How can design of wheelsets improve future rolling stock performance?
Posted: 10 September 2016 | Marcel Ujfaluši (ERWA) | No comments yet
Marcel Ujfaluši – Chairman of the Development Committee of ERWA, the UNIFE Railway Wheelset Committee – highlights the importance of wheelset development for both rail freight and passenger vehicles and includes some informative case studies from ERWA members who are all committed to enhancing their products and services.
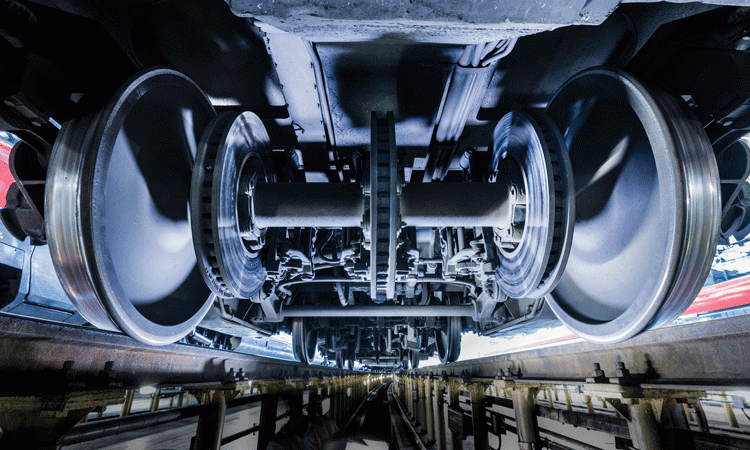
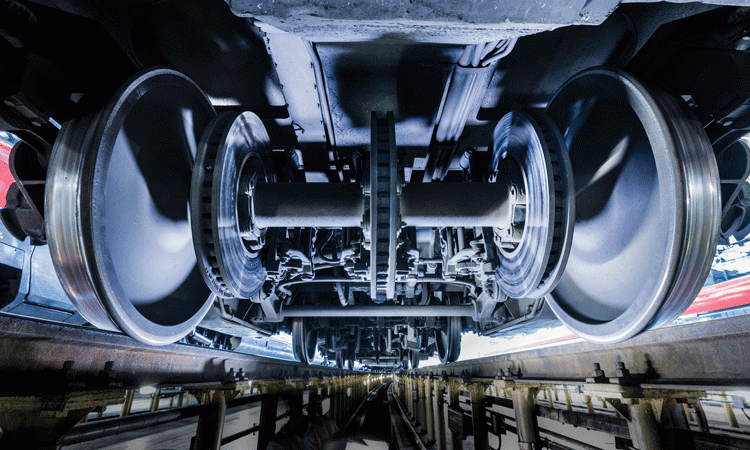
Wheelsets with noise absorber panels assembled on an ETR1000 bogie. Credit: Lucchini RS Group
Since the creation of the first railway the efficiency of wheel/rail interference defined the competitive advantage of railways in moving passengers and freight worldwide. Development of rail-bound transportation, from horse-driven carriages, through the steam era to modern heavy haul and high-speed trains, has always been closely connected to the development of the wheel/rail interaction in terms of the best possible transition of engine power to move the train without compromising the quality of the wheel and wheelset itself. Therefore, development of the wheelset either precedes – or goes hand-in-hand – with the development of railway transportation and directly affects all its efforts, such as the aim for higher loads, higher speeds, lower noise emissions, sustainability and eco-friendly solutions (related to CO2 creation per ton/passenger).
European manufacturers within ERWA (European Railway Wheelset Association) contribute to this evolution by developing, designing and manufacturing wheelsets used for all modes of rail transport worldwide. Its members are:
- Bochumer Verein Verkehrstechnik (BVV)
- CAF MiiRA
- GHH-BONATRANS (namely BONATRANS and GHH-RADSATZ),
- Lucchini RS Group (namely Lucchini RS, Lucchini Unipart Rail, Lucchini Sweden and Lucchini Poland),
- MG-VALDUNES.
ERWA wheelsets are currently used every day in revenue service under varying conditions that range from the mountainous regions of Switzerland; the tunnel under The English Channel and the highly urban area of the American Northeast; to the scenic landscape of China; the tough countryside in Scandinavia and the desert conditions of Maghreb and Saudi Arabia.
Why do ERWA wheelsets dominate this industry and how are they able to serve railways and their customers in such different conditions? The following are a few examples of how the members contribute to the development of this state-of-the art technology.
Bochumer Verein Verkehrstechnik (BVV)
Gauge changing wheelset
Hardly any rail vehicle is comparable to the other. In many cases, special requirements are to be taken into consideration. Due to the broad experience in wheelset technology, BVV has developed tailor-made solutions for passenger and freight transport. The objectives of these developments were, for example, the increase of the wear resistance by introduction of improved or newly developed steel grades, reduction in weight of wheelset components and reduction of noise emissions.
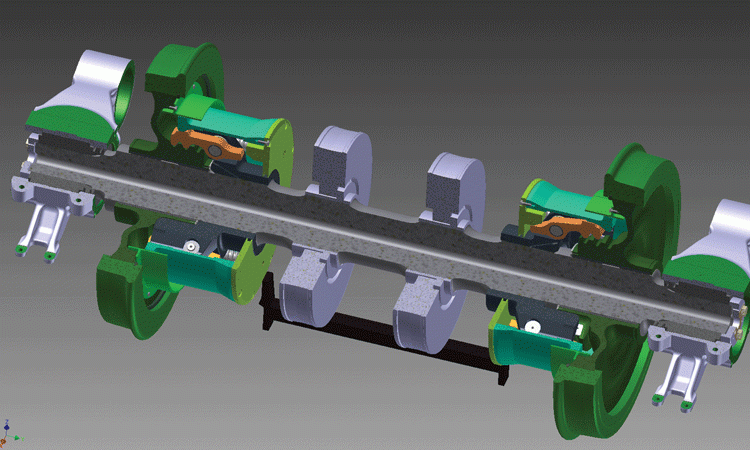
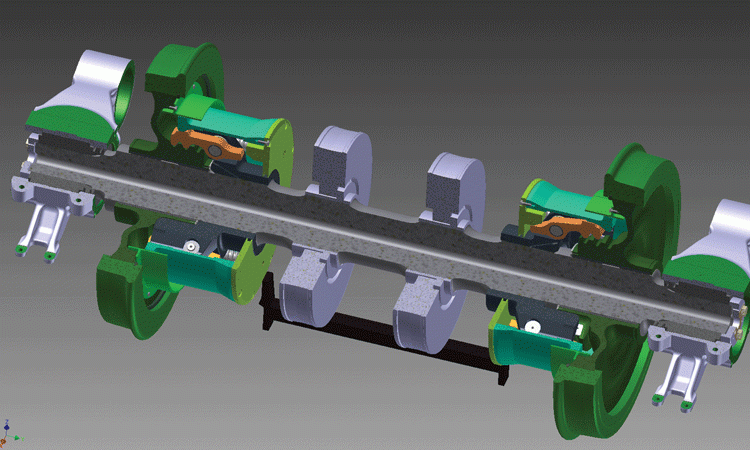
3D model of gauge changing wheel set completed with brake discs and bearings. Credit: Bochumer Verein Verkehrstechnik
Another aspect for the development of improved and specialised wheelsets is to improve the comfort of the ride for passengers. A recently developed solution to this is the updated version of its gauge changing wheelset. With this update BVV found a way to increase passenger comfort and significantly reduce travel time. Passenger coaches travelling between two areas with different track gauges will be equipped with automatic gauge changing wheelsets where unlocking, gauge changing and safe relocking of the wheelsets is performed fully automatically while passing an automatic changeover rail. The functionality is given without having to unload the wheelsets. Special focus during the design improvement process has been given to measures for improved wear resistance of locking mechanism parts. Without the need to change gauge width, the bogies can be equipped with standard single gauge wheelsets. Wheelsets of this design will be introduced for passenger coaches built by Stadler and will be operated between Azerbaijan and Turkey.
CAF MiiRA
Different railway vehicles are subjected to very diverse operational conditions. As expected, the requirements will be very different in a passenger vehicle operating through the desert in Saudi Arabia to that of a freight wagon that is subjected to extreme braking loads, for example.
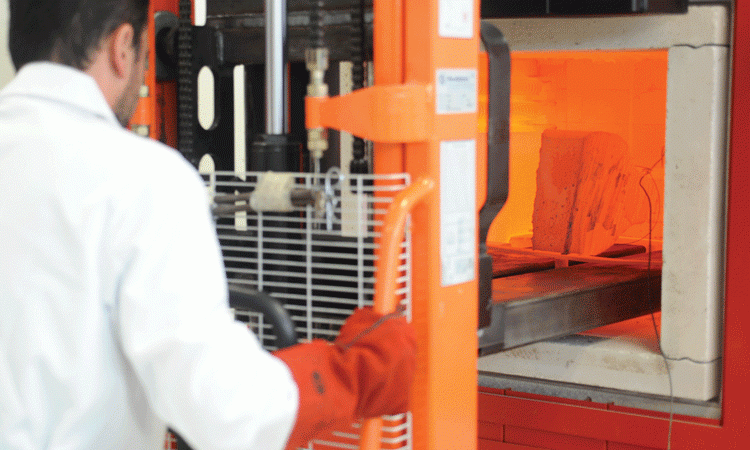
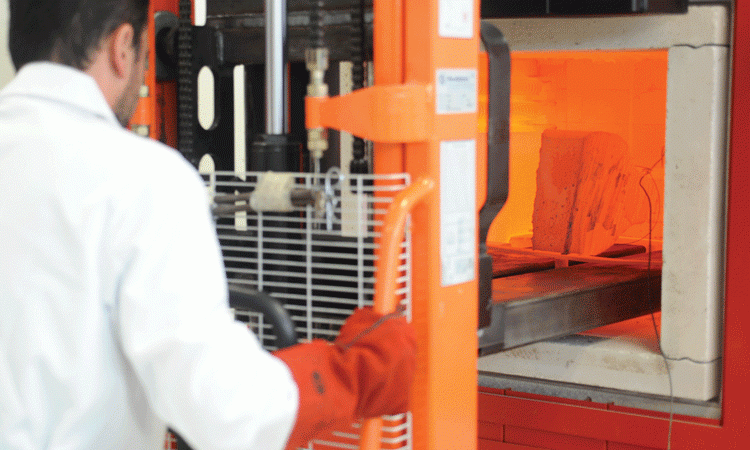
Pre-shaping heat treatment. Credit: CAF MiiRA
This fact represents a continuous challenge for the development of improved material grades specifically suited for each particular vehicle and its service conditions. In the case of the wheels, the challenge is especially severe because the service conditions produce enormous direct changes over the theoretical or expected final wheel life.
CAF MiiRA have a broad experience as producers of wheels for the most extreme environments. In close cooperation with their customers, CAF MiiRA have developed specific material grades that have allowed important improvements in total service life and safety.
Wheels for wagons working in harsh operation conditions
Very often freight operations can mean extremely long braking cycles that provoke the development of a dense network of thermal cracks on the centre of the wheel treads (thermal fatigue). This fact represents a drastic reduction of wheel life and a very significant increase in maintenance costs. A special alloy, fitting the requirements of the ER7 grade under EN16262 standard, was developed by CAF MiiRA. The wheels have been working in problematic fleets in service and have been closely monitored for over two years. The inspections carried out have revealed a significantly lower thermal fatigue damage of the tread, thus decreasing the re-profiling needs. This, of course, means that the life expectancy of the wheels will be greatly improved, with a higher level of safety in service.
Wheels for abrasive environments
CAF MiiRA have, for several years, supplied railway wheels for operating in dessert environments for both passenger vehicles (manufactured by CAF) and freight vehicles. The extremely abrasive environments of these areas (trains must literally plough through sand dunes) provoke dramatic wear in the wheels, thus reducing the wheel life down to a fraction of the conventional expected values. Following extensive research, including several on-site stays, CAF MiiRA introduced a family of high hardness abrasive resistant alloys known as ‘CAF-Sand’. After more than four years’ experience in service, the assembly of these new wheels has shown an average improvement of the wheel life by more than 20% resulting in a huge impact in the overall maintenance costs of the vehicles.
GHH-BONATRANS
GHH-BONATRANS pays close attention to the issue of noise. Their Research and Development Department has developed a number of solutions to reduce noise caused by rail-bound wheel operation. Specially developed noise absorbers mounted on the wheels is one such approach to achieve a reduction of the vibration (and thus also noise) of wheels in operation. The noise absorbers are able to achieve absorption of the rolling noise by up to 5 dB(A), while the most unpleasant squealing noise of wheels equipped with GHH-BONATRANS noise absorbers is up to 30 dB(A) lower than that of wheels without absorbers, especially in the significant frequency bands. Complete systems are specifically designed for different market segments such as urban, suburban and mainline passenger transportation, high-speed and very high-speed trains. Recently the demand for such solutions is also being made for freight transport.
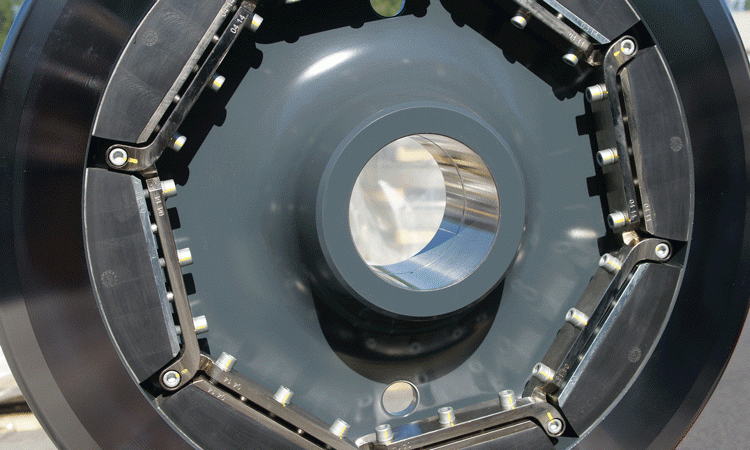
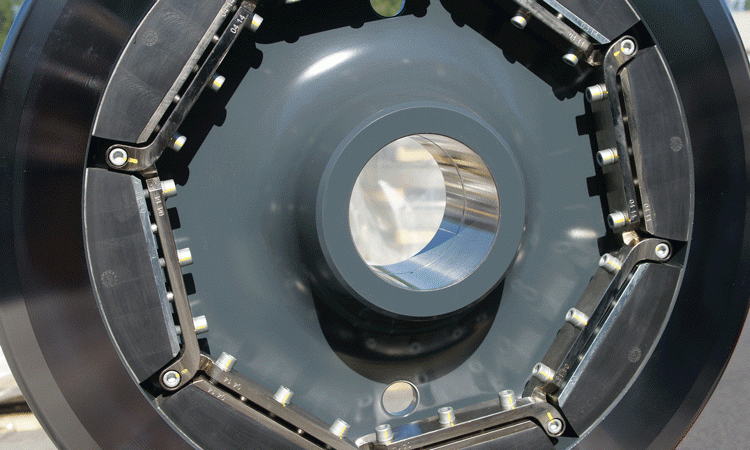
Detail of dynamic noise absorbers on monobloc wheel. Credit: BONATRANS
BONASILENCE® is a family of dynamic noise absorbing systems developed and being diversified by GHH-BONATRANS. The most recent example can be found in the new metro cars for Berliner Verkehrsbetriebe (BVG) supplied by Stadler. Driving and standard wheelsets are equipped with multi-segmented dampers, mounted on the wheels, which are able to reduce the wheel rolling noise by 10 dB compared to standard wheels. The dampers also significantly reduce squealing noise and their expected lifespan is minimum 15 years. The analogical damper can be designed to fit any wheel diameter.
GHHULTRA-S® is a newly developed super-resilient wheel designed for 12.5 tonne axle loads and meets all requirements for a resilient wheel with tread diameter of 600mm new / 520mm worn and secures low radial stiffness (20-40kN/mm). The design of all components has been enhanced and the rubber elements have been completely reshaped. The excellent strength was achieved by applying the German quality standards (FEM analysis and assessment of stresses by application of FKM-guideline).
Independent wheel axles
The technology was introduced in Europe more than 30 years ago and, nowadays, nearly all tenders for new trams and light-rail vehicles worldwide call for low-floor vehicles. These vehicles need to be designed for high capacity transport. The new 12.5 tonne independent wheel axle is based on the proven and reliable GHHV60® wheel type. Its modern upgrade for high axle loads is based on a one-piece, die-forged portal axle design and a pair of tapered roller bearings, adjusted optimally during assembly. The wheel diameter is increased to cover the higher axle load requirement. Portal axles for both type 1 (inner distances of wheels from 1,355mm to 1,392mm) and type 2 (from 1,380mm and above) applications can be supplied. Last but not least, rubber components of resilient wheels with modified compound fulfil the Fire Protection properties of EN 45545.
Lucchini RS Group
High-speed and low noise
Travelling by train is becoming an ‘experience’ and not just a transport solution for a single passenger. Improving the transportation pleasure linked to this experience is one of the goals of modern railways, focusing on customer satisfaction and supported by top level technologies. In September 2010 the Italian railway operator Trenitalia ordered 50 ETR1000/V300ZEFIRO trainsets (400 cars) – an ultra-modern train that combines the segment’s highest capacity with pioneering levels of passenger comfort, thanks to sophisticated aerodynamics, interior design, energy-saving technologies and outstanding high-speed performance, safety and noise reduction.
Lucchini RS was involved by the system integrator from the design stage to manufacture wheelsets that could meet the railway operator’s ambitious targets, thanks to the application of Syope® – a solution to reduce the noise generated by the wheel/rail rolling contact dynamics. Lucchini RS started developing low noise Syope wheels in the mid-1990s and the product is now applied on several rolling stock typologies. The solution is based on a multi-layer panel composed of special polymers with damping properties that dissipate the vibrational energy responsible for noise emission. The panel is applied to the web of the wheels, by means of special solutions, and becomes an undistinguishable part of the monobloc wheel itself, achieving noise reduction ‘at the source’. Zefiro wheelsets also utilise Lursak® – the latest generation axle-protection system conforming EN13261 Class 1 standards, anti-ballast proven, developed from aerospace technology with AkzoNobel® and based on composite materials.
Improved wheel steel
One way of enhancing rolling stock performance is to improve the wheel steel. Lucchini Unipart Rail has been successful in introducing parent company Lucchini RS’ improved wheel steel, called Superlos®, over the past decade into the UK, and now several train fleets have these as standard. One of these is Coradia Class 175, whose diesel multiple units of 2-car and 3-car sets have a top speed of 100mph and were manufactured by Alstom in the UK between 1999 and 2001. Standard R8T wheels were being re-profiled at approximately 75,000 miles due to Rolling Contact Fatigue (RCF). The total life of the wheel was approximately 500,000 miles which meant the life of the wheels was much shorter than that of the bearings and brake discs.
Initially four trains (2 x 2-car and 2 x 3-car) were fitted with Superlos® wheels and monitored during 2006. They achieved in excess of 250,000 miles between tyre turns and no RCF was recorded on the wheels. The wheels were re-profiled to reinstate the P8 profile, even though the flange height and width were within the operating limits, as specified in the Railway Group Standards for the UK. Due to the success of the trial the entire fleet of Class 175 trains (11 x 2-car trains and 16 x 3-car trains) has for the last 10 years been fitted with Superlos®. The wheels are re-profiled after approximately 230,000 miles to bring the life of the wheel in line with the bearings and brake discs. They have an expected life in excess of one million miles.
MG-VALDUNES
Heavy-haul applications
MG-VALDUNES proposes wheel design optimisation and steel grade improvements for heavy-haul applications for iron ore transportation. Developments have been made in Australia, Canada, South Africa and also Europe, to improve wheelset performance. Wheel designs that are able to support 50 tonnes per axle have been proposed using European standard calculation rules and American AAR practices. Some improvements are still required for such service load: the potential of forged wheels has been demonstrated for this extreme application. Design optimisation is also coupled with steel grades using micro-alloyed additions. Follow-up and tests have demonstrated a benefit of up to 15% on heavy-haul wheel mileage in Norse conditions.
All aforementioned examples prove that ERWA members are committed to the development of an eco-friendly and sustainable mode of transport. The fruits of current R&D efforts, built on the experience of more than 200 years of development, design, manufacture and caring about the life-cycle of wheelsets, are evident in applications for all loads and speeds the world over.
Main targets for near future?
The main goals for the near future – which are those specified by customers – include further enhancing the life-cycle of wheels, adapting to different worldwide standards and conditions and focusing on noise reduction.
Issue
Related topics
Related organisations
Bochumer Verein Verkehrstechnik (BVV), CAF MiiRA, GHH-BONATRANS, Lucchini RS Group, MG-VALDUNES