SBB awards Bombardier the contract to build 59 double-deck trains for long-distance services
Posted: 17 May 2010 | | No comments yet
SBB has placed the largest rolling stock order in its history, with the goal of improving its rail offering for its customers.
SBB has placed the largest rolling stock order in its history, with the goal of improving its rail offering for its customers.
SBB has placed the largest rolling stock order in its history, with the goal of improving its rail offering for its customers. The Swiss rail provider has commissioned Bombardier Transportation Switzerland AG to build 59 new double-deck trains for its long-distance services, a total order volume of approximately CHF 1.9 billion.
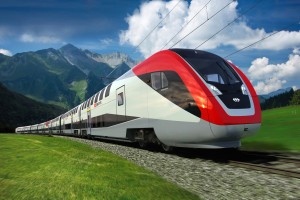
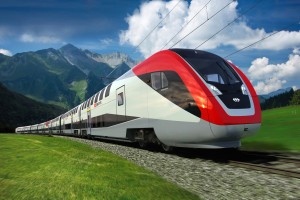
SBB awards Bombardier the contract to build 59 double-deck trains for long-distance services (©Copyright 2010 SBB CFF FFS)
The decision was taken following an extensive tender procedure governed by international agreements and Swiss legislation. But in the end, it was clear: Bombardier could provide the best product both in terms of passenger comfort and overall cost-effectiveness. The new trains are due to be rolled out in phases from December 2013, first on InterCity services on the St. Gallen–Zurich–Berne–Geneva and Romanshorn–Zurich–Berne–Brig routes, and on InterRegio services between Zurich and Lucerne, followed by other routes throughout Switzerland. SBB is ordering a total of 436 fully air-conditioned coaches with over 36,000 seats to enhance service quality for all its customers.
The SBB Management Board, after consultation with the Board of Directors, has decided to award the contract for 59 new double-deck long distance trains to Bombardier Transportation Switzerland AG.
Three rolling stock manufacturers were competing for this major order: Bombardier Transportation Switzerland AG, Siemens Switzerland Ltd and Stadler Bussnang AG. The winning project scored highest in all four main criteria and was particularly noted for the impressive levels of passenger comfort and for its high innovation potential in general. The winning project came in well ahead of the two other competitors.
The four main advantages of the Bombardier bid were as follows:
- Bombardier’s vehicles will have the widest interiors and deliver the largest number of seats, with distances between seats equal to that in IC 2000 coaches.
- The new trains will have energy-efficient power units, enabling energy savings of around 10%.
- Thanks to an optimised vehicle layout, the doors are equally spaced, enabling passengers to join or leave the train in the shortest time possible.
- Bombardier quoted the lowest overall price in terms of procurement and life-cycle costs.
The new trains will also offer other benefits:
- InterCity trains will include a large restaurant and a spacious family coach.
- Standard toilets on board will be roomier and will feature at least one baby changing table per train.
- Power sockets and wireless internet will be available at all seats in both 1st and 2nd class.
- A business compartment will also be available on all trains to allow meetings to take place in an undisturbed environment.
- All trains will be equipped with a modern customer information system.
- All vehicles will also have electronic seat reservation displays.
- To improve passenger security, all the new rolling stock will be fitted with video surveillance equipment and an emergency alarm system.
- The new vehicles will also be “pressure-resistant”: passengers will benefit from noticeably reduced pressure waves and less pressure on their ears in long tunnels and when trains pass one another.
“Objectively, Bombardier’s was the bid that best matched our specifications and offered us a very customer-friendly train,” SBB CEO Andreas Meyer told the media. Mr Meyer also stressed the cost-effectiveness of Bombardier’s bid: “Modern trains and a further improved offering will provide our customers with numerous tangible benefits. What is more the passive tilt capability of these trains will give us additional journey-time leeway throughout the network. This increases punctuality and leads to fewer missed connections. It is an important step in the continued improvement of our offering,” he said.
The total investment volume, including SBB’s own contributions and development costs, is CHF 1.86 billion. The competition in the tender process and the large procurement volume have driven this figure well below the credit volume of CHF 2.1 billion originally projected.
Bombardier has indicated that it will produce the new vehicles at two sites – in Villeneuve (CH) and Görlitz (D).
As well as the additional 59 trains now ordered, SBB has secured contractual options for over 100 more.
The award decision will be published on www.simap.ch on 14 May 2010, with a 20-day appeal period beginning on the same day. It is expected that the contract will be signed in June.
120,000 new seats by 2030
Over the next twenty years, SBB is going to need 120,000 more seats on its long-distance services: old, non-air-conditioned rolling stock must be replaced, and the company will also be increasing capacity on its long-distance services by 60,000 seats to take into account the additional demand expected. SBB’s current long-distance fleet consists of a mixture of double-deck trains, tilting trains and conventional single-deck trains, the oldest of which have been in service for over 40 years. The company will be investing an approximate total of CHF 20 billion in new and modernised rolling stock by 2030, and the funds for this must be generated entirely from SBB’s operating profits.
In April 2009 SBB put the largest order for rolling stock in its history out to tender: a total of 59 double-deck trains for long-distance services – 50 with a total length of 200 metres and nine totalling 100 metres. The offers received were put through a comprehensive evaluation process, which complied fully with the international conditions governing tender procedures of this kind, as well as the corresponding Swiss Federal Law and Federal Ordinance on Public Procurement. The evaluation criteria were listed in the public invitation to tender.
The following requirements were assessed:
- Fulfilment of the project’s list of specifications (30%): best ability to meet all of the approximately 2,600 customer-relevant and technical specifications
- Overall cost-effectiveness and deadline-orientation (30%): procurement costs (28%) and life cycle costs (42%); ability to keep to deadlines (30%)
- Contractual fulfilment (20%): best ability to meet the stipulations of the contract
- Continuity (20%): use of existing SBB standard components (20%), further development of the cooperation process (20%), design (20%), innovation (20%) and supplier project management (20%).
In accordance with the applicable legal provisions, the proportion of added value generated by a bid in Switzerland cannot be one of the selection criteria. In spite of the stringent requirements, SBB is nonetheless playing a vital role as a driving force and motor for the Swiss economy: the company is not only Switzerland’s fourth biggest employer, with a headcount of 28,000, but SBB is also a key customer of Swiss industry, placing orders worth some CHF 3.5 billion in 2009. Within the applicable legislation on public procurement processes, 87% of this order volume was awarded to companies in Switzerland. Thus, SBB additionally secured the equivalent of 16,000 full-time jobs at Swiss companies in 2009.
Passive tilt capability will save well over CHF 1 billion in infrastructure costs
In order to make travelling quicker and easier for passengers, Lausanne and St. Gallen need to be integrated into the timetable as “full hubs” with both hourly and half-hourly timetabled connections. This means reducing the journey time between Lausanne and Berne and between Zurich und St. Gallen to less than an hour each. This desired reduction is to be achieved on the one hand through infrastructure-related measures, and on the other through the introduction of new rolling stock.
The technology designed to be fitted to the new double-deck trains enables the vehicles to negotiate curves faster by tilting up to two degrees (the maximum tilt on conventional tilting trains is eight degrees). So with the trains’ passive tilt mechanisms enabling them to negotiate curves faster, journey times can be improved by around 10% without sacrificing passenger comfort.
Fitting the passive tilt mechanism specified in the tender to all 59 trains costs less than CHF 100 million in total. But the new technology obviates the need for well over CHF 1 billion worth of infrastructure expansion. It also generates increases in capacity and stability throughout the entire network thanks to the additional timetable leeway mentioned earlier.
Yet the idea of incorporating a passive tilt mechanism into trains is nothing new: similar systems are already in use on Talgo trains in Spain and Shinkansen services in Japan. SBB, too, has considerable experience with passive tilt mechanisms: its own class Re460 (“Lok 2000”) locomotives also feature similar technology.
SBB will join forces with Bombardier this year to retrofit a passive tilt mechanism to a double-deck coach from the existing fleet for testing. The first two new trains with passive tilt will be available from 2012/2013 for a class testing period of around one year. The two new trains will then be subject to two years of service-proving tests beginning at the end of 2013. The final decision on passive tilt is expected to be taken in mid-2016, with the tilting mechanism to be fitted to all new trains from 2016 onwards. SBB plans to involve the Swiss Federal Office of Transport (FOT) fully in the evaluation process. If, contrary to expectations, the trials are not deemed a success, the new trains will also be able to run conventionally. The manufacturer would then be required to pay SBB a penalty of up to CHF 100 million.
Preparing for certification in Germany and Austria
Another point that was widely discussed in the build-up to the award of the contract was the criterion specified by SBB that the new trains be prepared for possible use in Germany and Austria. This would enable the Swiss rail provider to ensure maximum deployment flexibility. The additional costs associated with preparation for certification in the two neighbouring countries total around CHF 2-3 million (adaptation of coach bodies, boarding height). Initially, SBB plans to have three trains certified for international use in Germany and Austria – a 200-metre InterCity set, a 200-metre InterRegio set and a 100-metre InterRegio set. This would cost a total of approximately CHF 10 million, and would pave the way for all sets to be retrofitted at a later date if required.
Nationwide rollout in phases from 2013
The new double-deck trains will be commissioned between 2012 and the end of 2019. Once preliminary commercial running is over, the first vehicles are expected to be phased in – starting at the 2013 timetable change – on the St. Gallen–Zurich–Berne–Geneva and Romanshorn–Zurich–Berne–Brig InterCity routes, and on InterRegio services between Zurich and Lucerne. More trains will then be introduced throughout Switzerland.
In order for the new double-deck trains to help provide enough seats on long-distance services in future, certain other investments are still required in rail infrastructure: some platforms will need to be lengthened to 400 metres. It will also be necessary to increase clearance on some routes to cater for double-deck rolling stock.