Insulated rail joints: Improving performance at high maintenance track sections
Posted: 27 February 2019 | Erik Frohberg, Harald Loy - Getzner, Martin Quirchmair - Getzner Werkstoffe | No comments yet
Signalling systems are part of every modern rail network. These systems create a safe and efficient operation by employing the rail as an electrical conduit for train location. To accomplish this, insulated rail joints (IRJs) are used to create blocks or independent sections of track by electrical isolation. Shortened IRJ life often occurs due to the different static and dynamic behaviour of IRJs compared to continuous rail. Consequently, many problems with track deterioration and signalling malfunction are related to them. Martin Quirchmair (Getzner Werkstoffe), Erik Frohberg (BNSF Railway) and Harald Loy (Getzner) explain further…
A singularity within the track
Ideally the static and dynamic behaviour of a railway superstructure is homogeneous within the entire network. Every change in bedding stiffness leads to impacts and accelerated deterioration. Unfortunately, local stiffness changes are unavoidable due to the need of special track work and signalling systems.
IRJs are essential for railway operation and safety, and therefore are used on signalised high-density main lines. To achieve electrical isolation, prefabricated bonded IRJs are used and welded in track. Various materials such as epoxy and Kevlar are used to create this insulation, as shown in Figure 1.
Increased dynamic forces at IRJs and their immediate vicinity are the most important cause of IRJ failure. Impacts from wheels lead to increased metal flow at the rail ends (short circuit), end-post battering and degradation of ballast. Furthermore, increased IRJ deflection as a result of fouled ballast induces stress onto IRJ components2.
On high-tonnage routes, IRJs may be replaced within as little as 12 to 18 months, which significantly reduces the availability of the track3 and increases operational costs. One approach to reduce these losses is to work on tailored solutions to keep the track quality on a high level over time and consequently increase the service life of all IRJ components.
Long-term performance due to enhanced track design
Under sleeper pads (USPs) are well known for their potential to enhance track design in high maintenance track sections like turnouts or transition zones. A diversified portfolio of stiffness and other mechanical properties makes USPs a viable solution to modify the static and dynamic bedding modulus of the track, which in turn helps to reduce settlement and ballast fouling. USPs can be installed within the concrete sleeper production process as well as on already finished sleepers. This flexibility makes USPs suitable for new installations as well as retrofitting.
Due to these positive characteristics, USPs should be considered to improve the long-term performance of IRJs.
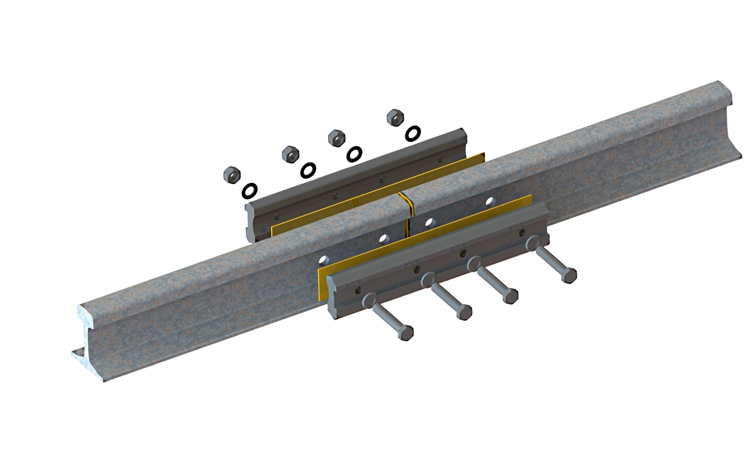
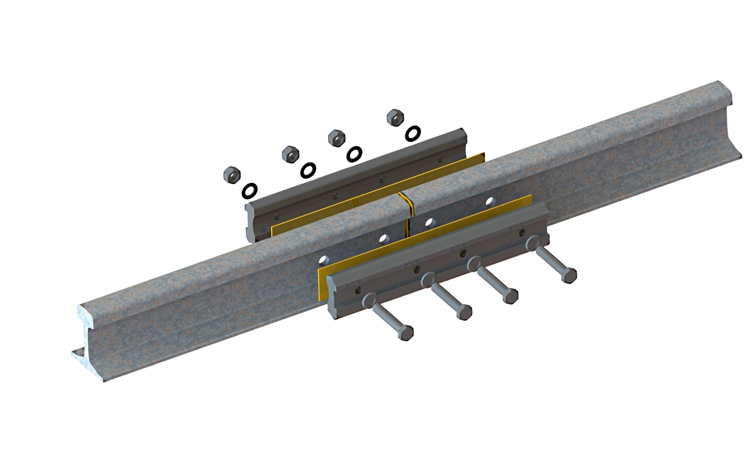
Figure 1: Principal of IRJ – Rail-ends are electrically insulated and bonded with fishplates and adhesives
Model-based design
Issues at IRJs have been a topic on and off in the past. At a meeting between BNSF Railway (the operator of one of the largest rail freight networks in North America) and Getzner USA Inc. in early 2016, an opportunity was identified as a way to study this sensitive area of track. Current practice at BNSF Railway has been to install wooden sleepers under IRJs in concrete sleeper territory. However, this practice does not create a homogeneous sleeper type.
Two IRJ concrete sleeper panels were scheduled to be installed in autumn 2016 which could be equipped with USPs. To figure out the best type of USP to be used for this special application, a custom-built finite element method (FEM) model was used.
Many analytical track models calculate rail deflection and other important design parameters by using the Zimmermann method – which idealises the track as an infinitely-long, continuously-bedded beam. These models work very well in homogeneous environments, where track parameters remain unchanged. This has been verified repeatedly.
In areas with suddenly altering properties the Zimmermann method reaches its limit as the differential equations cannot be solved analytically anymore. The solution to this problem can be found in numerical models like FEM. FEM subdivides the model into a finite number of elements and solves their differential equations numerically. As a result, complex track sections, such as special track work, can be analysed as a system for a holistic design approach.
The IRJ approach
Looking at the situation of an IRJ in particular, the singularity is found mainly at the IRJ itself. Differences in stiffness and mass ratio lead to extensive wear on all track components over time. In the beginning the characteristic behaviour of the IRJ is dominated by its properties, whereas after some time in revenue service the behaviour gets dominated by continuously increasing track defects, such as hanging sleepers and fouled ballast.
This problem can be tackled on two fronts. Firstly, reduction of inhomogeneity by decreasing ballast contact pressure and dynamic loads to limit wear of all track components. And secondly, the stabilisation of ballast to reduce ballast movement and improve long-term performance.
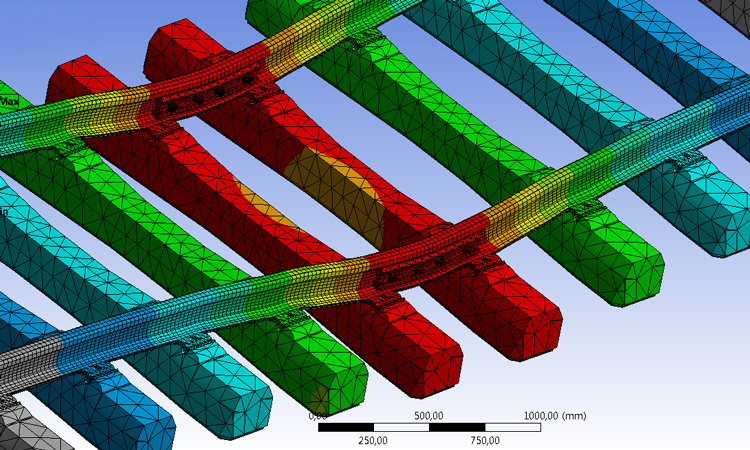
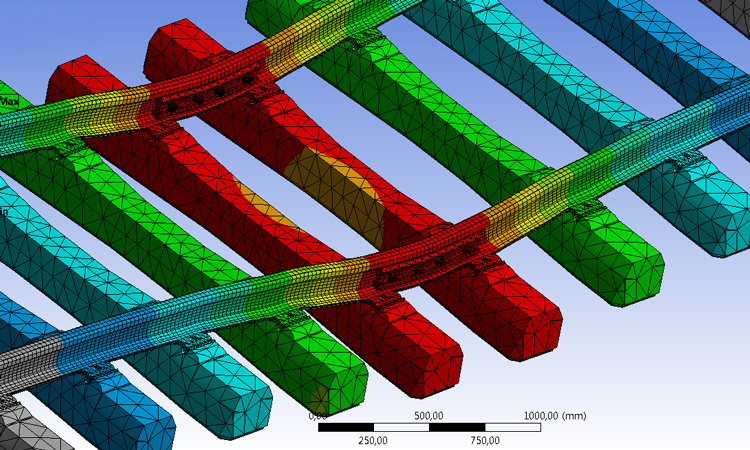
Figure 2: Calculated stress in IRJ panel for centre loading condition
Elasto-plastic USPs are able to handle both of these issues. The FEM calculation shows that static forces at a newly-installed IRJ and its immediate vicinity are reduced by roughly a quarter. Nonetheless, the biggest benefit can be found in the dynamic interaction between ballast and bottom of the sleeper. Unpadded sleepers show a ballast contact area of three to five per cent. This contact area can be increased to values up to 35 per cent and more, depending on the USP model4.
After taking all different properties of the new IRJ and USPs into account, the FEM calculation shows that the ballast contact pressure can be reduced by 70-90 per cent.
Additionally, the top layer of the ballast gets stabilised due to strong interlocking between ballast and USP. Lateral track resistance is increased. Ballast movement and surface irregularities are for the most part eliminated.
Validation in the field
The true test of a new technical innovation is field implementation. Engineers do their very best to find the optimum computational design, but performance in track determines if a solution delivers on its promises. Ballast and subsoil conditions can never be predicted perfectly, and some uncertainty is left in every calculation.
After more than a year of revenue service, measurements at the padded IRJ panels were taken. On this corridor BNSF Railway runs trains with 36 short tonnes (33 metric tonnes) axle load and speeds of roughly 60mph (100km/h).
Nearby, a standard IRJ with no USPs was selected for reference. At the control location trains with similar axle loads, speeds and frequency are operating. The setup chosen for this measurement had a focus on rail deflection.
Information about deflection during train operation is needed to achieve a fundamental understanding of the IRJ behaviour. With these findings the model can be refined for future calculations and the quality of the solution increases accordingly. Rail deflection was measured at four different locations.
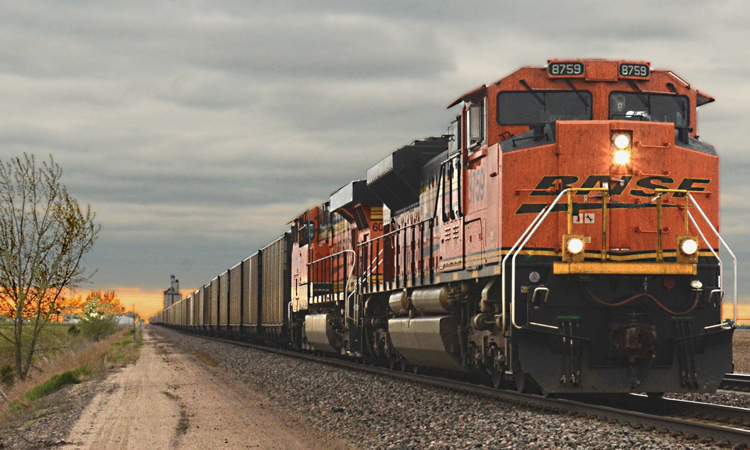
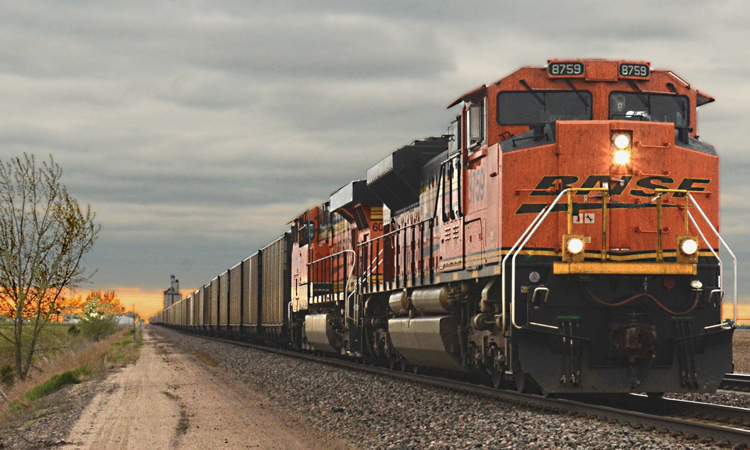
Figure 3: BNSF Railway runs 36tn. sh. (33t) axle load heavy-haul trains on its Powder River Division Track near Omaha, NE, U.S.
Evaluation and results
Due to the different configuration of each train the evaluation is based on the locomotives, which show similar axle loads for all measured trains.
In order to obtain statistically significant results for every single sensor, an average of the maximum deflection of the first three axles of all trains was made. This way the benefit of the solution in terms of stiffness adjustment can be seen in Figure 4.
The IRJs perform differently than the adjacent track. However, the IRJ itself shows less deflection with USPs compared to the control location. This phenomenon can be explained by looking at track alignment and surface over time. USPs are well known to reduce ballast movement and furthermore preserve track surface. Development of track defects is prevented and consequently the deflection at the IRJ location remains steady over time.
Conclusion
IRJs violate the homogeneity of railway tracks, which results in high dynamic stress and subsequent IRJ failure.
In 2016, BNSF Railway decided to test a new remedy for this high maintenance track section by installing IRJ concrete sleeper panels equipped with elasto-plastic polyurethane USPs. Getzner Werkstoffe’s expertise in designed elasticity for special track work provided tailored USPs based on modern FEM simulations.
The benefits of this solution regarding long-term track alignment were validated by in-field measurements in a heavy-haul track of BNSF Railway in Nebraska, U.S.
IRJ concrete sleeper panels equipped with elasto-plastic polyurethane USPs show a more uniform rail deflection compared to standard IRJs panels. Stress within the IRJ and roadbed is reduced, which leads to less maintenance, higher track availability and a more cost efficient operation.
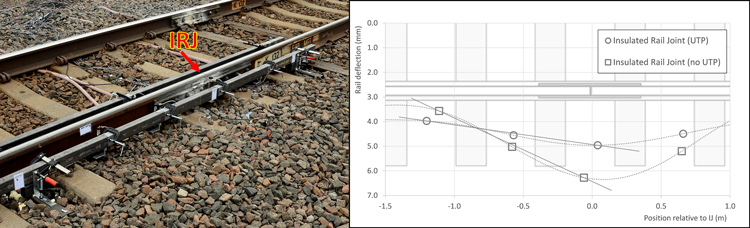
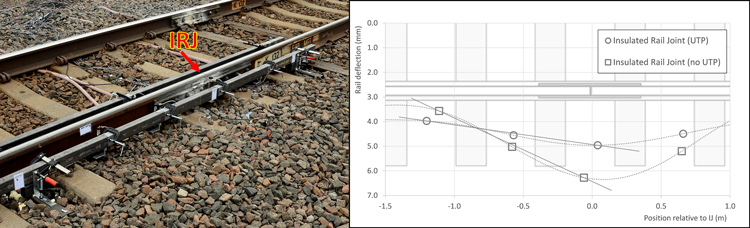
Figure 4: Rail deflection was measured at four locations close to the IRJ. Right: More uniform rail deflection of padded IRJ (○) vs. non-padded IRJ (□) in immediate IRJ vicinity leads to extended long-term performance
References:
- A. Wahnström: ‘Validation of insulated joints’; Chalmers University of Technology; 2011
- M Akhtar, D. Davis, T. O’Connor: ‘Revenue service evaluation of advanced design insulated joints’; AREMA 2008 Annual Conference, Salt Lake City, Utah, USA; 2008
- D. Davis, M. Akhtar, E. Kohake, K. Horiszny: ‘Eff ects of heavy axle loads on bonded insulated joint performance’; AREMA 2005 Annual Conference, Chicago, IL; 2005
- H. Loy, A. Augustin; ‘Pushing the limits of ballasted heavy-haul railway track by means of high-strength under-sleeper pads made of a specially developed PUR’; Rail Engineering International; 2015