Leading the wheelset industry: from tradition to innovation
Posted: 22 May 2023 | Riccardo Pasinetti, Steven Cervello | No comments yet
Riccardo Pasinetti and Steven Cervello explain how members of the European Railway Wheels Association (ERWA) have advanced railway wheels, wheelsets, and axles and how continued improvement is important for further developments.
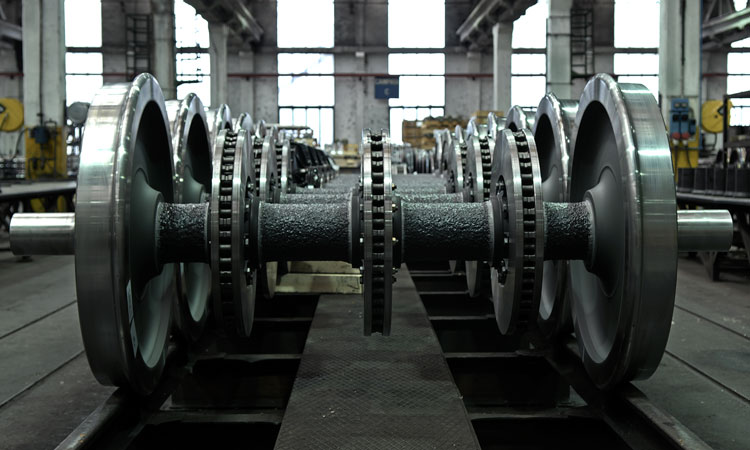
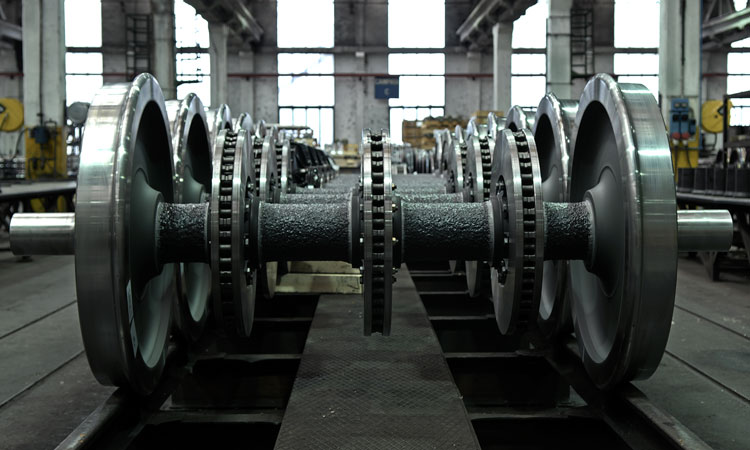
Railway wheelsets, wheels, and axles play a critical role in the safe and efficient operation of trains. In recent years, there have been significant developments in the usage benefits, lifecycle cost reduction, and standardisation of such components and assembled systems. In this context the European Railway Wheels Association (ERWA), is active to contribute to the development and advancement of the products manufactured and served globally by its members companies, composed of four industrial groups BVV, CAF MiiRA, GHH‑BONATRANS Group and Lucchini RS Group (see Figure 1).
Research and development
As an industry leader, ERWA is always focused on facts to intercept the needs of the market and drive innovation in the field of railway wheels and wheelsets. One of the main ways ERWA manufacturers achieve this is through their focus on research and development. The association works closely with its member companies and other industry stakeholders to identify the key challenges facing the railway industry. This includes the development of new materials and manufacturing techniques, as well as the testing and validation of new designs. One major development in the last 10 years has been the use of improved materials in the manufacturing of railway wheels and axles. For example, the use of high-strength steel and lightweight alloys has led to a reduction in wear and in the weight of wheelsets, resulting in lower lifecycle costs and lower energy consumption. One outstanding case is the development of special steel grades to solve practical issues that rail operators were facing in their daily maintenance works, such as wheel tread damages due to rolling contact fatigue phenomena that in many service conditions were drastically limiting wheel service life. A successful example is the steel grade classified as ERS8, which was introduced in the latest revision of the EN13262:2020 standard after long-term positive feedback collected from the from various European operators. This evolution also shows how proactive the ERWA association is in the CEN Standardisation working group (WG11) in contributing to the modernisation of European Standards that today finally open the possibility to more easily introduce new technical solutions not yet standardised to the market but compliant with defined safety requirements, providing chances to further develop service and durability performances.
Another relevant case is represented by the development of resilient tyred wheels for tramway applications, specifically developed with wheel centres made of forged aluminium alloy instead of steel with a clear scope of reducing vehicle loads and energy consumption.
Also, the introduction of advanced manufacturing techniques in the area of hot works, Non Destructive Testing precision machining, and surface treatments has allowed the production of wheelsets with improved accuracy higher performance and reliability which made ERWA manufacturers lead the market for wheelsets for high-speed and very high-speed applications.
Another area of focus has been the participation in UNIFE to ERA (the European Union Agency for Railways) working groups developing and revising the Technical Specification for Interoperability (TSI) for what concerns the interfaces and technical requirements that need to be certified in order be used in a unified European railway network.
This was a vivid example about how ERWA members actively engaged with regulatory bodies, such as ERA, to ensure that rules were in line with industry needs and were conducive to the development and advancement of the products. In terms of regulations, the European Union has also implemented regulations on the maximum permitted noise level for trains rolling, which has led ERWA manufacturers to the development of noise damping systems for wheels and wheelsets.
Combined experience and knowledge
Our members have also combined their extended experience and knowledge on axle coating solutions with the final aim of increasing the performance of standard axle protections. The clear objective of this was to improve the quality, reliability, and overall cost efficiency of railway wheelsets. To achieve this, ERWA has developed a guideline that proposes qualification tests to be performed in order to enhance the performance of the coating solutions. The guideline refers specifically to coating to protect railway axles manufactured and qualified according to the EN13261 standard. The tests outlined in the guideline are designed to evaluate the performance (durability) of the coating solutions under different conditions and environments that have an effect on the aging process, such as exposure to moisture, salt, and temperature cycles. The guideline also includes recommendations on the types of coating solutions that are best suited for different types of applications, as well as information on the proper application and maintenance.
The guideline developed by ERWA is an important tool for manufacturers and railway operators looking to improve the quality, reliability, and cost-efficiency of their wheels and axles. By following the tests and recommendations outlined in the guideline, manufacturers and operators can be confident that the coating solutions they use will provide the necessary level of protection for their axles and help improve the reliability in service of their railway wheelsets. In other words, ERWA’s guideline on axle coating solutions represents the combined experience and knowledge of our members in the railway wheel industry.
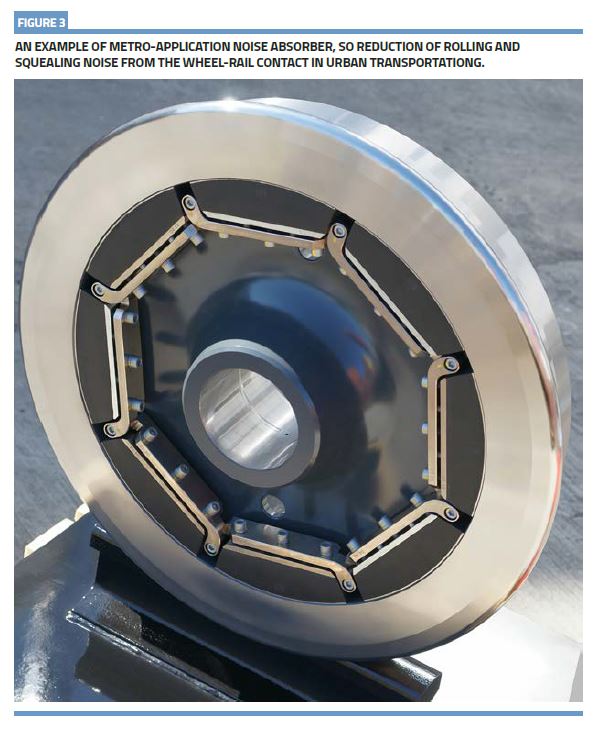
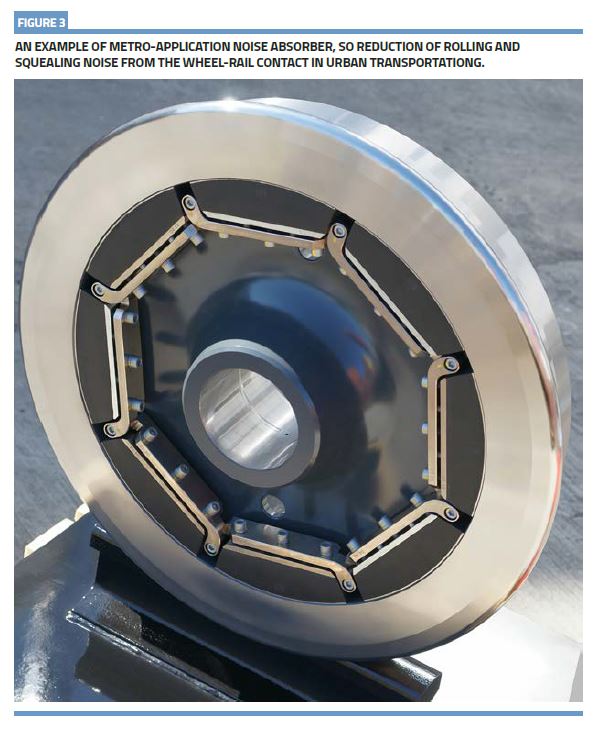
Projects
ERWA members are also actively involved in some ongoing UIC projects such as:
- Axle Surface Treatment to Improve Mechanical Properties (ASTIMP) which aims to define technical specifications for various available surface treatments that can improve the fatigue resistance or the corrosion protection of wheelsets components
- Brake Block Wheel Interaction, which is studying the thermomechanical behaviour of wheels with different brake block types in order to update the design and experimental validation procedure
- Wheels With holes in the Web (WWW) which is defining a more accurate method for modelling wheels with brake discs mounted on the web.
Continued developments
Performance and reliability
Looking to the future, research and development efforts will continue to focus on improving the performance and reliability of railway wheels and wheelsets. This will include the development of new materials and manufacturing techniques, as well as the testing and validation of new designs.
Regulations
Additionally, there will be a continued focus on standardisation and the development of regulations to ensure the safe and efficient operation of trains.
Digitalisation
One important aspect of this is the digital development of our products and related services. This allows us to provide efficient and accurate tracking to our customers, such as real-time monitoring and diagnostics, condition-based maintenance (CBM), as well as improved inventory management and forecasting.
Sustainability
Another key aspect of our philosophy is environmental sustainability. We understand that reducing the carbon footprint of our products is becoming increasingly important to decarbonise the transport sector, the second largest emitter after energy sector. We are actively working to measure and reduce the carbon footprint of our products, from steel manufacturing to machining operations. This can also be part of a dedicated certification.
The International Wheelset Congress (IWC)
ERWA, together with UNIFE, also organises international events such as the International Wheelset Congress (IWC) to share information and discuss new developments in the railway wheel industry. The first edition of the congress was organised in Italy back in 1963 and, since then, it has travelled across the world with successful editions. Following the last remarkable edition held in Venice, the congress is back in the United States of America for the 2023 edition in Chicago; the last edition in North America was held in Orlando in 2004.
In conclusion
The ongoing developments in the usage benefits, lifecycle cost reduction, and standardisation of railway wheels and wheelsets are helping to improve the performance and reliability of trains and support the growth of the railway industry. The future holds more research and development, standardisation, and regulations to ensure the safe and efficient operation of trains. As ERWA, we are active in all aspects of the development of the products and correlated services. Our member manufacturers are committed to providing the highest level of service to the train manufacturers and to the final users, the train operators.