LiTheS: CAF MiiRA’s innovative Light Thermo Stable wheel for rail freight
Posted: 6 June 2019 | CAF MiiRA | No comments yet
CAF MiiRA has been carrying out research that investigates the optimisation of low stress wheels for rail freight traffic, and the result is an innovative treadbraked wheel that will bring competition to future market needs.
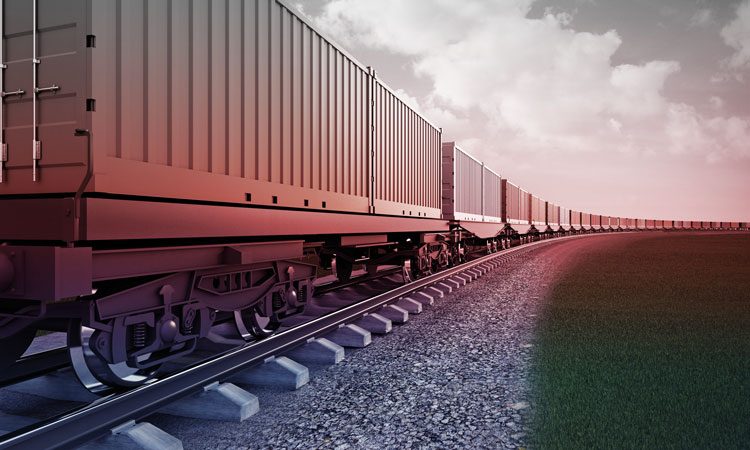
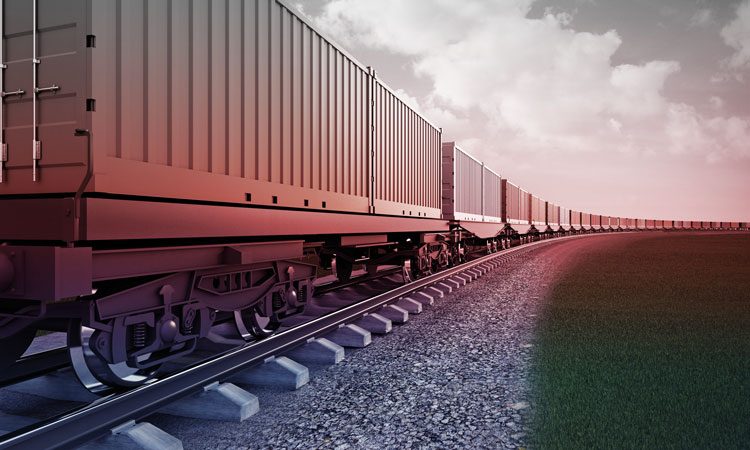
TREAD-BRAKED wheels have been used since the very beginning of railway traffic. UIC 510-51 defines the acceptable requirements for a tread-braked wheel suitable for European traffic. These requirements correspond to the very hard braking conditions of the South slope of the St. Gotthardt Pass in Switzerland, assuming a drag braking downhill, where a constant velocity of 60km/h must be constantly maintained for 45 minutes. This situation induces a thermal load corresponding to 50kW2 at the contact surface between brake block and wheel tread and can generate high stresses in the rim. Special wheel designs are developed to keep these values within the standard limits. In order to be able to resist these stresses, as well as to keep lateral displacements of the rim within certain limits that respect the required gauge, tread-braked wheels must have a special rim shape that keeps stresses and displacements as low as possible. Therefore, these kinds of wheels are usually referred to as ‘low stress wheels’.
It has been proven over the years that only a web with a curved shape will be able to satisfy the tough European requirements. Wheels with a double or triple curvature of the web have been proposed for this purpose, with the latter showing a better behaviour in terms of lateral displacement of the rim. As a result, these wheels tend to be heavier and louder than usual wheels with straight web because of the curved shape. In addition to this, freight wheels must resist the highest axle loads accepted in Europe – up to 25 t per axle. It would therefore be desirable to make available a tread-braked railway wheel for freight that effectively shows mass and noise emission figures, comparable to those of the wheels with straight web, without penalising the mechanical or the thermomechanical behaviour required by the current standards. The most competitive solution will be the one that fulfils the standard requirements while keeping the mass and noise emission to a minimum. Additionally, it has been identified that an increasing interest in the use of tread-brakes for passenger traffic, so developing low-mass and low-noise tread-braked wheels will have a positive impact also for the passenger business.
An innovative solution
Aware of these challenges, CAF MiiRA has been carrying out research to focus on the optimisation of low stress wheels. As a result, the new Light Thermo Stable wheel (LiTheS) has been released. This is an innovative tread-braked wheel for freight that aims to replace some of the existing wheels in the market, such as the BA004, with a competitive wheel that fosters the future market needs. It combines traditional knowledge on this group of railway wheels, as well as the most recent approaches for lightweight design of mechanical parts (including ISO 178493) and a considerable amount of research in material and acoustics.
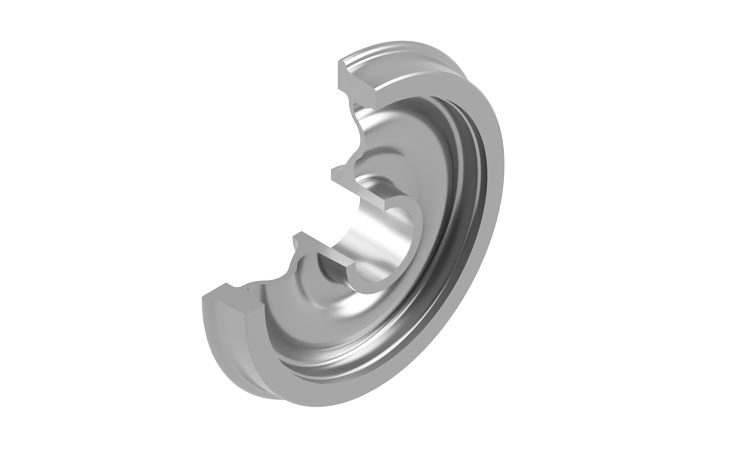
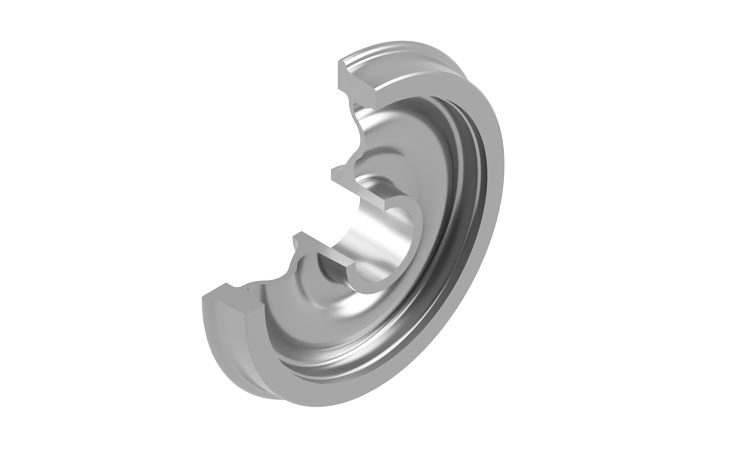
Three-quarter representation of the innovative LiTheS wheel
Material investigations address the problem of defining an improved thermomechanical model for the simulation of the test bench conditions. For this purpose, a new plasticity model has been developed, together with the right combination of all other mechanical and thermomechanical material properties and the election of the adequate heat transfer coefficients. This results in a new and more accurate model for the calculation of drag braking tests, according to EN 13979-14, that allows for more optimised wheel designs. Test results for this wheel showed stress and displacement values extremely close to the predicted ones.
This new thermomechanical model will be introduced by CAF MiiRA at the International Wheelset Congress 2019 in Venice.
However, it is not only research that has been carried out in terms of mechanical simulation. An acoustic optimisation of the wheel has also been performed with the CAF-developed software ‘CRoNoS’, validated with TWINS, which includes extra features for a more reliable approach, with the inclusion of the complete wheelset, instead of a single wheel5.
Apart from the different innovations that combine design and simulations, CAF MiiRA has also developed a modification of the ER7 steel grade in order to improve the thermal behaviour of the wheel material. This material, named ‘COMPOPAD PROVEN’, is the result of a tuned alloy composition and optimised heat treatment.
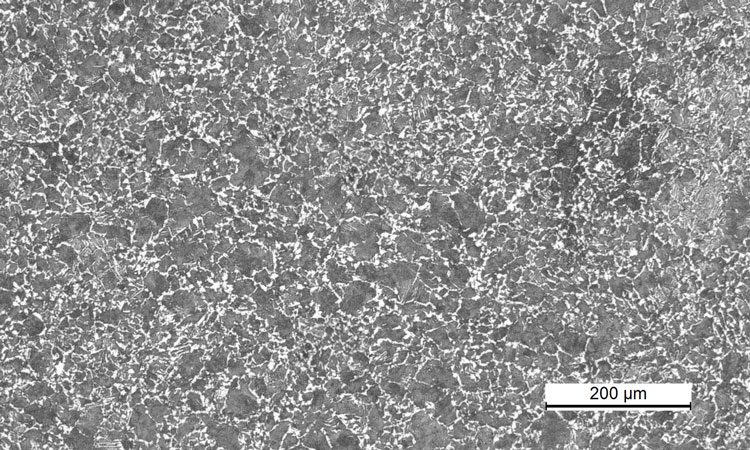
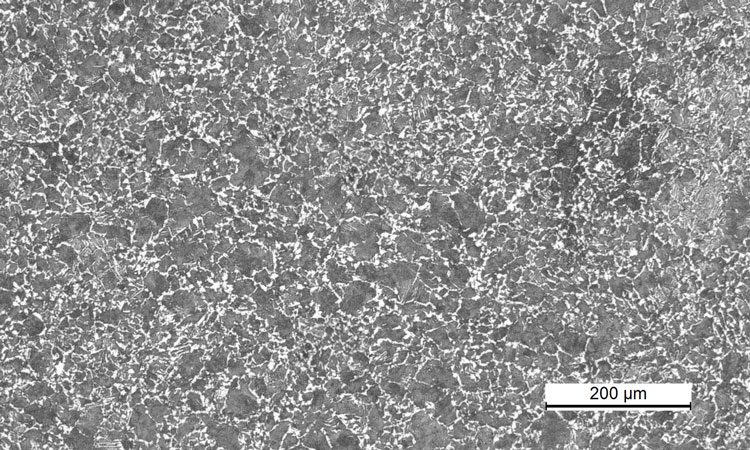
‘COMPOPAD PROVEN’ microstructure
The use of composite brake blocks increases wheel wear and tread temperature during braking when compared to the use of traditional cast iron brake blocks. Even if a higher wear rate, damage of the rolling contact surface due to thermal fatigue, or a combination of both exist, it requires more frequent reprofiling operations, thus, reducing the mileage of the wheel. ‘COMPOPAD PROVEN’ steel grade allows to extend the life of any tread-braked wheel in those cases where composite brake blocks are used, reducing the overall operating costs. Moreover, it fits the requirements defined in EN13262 for ER7, which means that the use of ‘COMPOPAD PROVEN’ for the manufacture of wheels does not, formally, suppose the use of a different wheel steel grade, that would force a new qualification process.
The combination of these new methods and investigations, together with the knowledge and experience of CAF MiiRA as one of the leading wheelset suppliers in Europe and in the world, has led to a tread-braked wheel that has been demonstrated to be better than any other wheel currently available in the market.
The most relevant skills of this new low-mass and low-noise development are aligned with the guidelines of the European Project Shift2Rail to increase the competitiveness of rail freight traffic, making it more efficient, environmentally-friendly and benefiting from a lifecycle cost saving. This is also in line with other European initiatives, such as the 5L project.
It should be highlighted that the importance of the reduction in the unsprung masses and noise emission, as valuable factors, especially for countries where track access charges and noise track access charges are already in force or are ready to be deployed.
For all these reasons, CAF MiiRA is currently carrying out an informative campaign for the wheelset market about the new LiTheS wheel.
Patenting activities of this innovative design are currently ongoing to assure the correct protection of the product’s added value features.
References
1. UIC 510-5:2007-05. Technical approval of monobloc wheels – Application document for standard EN 13979-1, 2007.
2. For wheels with a nominal diameter within the usual range between 840mm to 1,000mm.
3. ISO 18459:2015. Biomimetics – Biomimetic structural optimisation.
4. EN 13979-1:2003+A2:2011. Railway applications – Wheelsets and bogies – Monobloc wheels – Technical approval procedure – Part 1: Forged and rolled wheels.
5. Guiral, A. et al.: CRoNoS railway rolling noise prediction tool: wheelset model assessment, Euronoise 2018, Crete.