Developing bogies and wheelsets in passenger coaches of Indian Railways
Posted: 11 September 2020 | Samir Lohani | No comments yet
Samir Lohani, Executive Director (Standards)/Carriage at the Indian Railways’ Research Designs and Standards Organisation (RDSO), explains how Indian Railways is working on research projects with the Indian Institutes of Technology at Kanpur and Kharagpur to develop and improve LHB coach bogies.
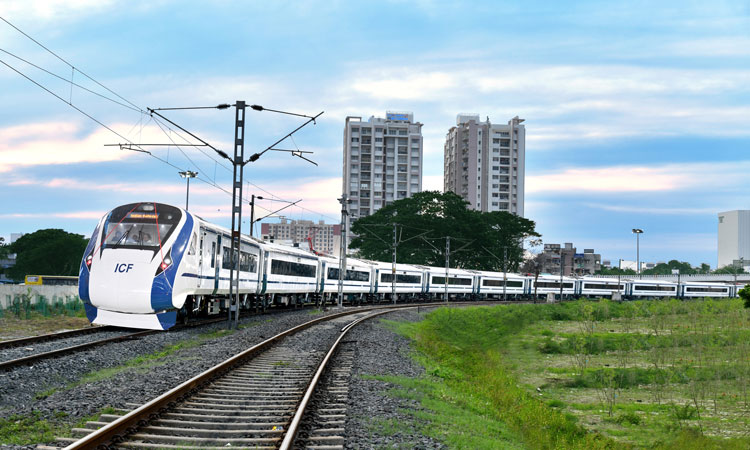
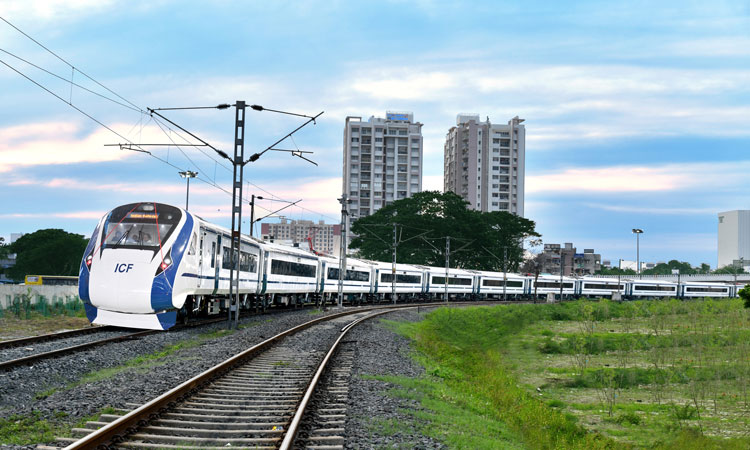
Indian Railways has one of the world’s largest rail networks, with the passenger transportation segment alone catering to 23 million travellers per day from over 7,000 stations spread over a network of 67,415km. For mainline long-distance trains, the bulk of passenger stock consists of locomotive-hauled coaches, with distributed-power trainsets that were introduced in early 2019. The short-distance segment sees extensive use of Electrical Multiple Units (EMUs) [suburban/metro networks], Diesel Electrical Multiple Units (DEMUs) and Mainline Electrical Multiple Units (MEMUs).
India’s rail network is predominantly broad gauge (1,676mm), with passenger trains providing safe and affordable travel at speeds of up to 160km/h. Presently, freight and passenger services share the same track network. With the commissioning of dedicated freight corridors, high-demand trunk routes are progressively being freed for running high-speed passenger trains. Infrastructure and rolling stock upgrades have received much attention in recent years. Green‑field projects – such as the semi high-speed project (200km/h) between Nagpur and Secunderabad, and the high-speed bullet train project (320km/h) between Ahmedabad and India’s economic hub, Mumbai – are being fast-tracked.
Passenger coaches in Indian Railways have adopted lightweight bogies with axle loads of up to 17 metric tonnes. Suburban trains are an exception, as they need to cater to super dense crush loads during peak hours – such trains use bogies of higher axle load capacities of 20.3 metric tonnes and operate at relatively slower speeds of 110km/h. These bogies have traditionally used axlebox guidance systems through dashpot arrangement, helical coil/conical springs in primary suspension and high capacity air springs in secondary suspension. Of late, improved bogie variants having bolster-less connection and fully suspended three‑phase IGBT-controlled traction motors with low un-sprung mass have also been inducted.
Indian Railways has adopted, developed and standardised Linke Hofmann Busch (LHB) coaches (23.5m length) with stainless steel shell and fabricated Eurofima Y-frame bogies for locomotive‑hauled long-distance mainline trains. LHB coach bogies with articulated axle box guidance through control arms and coil springs have proved themselves in Indian conditions for over two decades now. Lightweight, low-noise forged wheel discs with ‘S’ shaped profiles are used in these bogies. The speed potential of these coaches is 160km/h, which can be upgraded to 200km/h with minor changes. The development of LHB coach bogies has been a continuous process.
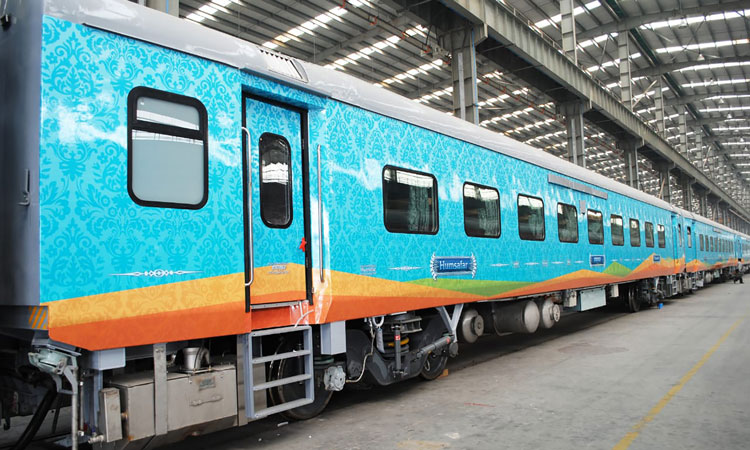
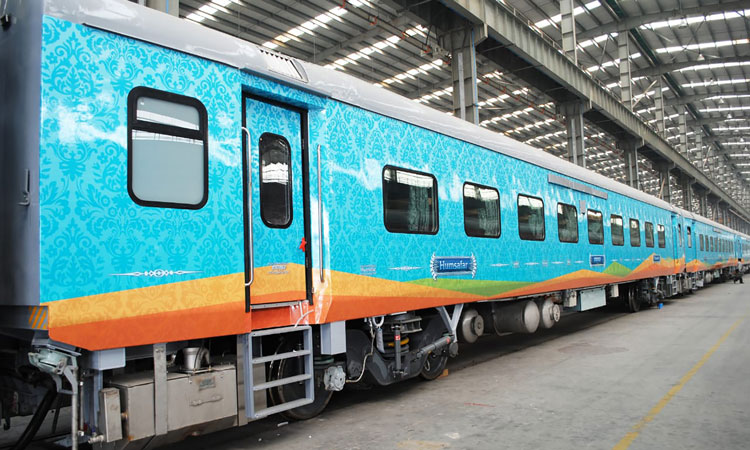
Development of LHB coach bogies has been a continuous process
Pneumatic suspension is increasingly replacing coil springs at a secondary stage for constant floor height, improved ride comfort and high payload to tare ratio. The initial LHB design coach had a maximum gross load of 56.65 tonnes and payload to tare ratio of 0.23. The bogie suspension has been progressively redesigned for a maximum gross load of 65 tonnes and payload to tare ratio of 0.69. Indian Railways is currently working on research projects with the Indian Institutes of Technology at Kanpur and Kharagpur for improvements in suspension elements in these bogies. Collaboration with reputed designers for upgrading LHB wheel designs for better service life and reduced susceptibility to shelling/spalling incidences has also been undertaken. The use of wheel discs indigenously manufactured through pressure controlled pouring process is also being explored.
Operating conditions for Indian Railways require bogie subassemblies to withstand hot and humid environments, dust and vibrations. Corrosion in structural members of the LHB bogie frame was noticed quite early, necessitating the upgradation of the material of the bogie structural members to EN 10025 Part 5 in place of EN 10025 Part 1. Improvements in surface protection for the bogie frame and its subassemblies were also carried out.
An essential bogie requirement is high reliability and availability. Indian Railways trains operate with up to 24 LHB coaches and, as such, reliability enhancements of braking components proved crucial to minimise spalling/shelling on wheel treads. Another important goal is standardisation, as customer requirements have resulted in continuous increases in mainline passenger coach variants (sleepers, chair cars, dining and hot buffet cars, power cars, parcel vans, tourist cars, unreserved cars, etc.). Modularisation and standardisation of bogie variants has assumed importance to reduce inventory and maintenance costs. Increases in passenger train speeds, low track‑wheel noise generation and its effective isolation for improved ride comfort are all areas of active research.
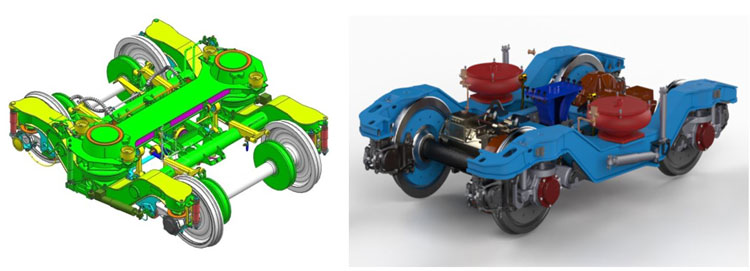
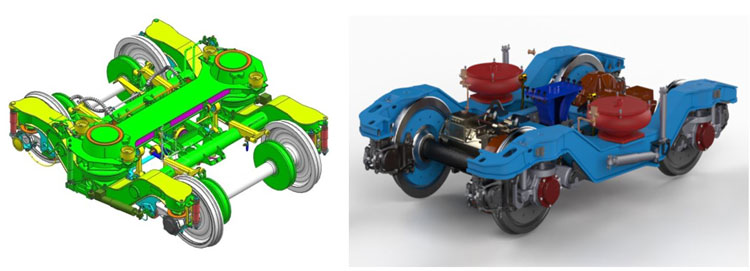
LHB and Trainset bogies
India’s first indigenous trainset, the Vande Bharat Express, which was designed for a 160km/h operating speed, has now completed over one year of trouble-free commercial service. Its bogie is an improved variant of the LHB bogie with bolster-less connection, wheel mounted brake discs on straight web profile wheels and fully suspended traction motors. The propulsion system is equipped with advanced TCMS control and is capable of a 30 per cent regeneration. EMU and MEMU trains with this variant of bogie have also been developed. Indian Railways is aiming for the rapid proliferation of trainsets, with best-in-class propulsion and bogie technologies from industry leaders under the government’s ‘Make in India’ policy.
Another area of development has been in the field of on‑board condition monitoring in the bogies to facilitate the migration from a preventive maintenance regime to a predictive maintenance regime. Traditional industry standard, energy harvester powered NB-IoT, as well as Fibre Bragg Grating sensors (Indian Institute of Science, Bangalore), are being incorporated closely with the bogie subassemblies for accurate condition monitoring of inaccessible bogie components and infrastructure.
The Research Designs and Standards Organisation (RDSO) of Indian Railways is in the process of establishing a Centre of Excellence for Bogie Design with roller rigs and software validation capabilities. With the soon‑to‑be‑completed dedicated test track, Indian Railways plans to uniformly adopt EN 14363 for acceptance testing and validation of all new designs of railway vehicles in the future.
Issue
Related topics
Bogies & Wheelsets, Rolling Stock Components (Interior/Exterior), Rolling Stock Orders/Developments