Whitepaper: Semi-automated Aluminothermic Rail Welding
Posted: 22 May 2025 | Pandrol | No comments yet
Increasing quality, productivity, safety and versatility with data and automation.
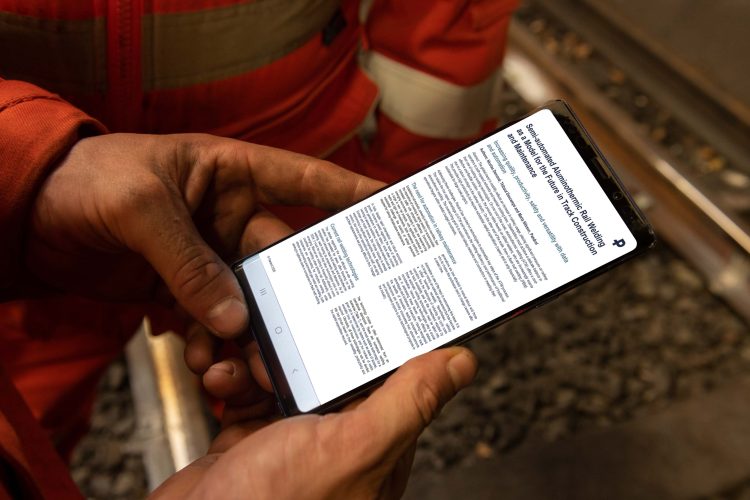
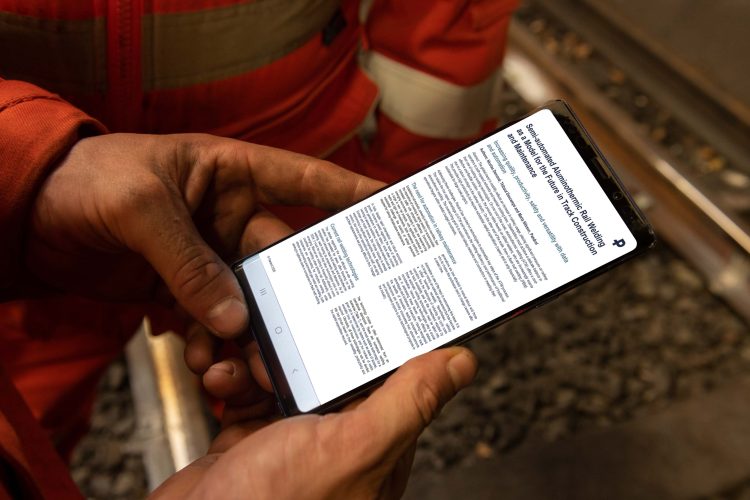
Discover the latest innovation in Aluminothermic Rail Welding from Pandrol in their newly released white paper.
In this comprehensive white paper, Pandrol delves into the advantages of semi-automated aluminothermic rail welding and how it is transforming the rail industry.
The global trend in mobility reflects an increase in railway usage, placing significant pressure on railway operators to both expand networks and maintain existing lines. Stakeholders must achieve a delicate balance in their use of existing welding technologies. On one end of the scale, aluminothermic welding (ATW) offers a cost-effective and flexible solution. However, the process relies heavily on skilled welders, who are increasingly scarce due to a labour shortage in the railway industry. On the other end of the scale, there is flash butt welding (FBW), which provides high productivity but requires substantial capital expenditure (capex) and is only financially sustainable for large-scale projects.
Addressing these challenges, Pandrol has worked on technologies to automate key steps of the ATW process. This retains the low capex advantage of ATW and enhances the welding efficiency and performance of traditional aluminothermic welding. The overarching goal is to assist railway networks and contractors in meeting their operational targets within realistic budget constraints.
Key highlights from the paper include:
- Automation of aluminothermic welding technologies
- Quality and operational improvements
- Addressing challenges in rail welding to maintain quality standards
Related topics
Infrastructure Developments, Safety, Sustainability/Decarbonisation, Track Construction, Track Maintenance Machinery, Track/Infrastructure Maintenance & Engineering