Utilising digitalisation and innovation to monitor and maintain rolling stock
Posted: 27 October 2022 | Peter Williams | No comments yet
Peter Williams, Fleet and Performance Data Manager at Avanti West Coast, explains how their collaborative and dynamic approach to fleet monitoring and maintenance helps to increase the efficiency, reliability, and the availability of its trains.
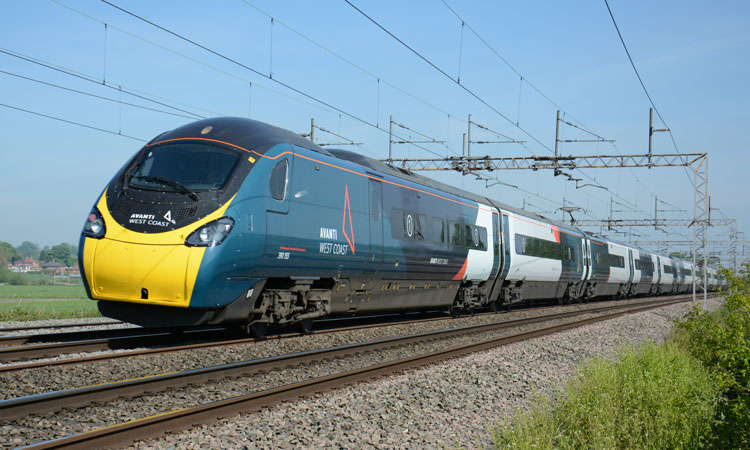
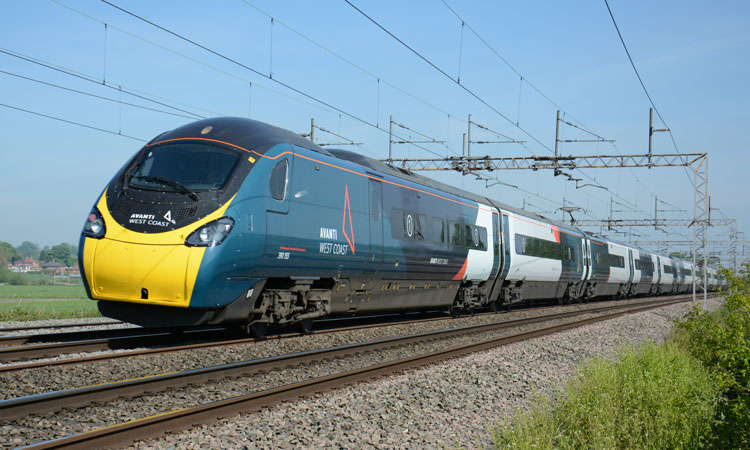
At Avanti West Coast we are proud to connect people and places across the UK with two fleets – our Super Voyager trains (Class 221) that operate over non-electrified sections of the West Coast Main Line in addition to running from London to Scotland via the West Midlands, and our electric Class 390 Alstom Pendolino high-speed trains, which are iconic to the West Coast and widely regarded as the UK’s hardest working train fleet, clocking up more than 270 million miles since they were launched.
To ensure our fleets continue to serve the communities and regions along our West Coast route like they have for 20 years, it is vital that their upkeep has customers, efficiency, and sustainability at its core. Digitalisation and innovative technology to monitor and maintain our fleets is integral to achieving this.
A dynamic approach
Working closely with Alstom, who maintain both our Pendolino and Super Voyager fleets, enables our teams at Avanti West Coast to utilise digital technology and innovations to adopt a dynamic approach to monitoring and maintaining trains that can be tailored, deliver benefits for fleet and maintenance teams, as well as drive improvements for our customers.
At Avanti West Coast we have built a collaborative relationship with Alstom, meeting the International Organisation of Standardisations (ISO 44001 – Collaborative Business Relationship). Together, we regularly exchange ideas to identify areas for maintenance improvements and explore new technologies. While Alstom are the main innovators for maintenance systems, we have found it is often only by working collaboratively that we realise the full potential of the technology available. Good evidence of this can be found within Alstom’s Rule Engine train monitoring system.
Alstom continually develop new intelligent rules within Rule Engine to monitor system reliability more proactively, and at Avanti West Coast, we assist in identifying rules that require a degree of interaction with our onboard operational staff. For example, we collaborated on the development of a new rule for ensuring the train was outstabled at stations correctly, this enabled the train to start up without delay on the next day of operation.
Condition-based maintenance and predictive maintenance tools
The maintenance of our Pendolino trains is underpinned by Alstom’s HealthHub – a condition‑based maintenance and predictive maintenance tool that uses data analytics to monitor the health of trains. Supported by technology data capture, it helps to identify key components that need to be repaired or changed and predict their remaining useful life.
Automated diagnostics portal, TrainScanner, which determines the condition of key components of our Pendolinos, supports HealthHub. Available at Longsight and Oxley depots, it scans the whole train to provide measurements and images of key components. Within 10 minutes of the train being scanned, we are provided with a visual of the train’s health. Carrying out assessments in this way enables more trains to be inspected and assessed more often.
TrainScanner measures the condition of the wheels, brake pads and pantograph carbon strips, as well as an ‘Integrity Check’ which comprises around 25 items on the body side and underframe of the train.
Utilising digitalisation and innovative technology ensures that we can take a proactive and preventative approach to monitoring and maintaining our fleets, helping to increase the efficiency, reliability, and the availability of our trains which ultimately has a benefit to our customers.
Our Super Voyager trains, which are soon to be retired, are monitored with equivalent technology. These technologies offer us and Alstom the opportunity to have a proactive approach to the monitoring and maintenance of our fleets, allowing us to predetermine potential issues and take preventative measures.
Using cloud-based technology, HealthHub provides us access to the intelligence of our Pendolino fleet at the click of a button – where all the data and records about a train can be found – helping to build one big picture of a train’s health. This remote in-service monitoring makes it easier to spot wear and potential issues earlier, establish if defects are isolated to one train or across the fleet, and can support with safety investigations – all while the train is running on the West Coast Main Line, so it doesn’t have to be taken out of service for longer than is necessary.
HealthHub triggers alerts based on data to monitor the fleet. Reports can also be generated to better understand the data acquired. This can help inform our maintenance plans, as we know what needs addressing and the required time to do this before the train is scheduled on the depot.
Items that need attention are automatically identified via HealthHub; therefore, Alstom’s maintenance teams can utilise their time to focus on those items, rather than identifying and diagnosing.
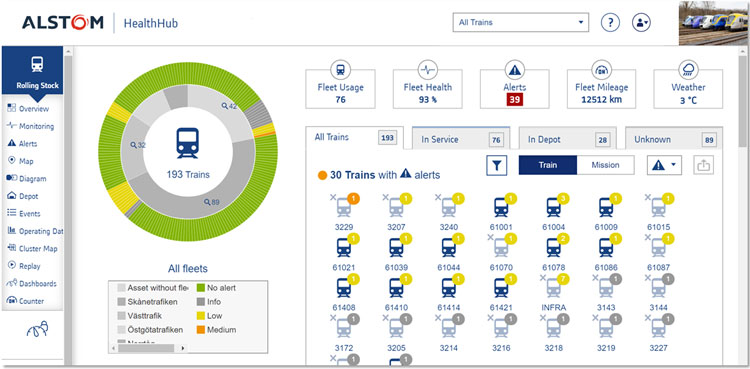
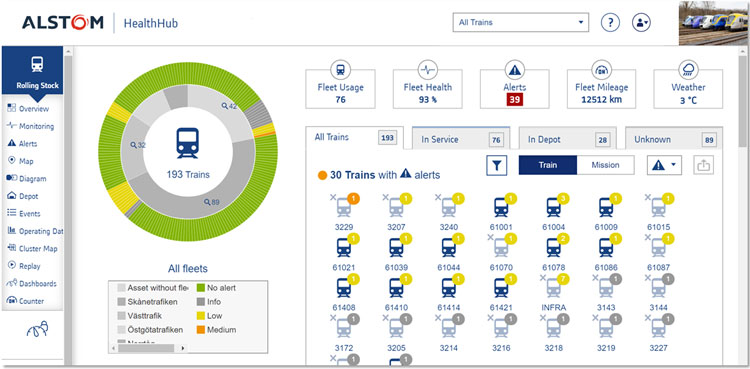
Using cloud-based technology, HealthHub provides Avanti West Coast with access to the intelligence of its Pendolino fleet, where data and records can help to build a big picture of a train’s health.
TrainScanner is used to monitor abnormal wear and helps to ensure that where rectifications have been made, they have reverted the wear to normal limits. As part of our winter preparation, we worked with Alstom to amend the carbon depth alert limits for the wear of pantograph carbon strips (equipment that is in constant contact with the overhead lines to enable the pantograph to draw the current when the train is in motion). This was done in response to conditions we endured over a particularly severe winter.
The following winter we saw a big reduction in ADD (Automatic Dropping Devices), a system that drops the pantograph and stops it from operating when the carbon strips are damaged or at low depth. The data suggests taking the approach to monitor equipment and intervene earlier once required has been hugely beneficial for performance in this area, which is crucial to the reliability of our Pendolino trains.
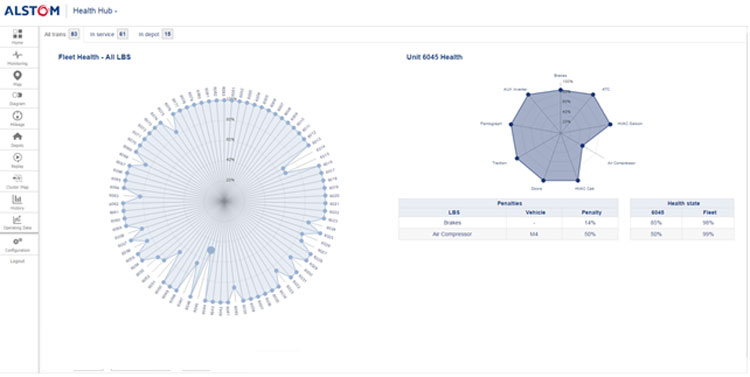
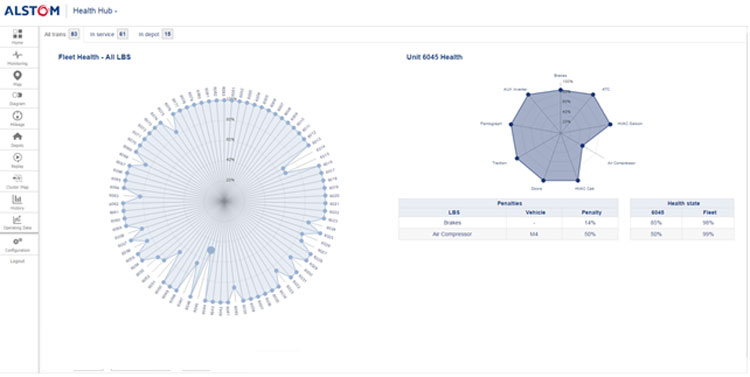
Using cloud-based technology, HealthHub provides Avanti West Coast with access to the intelligence of its Pendolino fleet, where data and records can help to build a big picture of a train’s health.
Monitoring assets can lead to unnecessary waste reduction
A reliable and punctual service is paramount for our customers. The fleets are imperative in helping us to deliver this, which is why the maintenance of our trains is focused on the customer – whether its ensuring facilities are fully functioning, or trains are resilient to extreme weather. This approach also considers the fact that our customers are more environmentally aware, and being a responsible business is becomingly increasingly important to them.
At Avanti West Coast we recognise the value of technology and digitalisation.
We want to make our operation as sustainable as we can. Utilising technology, such as TrainScanner, enables us and Alstom to maximise the material usage of items and equipment, as it allows for a reduction of SAFs (Service Affecting Failures) and helps increase reliability.
Measuring the brake pads across each train allows us to monitor the wear on them and change our maintenance regime. Rather than removing and replacing all brake pads after a prescribed periodicity (operation or mileage), we can set a rule to be alerted when a brake pad is approaching its change limit. By monitoring, we can also identify uneven wear to brake pads and mitigate it – prolonging their life and reducing unnecessary waste. Thus, supporting our commitment to being a responsible business.
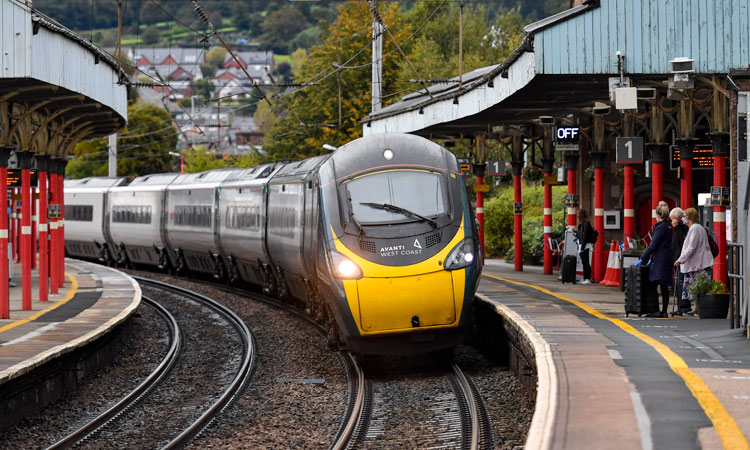
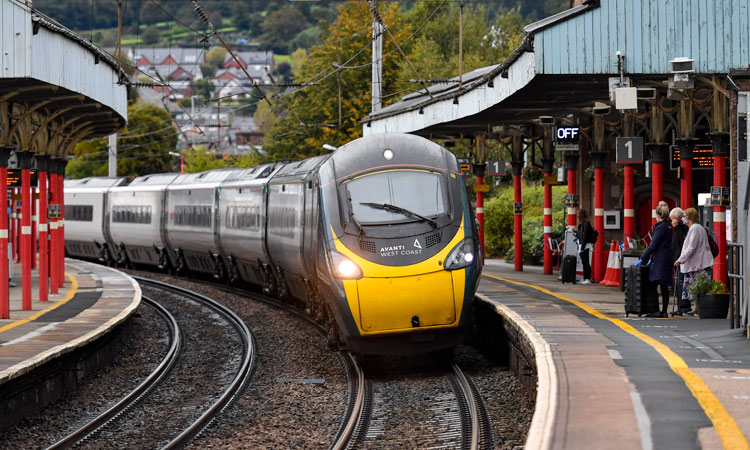
To ensure fleets continue to serve the communities and regions along West Coast routes, it is vital that their upkeep has customers, efficiency, and sustainability at its core.
Realising the full potential of technology
At Avanti West Coast we recognise the value of technology and digitalisation. We want to find innovative solutions and better ways of doing things, which is why as part of the £117 million refurbishment programme with Alstom for our Pendolino trains, the toilets onboard are being fitted with additional equipment to remotely monitor their condition and status. Data about the flush and wash operations, levels of waste tank and toilet occupied/free status will be monitored via HealthHub. This will enable us to better understand how our toilets are used and help to further inform how our approach to the maintenance and operational planning of our Pendolino fleet.
Utilising digitalisation and innovative technology ensures that we can take a proactive and preventative approach to monitoring and maintaining our fleets, helping to increase the efficiency, reliability, and the availability of our trains which ultimately has a benefit to our customers. It also provides the opportunity to work together with Alstom to realise the full potential of the technology available to support our commitments to sustainability and customer experience. Avanti West Coast and Alstom have a good history of collaboration to identify and evaluate new technologies. Our joint efforts in this area have delivered some great results and we want to continue to drive this forward – even more so as our Pendolino fleet will have a new lease of life following its refurbishment.
Issue
Related topics
Big Data, Digitalisation, Passenger Experience/Satisfaction, Rolling Stock Maintenance, Technology & Software