Advancing the role of additive manufacturing in rail
Posted: 25 November 2019 | Global Railway Review | No comments yet
The adoption of 3D printing, also known as additive manufacturing, in the rail sector has grown over recent years, but how effective is this technology and what true benefits does it bring? Speaking to Craig Waters, Editor of Global Railway Review, Stefanie Brickwede, Head of Additive Manufacturing at Deutsche Bahn (DB) and Managing Director of Mobility goes Additive, provided her insight into what rail can realise from this new and innovative technology.
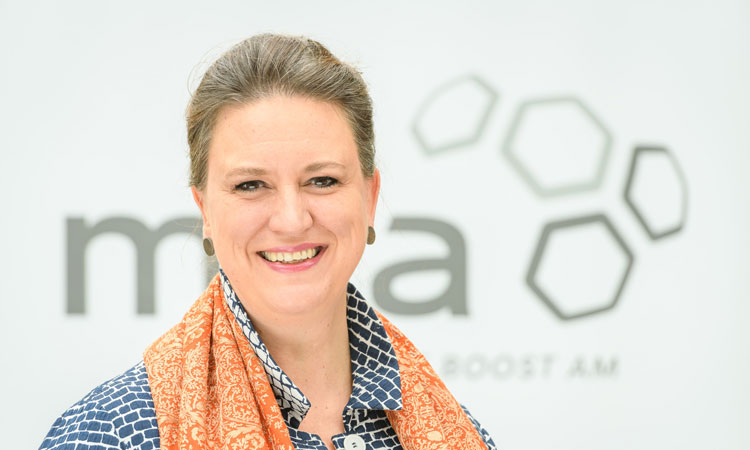
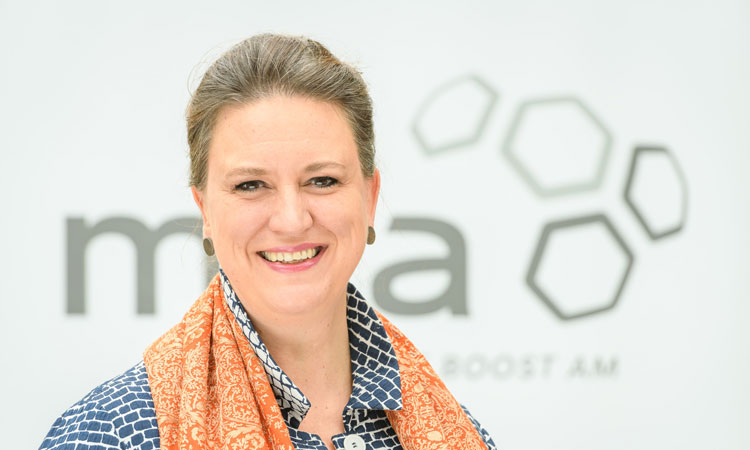
Stefanie Brickwede, Head of Additive Manufacturing at Deutsche Bahn (DB) and Managing Director of Mobility goes Additive
For Deutsche Bahn (DB), the benefits of 3D printing are true of those for the railway industry in general; to have an opportunity to manage the problems around obsolete spare parts that are no longer available, such as old components for infrastructure or old parts for trains, which have been previously used 30 years ago and are still in use.
Stefanie said: “We often have difficulty sourcing those spare parts, sometimes waiting up to two years. So, additive manufacturing makes a lot of sense, especially for small amounts of spare parts that may be needed.”
In the last four years, DB has printed more than 10,000 parts for more than 130 different use cases using a variety of materials. Stefanie continued: “We are still trying to identify more cases where additive manufacturing can be beneficial.”
In the printing of spare parts sector, I would say that DB are leading the way.
When compared to other railway companies, Stefanie was very keen to say that she thinks DB are leading the way. “At DB, we began to focus on additive manufacturing four years ago, figuring out what might be the best use cases for DB, as usually the whole technology comes from the prototyping. Since we are not a construction company, prototyping does not make that much sense to us, so we soon realised that we must focus on the printing of spare parts.”
Stefanie continued: “In the printing of spare parts sector, I would say that DB are leading the way. When we first started 3D printing, we wanted to get into an exchange of knowledge and experiences with other companies and were looking for existing networks, yet we didn’t find a suitable one. So, three years ago, we founded our own one – Mobility goes Additive, with nine founding partners, growing to today’s 105 members.”
Some automotive companies and suppliers have joined the Mobility goes Additive network, and Stefanie was clear that they are very experienced in printing prototypes, but not in printing spare parts. “This is an area where we want to learn together, avoid hurdles and overcome them. And we are definitely convinced that we can do this much faster when we do it together.”
Embracing the benefits of 3D printing
Rail needs to be made more reliable again, and additive manufacturing can play a crucial role in doing so. Trains do not need to be taken out of service for long periods of time, waiting for original spare parts to be delivered. This means more trains in service for passengers and less delays.
We started small – with a little coat hanger – something that is not a major drama if missing, but is still a nuisance to the passenger.
Stefanie explained: “We started small – with a little coat hanger – something that is not a major drama if missing, but is still a nuisance to the passenger. With something as small as a coat hanger, 3D printing allows us to remember the little details, which enhances the passenger experience as a whole.”
But now, the technology is far more advanced and capable of printing huge spare parts – for example, as Stefanie explained, a buffer box which is linked to the wagon of an ICE high-speed train. “Without the buffer box the train cannot operate and waiting for this spare part using the traditional method would take more than nine months – an expensive high-speed train cannot be taken out of service for nine months! With additive manufacturing, we can reduce that lead time for the spare part to just four months, including the certification, which is of course needed as safety is our highest concern and priority.”
But how much further can 3D printing be pushed to benefit Deutsche Bahn? “If, with the use of additive manufacturing technology, we are able in the future to print spare parts on-demand, we can reduce warehouse costs – and that’s a huge benefit – not only to Deutsche Bahn but also to our suppliers such as Siemens, Alstom, Bombardier, and others.”
Additive manufacturing is also a green technology. “You only require the material you really need for the spare part, if you compare it to former technologies,” explained Stefanie “And furthermore, since you’re able to produce spare parts much longer for let’s say motors or infrastructure, you can extend its lifecycle. So, the footprint is getting smaller, and this is why I believe this to be a truly green technology. So much so that, in our corporate project, additive manufacturing is now part of our ‘This Is Green’ campaign.”
The workforce
Unfortunately, skilled additive manufacturers are like “diamond dust – very rare”, says Stefanie. This is true in general, not only in the rail industry. Thus, it is very difficult to find suitable candidates. “Universities are trying to train them and trying to produce engineers who are capable of designing for additive manufacturing,” explained Stefanie, “but there are not enough right now. This is one point we would like to stress in our network, Mobility Goes Additive, that more work is needed in this educational field, because, of course, we need many, many more people who are capable of ‘thinking’ additive.”
But it is not enough to just focus on students or young people. The average age of someone who works for DB is more than 45, which means that they too must be taken by the hand and trained. “In cooperation with Fraunhofer institute in Hamburg which is focused on additive manufacturing, we’ve designed a training programme for our workers and procurement managers,” explains Stefanie. “It is not enough to just train the colleagues in the maintenance sites; we buy a lot of engineering services around additive manufacturing, so we also must train procurement colleagues. And that’s also fairly new – you won’t find many companies who do that.”
Sharing sector experiences
“We have a close cooperation with other train operating companies such as SBB, ÖBB, SJ, Trenitalia, and Angel Trains,” explained Stefanie. Together, a working group within that network, RAILiability, has been established, which aims to focus on the reliability of the rail sector and ensure frank exchange of experiences with additive manufacturing.
We have a close cooperation with other train operating companies such as SBB, ÖBB, SJ, Trenitalia, and Angel Trains.
Recently, wheelset bearing caps have been printed – a operation and safety relevant component of a train that is metal and typically weighs 17kg. “We had to find certain additive manufacturing technology for this, because the powder-bed technology we used before wouldn’t have been affordable, so we discovered a new technology called wire-arc additive manufacturing, which is an efficient and cost-effective method. We exchanged our wire-arc experiences with our Swedish colleagues and they’ve just recently printed another wheelset bearing cap.”
Through this collaborative experience, Stefanie explained that they’ve not only helped another organisation, but through their own testing and feedback, it has enabled DB to scale up the technology much faster, which will “ultimately benefit everyone.”
Mobility goes Additive
Stefanie explained that the goal of Mobility goes Additive is to bring more companies into additive manufacturing “because we believe that the more there are, the cheaper, easier, and faster it will be for all of us. We are acting from a user’s perspective, so we are not deep diving into research and development, but we try to express the wishes of the users; what they need, what quality levels those parts have to meet.”
Mobility goes Additive is also in communication with the material providers to exchange conversations about what kind of materials should be in development. “This is exactly what is done in our network; we have eight working groups working on approval, materials, ecological sustainability, education, digital supply-chain, and more. We try to lower the hurdles, and we are absolutely confident in our working group’s assertion – a rail-dedicated one, where we stick together, where we try to convince the authorities and certification bodies – that this is a reliable technology.”
Since 2015, Stefanie Brickwede has been heading the corporate project 3D Printing at Deutsche Bahn AG and is responsible for the successful introduction of additive manufacturing throughout the Group. As Managing Director, she passionately set up the international leading, neutral network Mobility goes Additive. The aim is to help industrial 3D printing technology achieve a breakthrough in the mobility sector and beyond. After graduating as an economist at the Technical University of Hanover, Stefanie started her career in the mobility sector and has held various management and project management positions at DB AG. As a recognised expert for additive manufacturing, she is a sought-after speaker on this topic.
Related topics
3D Printing/Additive Manufacturing, Digitalisation, The Workforce