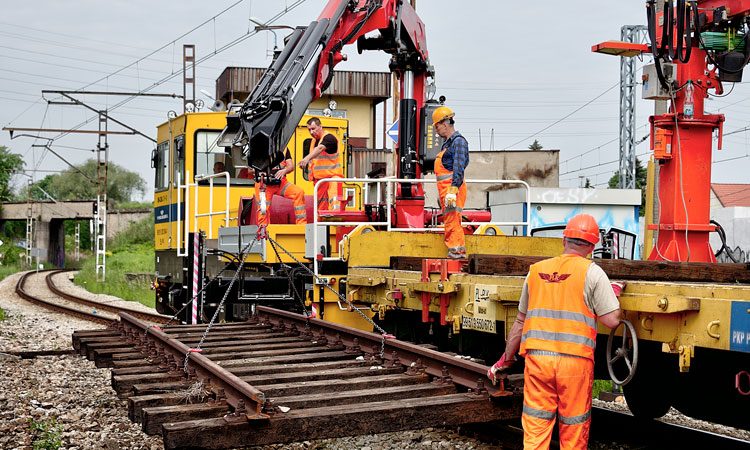
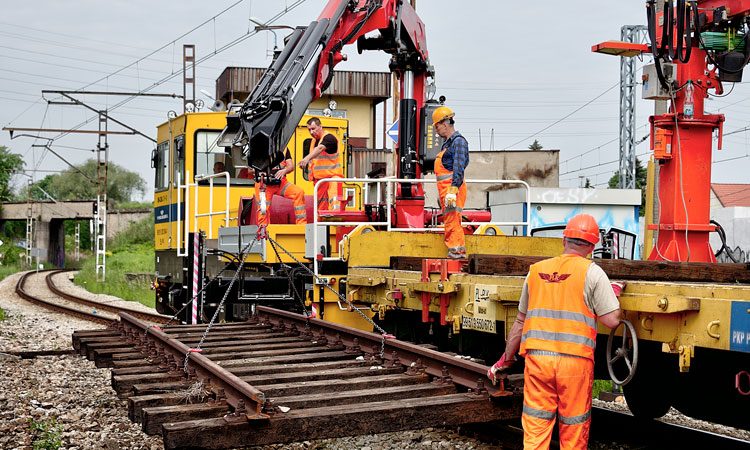
Professional diagnostics and effective track maintenance in Poland
Every day, approximately 7,500 passenger and freight trains travel on railway tracks managed by PKP Polskie Linie Kolejowe S.A (PKP PLK). We cooperate with carriers to ensure that passengers reach their destination safely and comfortably and that the transportation of goods is carried out efficiently.
PKP PLK is responsible for the maintenance of infrastructure, the preparation of timetables and the provision of transport services at the highest level. We must meet the challenge of providing an attractive railway offer and line capacity at the time of investment.
Currently, the largest investment programme in the history of Polish railways is being implemented – it is known as our ‘National Railway Programme’. By 2023, PKP PLK will have spent PLN 70 billion on modernisation activities across approximately 9,000km of tracks, passenger infrastructure and signalling systems. This will result in a significant improvement of railway traffic in raising the standards of travel on regional routes and improvement of conditions in the transport of goods. Passengers are benefiting from some already completed modernisation activities.
By designating units responsible for activities, be that transport system, maintenance or investment supervision, all tasks have been delegated to employees who are experts in their respective fields. The Railway Traffic Management Centre is responsible for the correct domestic and cross-border railway traffic. It also supervises work in emergency situations and manages technical security services.
Maintenance: From monitoring to routine repair
Within PKP PLK there is a territorial division of the railway network which splits the network into 23 regional units (Railway Lines District Units), which are responsible for the current operation and maintenance of approximately 8,500km of railway lines. It also includes approximately 40,000 turnouts, 14,000 level crossings, over 25,000 engineering facilities and roughly 14,500 structures. The infrastructure manager combines traditional methods of monitoring the condition of railway lines with modern solutions and technologies.
Appropriate maintenance of the railway infrastructure, investments in modern equipment and a properly prepared work schedule guarantee efficient train journeys. Proper track monitoring makes it possible to obtain comprehensive information about the condition of individual elements. Consequently, it is possible to prepare an action plan that prevents changes in the train timetable. The maintenance process consists of a series of interconnected practices: Diagnostics, maintenance, emergency and ongoing repairs.
Railway Lines District Units shall be responsible for the appropriate condition of the railway infrastructure entrusted to them in the specified area. They maintain railway lines and facilities according to the procedures adopted by PKP PLK. Their responsibilities also include full diagnostics of facilities carried out in cooperation with the Diagnostics Centre.
Technical documentation, including construction and maintenance documentation, is kept for each facility/line. The units determine maintenance needs and plan necessary works. They also supervise routine repair works, starting from the announcement of a tender procedure, through to the performance of works by external contractors, to the acceptance of works. Apart from the annual repair plan, long-term strategic investment activities and estimated costs of necessary works, which will ensure the expected results of maintenance, restoration or improvement of the parameters of the facilities/lines, are determined.
Support for track works carried out on the PKP PLK network is provided by two specialist units: Zakład Maszyn Torowych (Track Machinery Plant) and Przedsiębiorstwo Napraw Infrastruktury (Infrastructure Repair Company).
PKP PLK also exercise owner supervision over four subsidiaries which have their own human resources and equipment which performs track. Companies invest in more and more modern solutions in order to implement investment and maintenance projects more effectively. They are responsible, among other things, for routine repair works – replacement of turnouts and tracks on specific sections as well as current repairs. Most maintenance tasks are performed by the PKP PLK group using its own resources.
Infrastructure under the watchful eye of diagnostic technicians and machines
Thanks to the performance of periodic tests and monitoring of the technical condition of the tracks, it is possible to react to the wear and tear of infrastructure in advance. The employees of Railway Lines District Units check the condition of tracks and turnouts according to the cycle defined for specific lines. They supervise the condition of bridges, viaducts, culverts and railway traffic control equipment on a regular basis. They also monitor platforms along with infrastructure to ensure travellers have comfortable use of the railway system and full information about the train timetable.
Apart from the above-mentioned units, specialist and highly efficient measurements and diagnostic tests of railway lines all over Poland are carried out by the Diagnostics Centre. Such measurements, including track geometry measurements, flaw detection measurements of rails, and laser gauge measurements, are performed using measuring vehicles. Track measurements with the use of vehicles are carried out three times a year on lines with the maximum speed limit of V≥160km/h, twice a year on lines with the maximum speed limit of 100≤V<160km/h, and once a year on lines with the maximum speed limit of V<100km/h. The frequency of flaw detection tests of rails is determined depending on the maximum speed or load from one to four times a year. Such tests detect defects in rails and rail joints. In 2019, it is planned to measure approximately 49,000km of tracks with the use of vehicles (considering the total number of tests).
A specialist vehicle – a mobile diagnostic laboratory for tracks and contact lines – has been used as one of the diagnostic machines for several months. It enables a comprehensive assessment of the railway line by measures the geometry of tracks and rails and checks the condition of sleepers and rails, the profiling of the ballast bed and other parameters using laser equipment. The systems also check the operation of equipment responsible for the safety of trains. It is possible to perform the diagnostic testing of the contact line. Special sensors installed in the measuring vehicle show changes in acceleration on different parts of the vehicle. Based on the data obtained, defects are detected which may affect the quality of journey and the comfort of passengers. Cameras installed in the vehicle register the railway route and enables a complementary visual assessment of the area in which the defect has occurred. The use of non-contact laser systems makes it possible to take measurements without affecting the railway signalling systems. During measurements, the vehicle does not interfere with the operation of the equipment and thus does not affect the traffic on the railway network. Thanks to the systems used in the vehicle, PKP PLK can check 40,000km of tracks in a year. The equipment can measure track parameters up to 200km/h.
The diagnostic technicians of PKP PLK also have a unique ‘Scorpion’ tool at their disposal. It accurately measures the elements of railway turnouts using a 3D model.
Sensors detect defects in rail wheels of carriages and locomotives
More than 213 dSAT defect detectors installed on tracks monitor the condition of carriages and locomotives on a 24/7 basis. Special infrared and fibre optic sensors take the temperature of bearings and brake components remotely and in a non-contact manner. Such control increases the safety of passengers. Information about possible defects is automatically provided to the train dispatcher. The rolling stock is immediately switched off so that it does not destroy the tracks. Such measures make it possible to eliminate delays and inconvenience to passengers.
At the time of writing this article, dSAT defect detectors have so far in 2019 carried out over 1,800,000 inspections of passenger and freight trains during operation. They are installed on tracks on main international transport corridors including E 65 Gdynia–Warszawa–Kraków/Katowice, E-20 Kunowice–Warszawa–Terespol, and E-30 Węgliniec–Wrocław–Kraków–Medyka. The density and location of sensors is adjusted to the intensity of railway traffic.
Overhead contact lines under control
PKP PLK has concluded contracts for services in the scope of maintenance of overhead contact line equipment for a period of several years. This ensures the comprehensive maintenance of equipment on a continuous basis. The frequency and conditions of visual inspections of overhead contact lines, periodic inspections and test travels that are carried out to check parameters are determined in advance. The contract provides current repairs and the replacement of damaged components. 24-hour emergency service and maintenance are essential for quick remedy of failures and restoration of rail line performance for the movement of trains. All overhead contact line voltage cut-offs and conditions for the safe work in the vicinity of overhead contact lines are also maintained. Maintenance and intervention works are carried out by network trains located in 66 bases in Poland. By 2023, PKP Energetyka S.A. will be responsible for the service under a binding agreement.
PKP PLK will also introduce a modern system for detecting pantograph failures. A set of sensors located next to the track will diagnose the status of the pantograph while the train is running. If a failure is detected, the locomotive will be replaced. The system, which will contribute to reducing the number of overhead contact line failures, will be implemented in 2020.
Maintenance planned for the years to come
The long-term planning of investments in maintenance and repair of railway lines is ensured by the maintenance programme adopted last year. Guaranteeing funds for these activities enables planning and effective execution of works over a period of several years. The main benefits include the maintenance of railway infrastructure parameters in such a way so that the needs of the passengers, transport organisers and carriers, as well as shippers and receivers of goods transported by rail, could be met. It will also improve the safety of rail transportation, make travel more comfortable, eliminate barriers that hinder freight transport movements and will maintain travel times obtained as a result of investment works. It also means better preparation of the domestic market of contractors for the execution of contracts. The project is expected to run until 2023.
Investment in specialised equipment
PKP PLK invest in vehicles and equipment that ensures the efficient execution of required track work. This increases the efficiency of the works and shortens their time. The purchase of specialised equipment is also an investment in safety. The project for PLN 250 million is included in the National Railway Programme. The equipment will be used mainly for intervention works. In Poland, 27 out of 42 motor trolleys have already been delivered to PKP PLK’s units. The equipment supports the emergency teams, and thanks to additional elements, it will also be used in winter months to clear the lines of snow.
PKP PLK is also expecting the delivery of a road-rail vehicle for the inspection of engineering facilities. Thanks to the use of a boom lift, it will be possible to inspect the places difficult to reach on approximately 6,400 specific engineering objects, including bridges and viaducts. As part of the project, three tamping machines have been ordered. PKP PLK’s machinery will also be completed by a ballast tamper.
Biography
Issue
Related topics
Infrastructure Developments, Technology & Software, Track Maintenance Machinery, Track/Infrastructure Maintenance & Engineering