Modular coupler systems as the perfect response to a fast-changing world
Posted: 17 June 2021 | Dellner | No comments yet
Couplers are one of the products in Dellner’s portfolio of Train Connection Systems. This article explores how the organisation’s modular coupler systems can be configured according to a customer’s requirements and the benefits this brings.
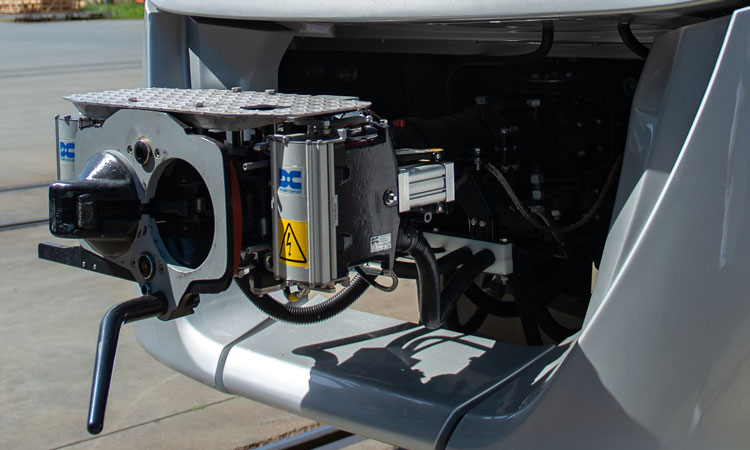
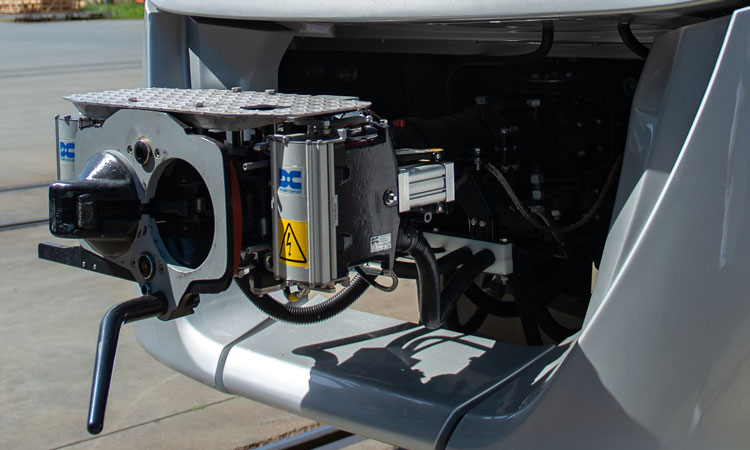
The Swedish company Dellner is one of the world’s leading suppliers of passenger Train Connection Systems with 80 years of experience in the rail industry. With over 1,200 employees in 22 branches around the world, Dellner continues to expand its product and services portfolio of railway couplings, gangways, front cover systems, adapters and crash energy management systems.
Couplers are one of the products in Dellner’s portfolio of Train Connection Systems. They are categorised as automatic couplers, semi-automatic couplers or semi-permanent couplers. The automatic coupler allows for remote connection and disconnection of vehicles directly from the driver’s cab. The semi-automatic coupler allows remote connection but manual assistance is required when disconnecting and the semi-permanent coupler requires complete manual operation for connecting and disconnecting vehicles.
Over the past few decades, people’s lives have changed remarkably. Consumer’s increased expectations of travel experience have provided opportunities for business development. Along with large investments in the railway industry – both in the production of new trains and the modernisation of rolling stock – companies have had to enter a new reality and adapt business to a world where everything should be done faster and better. Now, as never before, shortened project schedules and the demand for high quality products, have become one of the main priorities of customers.
Dellner is very flexible and puts the customer requirements at the centre of all activities. Dellner has developed a modular system of couplers, consisting of 14 modules (subassemblies). These modules can be configured according to the customer’s requirements significantly reducing delivery time and ensuring quick availability of spare parts. At the same time, the modularity contributes to an increase in the level of compatibility of technical solutions used in new projects while maintaining the excellent quality of products sold and services provided.
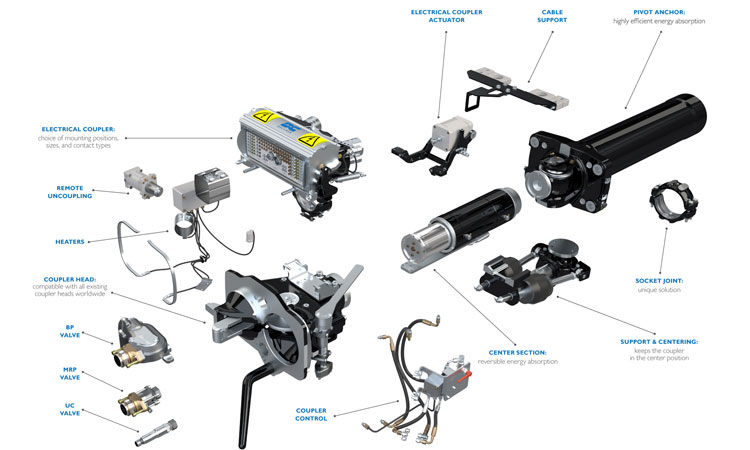
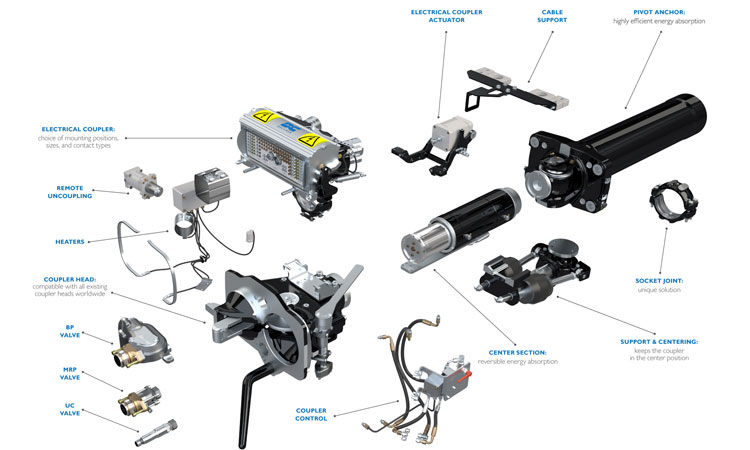
Front coupler modules (automatic coupler)
Each coupler is divided into three basic modules that form the core of the structure: the coupler head, a centre section and the anchor. The element that connects these modules is the socket joint. The remaining nine modules provide functionality depending on the customer’s technical requirements including centring devices and coupler supports, electric couplers, electric coupler drive types, coupler control, remote uncoupling drive types, main air line valves, brake line valves, remote uncoupling line valves, heaters, cable supports and supports for the gangway.
The coupler head is the first of the basic modules. The head type is selected based on whether compatibility with existing fleets is required, on the expected levels of compressive and tensile forces and the operational requirements of the authority, specifically if manual operation is accepted.
The centre section, in addition to the obvious function of joining the coupler head to the anchor, plays a key role in the energy absorption capability of the complete coupler. Energy absorption can be reversible or non-reversible.
Reversible energy absorption is provided by a buffer that compresses over a distance to absorb energy but returns to its original length and position after the collision. Non-reversible energy absorption is a ‘one shot’ mechanism that compresses over a distance to absorb collision energy but requires replacement after the collision.
The need for regenerative, non-regenerative or both types of absorption depends on the performance needs of the vehicle. For example, coupling, braking and normal service operation, as well as absorption during collision to support the vehicle Crash Energy Management (CEM). This type of performance could be covered using a buffer (regenerative) and deformation tube (non-regenerative) arrangement designed to work in series.
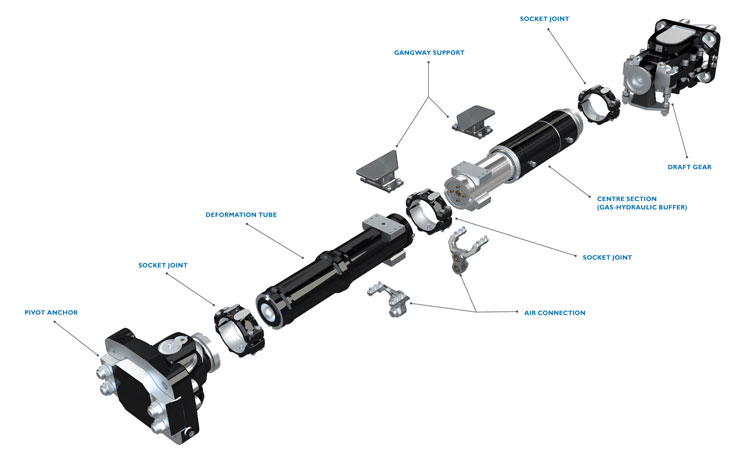
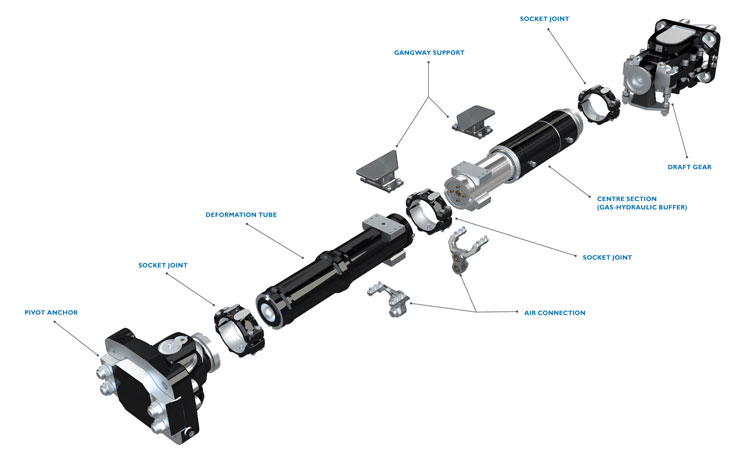
Inter-car coupler modules (semi-permanent coupler).
The anchor connects the coupler to the vehicle structure. The anchors are available in many configurations to meet is the customer’s specific requirements regarding the method of attachment, range of coupling movements and energy absorption.
The base modules are connected together using a socket joint. The selection of the appropriate socket joint must consider the levels of buff and draft forces expected as well as bending strength requirements.
The remaining modules supplement the coupler core and can be arranged in countless configurations to accommodate the specific needs of the end user. For example, to address connectivity requirements between vehicles, the electric couplers can be chosen based on the number and types of contacts needed to meet signal requirements and the type of drive that best fits the vehicle design, electrical or pneumatic.
Dellner’s modular construction offers rolling stock manufacturers cost savings potential in the form of lower prices for final products and spare parts as well as time savings potential in the form of established supply chains for fast order fulfilment. At the same time, customers can be sure that they receive the highest quality products and services.
A detailed description of the individual modules will be presented in future articles with Global Railway Review; the next article will focus on the first of the main modules – coupler heads.