The WESTbahn way of carrying out rolling stock maintenance
Posted: 20 April 2020 | Erich Forster | 1 comment
As a privately-owned open access operator in Austria, WESTbahn must ensure its rolling stock asset is always operational. Erich Forster, WESTbahn’s CEO, outlines what it takes to maintain their fleet, including the four pillars of maintenance activities it adheres to.
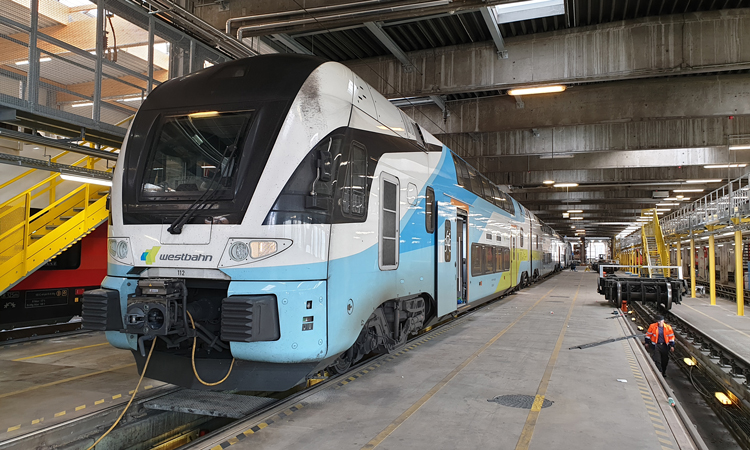
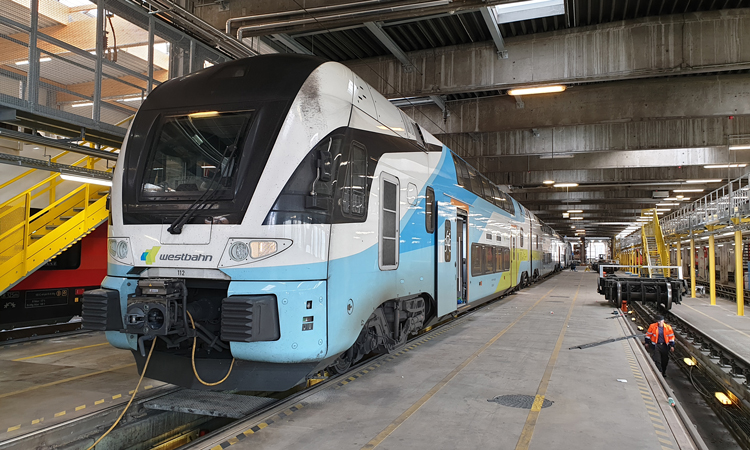
WESTbahn has been operating express train services in Austria since 11 December 2011, providing an open access offer between Vienna and Salzburg, competing with state incumbent ÖBB on that section. We have approximately 350 employees, about 85 per cent of which are employed on-board as train drivers and crew members. Complimentary to our on‑board staff, we have an exceptional back office service of employees covering every aspect of our business.
In 2011, WESTbahn started operating from Wien Westbahnhof (this line was later called WESTgreen) with a fleet of seven six-car Stadler KISS 1 (4010) sets, containing 501 seats each. In 2014, our supervisory board decided to invest in an additional KISS 1 (4010) trainset with 526 seats, and nine four-car (4110) trainsets with 326 seats each. WESTbahn needed this new additional fleet because, in December 2017, we opened a second line (called WESTblue) from Wien Praterstern (via Hauptbahnhof and Meidling), running parallel to WESTgreen, between St. Pölten and Salzburg. In 2019 – for several reasons – we decided to sell our whole fleet to Germany’s Deutsche Bahn (DB) in two batches. The first batch (the nine ‘short’ KISS 2 4110 trainsets) was passed into DB ownership in December 2019, which also resulted in a reduction to an intensified hourly WESTbahn service from Wien Westbahnhof to Salzburg. We will hand over the remaining eight 4010 trainsets to DB once we can move the 15 KISS 3 trains we ordered in 2019 into service – this is expected to be in the second half of 2021. We will then own a homogeneous fleet which, in turn, will help to improve all matters of maintenance.
Maintenance
Our top priority is to have all trains operating 365 days a year, which might be a rather unfamiliar approach to many other companies.
We are predominantly a privately-owned company competing in open-access traffic. This, of course, means that we have to prioritise all matters that strengthen our competitiveness. Thus, our top priority is to have all trains operating 365 days a year, which might be a rather unfamiliar approach to many other companies. We cannot afford to have one of our trainsets out of action; not even set aside as a reserve. These requirements define our attitude towards maintenance and provide the respective time window for it. The four pillars we base our maintenance system upon, are:
1. Preventive maintenance
Our maintenance is carried out by ÖBB Stadler Service GmbH, a joint venture of ÖBB Technische Services and the manufacturing company of our trains, Stadler. They complete our preventive maintenance in night shifts during the idle times in our schedule.
An important perquisite for this is that we split the main inspection of our fleet into several reasonably divided maintenance modules, each fitting into one of these eight hour periods. At the end, a full main inspection will have taken several weeks, or up to three months, but no single trainset will have been set aside for the procedure. This way, we need approximately one or two trainsets less than any comparable company doing their maintenance the ‘customary way’. We have hardly changed anything in this approach over the years; although, we used a workshop in Linz in the beginning, but we decided to move maintenance to Vienna in mid-2018, for matters of simplification (and to avoid empty runs) and not because of any changes in our overall approach.
Besides our modular preventive maintenance activities, we also have a 24/7 stand-by at our disposal if there is any damage en route. They do ad hoc eliminations of fault or decide how to proceed with a problem that occurs during operation. In single cases, they also establish direct contact between train staff and the maintenance workshop if that speeds up the procedure of necessary technical adjustments.
2. Modular maintenance
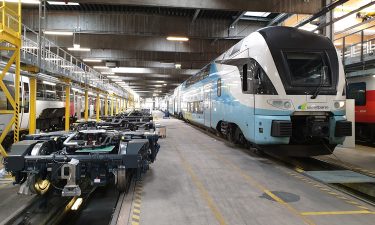
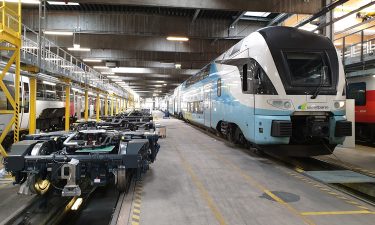
WESTbahn’s modular maintenance approach means extensive work on large components, such as bogies, can be performed within a night shift.
This approach to modular maintenance calls for foresight during the manufacturing period. It only works if all large components can be changed in (in our case) during an eight-hour interval. One example: WESTbahn requested (among many other components) a KISS bogie construction from Stadler that will allow changing both bogies of one coach within a night shift. This, as a result, also affected the cabling construction, which was tailor-made for WESTbahn.
What’s more, Stadler took over some of our construction improvements for the Swedish MTR KISS, where they also perform maintenance themselves. As manufacturers start to offer maintenance to operators, the industry will most likely see a lot of technical development in the near future. In order to adhere to the corresponding contracts (that are usually based on annual mileage or availability), they will have to rethink their components. A paradigm change will result from that: the manufacturing companies will, most probably, sell smaller batches of trainsets to operators (since these will not be able to afford a large reserve in an increasingly competitive surrounding) but make money from affiliate services, like maintenance.
3. Investment in technology
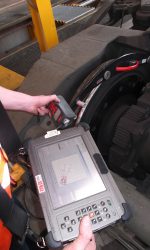
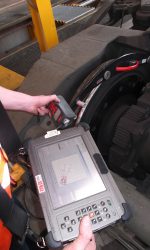
Digitalisation and innovative solutions play an important role in the close monitoring of trainsets.
The third backbone of our maintenance is a strong investment into technology, right from the beginning. Each of our trainsets commands a comparatively high number of redundancies, which allows unrestricted operation, even if any malfunction appears. Redundancies are costly: we have equipped our trains with, for example, eight traction motors, so that nobody will notice if one of them fails. In addition, we control the motors separately in order to avoid them failing in pairs. This investment requires a mid- or long-term view but, as aforementioned, we will do anything possible to avoid cancelling even one train in our schedule.
Furthermore, we have improved several details of our KISS 2 trainsets based on empirical values. The most prominent feature is our downsized and adapted front window in the driver’s cab. One benefit is that, due to the smaller size, there are less bird impacts. The other benefit is that, if anything happens, despite that reduction, changing the windshield will take one person just two hours, since the shield is being screwed into place (whereas KISS 1’s gummed larger window required approximately 24 hours for drying).
4. Digitalisation and data
We closely monitor our trainsets and digitalisation plays an important role in this. We come across problems much faster, since our KISS trains are equipped with a near real-time (i.e. 30 seconds delay) online monitoring system. This system observes any deviation from the norm and sends a diagnostic notice to the vehicle if a problem occurs. It delimits the problem in advance and sends the respective data to a server accessed by our maintenance specialists. They analyse the deviation so that any spare parts needed to fix the weak spot can be prepared, even before the train comes to our maintenance facility. Because of our monitoring, the people involved in corrective maintenance can react fast and minimise the standstill. That way, we can frequently debug during a turn without any interruption of service. Of course, we are not the only ones who collect data via such a monitoring tool. Still, what distinguishes us from other companies is that we have the manpower to interpret the data coming into the system so that we can react at short notice.
Another use case for digitalisation that helps improve our operational stability is the cooperation with ÖBB-Infrastruktur – the organisation that plans, develops, maintains and operates rail infrastructure in Austria – on the ‘rolling stock fingerprint’. One of their real-time measuring points is located in the Tullnerfeld area, and it provides real-time information about wheel load, shearing forces, wheel shape and other parameters. It documents the compliance and exceedance of technical thresholds of trains passing by at a velocity of up to 250km/h.
One of our representational projects with ÖBB‑Infrastruktur, in connection with that fingerprint tool, is about wheel roundness. In order to fit into our modular maintenance system, we decided that every wheel coming to a value of 0.20 should be reprofiled. Since we perform reprofiling at a very early stage, the milling will remove little material, and we can use the wheel for a much longer period. This also helps to maintain WESTbahn’s high standard of ‘smoothness’ when operating on tracks and, in addition, it’s also a win for the infrastructure operator, since we do not damage the tracks due to our wheels being in a bad condition.
One step ahead
Naturally, we know that our successful maintenance concept profits from the fact that we have a rather small fleet, that our Vienna headquarters is geographically close to our workshop and that we’ve adjusted our logistics to our way of doing preventive and corrective maintenance. Nevertheless, we are proud that we are one step ahead in these matters compared to other market players. And our success proves us right: we have an average train availability of 99.8 per cent.
Dr. Erich Forster has a doctorate in psychology from Vienna University. He joined WESTbahn Management GmbH in April 2011 as Chief Commercial Officer and, since May 2012, has been CEO. In addition to this, Erich became Executive Director of Rail Holding AG (WESTbahn’s mother company) in February 2014. Prior to his current position, Erich worked for the Austrian rail incumbent, ÖBB, since 1975, and finished there as its Head of Long-Distance Traffic.
Issue
Related topics
Big Data, Bogies & Wheelsets, Digitalisation, Operational Performance, Rolling Stock Maintenance, The Workforce
Related organisations
Deutsche Bahn AG (DB AG), ÖBB Stadler Service GmbH, ÖBB-Holding AG, ÖBB-Infrastruktur AG, ÖBB-Technische Services GmbH, Stadler, WESTbahn
Congratulations for your work! I think that a better knowledge of the human Psyche must have helped!
Retired supervisor – São Paulo Subway Company – Condition Monitoring Team