HS2 finish foundation work for UK’s longest railway bridge
Posted: 1 February 2023 | Elliot Robinson (Editorial Assistant - Global Railway Review) | No comments yet
HS2 have finished installing the 292 concrete piles that will form the foundations for bridge at the 2.1-mile Colne Valley Viaduct.
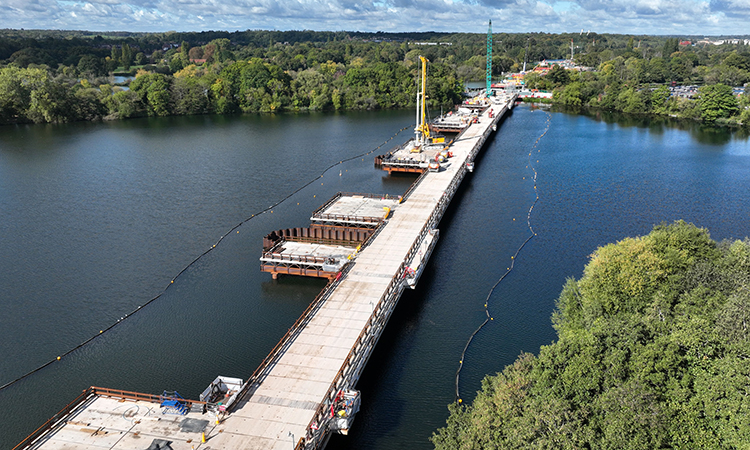
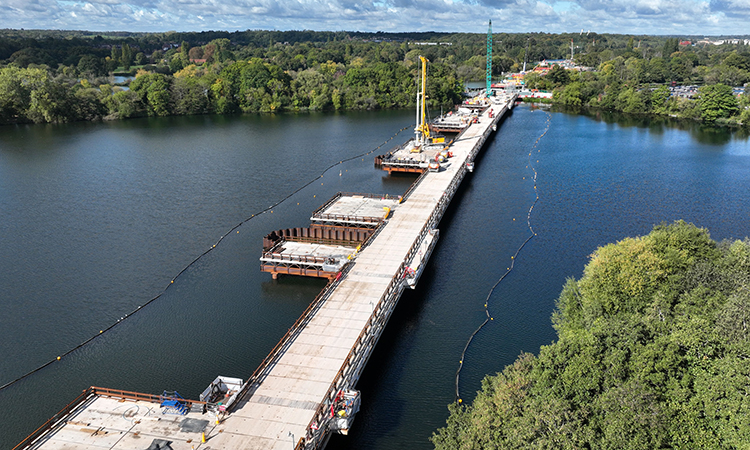
An aerial still of the Colne Valley Viaduct Site. - Credit: HS2
The last of 292 concrete piles that will form the foundations for the UK’s longest railway bridge have been installed at the site of HS2’s Colne Valley Viaduct, marking a successful end to the first phase of the record-breaking project.
Once complete, the 2.1 miles (3.4km) bridge will carry the new high-speed rail line across a series of lakes and waterways near Hillingdon on the north-west outskirts of London.
The construction of the foundations, the 56 huge piers and the deck on top, have all been happening in parallel – with separate teams working from north to south. Deck assembly began in 2022, with more than 500 metres of the viaduct structure now complete.
In order to deliver the 66 piles in the lakebed, the team first had to construct over a kilometre of temporary jetties, with cofferdams to hold back the water around each set of foundations. The jetties are also used to transport materials and equipment during the construction of the piers and viaduct deck, keeping vehicles off local roads.
Construction of the HS2 project – which is designed to improve rail links between London, Birmingham and North, help level-up the economy and provide a low carbon alternative to car and air travel – is ramping up across the UK with almost 30,000 jobs now supported by the project.
“Once complete, HS2 will transform journeys across the UK, help to boost the economy and support the UK’s transition to net zero,” David Emms, Project Client for HS2 Ltd, said. “The completion of the piling for the Colne Valley Viaduct is a major achievement for our whole team and marks the end of almost two years of hard work. With pier construction and deck assembly also well underway, the viaduct is fast becoming one of the most impressive and recognisable parts of the project.”
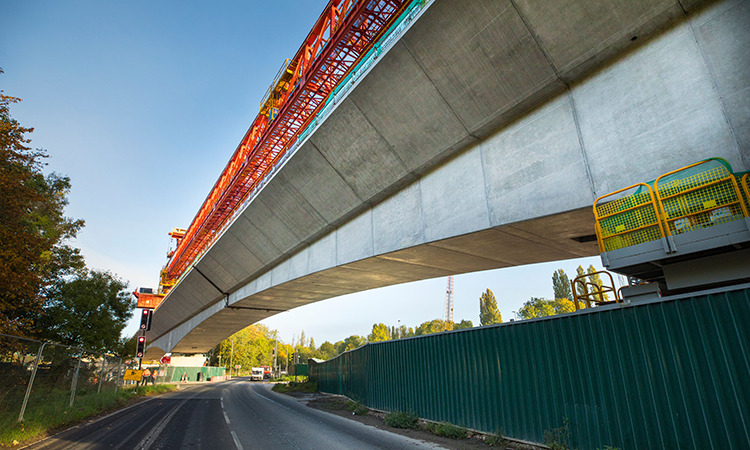
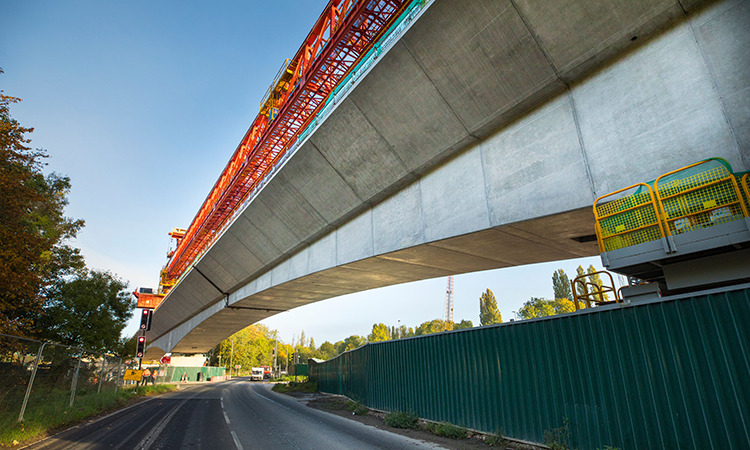
Credit: HS2
Building the viaduct
The viaduct is being built by HS2 Ltd’s main works contractor Align JV – a team made up of Bouygues Travaux Publics, Sir Robert McAlpine, and VolkerFitzpatrick, working with its contractor KVJV– who spent almost two years on the piling. KVJV is a team made up of Keller Group and VSL International.
On top of each group of piles – some of which are to a depth of 60m into the ground – a concrete pile cap will support the pier which will in turn support the weight of the bridge structure above. Instead of hammering the piles into the ground, holes were bored before being backfilled to create the piles.
The main deck of the viaduct is being built in 1,000 separate segments at a temporary factory nearby and assembled using a bridge-building machine which lifts each piece into position before shifting itself forward to the next pier.
“Completing the piling is a great achievement for both Align and the team at KVJV, working over the lakes and waterways across the Colne Valley,” Derek van Rensburg, Surface Operations Director for Align, said. “We were able to complete the piling with no significant impact on the environment, a great result for the whole team.”
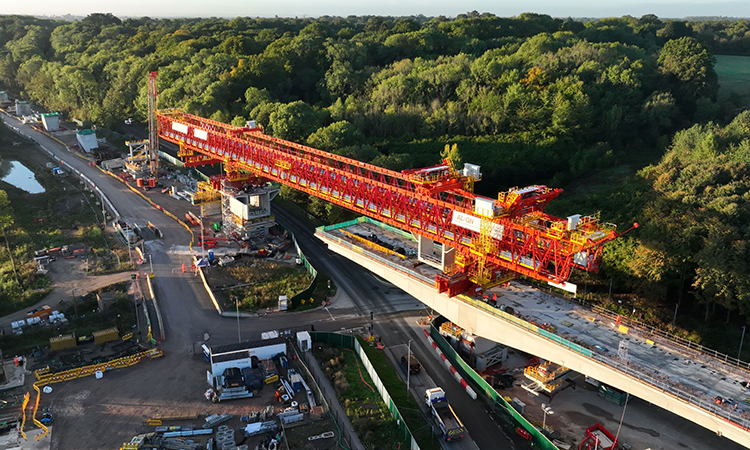
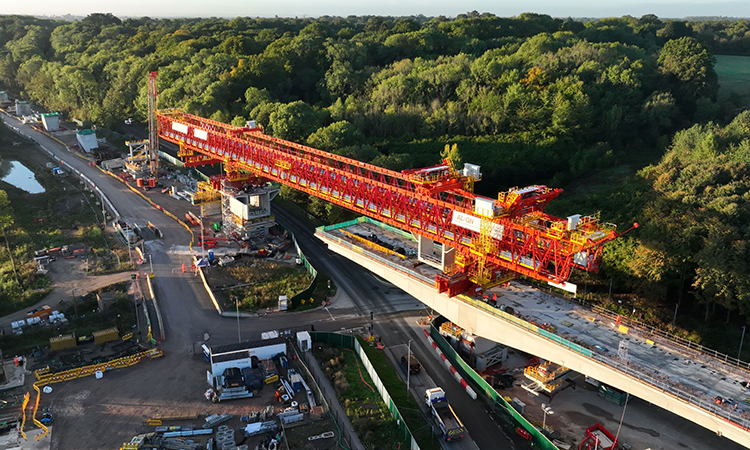
An aerial still of the Colne Valley Viaduct Site. – Credit: HS2
Choosing the design
Set low into the landscape, the widest spans reserved for where the viaduct crosses the lakes, and narrower spans for the approaches. This design was chosen to enable views across the landscape, minimise the viaduct’s footprint on the lakes and help complement the natural surroundings.
The design was inspired by the flight of a stone skipping across the water, with a series of elegant spans, some up to 80m long, carrying the railway around 10m above the surface of the lakes, River Colne and Grand Union Canal.
HS2 worked closely with Affinity Water and the Environment Agency to monitor water quality and agree working methods. These were monitored by a team of specialist engineers during construction in order to protect the natural environment.
Before work began, an extensive programme of test piling was completed with engineers sinking 12 piles at two locations with geological and structural data from these tests fed back into the design of the viaduct. This resulted in a 10-15% reduction in the depth of the piles and associated time and cost savings.
Related content you will enjoy:
HS2 boosts Oxford-Cambridge connections with East West Rail bridge
HS2 helps to encourage young people to get into construction
Related topics
Infrastructure Developments, Route Development, Sustainability/Decarbonisation, Track/Infrastructure Maintenance & Engineering