NGT LINK: A double-deck concept for rapid inter-regional transportation
Posted: 15 September 2015 | David Krüger, Joachim Winter | No comments yet
With the aim of making tomorrow’s trains faster, more comfortable and more efficient, the Next Generation Train (NGT) research project has now entered its third phase. This family of cutting-edge train concepts has been under ongoing development since 2007, with the ultra-high-speed NGT HST (formerly NGT HGV) leading the way since the project’s inception. With the beginning of the second phase of the NGT project in 2011, a new concept joined the family: NGT LINK. Here, the German Aerospace Center’s Joachim Winter, Project Manager and David Krüger, Research Associate, give an overview on aspects ranging from propulsion and power supply to aerodynamics and passenger flow.
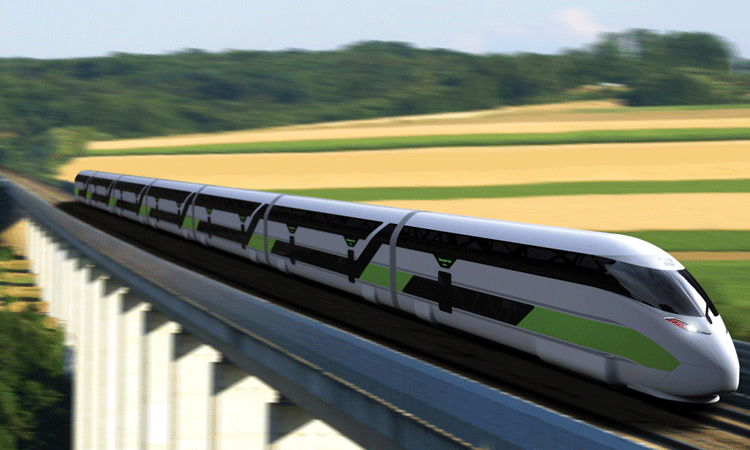
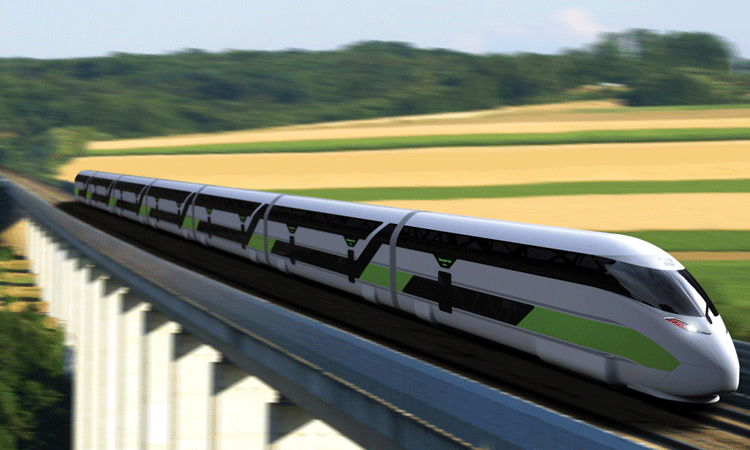
NGT LINK (above rendering pictured) is a high-speed feeder train which is designed to complement the service offered by NGT HST. While the ultra-high-speed NGT HST stops at major cities and covers international long-distance routes at a top speed of 400km/h, NGT LINK serves the surrounding medium-sized cities at 230km/h and feeds travellers to the NGT HST service.
Like NGT HST, NGT LINK is a double-decker train which combines many of the technologies that future railways will need in order to keep pace with society’s evolving needs. However, whereas NGT HST is designed from a blank sheet with new, purpose-built infrastructure in mind, NGT LINK is designed to make use of the technology developed for NGT HST while maintaining compatibility with existing infrastructure. For instance, this means that where NGT HST maximises space and minimises dwell times by having passengers board and disembark on both levels simultaneously, NGT LINK is equipped with stairs, allowing it to stop at conventional stations lacking the Next Generation Station’s bi-level platforms.
Among the marquee technologies fitted to NGT LINK are its lightweight car bodies and its flexible hybrid power supply system. Supporting these technologies is a raft of subtle details that together comprise a complete package for fast, efficient and comfortable inter-city and inter-regional transportation. According to simulations, NGT LINK has achieved the goal of using only half the per-capita energy of its reference train, the German ICE TD. The lightweight car bodies and the hybrid powertrain are helped here by an efficient seating plan and the cars’ double-deck design.
NGT LINK’s car bodies are designed to marry lightweight design with ease of assembly and manufacturing. Especially for trains with shorter distances between stops, mass reduction is one means of significantly reducing energy consumption, so the concept employs a dedicated lightweight design strategy for all structural components of the body shell. For the body, a method developed at the DLR’s department of Lightweight and Hybrid Design Methods was applied to ensure the lightest possible design. After determination of the basic dimensions of the car body, such as length, width, wheelbase and door placement, the geometry is put through a topology optimisation, which produces a numerically optimised, load-path oriented structure based on the relevant loads such as weight, payload and maximum static loads according to EN 12663. The mechanical design of the NGT LINK aluminum space frame, the shape of which is derived from the preceding optimisation, ensures that the parts count is kept as low as possible while still adhering to the results of the optimisation. The car body consists of an aluminium frame built out of CNC-bent round tubes and CNC-laser-cut rectangular profiles, with a load-bearing outer skin of aluminium sandwich panels with polymer foam cores. The tubes and profiles are cut and bent in a way which allows both to be continuous through intersections with each other, resulting in a lightweight construction similar to a differential design but with fewer parts.
Designed to operate on existing lower capacity lines
Because NGT LINK is designed to operate on existing lower capacity lines, it needs to be compatible with a wide range of current infrastructure. The reference route chosen for the evaluation of the concept leads from Stuttgart over Ulm to Oberstdorf, on the edge of the Alps in the south of Germany. This route is only electrified from Stuttgart to Ulm, so in order to travel the entire length of the route NGT LINK requires a trivalent hybrid drivetrain. On conventionally electrified lines, NGT LINK extends its asymmetrical, telescoping current collector, while on NGT HST routes it can pick-up energy wirelessly like the NGT HST. On non-electrified routes, NGT LINK can draw power from its on-board batteries.
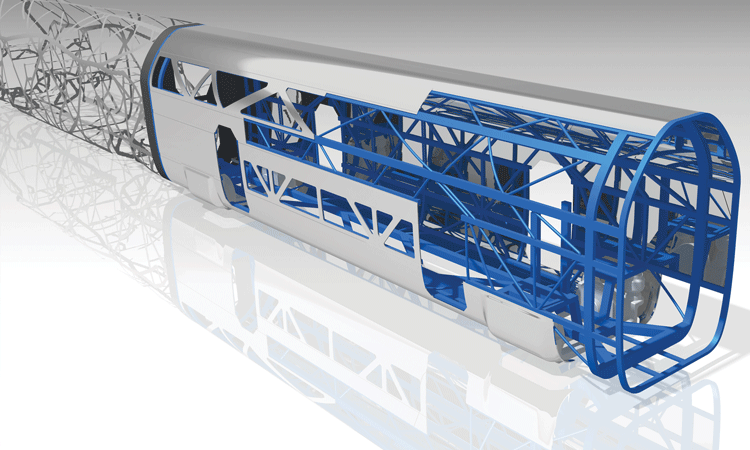
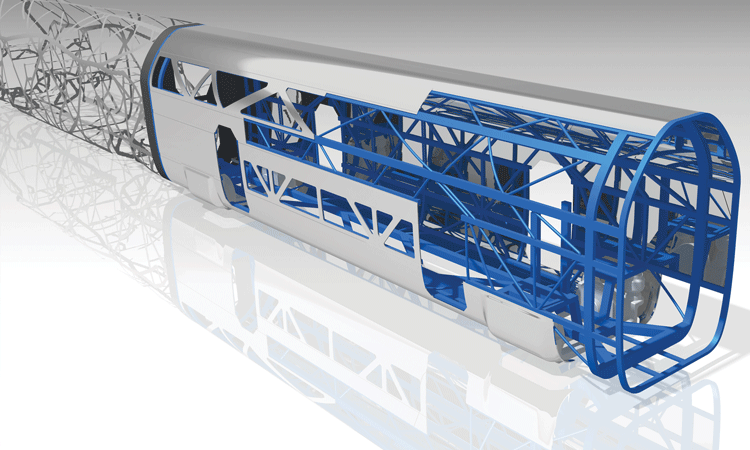
Figure 1: The aluminium space frame construction of an NGT LINK car. The topology optimisation
model, from which the mechanical structure is derived, is visible in the background, top left.
The wireless power supply is a technology shared with NGT HST and functions on the basis of inductive power transmission. In this system, primary coils mounted between the rails send energy to the secondary coils mounted in the belly of the train. This sophisticated system precisely locates the train and only energises coils as the train passes over them, ensuring safety and minimising energy losses. This system is, in essence, similar to those used for wirelessly charging cars and by some inductively powered streetcars. The demands placed upon it are, however, more rigorous due to the requirements for railway vehicles with the corresponding power demand. It needs to function through a wide range of conditions, since the train is not only moving past the primary coils at anything up to 230km/h, but the distance from the belly of the train to the track surface can vary from 80mm to almost 300mm – based on wheel wear and suspension travel. In addition, the system must be capable of transmitting over 3MW continuously in order to power NGT LINK and its systems. The benefits of the system are not limited to the elimination of wear; with no pantograph exposed to the wind, NGT LINK has removed a significant source of noise, giving it the potential to be quieter than comparable, conventionally electrified trains. Wind tunnel tests1 on the pantograph used on the German ICE 1 showed an aerodynamic drag amounting to 126kW at 250km/h; wireless power transmission completely avoids this, resulting in further energy savings. With no moving or wearing parts and no vulnerable catenary, the availability of the wireless power system is also expected to be significantly better than conventional designs, and communications signals can also be piggybacked on the power system, providing an additional mode of communication and train control.
Save space and reduce noise
Much like the current collector used on the 500 Series Shinkansen, NGT LINK’s current collector telescopes vertically in order to save space and reduce noise. However, its unique asymmetrical design derives from the need for it to be installed in the double-deck area of a car without imposing on the upper centre aisle or exceeding the G2 loading gauge. When not in use, the NGT LINK current collector telescopes down into its ready position, then swivels 90 degrees until the pan is parallel to the length of the car. It can then be lowered further into its storage bay next to the aisle on the upper floor. Storage bay doors then close over the current collector, restoring the smooth outer skin of the train and preventing noise, which conventional pantographs produce – even when not in use. The strut and pan of the NGT LINK current collector have elliptical cross-sections and surface features which are designed to trip the boundary layer in order to reduce noise and drag.
In addition to the wireless power supply and the asymmetrical current collector, a series of batteries allow NGT LINK to run on non-electrified lines such as what exists on the way from Ulm to Oberstdorf. This uphill route covers a distance of 127km, necessitating almost 900kWh of energy for a fast driving style2. This translates to 19.8 tonnes of lithium-based batteries, assuming a conservative state of charge strategy. These are distributed throughout the train, with nine tonnes in each end car and a further 360kg in all others. Concentrating the battery mass in the end cars renders these less susceptible to crosswinds, while batteries in the middle cars aid the scalability of the train in cases where cars are either added to or removed from the formation. Ongoing research is looking into reducing the battery mass by charging at stations on otherwise non-electrified lines, as well as on stretches with high power demand such as hills and sections where trains accelerate.
With each car possessing its own on-board power supply, all cars can also shunt themselves instead of requiring external traction, and the batteries allow NGT LINK to recuperate its kinetic energy when running on non-electrified lines. Indeed, even on electrified lines there are advantages to storing recuperated energy on-board, since this circumvents both efficiency losses in transmission and the costs due to low compensation for energy returned to the grid.
NGT LINK has a series of motors driving each one of its 32 wheels independently, providing a total tractive power of 2.5MW. This electrical power, plus the additional approximately 20% required for ancillary components3, is drawn from one of the three sources listed previously. NGT LINK is designed for high flexibility; equipped with the appropriate power electronics and with these three power sources to choose from, NGT LINK can be used on virtually all G2 compatible routes.
Trains today are increasingly confronted with a world in which resources are becoming scarcer, strict emissions regulations are constantly tightening, and expectations of mobility and comfort are continually increasing. To maintain a competitive edge over other modes of transportation and to provide responsible, attractive mobility to as many people as possible, trains will need to adapt in ways that require a complete rethinking of many aspects that are taken for granted today. NGT LINK aims to unify bold applications of diverse technologies and unconventional ideas in order to make travel faster and more comfortable – all while setting new standards for energy efficiency and emissions.
References
- Bartels; W. Herbert: Hochgeschwindigkeits-Stromabnehmer für den ICE, Elektrische Bahnen, Issue 11, 1991
- Kaimer, S. Streit and J. Winter, High-Speed Passenger Train NGT Link – Propulsion- and Electrical Power Supply Concept, Civil-Comp Press & Saxe-Coburg Publications, 2014
- Nolte; F. Würtenberger: Event – Evaluation of Energy Efficiency Technologies for Rolling Stock and Train Operations of Railways, Berlin: UIC, 2003