The future of journal bearings for high‑speed trains
Posted: 20 September 2022 | Riccardo Licciardello | No comments yet
Riccardo Licciardello, Professional Engineer at ANSFISA, the Italian rail and road safety authority, explains how the journal bearing workstream of the Shift2Rail-funded GEARBODIES research project is looking to reduce the lifecycle cost of rolling stock bearings and running gear, primarily through improving the longevity of bearing units.
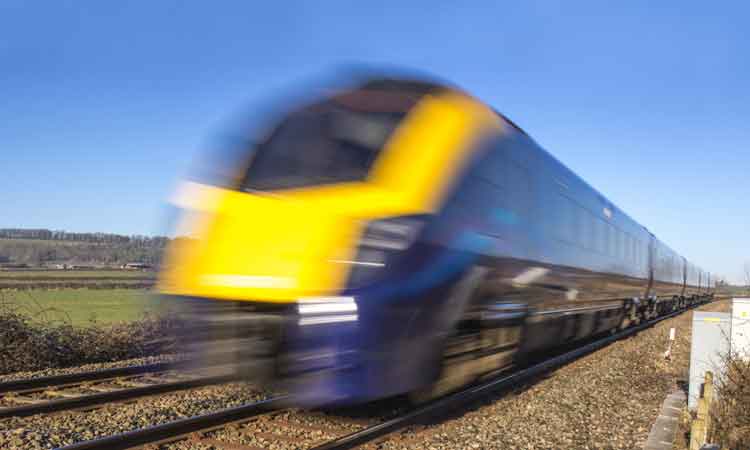
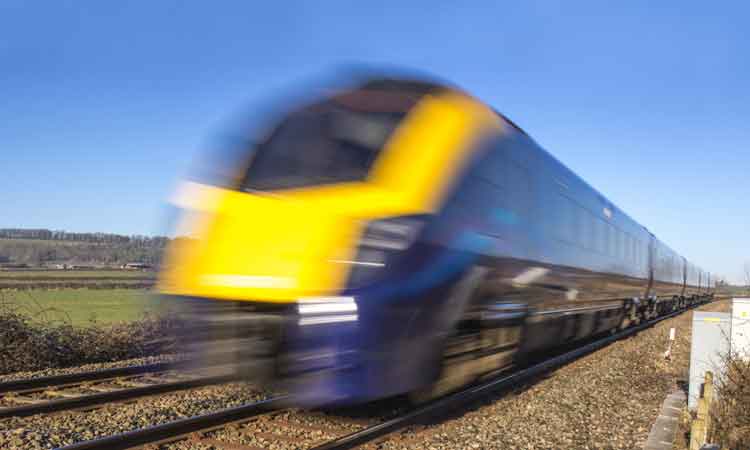
The journal bearings of today’s high speed trains – i.e., the components that allow free relative rotation of the wheelset with respect to its axleboxes – are hightech precision mechanical assemblies transmitting loads of tens of kilonewtons up to rotation speeds of 2,000 rpm.
The widespread tapered and cylindrical double‑cage bearing units are safety-critical parts. Just one failure may lead to a catastrophic accident, particularly at high speeds. Thus, the related maintenance activities are a key part of any running-gear maintenance plan.
Conventionally scheduled maintenance is being replaced by ‘smarter’ predictive maintenance, with sensors (such as for temperature and vibration) used to diagnose any adverse health condition early and enable the prediction of residual lifetime.
In spite of the on-going advancements, historical maintenance activities are still the cornerstones of an effective plan: regular visual inspections (e.g., for lubricant leakage) and a major overhaul – most often a replacement with a new or re-conditioned bearing unit. Bearing replacement requires wheelset removal and, thus, significant down-time of the related vehicle/vehicles. It is convenient to arrange other maintenance activities that require wheelset removal at the same time, even if their potential maintenance interval is longer than that required by the bearings. This is the reason behind the main goal of the journal bearing workstream of the Shift2Rail-funded GEARBODIES research project, to reduce the lifecycle cost (LCC) of bearings and running gear mainly through the improvement of the longevity of bearing units. The aim is to investigate and develop technologies for extra-long maintenance intervals (3 Mkm compared with today’s 1.65 Mkm) and ultra-long maintenance intervals (more than 5.5 Mkm). The overall bearing lifetime of two maintenance intervals, in the latter case, would correspond to over 11 Mkm and 25 years of service.
The GEARBODIES project
GEARBODIES, coordinated by Eurnex, started on the 1 December 2020 and is due to close on 31 December 2022. The research team for its journal bearing workstream comprises three academic partners (SAPIENZA University of Rome, Italy; University of Newcastle, United Kingdom; Vilnius Gediminas Technical University, Lithuania), a non‑profit private R&D association (AIMEN Technology Centre, Spain) and a world-leading bearing manufacturer (Schaeffler Technologies, Germany). With a budget of approximately €650,000, the team is addressing the goal of LCC reduction in a structured manner. The technology concepts initially screened were analysed by means of the so-called Analytic Hierarchy Process, a multi‑criteria technique based on pair-wise comparison of alternatives, as shown in Figure 1. The analysis went through the break-down of the goal into specific objectives, each of which was assigned corresponding criteria, in turn related to the alternative technology concepts.
LCC reduction is pursued mainly through the improvement of lubricant longevity. In fact, this specific objective was generally shown to be the current driver of the maintenance interval. The lubricant (currently special bearing grease) degrades through exposure to ambient and frictional heat, as well as accumulation of contaminants.
For extra-long bearing lifetime, slowing lubricant degradation is being pursued by Schaeffler, mainly by means of an optimised design of component geometries: for example, the use of balls instead of tapered or cylindrical rollers, as well as carefully studied changes in geometrical details such as the shape of the inner ring lips and the polymer cage (see picture in Figure 1). The purpose of these innovations is to reduce the frictional heat generated during service to a minimum, with significant extensions of lubricant lifetime. The plan is to validate the solutions in the GEARBODIES project by means of bench testing according to EN standards.
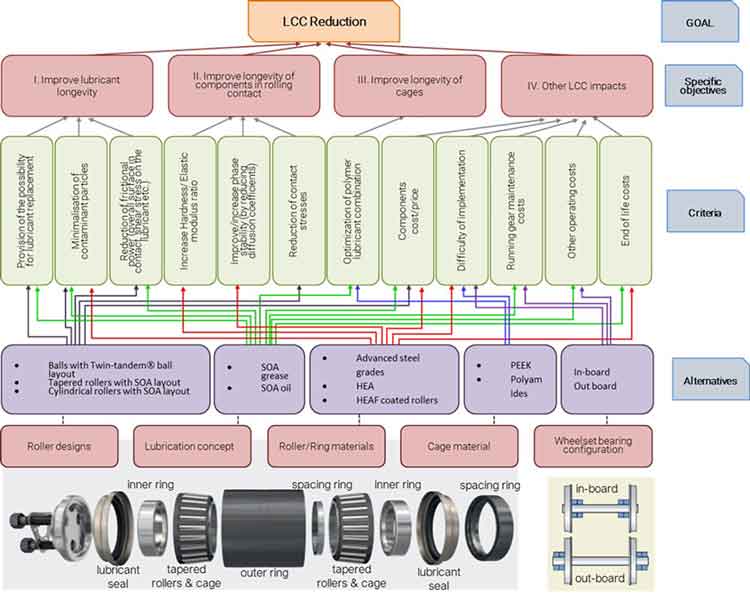
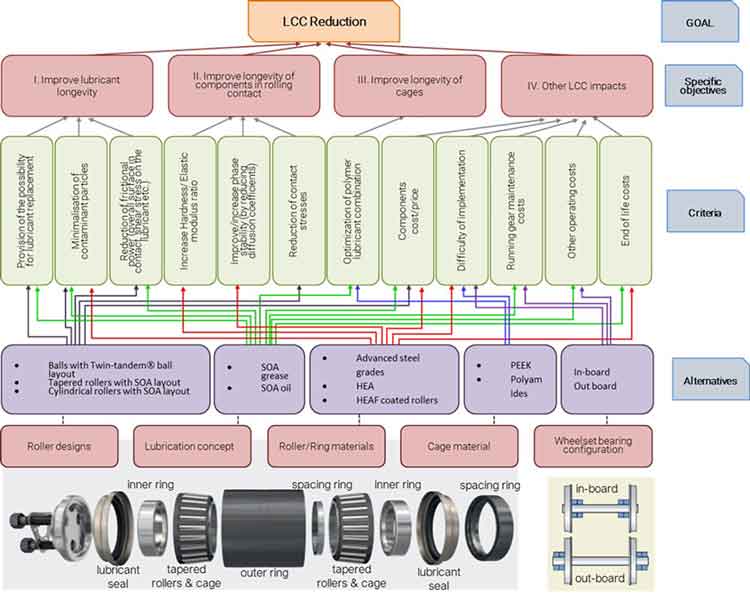
Figure 1: The Analytic Hierarchy Process.
For ultra-long lifetime, the work is more conceptual. Oil lubrication, sometimes used in the past but now universally replaced by grease, is being considered due to its potential for lubricant cooling and filtration, as well as ease of replacement without removing the bearings. Tests have been performed by Schaeffler on state-of-the‑art bearings to check the capability of the bearing seals to prevent oil leakage, with unsatisfactory results. The most promising solution is to work with sealed housings, to be developed in future projects.
The consequent ultra-long lubricant lifetime could extend beyond the current lifetime of the state-of-the-art steel grades used for the rollers and rings, as well as that of the widely used polymeric materials for cages (although metallic cages are a possibility, they offer less guarantee against a sudden seizure in case of failure). For this reason, the specific objectives of increasing the longevity of components in rolling contact and of cages were included.
For the components in rolling contact (rollers, inner/outer rings), the focus is on High Entropy Alloys (HEA). As opposed to conventional alloys, which are composed of one principal element (such as iron for steel alloys) with secondary elements in much lower concentrations, HEA involve four or more principal elements, all in relatively high concentrations. The large number of element combinations implies an enormous number of possible systems and the freedom to tune compositions to achieve desired mechanical properties. HEA is thus a promising solution for the development of highly wear-resistant and low friction rollers and rings. In the GEARBODIES project, the University of Newcastle has selected potential candidate HEAs (for example Nb25Fe25Cr25V25). The key properties (tribological, hardness etc.) of HEA film-coated steel samples are being laboratory tested in Newcastle for their suitability as roller and ring materials. In fact, for the bearing application it is the surface properties that count the most (i.e. those that keep friction low and fatigue resistance high). The use of HEAs as base material was ruled out, at least initially, due to the foreseeably high component prices.
Similarly, samples of a commercial PA66 reinforced with glass fibre (33 per cent) and a novel PEEK solution are not employed for journal bearings yet are being tested by AIMEN. Themost interesting aspect for ultra-long lifetime is their ageing behaviour in the bearing lubrication environment. Samples manufactured by injection moulding are being auto-clave tested with both a solid lubricant (grease) and a liquid lubricant (oil) to identify differences in ageing behaviour (accelerated ageing tests). Mechanical tests (tensile and three-point bending) are performed by AIMEN and VILNIUS TECH before and after the ageing test to evaluate the differences in the key properties.
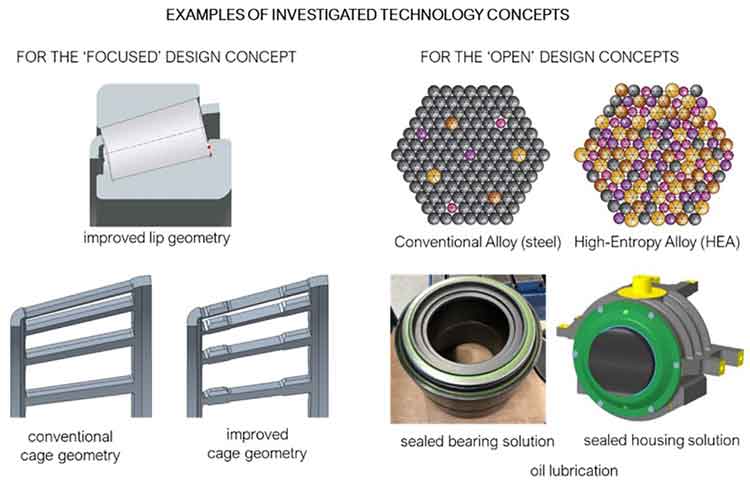
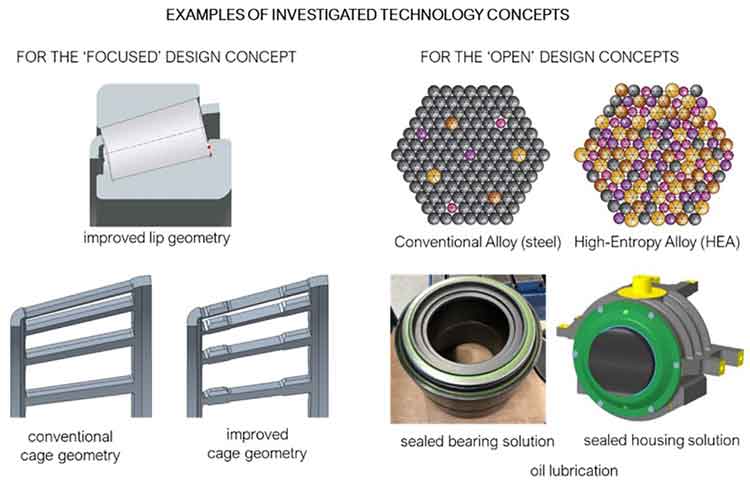
Figure 2
The findings of the aforementioned investigations and tests are being used by SAPIENZA and Schaeffler to inform the GEARBODIES journal bearing Design Concepts (DC):
- A ‘focused DC’ targeting extra-long lifetime, with higher Technology Readiness Level (TRL) and subjected to validation tests in the laboratory
- A suitable number of ‘open DCs’ targeting ultra‑long lifetime, with a lower TRL.
The conceptual work is accompanied by a preliminary identification and, where possible, quantification of stakeholder impacts. The most important stakeholder for market uptake is the train operator, for which a favourable business case is crucial if the GEARBODIES project innovations are to roll out of a production line for the next generation of high-speed trains. The key operator benefits are expected to be the lower running-gear maintenance costs associated with the much longer bearing maintenance interval. Additional benefits are the lower traction energy bills, due to the lower bearing friction. Moreover, the GEARBODIES project bearing innovations are key enablers for the attractive on-board bearing configuration, which can also lead to traction energy savings due to the consequent aerodynamic motion resistance improvements, as well as to favourable wheel and track maintenance impacts due to the lower unsprung mass.
Issue
Related topics
Bogies & Wheelsets, High-Speed Rail, Rolling Stock Maintenance, Track/Infrastructure Maintenance & Engineering