Rail Performance Monitoring: Paving the way for advanced track solutions
Posted: 11 June 2019 | Johannes Wundersamer | No comments yet
Using metro systems as an example, Johannes Wundersamer, Head of Rail Performance Services at voestalpine Railway Systems, provides an overview of their customised Rail Performance Monitoring service, a tool to investigate the operating characteristics of rails and to assist rail maintenance organisations in changing re-active systems into pro-active ones.
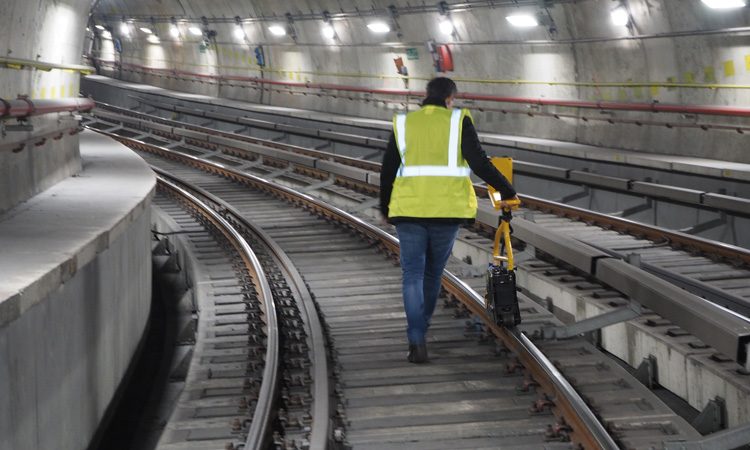
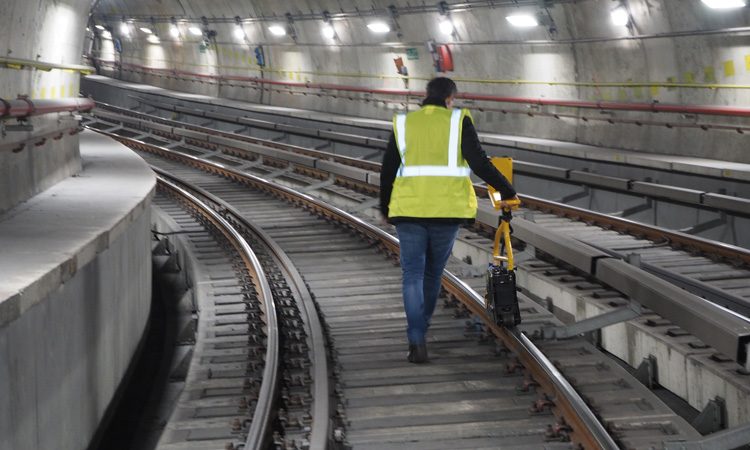
Generally, metro systems are subjected to increasing train frequencies and decreasing engineering hours for maintenance, mainly caused by the growing population in urban city centres. Usually metro services start early in the morning around 06:00 and finish approximately at midnight, but some cities are considering running 24/7 operations. For track inspection and maintenance teams, this means important track work needs to be carried out within very tight timeframes – the so-called ‘engineering hours’.
The main driving forces for metro system rail maintenance are operational damages such as rail wear and plastic deformations, corrugation and rolling contact fatigue defects (head checks) as well as system-caused defects such as squats.
The total service life of rails as well as its maintenance demand throughout the entire product lifecycle is mainly determined by the initial quality and the chosen maintenance strategy. A high initial quality is the basis for a long-lasting service life and can be achieved by considering heat treated premium or super premium rails in critical track segments, such as curves and stations. In addition to the initial quality, operational rail maintenance is at least as important in order to achieve a satisfying rail service life. State-of-the-art maintenance strategies in metro systems are based on a corrective and/or a preventive approach, whereas the general trend of advanced maintenance management is more and more going into the direction of condition-based or even predictive rail maintenance in order to increase efficiency and to significantly reduce the entire lifecycle costs. For achieving this step-change in rail maintenance, detailed knowledge about the operational product performance regarding the deterioration progress is required.
voestalpine Railway Systems has been successful in developing a new kind of customised service, called Rail Performance Monitoring, in order to support advanced maintenance managers by means of investigating the operating characteristics of rails in collaborative projects.
Monitoring of operational rail deterioration
Operational rail deterioration in metro systems can mainly be distinguished in wear and plastic deformation, corrugation, rolling contact fatigue (head checks) and system-caused defects such as squats1. A detailed description of rail defects is given in literature such as the UIC Code 712 – Rail Defects2.
All these operational rail deterioration mechanisms and rail defects require different inspection technologies in order to identify the current rail condition and to derive the deterioration progress as a function of load. Depending on the maintenance strategy the overall target is to know the current rail condition in each location at any time and to define adequate maintenance measures at the right moment.
For a continuous and detailed analysis of operational rail deterioration as a first step a customised selection of heavy-duty track segments is necessary in order to determine the respective rail damage mechanisms and to derive the required inspection technologies. In the following, a collaborative project with specific goals is set up in order to monitor the rail deterioration progress in several missions as a function of load. During the monitoring period the main targets are:
- To determine the vertical and horizontal rail wear progress
- To determine the rail corrugation growth
- To detect and evaluate rolling contact fatigue and system-caused defects (head checks and squats)
- To determine the head check growth.
The results of the monitoring period are the basis for all further investigations and provide an essential basis for the development and implementation of advanced rail maintenance strategies.
Development support for customised rail maintenance strategies
When the monitoring period is complete, the development of customised maintenance strategies begins. Rail material loss can be distinguished in natural and artificial wear. Depending on the respective maintenance strategy and the defined maintenance intervention limits, artificial rail processing, such as grinding or milling, is occasionally necessary in order to remove surface defects and to adjust suitable target profiles. Figuring out the right moment for maintenance intervention is essential in order to assure an optimal usage of the rail over its entire lifespan. In particular, if the maintenance intervention takes place too late, surface defects cannot be removed completely, and a rail renewal is the only alternative in many cases. In a worst-case scenario, rails can sometimes need renewing without having achieved its final wear limits due to heavy rolling contact fatigue defects such as head checks or other surface defects.
The development of customised rail maintenance strategies is based on real rail performance data and includes, for example, recommendations for inspection technologies and intervals, technical and economically meaningful intervention limits, lifecycle comparisons of different alternatives (rail grinding vs. milling) and wheel-rail interface optimisation including recommendations for appropriate target profiles.
The overall target of this ‘Rail Performance Monitoring’ approach is to assist rail maintenance organisations in changing re-active systems into pro-active ones in order to assure a longest possible rail service lifetime with the lowest possible maintenance effort.
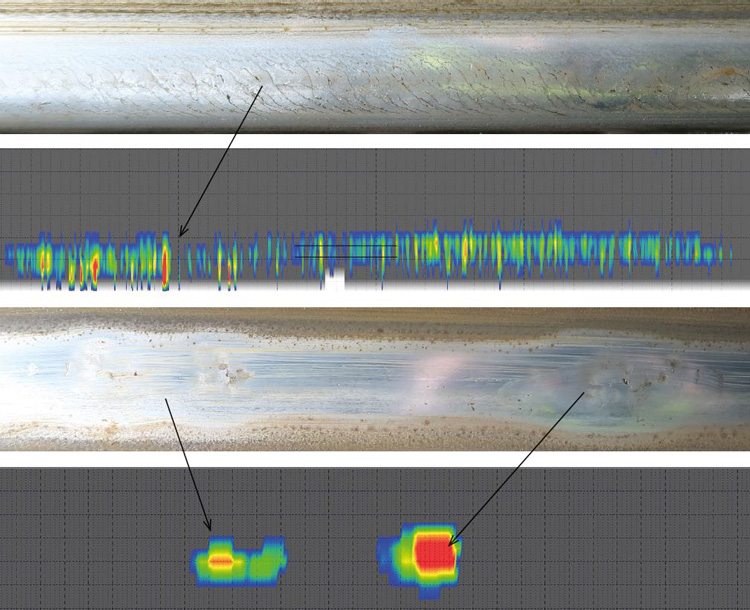
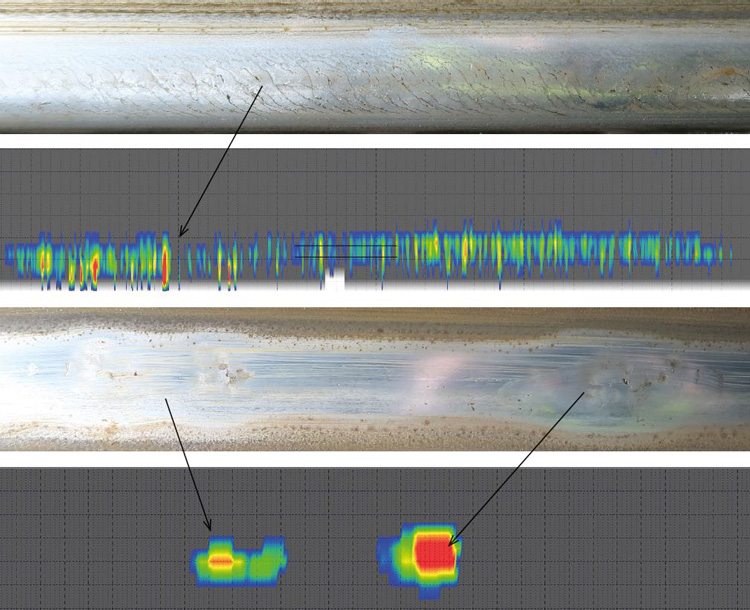
Figure 2: Practical rail testing examples – head checks and squats
Practical examples
Monitoring of rolling contact fatigue (RCF) defects such as head checks or system-caused defects like squats have become increasingly important in metro systems over recent years since these defects are a main driver for corrective rail maintenance measures such as grinding or milling. In Figure 2, practical rail measurement and testing examples are given, which provide the database for further analyses of the rail deterioration progress. Beside the strategic long-term benefits, the acquired results can also be used as an immediate decision-making basis for short-term maintenance activities.
Beside the detection of surface cracks, the determination of the real defect depth is also possible. In connection with other monitoring results such as rail wear reserves and corrugation depth, a detailed prediction of the future deterioration development and required maintenance effort is possible.
Summary
Rail performance monitoring is a systematic method to determine the deterioration progress of rails in metro systems as a function of load. The acquired results provide an essential basis for the development and implementation of customised rail maintenance strategies. The overall targets are to assure a longest possible rail service lifetime with the lowest possible maintenance effort by defining technical and economically meaningful intervention limits and by changing re-active into pro-active maintenance strategies. Beside the depiction of the operational behaviour of rails, a wheel-rail interface optimisation as well as lifecycle comparisons of different alternatives can also be included in customised rail performance monitoring projects.
References
- A. Jörg, R. Stock, S. Scheriau, H.P. Brantner, B. Knoll, M. Mach, W. Daves: The Squat Condition of Rail Materials – a Novel Approach to Squat Prevention; 10th International Conference on Contact Mechanics, Colorado Springs, USA; 2015.
- UIC Code 712 R – Rail defects; 4th edition, January 2002.
Biography
Johannes Wundersamer has worked within the railway industry since 2011. For voestalpine Railway Systems he has held several positions within the Technical Customer Service, Sales and Business Development departments. Johannes is currently responsible for Rail Performance Services. In 2010 he received a master’s degree in Metallurgy at the University of Leoben.
Issue
Related topics
Digitalisation, Technology & Software, Track Systems, Track/Infrastructure Maintenance & Engineering