Building tomorrow’s rolling stock with NEXTGEAR
Posted: 10 August 2021 | Jose Bertolin | No comments yet
Jose Bertolin, a UNIFE Technical Affairs Manager, provides an insight into the work of the NEXTGEAR project and how next generation running gear technology could drive more competitive, efficient and green European rail.
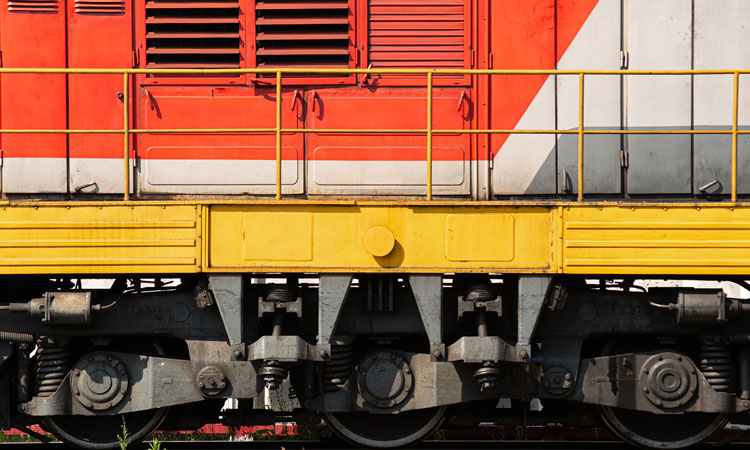
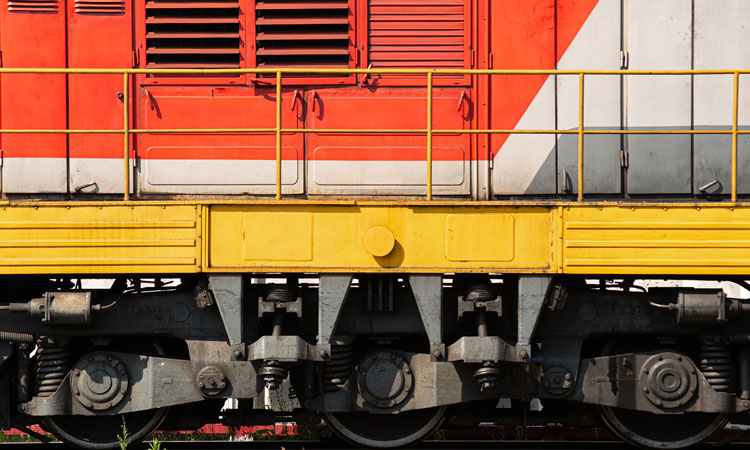
It is no coincidence that 2021 has been designated as the ‘European Year of Rail’. Given the ecological devastation generated by the Australian wildfires that concluded 2019 and then ushered in a year that would soon be defined by a pandemic without precedence in living memory, Europe and the world are aware of the impetus to build new systems that confront the dual climate and public health crises. Rail, the cleanest mode of mass transportation and one that has proven critical to providing essential goods and personnel, is one such system. However, to deliver on the European Union (EU) Green Deal’s ambitious goals, such as the decarbonisation of transportation and carbon neutrality by 2050, we must now begin to develop technologies capable of delivering a green transition. Through the Shift2Rail Joint Undertaking (S2R JU) – led by its Executive Director, Carlo Borghini – the sector’s institutionalised partnership, NEXTGEAR (NEXT generation methods, concepts and solutions for the design of robust and sustainable running GEAR) is working to develop next generation running gear fit for future European trains that align with the aforementioned ambitions.
When the European Commission (EC) proposed S2R JU’s successor – Europe’s Rail Joint Undertaking – and nine other institutionalised partnerships in February 2021, the European Transport Commissioner, Adina Vălean, stated that: “To make our ambitions come true, we need to develop disruptive technologies bringing zero‑emission vessels and aircraft to the market; we need to develop and deploy cooperative, connected and automated mobility; and we need to enable more efficient and modern traffic management.”
NEXTGEAR is a 27-month project within S2R’s first Innovation Programme (IP1) that seeks to do just that by making rail more attractive and competitive. After starting in December 2019, the project is contributing to the development of new generation running gear that generates substantial reductions in lifecycle costs, improves reliability and increases energy efficiency. NEXTGEAR’s overarching mission is the identification, development and evaluation of key methods and concepts for high performance railway vehicle running gear systems, including wheelsets using novel materials and manufacturing methods; the development of a high safety integrity level controller for active running gear; and, last but not least, a lifecycle cost analysis tool to support the business cases needed for the adoption of these novel technologies.
The outcomes generated by this UNIFE‑coordinated, 16-partner consortium seek to also reduce noise emissions and other externalities whilst enabling full rolling stock interoperability. By doing so, it is providing the cost-effective, green transport solutions needed to position rail as the backbone of tomorrow’s sustainable mobility paradigm.
The project aims to make a marked step change towards this essential rail component. To achieve the development of a new generation of running gear, NEXTGEAR is working on three main elements. The first is building upon the Universal Cost Model (UCM) created by the Shift2Rail Lighthouse project, which sought to “remove already identified blocking points for radical innovation in the field of railway vehicles”, Roll2Rail. The UCM designed by this earlier project seeks to quantify the system-wide influences of technical innovations in running gear design, such as new materials to reduce weight or active suspension to reduce track deterioration. ‘UCM 2.0’ will help to bridge the gap between UCM users and technical developers by focusing on usercentered interface and robustness. It will include a complete set of cost calculation and modelling techniques for different performance indicators, such as track settlement, damage in switches and crossings, noise impact and the addition of CO2 emissions to the final cost calculation, all while improving the user‑friendliness of the UCM tool and technical models. Furthering the usage and acceptance of the UCM in the railway sector will make it possible to judge the economic impact of innovations for both the operators that adopt them and the infrastructure owners were these run, first and foremost for NEXTGEAR innovations, but also for future Shift2Rail projects.
Concurrently, the consortium is also suggesting new ideas for the Running Gear Technology Demonstrator (TD1.4). These will be based both on the use of new applications of materials and new manufacturing methods. Thirdly, NEXTGEAR is designing the wheelset of the future by proposing a concept for a hybrid carbon fibre/ metallic design that enables substantial reduction of un-sprung masses without compromising safety. Completing these objectives is intended to create new ways to design trains that are more reliable, lighter and less damaging to the track. The consortium hopes, as well, that these designs will be more comfortable, less noisy and incur lower lifecycle costs.
However, all work starts somewhere. In its first year, between 2019 and 2020, our project contributed to the earlier discussed TD1.4 through the selection, design and manufacture of two running gear sample components using novel materials and emerging manufacturing methods. An aerial bracket for a metro vehicle was manufactured using an additive manufacturing technique, obtaining a 60 per cent of weight reduction. In 2021, a carbon fibre composite frame for a single axle running gear for a two-axle metro vehicle including a novel longitudinal actuator with internal spring will be manufactured. Additionally, we have designed a high safety integrity level (SIL4) controller that has been manufactured and initially tested based on a systematic study of active suspension systems. This was carried out to identify key requirements for an active suspension controller.
NEXTGEAR has also, through another workstream, been investigating the feasibility of different materials and designs for the construction of a hybrid metallic-composite (HMC) wheelset. Three concepts for an innovative composite axle to replace the benchmark steel axle were defined based on a set of criteria established for the definition of feasible technological solutions. The consortium’s partner concluded that ‘Concept 3’ (seen in Figure 1) was the most suitable prototype for further exploration because of the larger mass savings it enables, but, also, its adhesives demonstrated substantially less stresses.
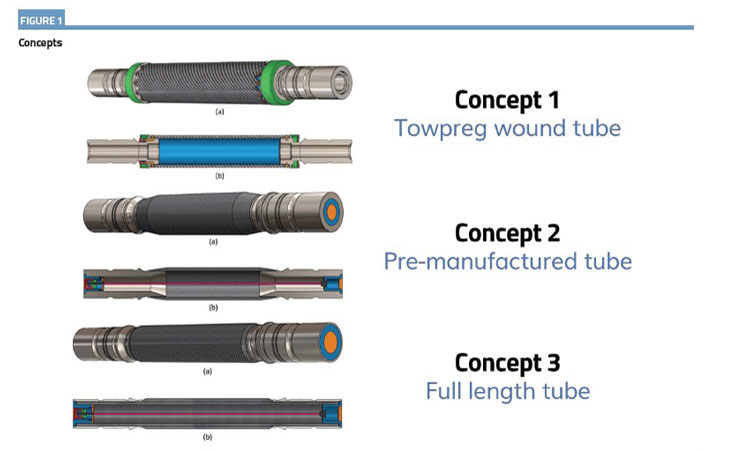
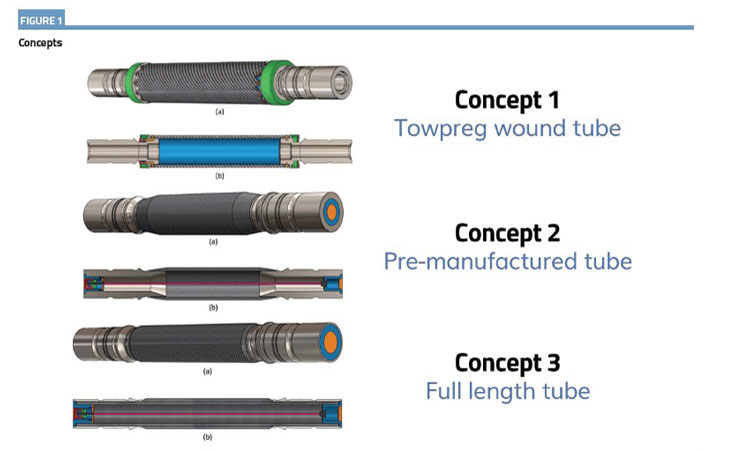
NEXTGEAR has been investigating the feasibility of different materials and designs for the construction of a hybrid metallic-composite (HMC) wheelset.
‘Concept 3’ was established as the most suitable prototype for further exploration because of the larger mass savings it enables, but also its adhesives demonstrated substantially less stresses.
During the European Year of Rail, NEXTGEAR – and other similar research and innovation projects – will continue building towards tomorrow’s next generation rail solutions. We work on making European rolling stock more reliable and less cost intensive. By doing so, we hope to make rail even more comfortable and less noisy for an optimal transportation experience. Achieving these goals is essential to ushering in a future mobility system that leverages rail at its backbone and serves as an engine for a just, digital and green transition.
Issue
Related topics
Bogies & Wheelsets, Rolling Stock Components (Interior/Exterior), Rolling Stock Maintenance, Sustainability/Decarbonisation, Technology & Software