Continually improving track systems for optimum safety and efficiency
Posted: 8 April 2019 | David Clarke | No comments yet
The ‘permanent way’ is often seen as a traditional and well understood technology – surely there can’t be much new out there? But as David Clarke, Technical Director of the Railway Industry Association (RIA) explains, you’d be surprised – UK railways, their suppliers and British universities are at the forefront of innovation to continuously improve the track system regarding both safety and efficiency.
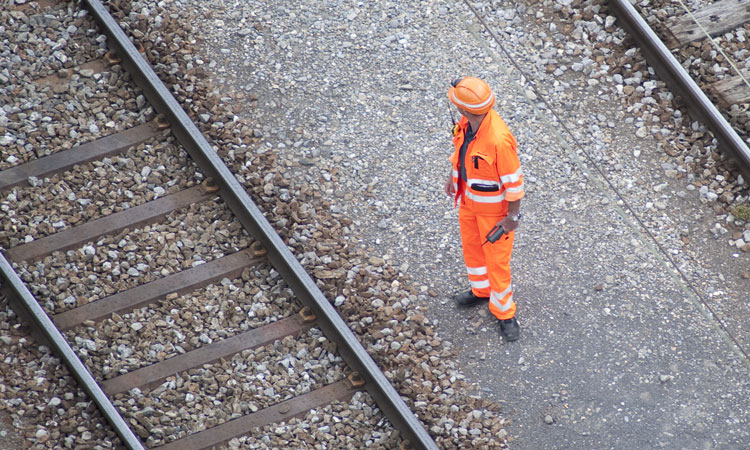
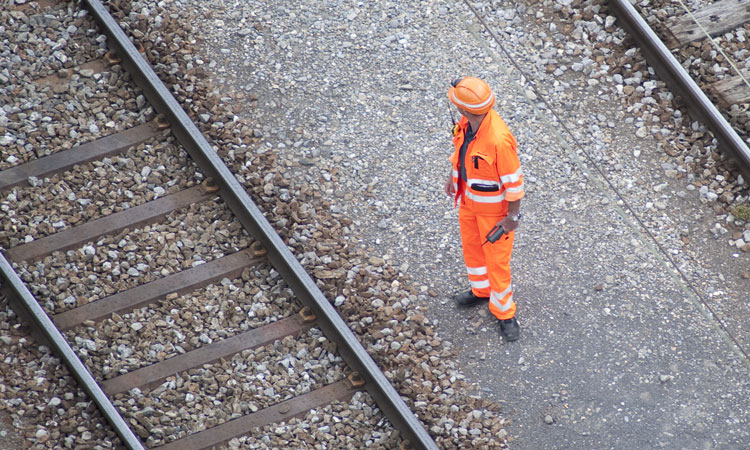
IT IS A fact that steel wheel on steel rail remains an extraordinarily energy efficient means of moving heavy loads, be it passenger or freight trains, due to the low rolling resistance. This must be carried out safely, dealing with high speeds and accumulated tonnage and, like their cycling peers, British track engineers have been rigorously pursuing marginal gains to reduce the number of broken rails by approximately 70 per cent in the last 15 years to levels which are world-class. The techniques deployed include rail grinding, train borne ultrasonic testing, hand-held eddy-current testing, plain line pattern recognition and the rail defect management system.
Research and testing to prevent wear and rolling contact fatigue
Managing the rail-wheel interface is key to safety, train performance and rail life. The University of Sheffield is at the forefront of rail-wheel interface research focused on preventing wear and rolling contact fatigue while optimising lubrication and adhesion. Recent projects include; determining wear characteristics of new premium rail steels, with Network Rail understanding the influence of bridge locations and track alignment on rail-wheel adhesion; RSSB new techniques of low adhesion mitigation (see Figure 1) are being developed; and new equipment through the UK Rail Research and Innovation Network (UKRRIN) with British Steel is driving materials research. A creep-force model (WILAC) has been developed for small amounts of water in the wheel-rail interface that is now being extended to take account of leaves, and WILAC has been integrated with the LABRADOR train braking model. It is hoped that this research will lead to a better understanding of how to manage rail adhesion; maintaining safety whilst realising a potentially significant performance benefit.
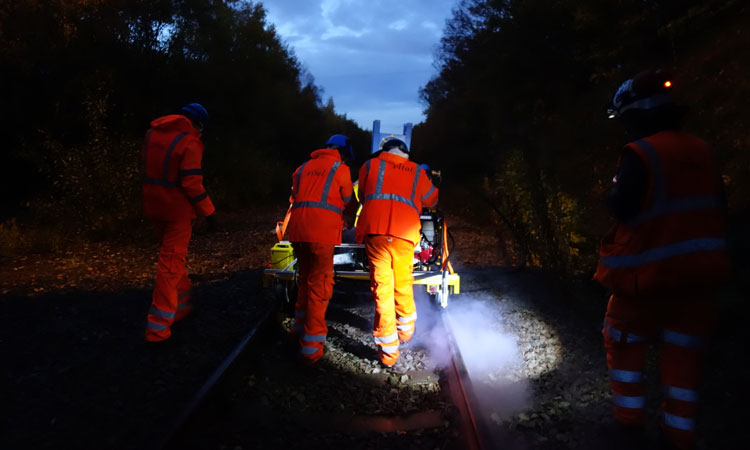
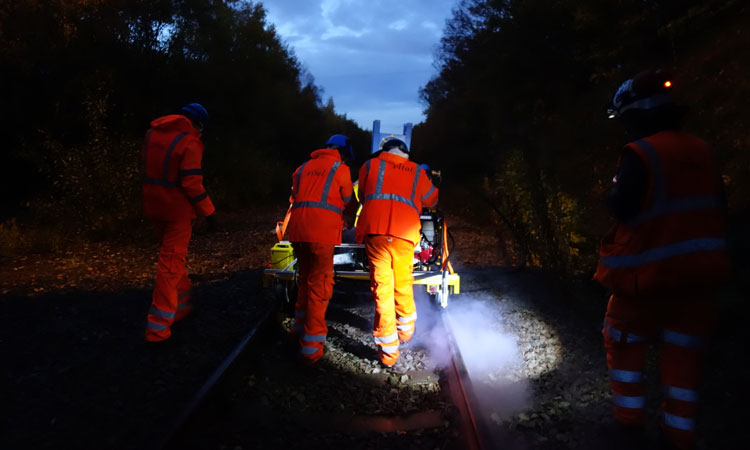
Figure 1: Preparing the rail head for adhesion testing
Conventional and even premium rail steel cannot always meet wear and rolling contact fatigue performance demands. The University of Sheffield has been working with British Steel (see Figure 2) and Network Rail on non-steel rail coatings applied with a laser cladding additive manufacturing process. These coatings bring dramatic reductions in plastic damage from passing wheels, for example reducing rail material flow (‘lipping’) at insulated block joints that can otherwise form unwanted electrical connections between signalling blocks. In 2019 this work is moving from full-scale laboratory studies to its first track installation. It is hoped it will also be valuable in reducing wear on switch blades and crossing noses.
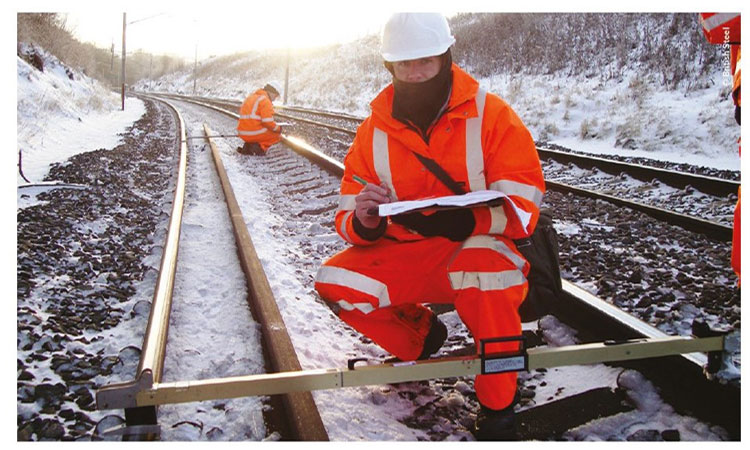
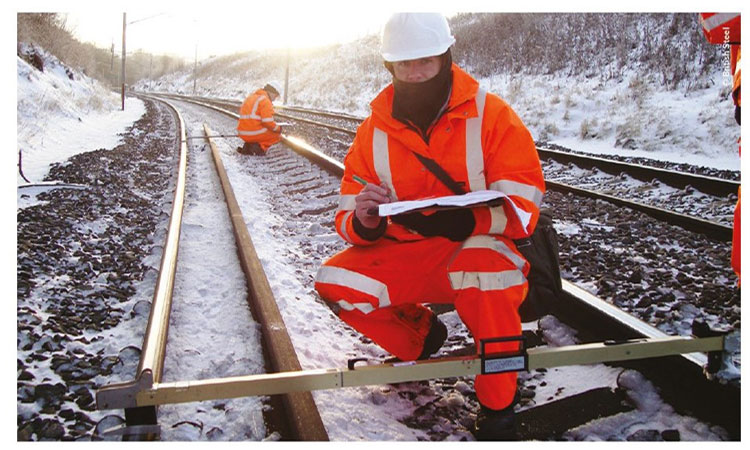
Figure 2: Premium rail performance monitoring is carried out whatever the weather
Reducing track deterioration
Rail is held in position and supported by either a sleeper and ballast system or a slab track system and the formation beneath. Track engineers have always understood that variability in the resilience of this system caused by deterioration in either or both the formation or the track system leads to poor ride and increased maintenance. Through the work of the Cross Industry Track Stiffness1 Working Group and their freely available guide, there is an improved understanding of how to design and maintain the track system to avoid these issues. The guide includes case studies providing practical examples of remediation techniques.
Focus on effective drainage
Effective drainage is crucial to the stability of the formation and therefore also railway operation. Poor drainage can lead to flooded lines and expensive service delays, or to instability of the track substructure and embankments with potentially deadly consequences. A combination of modelling and intelligent instrumentation is being developed by the University of Sheffield with Network Rail to monitor drainage assets, including implementing a pilot scale monitoring programme. This will enable automated drainage condition assessment with triggers to send maintenance staff to the correct location prior to flooding events, ultimately improving rail safety and service reliability.
Track stiffness
The concept of track stiffness is especially important for high-speed lines with, in the case of High Speed Two (HS2), up to 18 trains an hour at 330km/h equating to more than 60 MGTPA. Where slab track is used it is proposed to be in prefabricated panels around 6.5m-long which is intended to allow a balance between factory quality and ease of replacement. In this case the client has specified the track stiffness and track fastening adjustment they require.
Pandrol is one supplier who have developed an innovative approach to this challenge. Its Fastclip Baseplate provides the necessary adjustment including the ability to be slued to suit the curvature. This allows the pre-fabricated slabs to be identical with a Pandrol-developed robotic system (see Figure 3) which will pick baseplates and place them in the exact positions and orientations required. The combinations of baseplate positions on a given slab can be selected at the touch of a button. Scanning assists and confirms the baseplate positioning, and the configuration of each slab is coded into an RFID tag that is affixed to the slab before it leaves the factory, so that the curve or transition where it is destined to be installed can be recalled at any time. This robotic installation increases the reliability and quality of the installation on which the ultimate quality of the track alignment depends. It also increases the rates of production and reduces the risks of delays or interruptions.
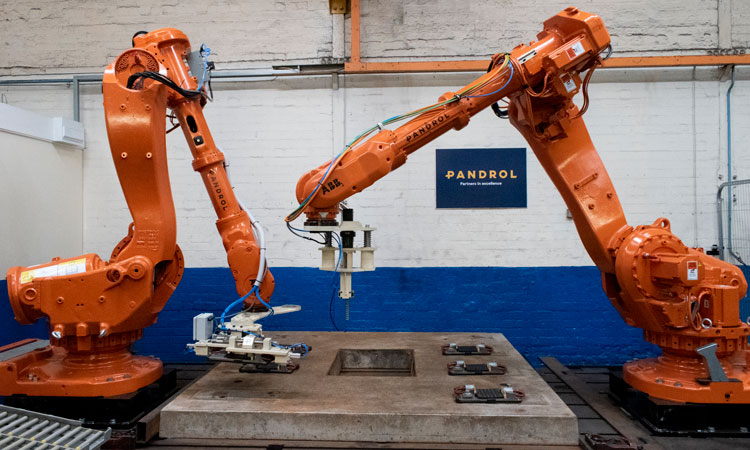
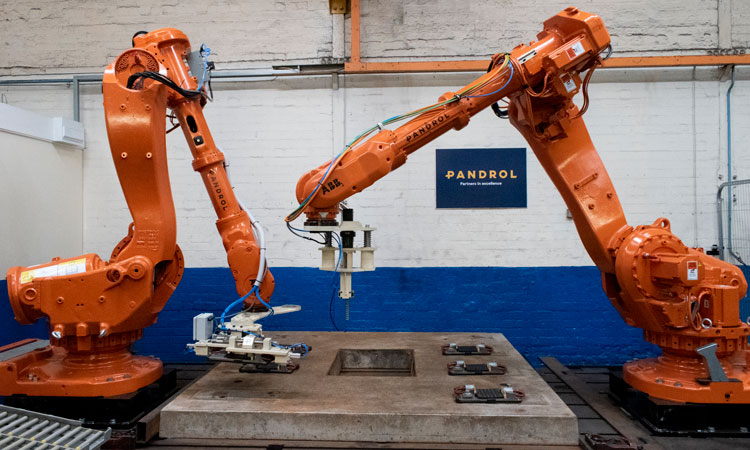
Figure 3: Robotic positioning of baseplates on prefabricated slab track panels
‘Track to the Future’ research programme
Significant work on other means of managing track stiffness, particularly in ballasted track, has been carried out by the industry supported by consortia of universities. In particular the ‘Track to the Future’ research programme has investigated measures including; fibre reinforced ballast which is under trial on London Underground; Under Sleeper Pads which have been shown to increase the contact area and thus reduce stress; work to improve the understanding of the relationship between track stiffness, settlement and rail geometry deterioration; the scope for recycling a greater proportion of ballast; and understanding the influence of undertrack crossings on track quality.
Another Track to the Future project focuses particularly on Switches and Crossings (S&C) aiming to gather evidence from site measurement (see Figure 4) and modelling of performance in terms of geometry and rail profile, deformation under train load, support variability modelling, rate of geometry deterioration and noise.
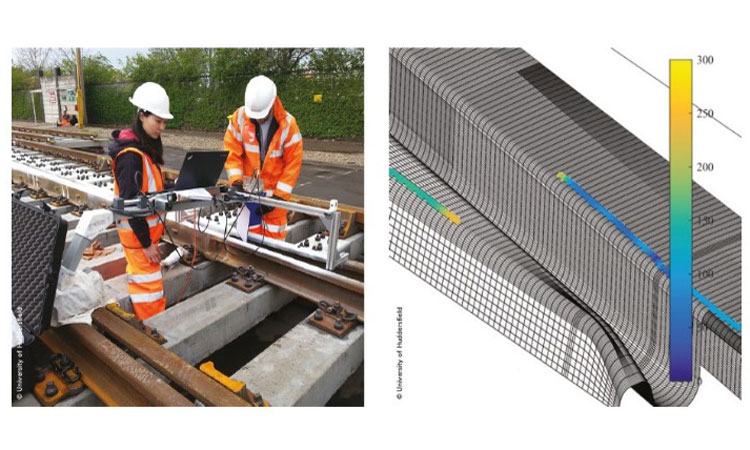
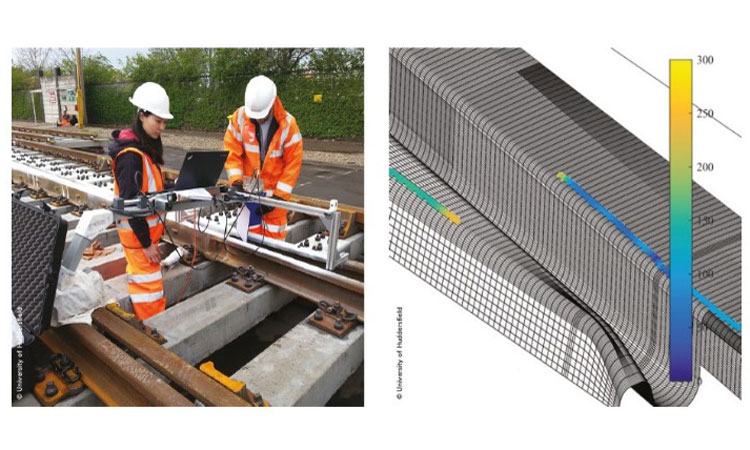
Figure 4: Track to the Future: Left, trolley developed for 3D shape survey. Right, post processing of results
The way track and its components behave is intrinsically linked to the way the train rides on the track. The University of Huddersfield has been applying advanced computer simulations and numerical methods across a range of track design improvement and maintenance optimisation projects. Through analysis of vehicle induced dynamic loadings, their work has supported Network Rail and its suppliers in the re-design of the NR60 S&C unit, improving wheel-rail guidance to reduce forces and addressing cast component failures.
Simulations of vehicle-track dynamics are being used to analyse the forces between wheel and rail, enabling the use of damage prediction models to reduce the occurrence of rolling contact fatigue and wheel-rail wear on major infrastructure projects including Crossrail and HS2. The simulation methods are also being used to assess vehicle ride performance in high-speed curve transitions, ensuring that the UK’s high-speed track alignment delivers world-class passenger ride comfort.
Taking advantage of new tools
As a result of computer simulation studies such as these, track designers are changing their design principles to take advantage of the new tools available to them.
An additional benefit of computer simulation techniques is the generation of very large amounts of data that can be post-processed and applied in the development of predictive maintenance planning tools. This technique has been applied to the Crossrail network and has allowed Transport for London (TfL) to plan rail grinding and replacement regimes in advance of the system opening to traffic.
There is lots of recent activity in the sector, both in UK industry and universities, all of which is continuously improving the products and techniques available to track engineers.
Reference
1. ‘Track stiffness’ is the (point) load required to produce a unit deflection of the rail at the location where the load is applied (kN/mm)
Biography
Issue
Related topics
Track Systems, Track/Infrastructure Maintenance & Engineering