Developing a train derailment detection system
Posted: 29 March 2022 | Giandomenico Cassano, Mauro Cassano | No comments yet
For Global Railway Review, Professional Engineers Giandomenico Cassano and Mauro Cassano explain how a newly developed train derailment detection system (TD2S) can reduce the damage caused by rolling stock derailments.
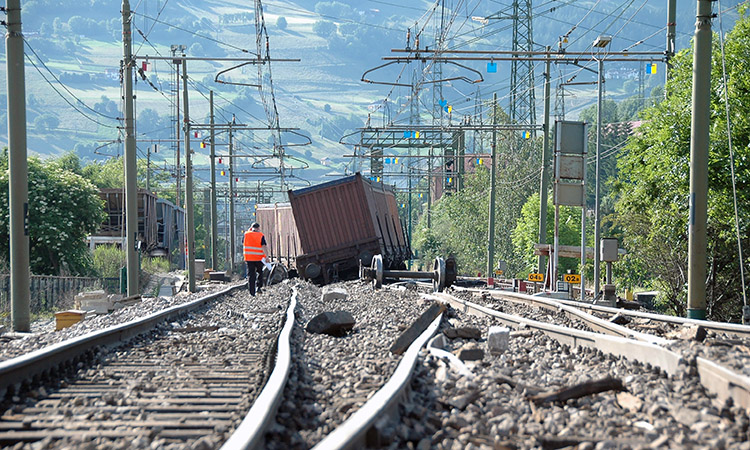
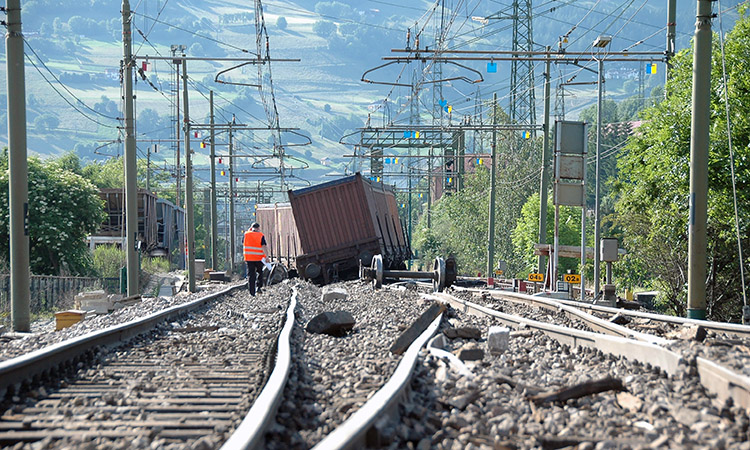
In a joint project between the Politecnico di Milano University and Alpha Caesar Srl, a train derailment detection system (TD2S) has been developed which can reduce the damage caused by derailments by providing an early warning of ‘derailment in progress’. This can enable the driver to reduce the derailment space and consequently mitigate the damage. The development project aimed to engineer a system that was as less invasive as possible.
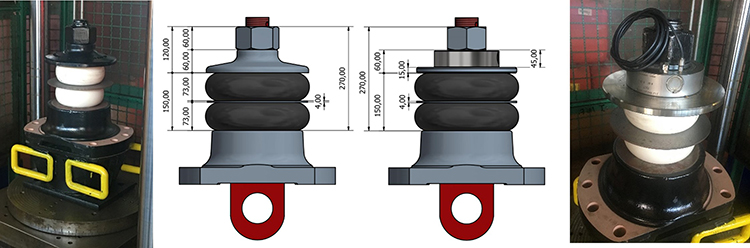
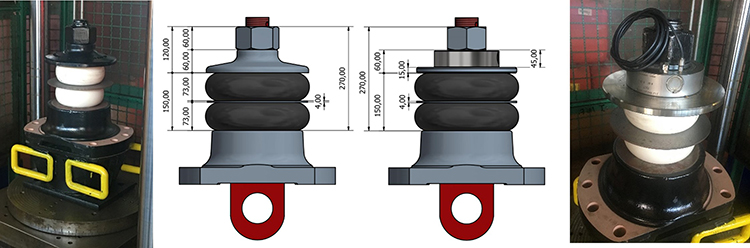
Figure 1
There are several objectives of the TD2S system, including:
- Detecting anomalous tensile stresses on the hook
- Warning the driver of any derailment
- Communicating events to the control operating rooms for emergency response
- Georeferencing the anomalous stresses on the hook
- Georeferencing the infrastructure defects
- Historicise/documenting the data.
The TD2S system
In its first prototype configuration, the TD2S system is completely independent of rolling stock on-board systems, and consists of:
- A pair of sensors engaged on the traction rod of the hook
- An antenna on the top of the locomotive for data transmission and GPS reception
- Accelerometers and inclinometers (IMU) mounted on the bushings of the wheelsets of the locomotive
- A pair of acoustic and light signals in the driver’s cabs
- A control unit for detecting the derailment, for issuing the alarm even remotely and for transmitting data.
The TD2S system is already set up for possible integration with the on-board systems and sensors of the locomotives. The integration would eventually allow to act on the automatic braking (which can be inhibited by the driver) and to record the data on locomotive server.
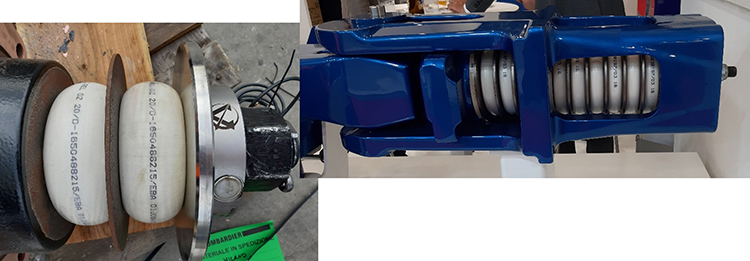
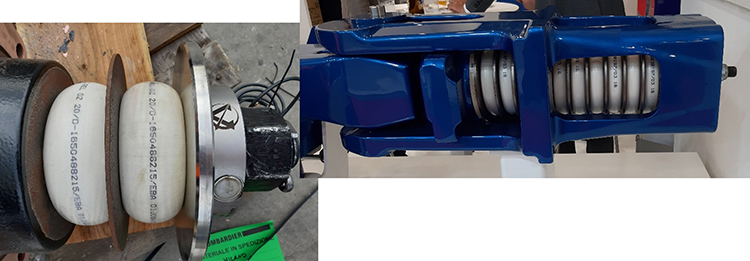
Figure 2
The TD2S system requires, on the hooks of the locomotive, the replacement of the shock absorber group partition washer with the toroidal load cell and the insertion of a new, suitably modified distribution washer.
There is no historical data relating to the evolution of traction stresses on the hook in the event of derailment. There is a numerical simulation of the hook stresses of an entire convoy during the derailment of a vehicle, carried out by the Bryansk State Technical University (Russia). Therefore, we hypothesised an increase in traction on the hook given by the sudden impact of the wheelset with the sleepers and the ballast; imagining that the phenomenon is repeated for each sleeper until the convoy stops.
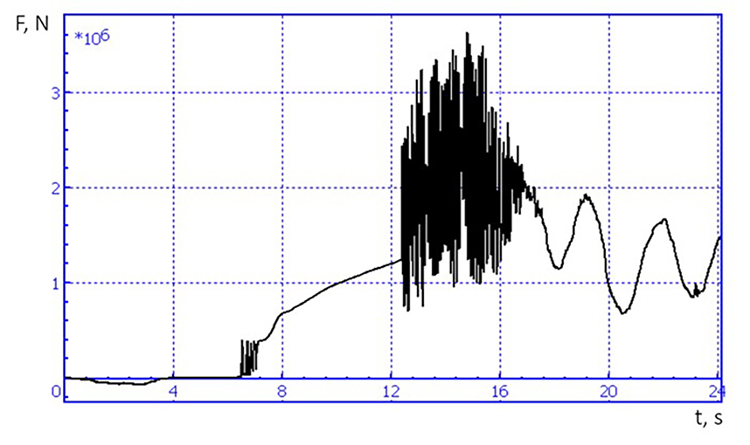
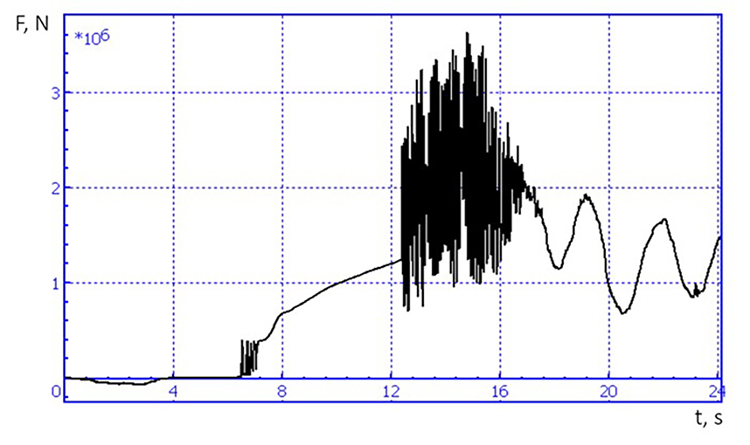
Figure 3: Numerical simulation of railway vehicle derailments – Bryansk State Technical University
We hypothesised an algorithm capable of detecting the derailment based on the analysis of the following four characteristic parameters:
- The definition of the increase in peak traction
- The variation over time of the residual effort at the hook that we expect is greater than the effort threshold at the start of the derailment
- The rate of variation of the angular coefficient of the straight line representing the increase in stress at the beginning of the derailment
- The rate of variation of the angular coefficient of the straight line representing the decrease in stress at the exit from the peak of traction.
Derailment test
Derailment test activities took place at RFI’s Bologna San Donato plant in April 2021. Track 116 was made available by RFI for the derailment test and track 117 for parking and intervention of the rescue wagon in preparation for the recovery of the derailed bogie.
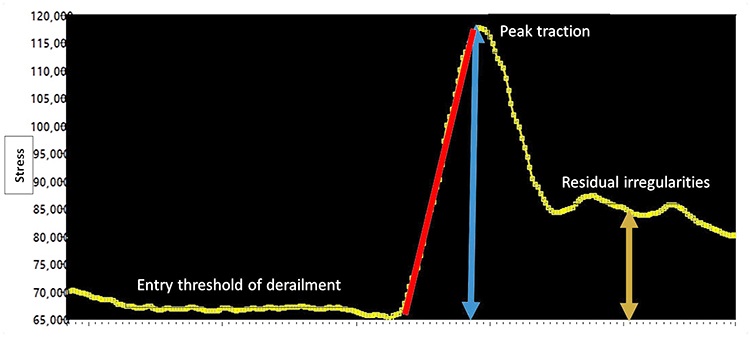
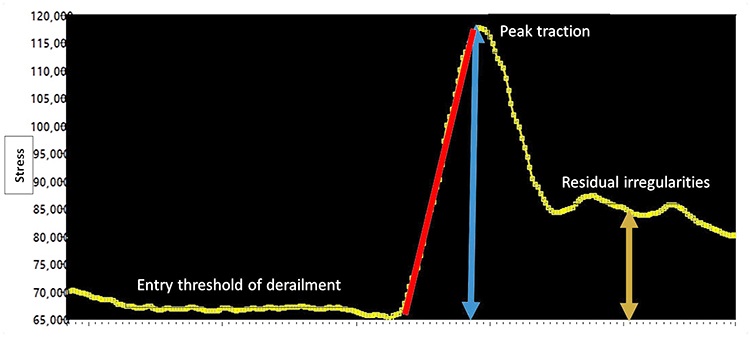
Figure 4
The derailment test consisted of derailing the last bogie of the last wagon of the convoy consisting of:
- A diesel locomotive in charge of pulling the convoy because of the lack of electrification
- The electric locomotive equipped with the TD2S system in towing position
- Two empty shield wagons to protect the electric locomotive
- An empty demolition wagon whose two axles of the last cart have been derailed.
The weight of the two derailed axles was 5.5 tonnes each.
The derailment occurred at around 18km/h and the derailed convoy was pushed up to 30km/h (maximum speed allowed on the test track) and then stopped.
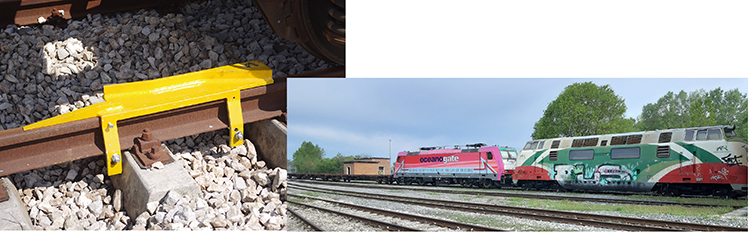
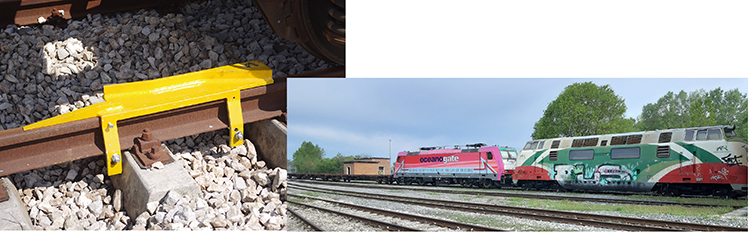
Figure 5
The derailment used a specially designed derailleur to best simulate derailment conditions. The test conditions were the most realistic possible and most difficult to recognise for the TD2S system.
A full wagon will only increase the effort in the derailment phase, improving its recognition by the TD2S system.
Derailment test analysis
The graphs shown in Figures 6a and 6b compare three free runs, and the derailment one highlighted in red. Figure 6a (in tonnes) reports the trend of the absolute values of the traction effort on the hook while Figure 6b reports the trend of the effort variation coefficient.
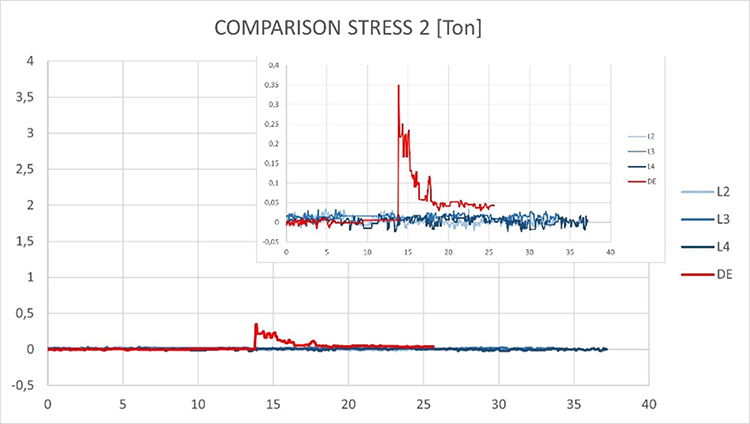
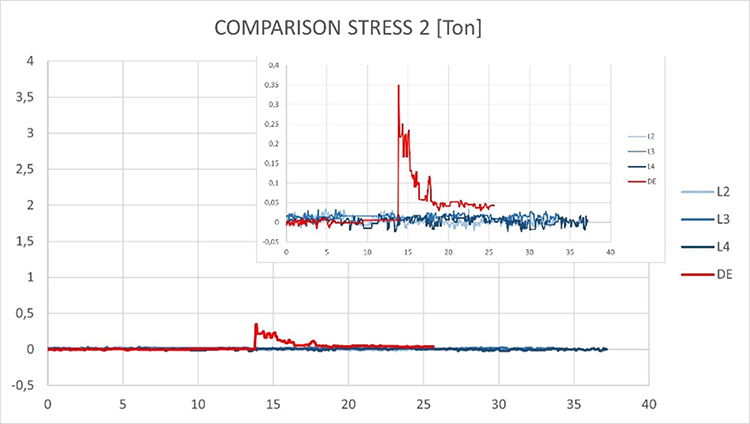
Figure 6a
It is evident that the derailment coefficients related to the derailment run are significantly higher compared to those of the free runs analysed.
The recognition of the derailment by TD2S does not depend on the towed mass but depends on the trend of the other recorded parameters (acceleration, speed, effort, derailment coefficient, IMU attitude).
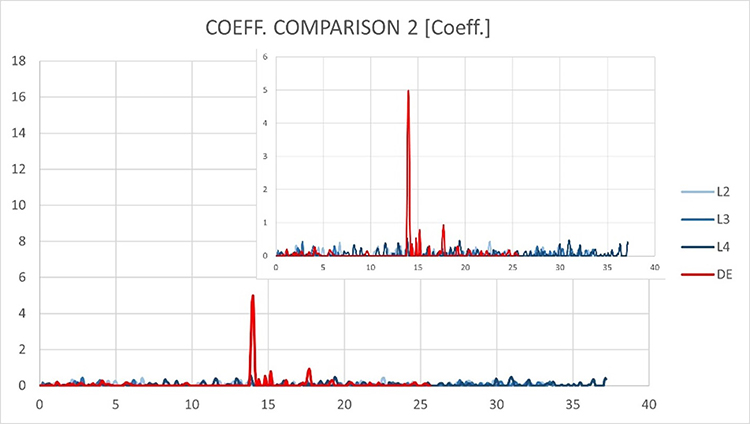
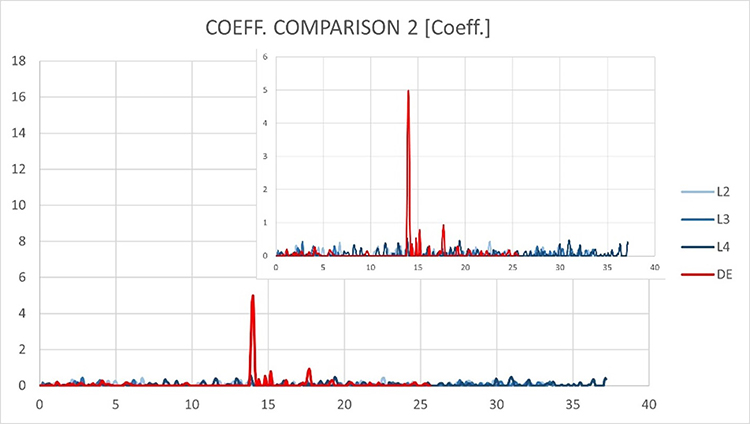
Figure 6b
The derailment test gave excellent results and was highly appreciated by the European Union Agency for Railways (ERA) who analysed the results obtained with us.
Further derailment simulations
After the derailment test, further simulations were carried out with the data recorded in two years of normal operational freight service of the locomotive.
As regards the criteria for the simulation, we used the principle of the superposition of loads.
We added to the values of the stresses detected during the journey performed in operation (Figure 7 Original Stress – top left graph) the values of the derailment stresses related to the front hook (Figure 7 Derailment Stress – centre graph), detected during the derailment test performed in Bologna.
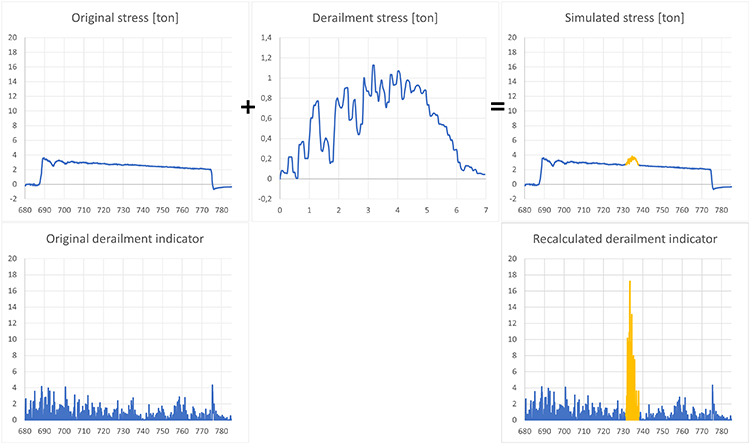
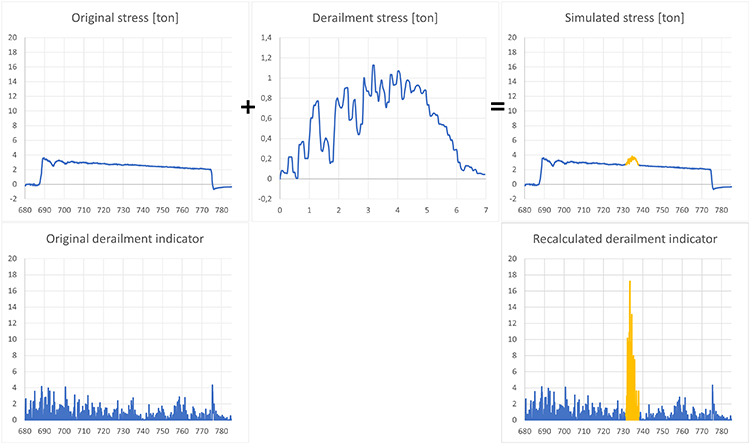
Figure 7
The result obtained is shown in Figure 7 related to Simulated Stress (top right graph). The added derailment stress is highlighted in yellow.
Figure 7 also shows the resulting derailment indicator that has been recalculated. The values of the indicator relating to the deviation (highlighted in yellow) are significantly higher than those of the original stress and are easily identifiable.
The analysis was carried out in all possible traction conditions, coasting, braking and acceleration, and for all the maximum and minimum values of the traction forces on the hook.
The values of the derailment indicator in correspondence with the simulated derailments are always clearly identifiable.
In all the analysed configurations, the TD2S system can recognise derailment.
RAMS analysis
A Reliability, Availability, Maintainability and Safety (RAMS) analysis related to the TD2S system was also performed. This analysis is significant for defining the SIL safety degree of the TD2S system over time.
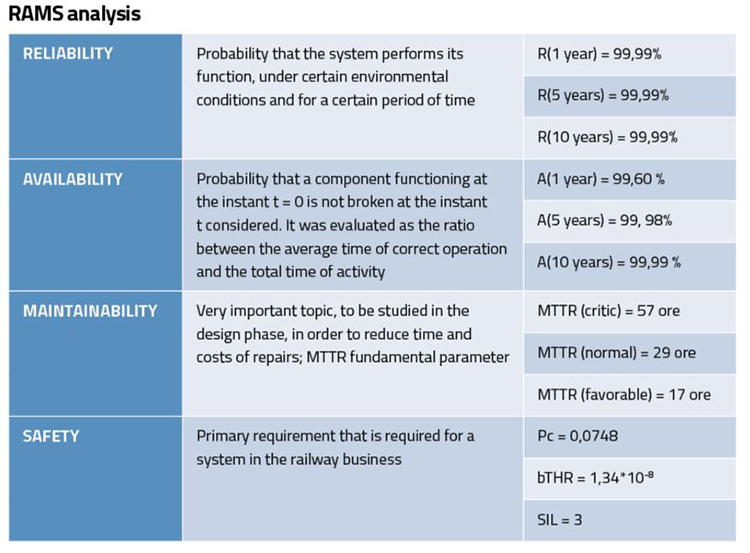
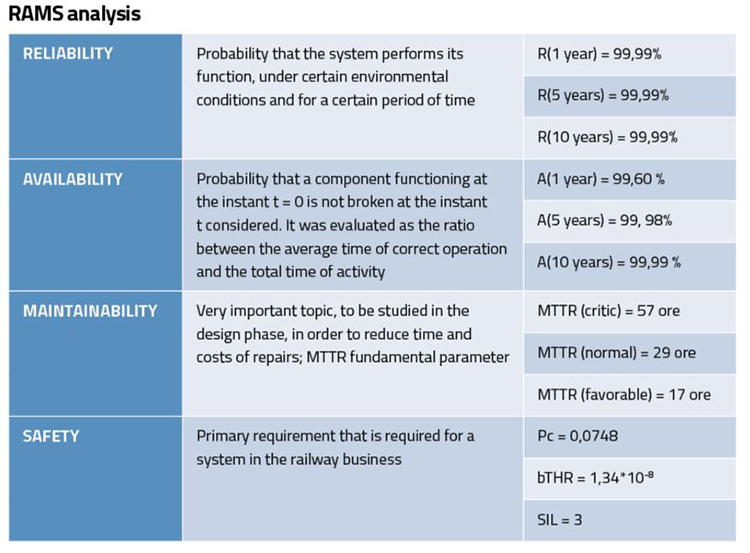
Table 1
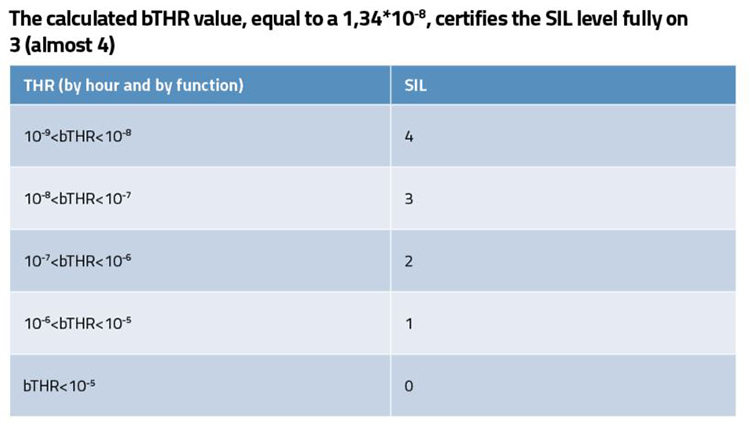
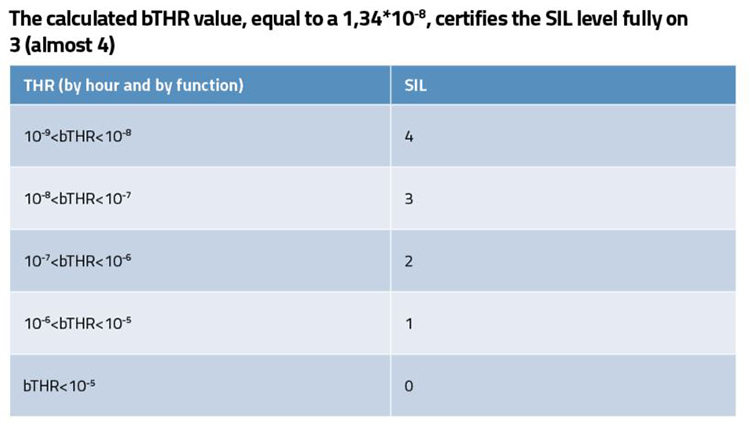
Table 2
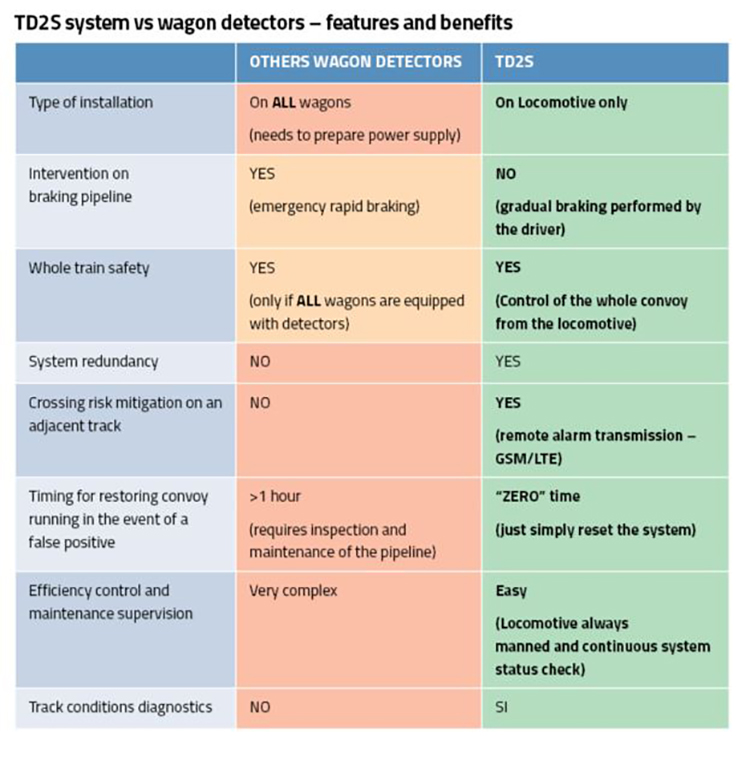
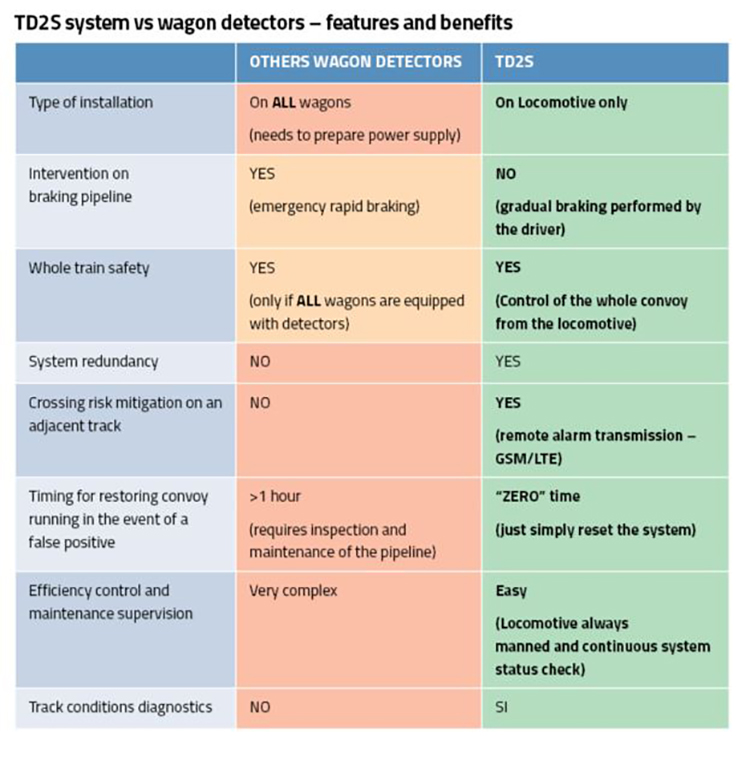
Table 3
In our case, the value of SIL 4 shown in Table 1 cannot be reached since the operations of stopping the train and making the line safe are a function of the human factor. Only in the case of complete automation of these latter processes (train stop and reorganisation of railway traffic) could SIL 4 be achieved.
Eng. Mauro Cassano is Chief Executive Officer and Technical Director of Alpha Caesar Srl, an engineering company based in Milan (Italy) that researches and develops innovative techniques in the railway field. Graduated in civil engineering at the Politecnico di Milano, Mauro was Technical Director of SEIT – Schweizer Elettronic Srl, a company engaged in the field of safety of railway yards.
Related topics
Bogies & Wheelsets, Cargo, Freight & Heavy-Haul, Electric/Hybrid Rolling Stock, High-Speed Rail, Operational Performance, Safety, Technology & Software
Related organisations
Alpha Caesar Sri, European Union Agency for Railways (ERA), Politecnico di Milano University