DB use 3D printing to transform train maintenance
Posted: 22 May 2023 | Elliot Robinson (Editorial Assistant - Global Railway Review) | No comments yet
Deutsche Bahn have produced 100,000 3D-printed spare parts for train maintenance, allowing them to save time, money and resources.
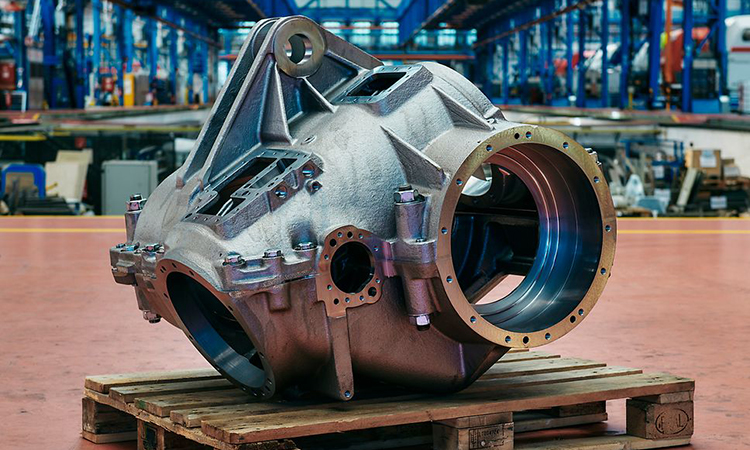
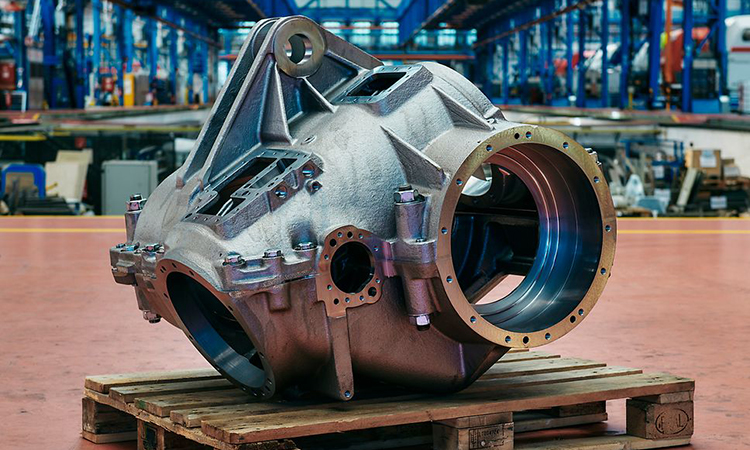
Transmission housing - manufactured using indirect 3D printing - Credit: Deutsche Bahn AG /Dominic Dupont
Deutsche Bahn (DB) have produced 100,000 spare parts using 3D printing technology. The 100,000th part is a gear housing for shunting locomotives. With a volume of almost one cubic metre and a weight of 570 kilograms, it is both the largest and the heaviest 3D printed part that the group uses. The spare part is indispensable for the operation of the shunting locomotive – the vehicle stands still without the gearbox housing. In the future, around 370 locomotives will benefit from the speed of the new process, can be repaired more quickly and used again in shunting operations.
Using conventional procurement methods, the part would only have been available with the long delivery times averaging ten months. By opting for a replica using 3D printing technology, DB shortened the delivery time to just two months. The new gearbox housing is produced in an indirect 3D printing process using binder jetting. A powdered starting material is combined with a liquid binding agent to form the mould into which the gearbox housing is later cast.
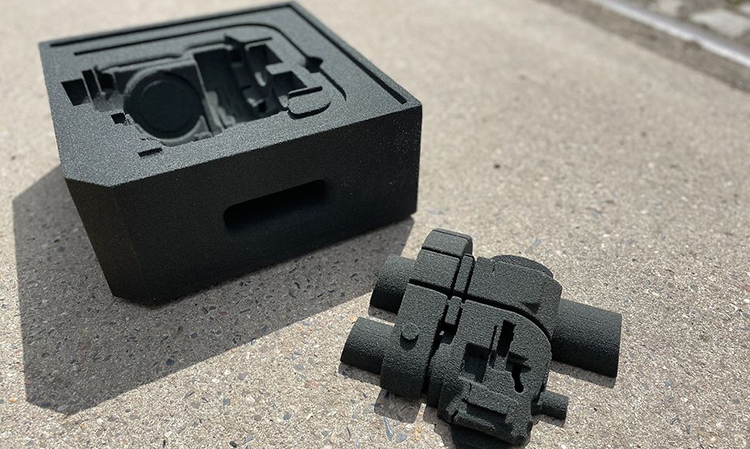
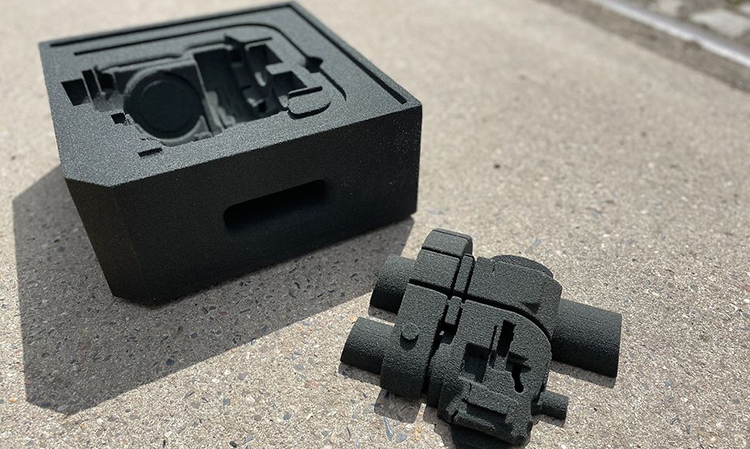
Model of a 3D printed sand mould – Credit: Deutsche Bahn AG /Susanne Tost
The gearbox housing is part of the digital warehouse that DB is continuously expanding. Virtual technical drawings of spare parts are stored in the database. If required, these parts can then be produced quickly and easily using 3D printers. This saves logistics space, storage costs, shortens delivery times and logistics chains and thus creates independence.
In this way, DB also ensures greater sustainability. Shorter distances and smaller physical warehouses avoid CO2 emissions and the waste of resources through superfluous inventories. In addition, 3D printing itself saves resources because only the raw material actually required are used in production. This is more economical than so-called cutting processes, in which parts are milled out of a block. In addition, 3D printing extends the life cycles of vehicles. This is because Deutsche Bahn can use it to manufacture components that are no longer available from the manufacturer.
Related content you will enjoy:
“3D printing is transforming maintenance,” Daniela Gerd tom Markotten, DB Board Member for Digitisation and Technology, said. “It saves time, money and resources because we can produce spare parts at the touch of a button thanks to a “digital warehouse” and do not need large inventories. In times of global supply bottlenecks and raw material shortages, 3D printing is more important than ever.”
DB is the world leader in 3D printing for the railway industry. What started in 2015 with simpler spare parts like a plastic coat hook has now grown into 100,000 parts for over 500 different applications. More and more of them are operationally relevant. This also includes steel parts such as wheel set bearing covers for shunting locomotives, a box link for ICE trains or the gearbox housing for shunting locomotives. Around 1,000 virtual models are currently stored in the digital warehouse. By 2030, around 10,000 different components are to be kept in stock in this way.
Related topics
3D Printing/Additive Manufacturing, Regulation & Legislation, Rolling Stock Maintenance, Sustainability/Decarbonisation, The Supply Chain