Expert Panel: Bogies & Wheelsets
Posted: 12 August 2021 | Francesco Lombardo, Markus Hinterwallner, Radim Zima | No comments yet
As part of our Bogies & Wheelsets In-Depth Focus, Global Railway Review asked a panel of experts: What do you expect to change from a technology perspective over the next five years to ensure the lifecycle of bogies and wheelsets can be extended?
Markus Hinterwallner, Head of Technics, Maintenance & Fleet Management, WESTbahn Management GmbH
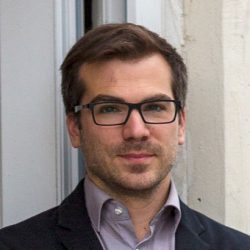
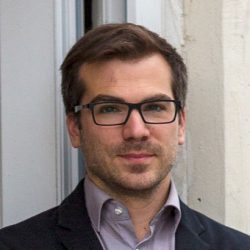
Markus Hinterwallner
“I think there will not be just ‘one big’ change, but a series of changes aiming at different aspects of development regarding the technology perspective so that the lifecycles of bogies and wheelsets can be prolonged.
“One point is to further research for an ideal material grade which extends the machining intervals without destroying the rails. Several manufacturers already produce induction hardened components to reduce lifecycle costs. Another aspect is to reduce non-suspended weight inside the bogie itself to provide a longer wheel lifetime. A third topic: WESTbahn uses the infrastructure checkpoint system ‘Fingerprint’ for measuring the wheel roundness of all wheels of a trainset. If there are deviations from the target and the operator mails a failure report, the trainset is placed onto a lathe and the flat spot or the pitting gets machined without further damage to the infrastructure. This can extend the lifecycle by up to 50 per cent. If there was more checkpoints throughout the whole infrastructure system, more vehicles could be checked to also reduce their lifecycle costs.
“Another important issue is the maintainability of the bogies and wheelsets. Any work procedure concerning the components must be possible to perform within one shift. In a worst-case scenario, the whole bogie must be replaced within that period. In addition, components such as earthing contacts or speed sensors, which can be damaged by gravel, must be quickly fixable if the train stops.
“These and many other small aspects would help to extend the lifecycle of bogies and wheelsets.”
Francesco Lombardo, Strategic Commercial Projects Manager – Railway Division, Lucchini RS
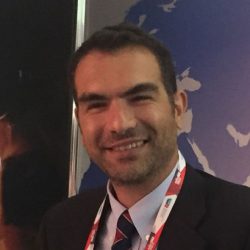
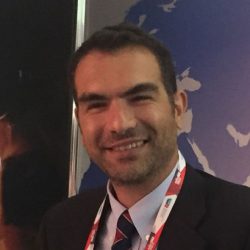
Francesco Lombardo
“Innovative technologies including the Internet of Things (IoT), digital twins, artificial intelligence (AI) and machine learning will contribute to the development of condition-based maintenance (CBM), which represents a quantum leap in maintenance strategies for rail sector operation managers. As of today, inspection and testing of rolling stock has been among the most complex and safety sensitive issues that rail operators and OEMs have had to deal with.
For instance, the inspection intervals on wheelsets are not directly related to real service conditions nor are they based on a crack propagation approach. This is a major expense for service operators and managers in charge of maintenance.
“Lucchini RS has developed the SMARTSET® intelligent sensor that is embedded on railway axles and continuously records wheelset loads in operation. Combined with the AI of the STARCRACK algorithm, it is able to estimate the optimal service NDT inspection intervals with remarkable accuracy. After numerous tests and collaborations on pilot projects over the past three years, it has been demonstrated that intervals between two NDT inspections of wheelsets could be up to 250 per cent longer than the current one, once real loads from service are measured and considered.
“SMARTSET® is proof of how new technology can significantly cut time and maintenance costs while sustaining or improving the safety level of inspections. At the same time, this system can provide precise feedback about loads on wheelsets from operating conditions, which can enable CBM strategies and optimise the lifecycle of all bogie components.”
Radim Zima, Engineering Director, BONATRANS
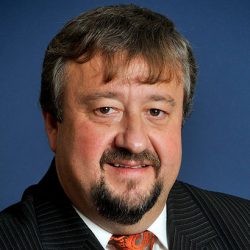
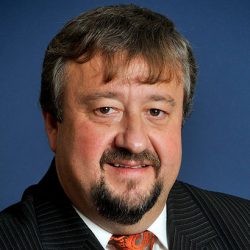
Radim Zima
“The prolongation of the lifecycle of bogies and wheelsets is complex, requiring innovation in design, as well as in materials used. In the coming years, it will still be a sophisticated work of engineers designing not only bogies and their wheelsets, but complete vehicles, with the need to integrate new equipment (including relevant software), with which we will be able to diagnose and evaluate the current condition of these key vehicle parts at any time. Partial differences in new designs and materials will be related to the transport modes and therefore differ for freight vehicles and for passenger rolling stock wheelsets. Freight transport will be focused on maximum use of the load capacity of vehicles. On European tracks, it will be 25 tonne axle loads. In all segments, improved steel grades will be adapted for wheelsets, which will ensure higher mileage with less maintenance. In freight transport, complex wheelset products will include a wheelset with guaranteed minimum service life of all its parts. The experience with replacement of metallic materials in the construction of vehicles will be further extended to selected parts of bogies for passenger and urban rolling stock, and to wheelsets and their accessories, using high-strength composites. The weight reduction related to the use of these materials will be used partly for higher transport volumes, partly for lower energy consumption of rail transport.”
Issue
Related topics
Artificial Intelligence (AI), Big Data, Bogies & Wheelsets, Cargo, Freight & Heavy-Haul, Digitalisation, Rolling Stock Components (Interior/Exterior), Rolling Stock Maintenance, Rolling Stock Orders/Developments