Wayside Train Monitoring Systems: Networking for greater safety
Posted: 4 August 2011 | Urs Nietlispach - SBB, Wassim Badran - SBB | No comments yet
Swiss Federal Railways (SBB) has the densest rail network in the world in terms of the number of trains per kilometre per day – and the number is still rising. This is a challenge that must be met without compromising on safety. Trains must therefore be monitored and scheduled with the utmost care. SBB’s Switzerlandwide integrated system of networked Wayside Train Monitoring Systems (WTMS) is one of the key elements in this process.
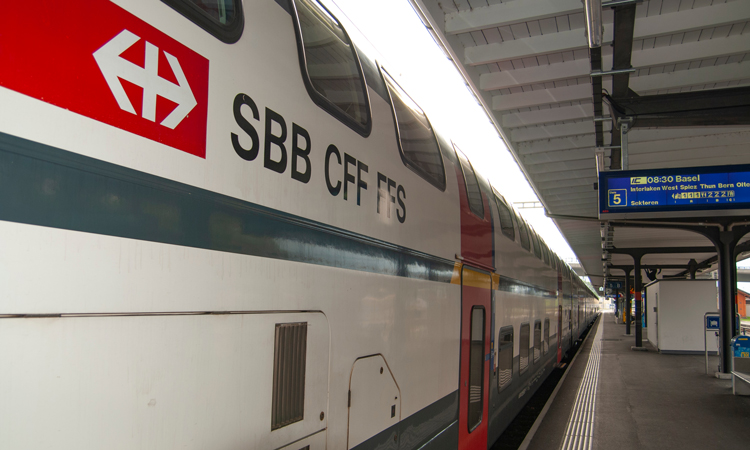
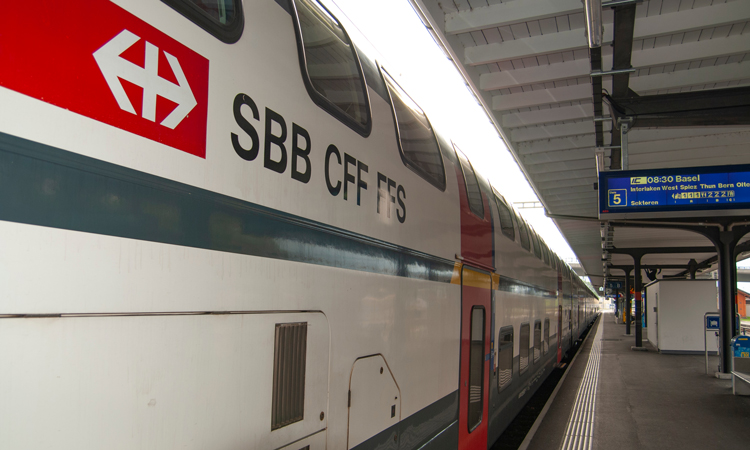
Swiss Federal Railways (SBB) has the densest rail network in the world in terms of the number of trains per kilometre per day – and the number is still rising. This is a challenge that must be met without compromising on safety. Trains must therefore be monitored and scheduled with the utmost care. SBB’s Switzerlandwide integrated system of networked Wayside Train Monitoring Systems (WTMS) is one of the key elements in this process.
SBB is faring well: in 2010, 951,000 people a day travelled on the company’s train services – more than ever before. SBB Cargo also increased its output significantly, carrying 200,000 tonnes of freight a day. Utilisation of SBB network capacity had already been high, and the increase in demand has raised it even further. An average of 95.4 trains a day travelled over each kilometre of SBB track in 2010. This figure is unequalled anywhere in the world – and is still rising.
A variety of control functions
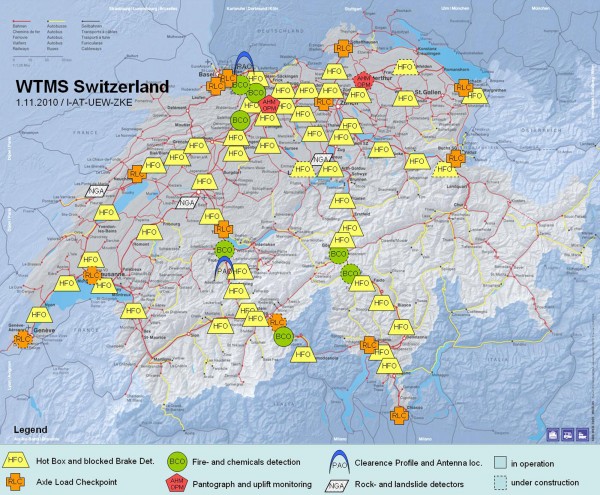
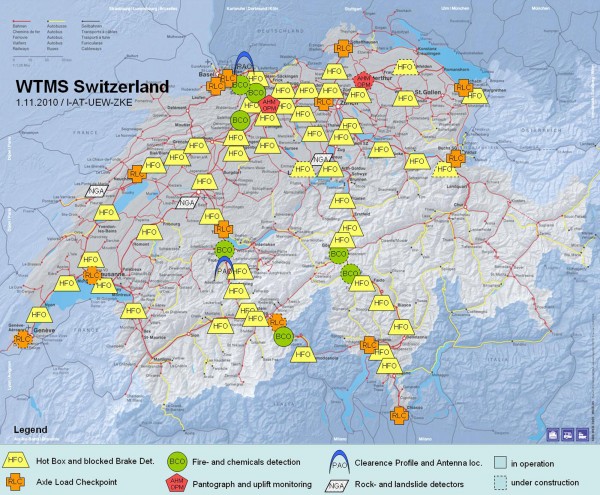
Figure 1: Over 100 measuring systems across the SBB network
This world-beating traffic volume has to be mastered on a daily basis – without compromising on safety. So-called WTMS, of which Switzerland now has over 100, make a significant contribution to the safety of the country’s rail network. The various measurement and detection systems monitor rail traffic around the clock and perform a variety of control functions automatically. These include identifying technical deficiencies such as load displacements, overloading, out-of-gauge rolling stock and dangerous chemicals. The network is constantly being expanded. SBB has currently integrated the following operational measurement sites of various types into its network (see Figure 1):
- Hot axle box and brake-locking detectors (~80 sensors)
- Wheel-load check points (~12 sensors)
- Fire and chemical detectors (~10 units)
- Clearance profile and antenna detectors (2 units)
- Pantograph uplift measurement stations (2 sensors)
- Natural disaster alarm systems (avalanches, rock falls; 3 sites).
The hot box and brake-locking detectors are used the most frequently. These systems measure the temperature of the axle bearings and brake discs on trains passing at full line speed. The measurements enable the systems to identify locked brake pads, hot brake discs and overheated axle bearings. Since 1998, there have been no derailments in Switzerland as a result of hot axle boxes or locked brakes.
Networking WTMS is the key
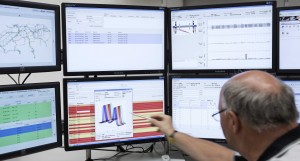
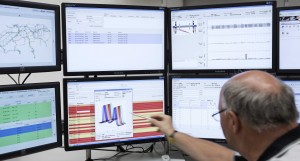
Figure 2 ‘ZKE Netz V2’ in operation
An important factor in this success has been the consistent networking of the various wayside monitoring systems and the connection of these to the ZKE-Interventionszentrum (WTMS Train Monitoring Facility) in Erstfeld. In Switzerland, the related application is known as ZKE Netz (network) V2 – see Figure 2. The nationwide networking of the sensors gives rise to numerous benefits for a careful and nonetheless rapid analysis of each alarm. Whereas various WTMS can work on their own to detect vehicle problems with varying degrees of reliability, only the consistent networking of all sensors can:
- Virtually eliminate delays caused by false alarms
- Enrich measurement data with train data (departure station, destination, list of vehicles, GSM R contact details of train driver and manager), so that an optimised intervention can be initialised at the train
- Significantly reduce stopping times for trains with locked brakes by providing the driver with professional support by phone from the Train Monitoring Facility as soon as the alarm is triggered
- Ensure early diagnosis of problems on the train so that a stop can be scheduled on time and with a minimum effect on train path availability
- Guarantee train monitoring across the entire Swiss rail network.
Automatic classification and prioritisation
Alarms from sensors in the WTMS, or from algorithms evaluated by the sensor data, are immediately classified by ZKE Netz V2. The application selects the alarm process automatically depending on the severity, alarm value, day of the year, time of day and vehicle type, and prioritises it accordingly. This ensures that any alarms with a high likelihood of being serious are given top priority by the Train Monitoring Facility in Erstfeld. Potential false alarms are flagged to prevent the operator from becoming overloaded.
Erstfeld’s specialists assess the alarm signals 24 hours a day, 7 days a week, 365 days a year. Human intelligence and expert knowledge in the decision-making process guarantee correct classification and assessment. A consistent follow-up procedure for all alarm signals ensures continuous improvements to classification.
Immediate train stop
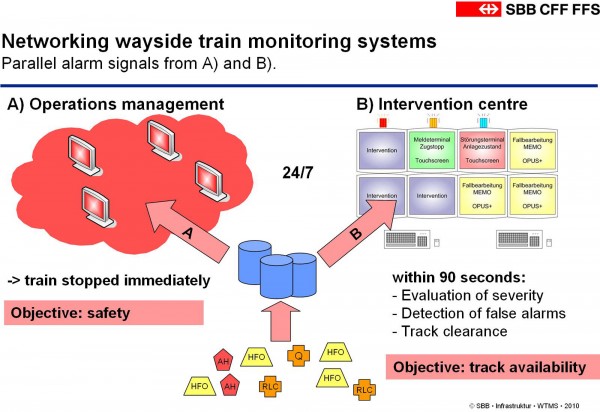
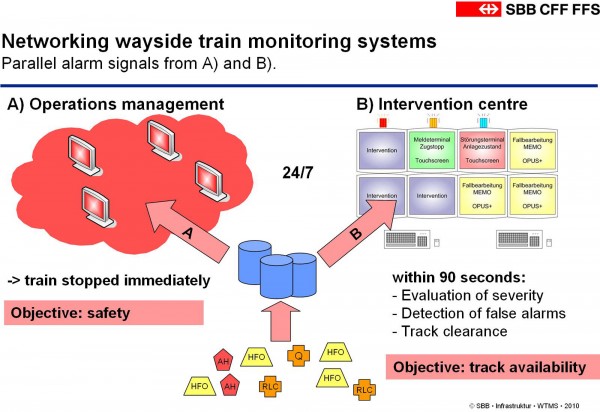
Figure 3 The Movements Inspector and the Train Monitoring Facility receive alarm signals in parallel
For alarms of the highest level, such as for a hot box over 100°C, the train is stopped immediately, i.e. no further signals will be set at green. In order to achieve this, the alarm is triggered for the Movements Inspector responsible for the area in which the problem has occurred. If the alarm is not cancelled by this inspector within 30 seconds, it is immediately escalated to the train monitoring facility.
A parallel alarm to that received by the Movements Inspector is also triggered at the Train Monitoring Facility (see Figure 3). In contrast to the Movements Inspector, who is responsible for stopping the train, the experts in Erstfeld analyse the detailed raw data from the measuring system that set off the alarm. They are able to use this information to classify the alarm more exactly. False alarms, such as sunlight reflections or sparks emitted by hot boxes, are recognised within seconds. In the event of a false alarm, access to the train path is immediately restored by the Movements Inspector without the train having to be stopped. In an ideal situation, the train driver will not even notice that the train has sent out a (false) alarm.
Optimised train stop
For less dangerous alarms – locked brakes (>350°C for disc brakes, 250°C for shoe brakes), for example – the train may continue for a maximum of 10km. The driver can thus select the best possible place to enable passengers to be transferred to a replacement train. In the case of a freight train, the process allows for a train of the corresponding length to move out of the way and avoid blocking the path.
For classification, the same process is used as for immediate stops: the Movements Inspector stops the train, while the experts in the Train Monitoring Facility analyse the data from the measurement sensors in parallel, giving the train the ‘all clear’ within 30-90 seconds, depending on severity. Around 45% of all train stops can be avoided in this way.
Trend alarm
For alarms that are relatively unlikely to indicate major problems, the ‘trend alarm’ process is triggered. Examples of causes might be a brake shoe temperature of 200–250°C or hot box alarms for which the measuring system itself suspects the cause to be sun reflection or sparks flying.
Trend alarms are only received by experts in the train monitoring facility. The Movements Inspector is not notified immediately. If the expert responding to the alarm believes that a real problem is developing, the Movements Inspector can be asked to stop the train at the next suitable location. In this instance, it is the expert who decides how much further the train should be allowed to travel and at what speed.
This early detection from the analysis of irregular measurement values within the effective scope of the alarm enables faulty trains to be dealt with early and the selection of the best possible location to stop the train. These are two decisive factors in train path availability.
Differentiating between alarm signals
When selecting alarm limits and tuning classification algorithms, the trade-off is always between safety (the lower the alarm limit, the safer the process) and availability (the higher the limit, the fewer false alarms). Experts can use the three procedures to reliably detect an overly conservative automatic classification without it causing availability problems. This additional safety layer facilitates innovation in automated alarm assessment without compromising on safety. So, for example, automated sun reflection and spark recognition was only activated on the measurement systems once this safety layer was made available. It is also worth considering that when software automatically classifies alarms, it only selects the alarm process and the alarm priority. No alarm is ever actually switched off. Even if sparks can be reliably detected in time to register a false alarm, they are only harmless if the train is braking. If the train does is not brake but sparks are still being detected, this is indicative of a very dangerous situation: it means a completely locked wheel is sliding along the track!
Avoiding delays
As soon as a train has been stopped, it is up to the expert in the Train Monitoring Facility to provide maximum support in order to get the train moving again as soon as possible – whether at full or reduced speed – to the next siding or to its destination. In 90% of all cases, the problem can be solved simply thanks to the telephone support provided by the expert to the train driver.
In the event of a serious problem where a vehicle has to be removed (detached) from the train, the average delay incurred is 106 minutes. Simple actions such as releasing the handbrake cause delays averaging 26 minutes. In such circumstances, the train driver as the ‘man on the ground’ is also helped to classify damage already done and to decide on the train’s onward journey. Sending out technical vehicle inspection staff can therefore be kept as a last resort. This not only prevents staff being deployed unnecessarily, but above all saves long waiting times on site until the vehicle inspectors arrive.
Two principles
The network of WTMS is based on two decisive principles:
- People as decision-makers
- Maximum redundancy – using simple methods to achieve high availability.
ZKE Netz V2 sensors transmit their information to two data processing centres simultaneously. The data are assessed independently and both processing centres send their alarms to the Movements Inspector. The Movements Inspector’s application merges the two signals into his one alarm. In a worst case scenario such as a partial network closure, the alarm would sound twice and possibly in two different locations. This double train stop is a fail-safe procedure and will at the latest be noticed by the driver: he can only stop once in the same place, after all.
This active-active redundancy alleviates the need for maintenance slots. Even updates can be carried out without interrupting the system. The application has achieved 100% end-to-end availability over the last 20 months.
Data enrichment
The raw ZKE Netz V2 measurement data are enriched with details such as the train number, vehicle information, loading and contact information, etc. These enriched data are needed to ensure correct and efficient alarm processing. The enrichments come from various peripheral systems (see Figure 4). They are also stored in the database, creating a valuable resource for analyses as well as evaluations and investigations:
- Train numbers are taken from the operation control system. This communication is currently one-way, but could be expanded to include an automatic train stop option
- Freight train information, such as vehicle weight and details of dangerous goods, comes from the Cargo Information System (CIS)
- Passenger train information is derived from the KompoEVU system, which supplies information about individual trains, including real-time vehicle identification data from the RF-ID systems
- ProSurf delivers the scheduled routes and timetable information for the trains, as well as the train company that operates each service
- ESI is an SBB-wide database of previous safety-relevant rail traffic incidents.
Conclusion and outlook
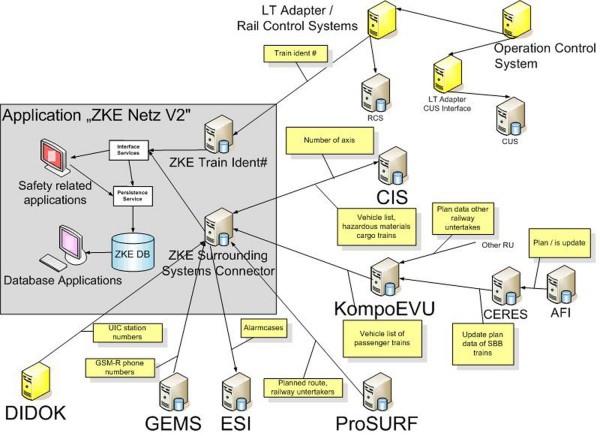
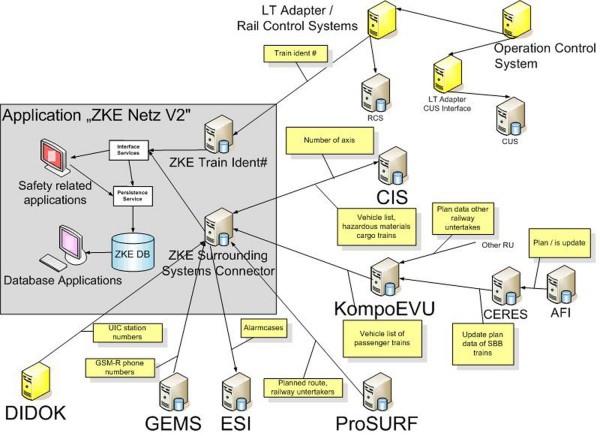
Figure 4 Interfaces of ‘ZKE Netz V2’ to peripheral systems
In 2010, SBB again suffered no major accidents in which passengers died or were seriously injured. Our WTMS and the globally unique way in which they are networked have made an important contribution to the safety of rail travel. In addition, a potential 390,000 minutes of delays each year are reduced to around 90,000 minutes. This is impressive proof of the high performance provided by the solutions introduced to avoid delays and increase train path availability. SBB has now been operating this system for five years. The fact that not a single derailment during this period has been caused by hot boxes or wheel failures is further evidence of the contribution that this system makes to safety.
So what does the future hold for WTMS? The exchange of data across a network has already become a reality in Switzerland – WTMS alarm signals from BLS are already being processed by SBB’s Train Monitoring Facility in Erstfeld. But we must not rest on our laurels. The cross-border exchange of data throughout Europe has to be the future goal among infrastructure operators. Only when this becomes reality will it be possible to solve developing problems at a border station. Almost everywhere there are ample reserves of space, available staff and replacement vehicles, loading cranes and shunting and stabling options, and these must be used to alleviate vehicle problems and load displacements. This will help us achieve a further increase in the punctuality of cross-border services and avoid blocked train paths across whole countries. As a minimum, this measure should be implemented throughout the European freight corridors in the near future. Hurdles in this process should be more of a political than a technical nature. Under the direction of Europoint, SBB is taking a step forward in this process by organising an international WTMS conference in Lucerne on 22 September 2011. We would be delighted to welcome you to this event.
References
- http://www.waysidemonitoring.eu/
- Nietlispach, U. (2009) “Zugkontrolleinrichtungen bei den SBB” (“Wayside Train Monitoring Systems at SBB”) in: Signal + Draht 101, Edition 1, pages 25-28
- Frey, M.; Nietlispach, U. (2011) Consistently Networked WTMS at SBB in: RTR Special 2011.
- Schöbel, A. (2011) Networked Wayside Train Monitoring Systems as a Key Issue for Rescheduling Freight Traffic, RailRome 2011 in Rome, 16-18 February 2011
Biographies
Wassim Badran is a Member of the Infrastructure Management Board and has been Head of Installations and Technology since April 2011. He is responsible for the monitoring, optimisation and development of all installations on the rail network. Wassim is a qualified specialist in his field and has gained extensive experience both inside and outside the railway industry. For 20 years, he held various management positions in the IT and engineering sectors. Prior to joining SBB Infrastructure, he worked for the SBB IT Unit as Head of Business Applications. Wassim studied Applied Chemistry and Control and Control Engineering in the UK, and holds a doctorate from the University of Oxford. In addition, he completed a postgraduate diploma in Business Management.
Urs Nietlispach has headed the Wayside Train Monitoring Systems (WTMS) business area of Swiss Federal Railways (SBB AG) since 2006. A key achievement of his leadership has been the development of WTMS on many levels of the Swiss network. This includes the steady expansion of the existing network with additional hot axle box detectors and wheel-locking detection systems, the development and implementation of new devices such as wheel-load checkpoints, fireand chemical-detecting systems as well as loading gauge and aerial detection systems – plus the consistent interlinking of the various systems. The focus is on a comprehensive network of measuring systems for monitoring significant, physical rail-traffic parameters on the SBB network in real-time. This system has contributed greatly to the safety of rail operations and to improved availability of train paths in Switzerland. Urs has an engineering degree in electronics and software development from the Lucerne University of Applied Science and Arts and has added an Executive Master of Business Administration to his basic technical training. Urs came to SBB in 2005 after extensive experience in building management systems, product development and manage – ment. In SBB AG’s former Rail Automation business unit, Urs took over the management of the Wayside Train Monitoring Systems area in early 2006 with 16 employees and annual sales of approximately CHF 12 million.