The importance of instrumented wheelsets – accuracy is key
Posted: 21 March 2014 | Eduardo Elizalde Urdian, Julen Garzo Hernandez | No comments yet
Instrumented wheelsets (IWS) are designed to measure the wheel-rail contact forces. The evaluation of such forces is a key point in the processes of approval of railway vehicles in terms of dynamic behaviour. CETEST, a fully-accredited independent test laboratory, has its own solution for the design and implementation of instrumented wheelsets. This article describes the calibration and verification requirements for these wheelsets and presents the new rolling test rig developed by CETEST to meet these needs. The design of the test rig covers the objectives of reducing time and improving the accuracy and uncertainty assessment associated to the process.
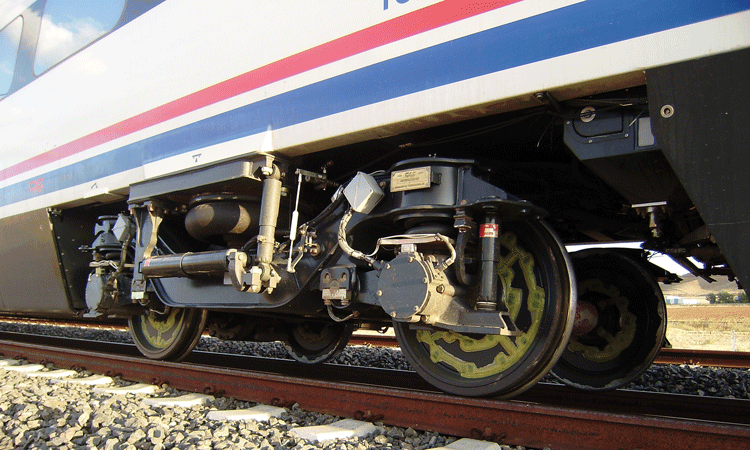
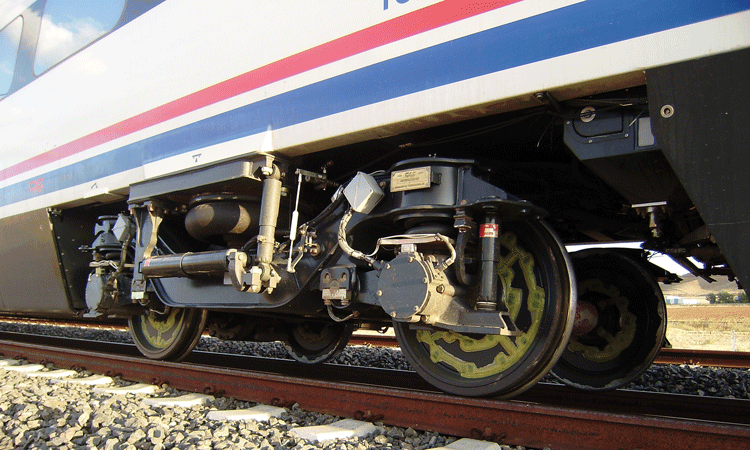
An instrumented wheelset on track
The wheel-rail contact plays a key role in the vehicle dynamics from the point-of-view of aspects such as rolling safety, ride quality, track fatigue, safety against derailment or wheel and rail wear.
Issues related to the acceptance process of new rolling stock – according to the main international standards – are particularly critical. This process is of extreme importance in terms of safety and economic consequences due to its high cost.
It can be particularly critical for high-speed vehicles or heavy load locomotives where – under extreme conditions – the measured forces tend to be very close to the limits established in the standard. In these cases, measurement accuracy of forces transmitted through wheel-rail contact is a highly important factor.
Instrumented wheelsets are designed to measure the wheel-rail contact forces. There are different solutions for implementing dynamometric wheelsets, generally based on strain measurement at different points of the wheels and/or axles.
The two key aspects that differentiate a ‘good’ measuring wheelset are the reliability and the accuracy of the solution. Developing a method that properly addresses both issues is a real challenge.
Reliable IWS
Different factors can affect the reliability of a measuring wheelset. First of all, the instrumentation has to respond adequately to the high accelerations that the wheelset is suffering. Secondly, it has to be prepared to avoid the degradation due to environmental factors like rain or extreme temperatures to which it is going to be exposed. Finally, the instrumentation has to resist to specific events such as the impact of stones from the ballast.
Another factor that could affect the life-cycle of the wheelset is the modification of the axle in some instrumented wheelset solutions. CETEST solves the need for connectivity between wheelset instrumentation and on-board equipment through slip ring or wireless solutions that must be adapted to the wheelsets.
An important characteristic of CETEST’s solution is that the measuring method is independent of the wheel shape so there is no need to manufacture any special wheel for the application. The easy installation radio frequency telemetry allows avoiding the manufacture of any destructive machining of the axle which increases the safety of the project.
These wheelsets have been successfully used in the complete range of railway vehicles: high-speed trains up to 350km/h, trams, metros, locomotives, freight cars and regional vehicles. For the case of high-speed vehicles, locomotives, freight cars and regional vehicles the complete method of the EN14363 standard has been successfully completed.
Accurate IWS
The improvement in accuracy can be understood as a reduction of the different sources of uncertainty in the measurement. The lack of linearity and reproducibility, the ripple effects resulting from the discretisation of the instrumentation, the effects of temperature and speed or the cross effect between different forces have to be considered.
CETEST has its own patented strategy for strain gage based measuring wheelset solution specially designed to minimise the effects of different sources of uncertainty.
Calibration process
During the manufacturing of the instrumented wheelset, the calibration process appears crucial in order to assess the accuracy of the measurement system. In this phase, calibration forces of known magnitude are applied to the wheelset and the corresponding output of the measuring system is acquired.
The starting point in the calibration process lies in the accuracy of the input variables on the calibration rig and the ability of the system to simulate the actual operation conditions of the wheelset under the vehicle.
The calibration of each wheelset takes place on a dedicated test rig which can be static or dynamic (rolling). Static test rigs are usually simple structures that allow applying vertical and lateral forces to the wheelset by means of hydraulic actuators. Reaction forces are directly measured with reference load cells. On the other hand, roller rigs are sophisticated machines capable of reproducing working conditions that are much more similar to those encountered during line tests. The advantages of roller rigs over static test benches are noticeable in terms of real simulation of running conditions…but also time saving.
Under this scenario, CETEST decided to develop its own roller test bench for wheelsets, which allows the independent application of turn, vertical and lateral loads in both wheels. As it has been explained, the main objectives were focused on the improvement in the calibration accuracy, the simulation of real operation conditions, the reduction of the calibration process time and the design of a universal solution for any wheelset.
Calibration accuracy is obtained by knowing load values and their position accurately. Actuation and positioning cylinders can be fine-tuned controlled in force and displacement, both in vertical and transversal direction, and independently of the wheel.
The rail gauge can be automatically adapted from 1,000mm to 1,668mm; and wheels form 500mm up to 1,300 diameter can be tested. Both sides of the wheelsets can be calibrated and verified both independently or together.
For each wheel there is a roller that is capable of applying both the vertical and lateral forces guided through two carriages with independent movement via servo-controlled actuators. Another actuator is used for applying calibration lateral loads. In this case, the load is also applied by means of a roller that contacts on the side of the wheel.
Simulation of the running conditions can be achieved by combining vertical and lateral loads, and by turning the wheelset up to its maximum speed. Vertical loads can be applied in any point of the wheel tread, whereas lateral loads can be applied both by contacting on the wheel flange or by changing the angle of attack via another actuator. In this way, real loading conditions, as for example derailing, can be simulated.
The reduction in the calibration time is achieved by programming discrete load sequences in known positions, in combination with a turn of the wheels. This implies that input variables for the correlation matrix between external forces and moments and the measures acquired from the instrumented wheelset can be obtained in a reduced time. Moreover, by turning the axle, the rippling effects can be simultaneously taken into account.
Finally, the developed solution is universal because it can be adapted to different rail gauges, different wheel diameters and axles with independent turning wheels.
This test bench allows CETEST to offer more accurate instrumented wheelset solutions, perfectly tested and in short development times. This test bench complements the CETEST’s portfolio in terms of fixed and portable rigs that – together with a broad set of instrumentation – set CETEST in a leading position between railway laboratories worldwide.